PCB Electronic Manufacturing Services
Immersion Tin (ImSn) PCB Surface Finish
JHYPCB is a pioneering printed circuit board manufacturer based in China. With state-of-the-art facilities and stringent quality control, JHYPCB produces high-quality PCBs for customers worldwide.
As a leading producer of rigid, flexible, and rigid-flex PCBs, JHYPCB offers a variety of surface finish options to meet application requirements. One such surface finish is immersion tin plating for PCBs.
Immersion tin refers to a PCB surface finish applied through immersion plating. It involves dipping PCBs in a heated tin-based solution to deposit a thin layer of tin onto the copper traces. The immersion tin plating provides excellent solderability while remaining cost-effective.
This article provides a comprehensive overview of the immersion tin PCB surface finish offered by JHYPCB. We discuss the key benefits, suitable applications, plating process, and JHYPCB’s capabilities regarding immersion tin PCB manufacturing. Whether you are looking for a RoHS-compliant, budget-friendly PCB finish or require mass production of immersion tin PCBs, JHYPCB has the expertise to deliver.
Read on to learn all about immersion tin PCB surface finish and how it can meet your PCB plating needs. JHYPCB has manufactured thousands of immersion tin PCBs and is ready to transform your design into reality.
Benefits of Immersion Tin Plating
Immersion tin offers several advantages that make it an appealing PCB surface finish for many applications. Here are some of the key benefits of using immersion tin plating on printed circuit boards:
- Cost-Effective Solution
Compared to other common finishes like ENIG (electroless nickel immersion gold), immersion tin is a more budget-friendly plating option. It does not use expensive metals like gold or palladium. The low cost of immersion tin makes it suitable for high-volume PCB production. - Excellent Solderability
The tin deposit on the PCB leads to excellent solderability. The solder wets nicely to immersion tin surfaces, allowing for good solder joint formation. JHYPCB performs solderability testing to ensure the PCB’s immersion tin coatings meet IPC standards. - Long Shelf Life
Immersion tin plating has a long shelf life of over 12 months. The finish resists oxidation and tarnishing, maintaining solderability over extended periods. This ensures the PCBs work reliably after prolonged storage. - Environmentally Friendly
Immersion tin chemistry does not use harsh chemicals. The plating process is environmentally benign, producing minimal hazardous waste. It is also RoHS-compliant, containing no lead or other restricted substances. - Fine Pitch Compatibility
With its ability to plate thin and uniform layers, immersion tin can reliably coat fine-pitch components. This makes it suitable for HDI (High-Density Interconnect) PCBs with compact spaces.
Applications of Immersion Tin PCBs
The benefits of immersion tin plating make it a versatile PCB finish suitable for a wide range of applications, including:
- Consumer Electronics
Immersion tin is commonly used in consumer electronics like smartphones, tablets, TVs, gaming devices, and more. It meets the need for budget-friendly high-volume PCB production. The stable shelf life ensures reliability over the product’s lifetime. - Automotive
Stringent quality demands and long product lifecycles make immersion tin suitable for automotive electronics. It survives under-hood conditions while maintaining solder joint integrity over many years. - Telecommunications
Immersion tin’s fine pitch plating capabilities allow it to be used in telecom devices like routers, switches, and base stations. The surface finish reliably plates the dense PCBs used in telecommunications. - Medical
For medical devices, immersion tin provides a lead-free, RoHS-compliant finish. It also withstands repeated exposure to high temperatures during soldering and component attachment. - Other Applications
Immersion tin also sees usage in industrial electronics, IoT devices, avionics, instrumentation, and military equipment, among other areas. It is a versatile finish for a broad spectrum of PCB applications.
For most applications, immersion tin is recommended for mass production runs rather than low-volume prototyping. JHYPCB has expertise in delivering large quantities of immersion tin PCBs per customer specifications. Contact us to discuss your immersion tin PCB requirements.
Immersion Tin Plating Process
At JHYPCB, we use a highly controlled immersion tin plating process to apply uniform and consistent coatings onto printed circuit boards. Here are the key steps involved:
- Surface Preparation
The PCBs undergo thorough cleaning and microetching to remove oxidation and activate the copper surface. This prepares the substrate for immersion tin deposition. - Flux Application
A protective flux coat is applied over the copper to prevent re-oxidation. The flux also facilitates tin deposition during immersion. - Tin Immersion
The PCBs are immersed in a heated tin-based solution which deposits a thin layer of tin onto the copper traces. The immersion time and temperature are controlled to achieve the desired coating thickness. - DI Rinse
After immersion, the PCBs are rinsed thoroughly in deionized water to remove excess chemicals and flux residues. - Drying
The PCBs are then dried to remove any moisture before further processing and testing.
JHYPCB maintains strict process controls throughout the plating steps. Parameters like solution concentrations, temperature, pH, exposure times are continuously monitored. This results in repeatable and reliable immersion tin coatings batch after batch.
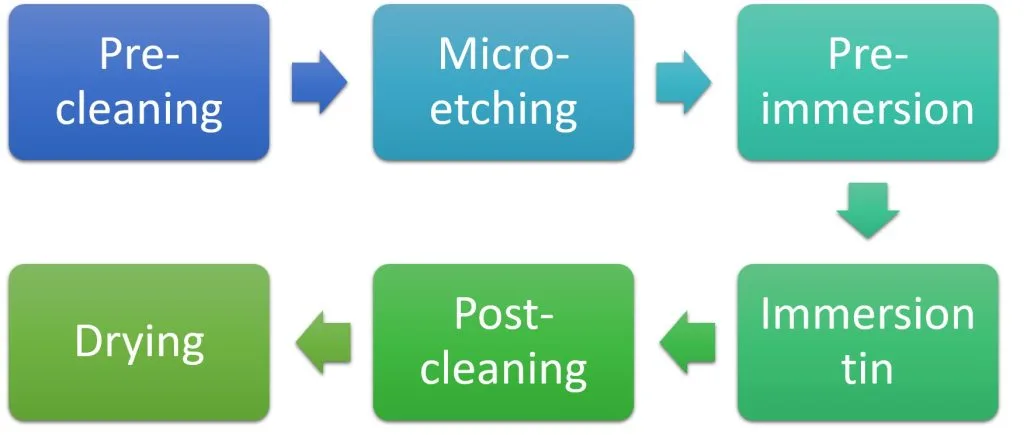
Immersion Tin Vs. ENIG: What is the difference?
Immersion tin and ENIG are two common PCB surface finish options that have some key differences:
- Cost – Immersion tin is more affordable than ENIG. ENIG uses expensive gold which drives up cost.
- Durability – ENIG is more corrosion resistant than immersion tin over very long periods, but tin still provides good shelf life.
- Solderability – Both offer excellent solderability out of the box. Immersion tin may require freshening for soldering after prolonged storage.
- Wear Resistance – ENIG withstands repeated mating cycles better than immersion tin due to the hardness of nickel.
- Environmental – Immersion tin is more eco-friendly with minimal waste compared to ENIG.
- Pitch Capability – Immersion tin can coat ultra fine pitch pads while ENIG has limitations coating pitches under 150um.
- Termination – ENIG is preferred for gold wire bonding termination. Immersion tin requires hot air solder leveling for termination.
- Whiskering – Immersion tin is more prone to tin whisker growth over time compared to ENIG.
In summary, immersion tin provides a budget-friendly PCB finish with good solderability. ENIG is used when higher durability, wear resistance and corrosion protection are needed despite the higher cost. The choice depends on the application requirements.
Immersion Tin Vs. HASL: What is the difference?
- Process – Immersion tin involves chemical deposition while HASL applies solder coating.
- Flatness – Immersion tin provides a very flat finish even on fine features. HASL can create uneven finish with bridging risks.
- Solderability – Both offer excellent solderability. But HASL may need pre-tinning before soldering after long storage.
- Durability – Immersion tin stands up better to mechanical wear and tear over time vs HASL.
- Environmental – Immersion tin is more eco-friendly than lead-based HASL formulas. Lead-free HASL is an option though.
- Repairability – It’s easier to rework solder joints and modifications on HASL PCBs than immersion tin.
- Cost – Immersion tin has higher initial PCB fabrication cost compared to HASL.
- Pitch capability – Immersion tin can coat ultra-fine pitch pads. HASL has limitations coating below 0.5mm pitch.
- Whiskering – Immersion tin is prone to tin whisker growth over time. HASL does not have this risk.
Immersion Tin Vs. Immersion Silver: What is the difference?
- Cost – Immersion silver is more expensive than immersion tin due to the higher cost of silver.
- Oxidation – Immersion silver oxidizes faster than immersion tin, limiting its shelf life. It requires conformal coating for oxidation protection.
- Solderability – Immersion silver offers excellent solderability that lasts longer than immersion tin over time.
- Durability – Immersion silver is harder and more wear resistant than immersion tin. It withstands repeated mating cycles better.
- Whiskering – Only immersion tin faces the issue of tin whisker growth over time. Immersion silver does not have this risk.
- Environmental – Immersion tin is more eco-friendly than silver plating solutions which can contain cyanides.
- Termination – Immersion silver allows direct wire bonding. Immersion tin needs hot air solder leveling for termination.
- Pitch capability – Both can coat ultra-fine pitch pads below 100 microns.
In summary, immersion silver provides superior solderability and durability but at a higher cost. Immersion tin is more budget-friendly but prone to whiskering over time. The trade-offs depend on PCB performance needs.
JHYPCB's Capabilities in Immersion Tin PCBs
With over a decade of experience manufacturing printed circuit boards, JHYPCB has honed its capabilities in immersion tin PCB production:
- Advanced Plating Equipment: JHYPCB has invested in state-of-the-art immersion tin plating lines from leading global suppliers. The automated equipment allows for efficient, high-volume PCB finishing.
- Stringent Quality Control: From incoming materials inspection to process monitoring and final testing, stringent QC procedures ensure consistent immersion tin quality. PCBs are tested for thickness, solderability, adhesion and other parameters.
- Skilled Engineers: JHYPCB’s team comprises experienced engineers who ensure optimal immersion tin plating performance based on the product needs and requirements.
- Range of PCB Services: JHYPCB offers immersion tin finishing for rigid, flex, rigid-flex, and HDI PCBs. We can manufacture simple or complex board designs with immersion tin coating.
- Volume Production: With a monthly output of over 500,000 square feet of PCBs, JHYPCB has the capacity to deliver high volumes of immersion tin PCBs according to customer demand.
With JHYPCB as your immersion tin PCB partner, you can be assured of the highest quality standards and production capabilities tailored to your requirements. Contact our engineering team to discuss your specific project needs.
Contact JHYPCB for Your Immersion Tin PCB Needs
JHYPCB has the expertise and experience to manufacture immersion tin PCBs to the highest quality standards. To get started with your immersion tin PCB project:
- Send Your Requirements: Contact our engineering team to discuss your design, technical specifications, volume needs, and any other requirements. We will provide expert guidance.
- Get a Quote: Upload your PCB design files and get a free quote for immutable tin PCB fabrication and assembly. Our sales team is ready to assist you.
- Place Your Order: We make the ordering process quick and easy, with online file uploads and order tracking. Reliable delivery in the fastest turnaround times.
- Receive Support: Our engineers provide technical support through the design, prototyping, and production process. Contact us anytime for assistance.
With a customer-focused approach and passion for innovation, JHYPCB is ready to realize your vision with immersion tin PCBs tailored for your application needs. Reach out to us today to get started on your next project!
FAQs
What is immersion tin plating?
It is a PCB surface finish where bare copper traces are dipped in a heated tin-based solution to deposit a thin layer of tin by chemical reduction.
What are the benefits of immersion tin?
Key benefits are low cost, good solderability, fine pitch capability, and environmentally friendly process.
What industries commonly use immersion tin PCBs?
Consumer electronics, telecom, automotive, medical, and industrial control sectors widely use immersion tin PCBs.
Does immersion tin meet lead-free requirements?
Yes, it is RoHS compliant and lead-free. The plating solution contains only tin salts.
How long is the shelf life of immersion tin PCBs?
Typically 12 months or more. The finish resists tarnishing and maintains solderability.
Is immersion tin suitable for harsh environment applications?
It withstands humidity, thermal cycling and other environments quite well. But not as robust as gold or nickel finishes.
Can immersion tin withstand multiple reflow cycles?
Yes, it can survive over 3x reflow cycles with proper process controls. Extended high-heat exposure can consume the finish.
What are the limitations of immersion tin plating?
Potential for tin whisker growth over time and lower wear resistance than other finishes.