PCB Materials
Pressure Sensitive Adhesive (PSA)
PSA, short for Pressure-Sensitive Adhesive, is a kind of adhesive tape that falls under the category of major adhesive tapes. It is a thin and flexible material with a coating on one or both sides, sometimes also referred to as Self-Stick Adhesive.
Table of Contents
Add a header to begin generating the table of contents
What is Pressure Sensitive Adhesive (PSA)?
Pressure Sensitive Adhesive (PSA) is a type of adhesive that forms a bond when pressure is applied to it. It is a versatile adhesive that is widely used in various industries, including electronics, automotive, packaging, and medical devices. In the field of electronics, PSA is used for a wide range of applications, including the manufacturing of Flexible or Rigid-Flex PCBs.
One of the key features of PSA is its ability to adhere to a variety of substrates, including metals, plastics, and glass. This makes it an ideal adhesive for electronic applications because it can bond to a wide range of materials that are commonly used in the manufacturing of electronic devices. Additionally, PSA does not require any heat to activate, which reduces the risk of damage to the electronic components during the manufacturing process.
Another important feature of PSA is its mechanical strength. PSA has the ability to absorb shock and provide vibration dampening, which is essential in electronics applications where devices need to withstand harsh conditions.
Due to its unique properties, PSA is an ideal adhesive for the manufacturing of Flexible or Rigid-Flex PCBs. These types of PCBs require an adhesive that can bond to both flexible and rigid substrates while maintaining mechanical strength. PSA fits the bill perfectly because it can bond to both flexible and rigid substrates, and its mechanical strength ensures that the bond will remain stable even under harsh conditions.
Types of Pressure Sensitive Adhesive
In general, there are two main types of pressure sensitive adhesives: single-sided and double-sided. Single-sided adhesives are designed to only stick to one side of a surface, while double-sided adhesives can bond two surfaces together.
Single-sided adhesives are often used for applications where only one surface needs to be bonded, such as attaching a label or a piece of tape. Double-sided adhesives, on the other hand, can be used for a wide range of applications, including in the production of flexible or rigid-flex PCBs.
Another key distinguishing factor between different types of pressure sensitive adhesives is whether they are thermal or pressure sensitive. Thermal adhesives require the application of heat to initiate the bonding process, while pressure sensitive adhesives bond simply by applying pressure.
In general, pressure sensitive adhesives are preferable for many applications, including flexible or rigid-flex PCB production, because they are more versatile and require less equipment to apply. In addition, pressure sensitive adhesives tend to be more reliable and have better long-term stability than thermal adhesives.
Commonly Used PSA Tapes
The pressure sensitive adhesive materials that are frequently used to bond stiffeners and FR4 frames (which act as a supporting plate and perform a similar function to an SMT carrier) on the flex circuits include:
- 3M467
- 3M966
- 3M9077
- Tesa 8853
- Tesa 8854
- And any other double-sided PSA tape models that may be required
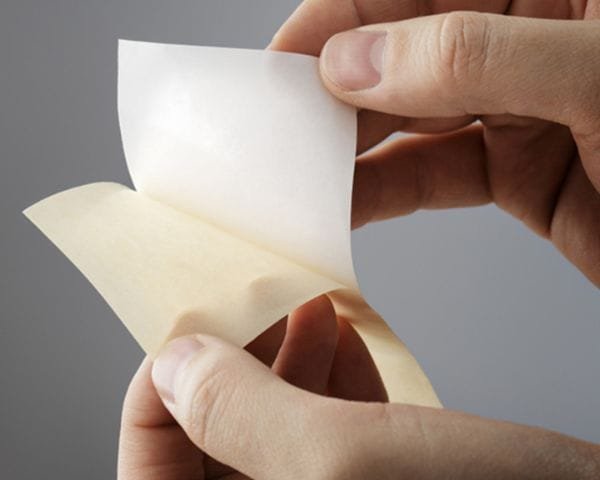
Benefits of PSA Tapes
PSA tapes, also known as Pressure Sensitive Adhesive tapes, are widely used in various industries due to their excellent properties. In this section, we will discuss the advantages of PSA tapes.
Easy to use: PSA tapes are very easy to use and do not require any special equipment or tools for application. They can be easily applied by hand or by machine.
Reduces mechanical damage: The use of PSA tapes eliminates the need for screws, bolts, and fasteners that require drilling or punching holes in the material. This minimizes the chances of mechanical damage to the materials.
Improved precision: PSA tapes have uniform thickness and provide excellent gap filling properties. This helps in improving the precision of the final product.
Cost-effective: The use of PSA tapes reduces the need for surface refinishing and improves the overall cost-effectiveness of the product.
Increases efficiency: PSA tapes reduce assembly time as they do not require any curing or drying time. This increases the overall efficiency of the manufacturing process.
Thinner and lighter material: PSA tapes are thinner and lighter in weight compared to other bonding materials. This reduces the weight of the final product.
Bonds dissimilar materials: PSA tapes can bond dissimilar materials without any compatibility concerns. This makes them suitable for a wide range of applications.
Provides vibration dampening and noise reduction: PSA tapes provide excellent vibration dampening and noise reduction properties. This makes them ideal for use in automotive and aerospace industries.
In summary, PSA tapes have numerous advantages over traditional bonding methods. They are easy to use, cost-effective, and provide excellent precision and efficiency. The use of PSA tapes can also reduce mechanical damage to materials and provide excellent vibration dampening properties.
FPC Adhesive (Bonding Sheet) vs. PSA
To complete the creation of a flexible circuit, stiffeners are added as one of the final fabrication steps. These stiffeners can be applied using either a layer of pressure-sensitive adhesive or a layer of thermal setting adhesive known as a Bonding Sheet. The PSA application is generally less expensive than the thermal setting method.
To use thermal setting adhesive, the flex PCB must be returned to the lamination press and subjected to heat and pressure to properly cure the adhesive. Additionally, the adhesive must be pre-cut to fit the exact shape of the stiffener using laser cut or die punching techniques. The type of adhesive chosen will depend on the configuration and location of the stiffeners. If a stiffener does not extend to the circuit outline, then PSA attachment and an additional stiffener outline added to the silkscreen may be necessary for accurate placement.
Thermally bonding stiffeners using heat and pressure is the preferred method and produces a very strong, permanent bond when using the same flexible adhesive as that used to attach the coverlay. When the design prevents the use of flexible adhesive, bonding only with pressure using PSA is an alternative method. The specific PSA used will vary depending on whether the flex PCB will be subjected to an automated reflow cycle and the material it will be adhered to.
Flex Circuit PSA Design Considerations
PSA sections have specific design requirements that are based on their manufacturing and installation onto the flex circuit. Typically, PSAs are cut into separate shapes and then manually attached to the flex circuit. Laser cutting or a punch and die set can be used to create the PSA outline, but the size of the PSA may impact its manufacturability. To ensure accurate placement, it’s recommended to include the PSA outline on the silkscreen layer of the design.
For designs that involve automated component assembly and reflow, the type of PSA used may be limited due to the high temperatures involved in the reflow process. Only a few PSAs are rated for RoHS reflow temperatures and are limited to mechanical attachment purposes. No thermally or electrically conductive PSA that is reflow temperature rated has been identified. If needed, these PSAs must be added to the flex circuit after the component assembly process. If the PSA is used to attach a stiffener, the PSA is added to the stiffener material first and then cut simultaneously with the stiffener outline using a routing operation.
Explore Our PCB Fabrication Services
Related Reading
- What is Flexible Copper Clad Laminate (FCCL)?
- EMI Shielding Film In FPC Applications
- Complete Guide To PCB Copper Foil
- PET vs. PI: the Differences Between these Materials for Flex PCBs
- Comprehensive Guide to Manufacturing Flex PCB with Stiffener
- What are the Different Types of Flexible Circuits?
- Unlocking the Versatility of Flex Circuit Design: Applications and Benefits
- What are the Materials for Flex Circuits?
- Flexible PCBs: Advantages And Disadvantages