PCB Electronic Manufacturing Services
Immersion Silver PCB Surface Finish
At JHYPCB, we specialize in high-quality PCB prototyping and manufacturing services. One of our most popular offerings is immersion silver PCB plating. As experts in immersion silver technology, JHYPCB provides reliable and cost-effective immersion silver PCB surface finishing for prototypes and production runs. This revolutionary plating process yields excellent conductivity while remaining environmentally friendly. In this comprehensive guide, we will explain everything you need to know about immersion silver PCB plating. You’ll learn about the numerous benefits of using immersion silver over other platings like ENIG or OSP for your PCB fabrication needs. We’ll also walk through the immersion silver process step-by-step and showcase why it’s an ideal PCB surface finish for a wide range of electronics applications. Let’s dive in and explore the impressive capabilities of immersion silver PCBs!
Table of Contents
Add a header to begin generating the table of contents
What is Immersion Silver PCB Surface Finish?
Immersion silver, sometimes referred to as immersion silver plating or immersion Ag plating, is a method of depositing a thin silver layer onto a copper PCB substrate. It is an economical and environmentally friendly alternative to other common PCB platings like ENIG (electroless nickel immersion gold), OSP (organic solderability preservatives), and hard gold.
Immersion silver provides excellent conductivity and solderability while avoiding issues like gold embrittlement. It is suitable for a broad range of PCB applications from prototyping to medium-volume production runs. The immersion silver process has gained popularity in recent years for its ability to meet the needs of modern high-speed, high-frequency PCB designs cost-effectively.
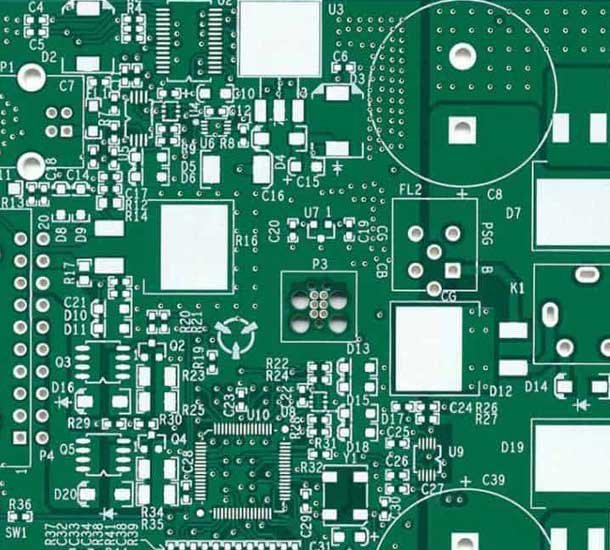
Benefits of Immersion Silver
Immersion silver offers numerous advantages that make it an excellent PCB surface finish for prototypes and production. Here are some of the key benefits of immersion silver plating:
- Cost-Effective
Immersion silver is more affordable than gold and palladium plating. It is priced competitively with OSP finishes while providing better solderability and shelf life. The low cost makes immersion silver ideal for prototyping where budget is a major consideration. It also allows smaller production runs to be plated economically. - Good Solderability and Shelf Life
The immersion silver deposit creates a solderable surface finish that holds up well during reflow soldering. Testing shows immersion silver can withstand multiple reflow cycles with minimal impact on solderability. The finish also has a longer shelf life compared to OSP with good solderability retention for up to 1-2 years when properly stored. - High Conductivity
Silver is the most conductive metal after copper. Immersion silver preserves the high conductivity of the copper traces, allowing it to perform well at high frequencies up to 6GHz. This makes it suitable for RF, microwave, and other high-speed circuit designs. - RoHS Compliant and Eco-Friendly
Immersion silver is free of lead, cadmium, and other hazardous substances. It complies with RoHS and other environmental regulations. The process is also non-toxic, avoiding the use of cyanides present in some silver plating baths. This makes immersion silver one of the most environmentally friendly PCB finish options.
Applications of Immersion Silver PCBs
Immersion silver’s combination of reliability, conductivity, and cost-effectiveness make it suitable for a wide range of electronics applications. Here are some of the top uses for immersion silver plated PCBs:
- PCB Prototyping
The low cost of immersion silver is ideal when prototyping circuits on a budget. It allows multiple iterations of a PCB design to be fabricated and tested without high plating expenses. The good solderability also enables easier assembly and modification of prototypes.
- Small to Medium Production Runs
For production volumes from tens to thousands of boards, immersion silver offers a cost-effective plating solution. It avoids the premium cost of gold plating while providing better performance than OSP or HAL finishes. This makes it a popular choice for mid-volume consumer electronics and industrial control products.
- High Frequency and High-Speed Designs
Immersion silver’s excellent conductivity facilitates its use in RF, microwave, automotive, and fast digital circuits where high frequencies are important. The smooth silver finish minimizes signal loss across traces.
- SMT and Through Hole Assembly
The finish solders well to both surface mount and through-hole components. So immersion silver can be used for mixed technology designs. It is also compatible with lead-free solders and reflow processes.
In summary, immersion silver’s versatility makes it suitable for prototyping, low-mid volume production, and high-speed PCB applications. Its reliability and cost profile provides the right balance for many electronic products.
Immersion Silver Plating Process
The immersion silver plating process involves chemically depositing a thin layer of silver onto a copper PCB without using external electrical current. Here is an overview of the key steps:
Step 1: Surface Preparation
The copper traces are cleaned and microetched to remove oxidation and activate the surface. This prepares the copper for accepting the silver layer.
Step 2: Activation
The boards are immersed in a palladium-tin colloidal solution which deposits a thin layer of palladium particles. This acts as a catalyst for the silver deposition.
Step 3: Silver Deposition
The activated boards are immersed in a solution containing a silver salt (usually silver nitrate) and reducing agents. The silver ions are attracted to the palladium sites, where they undergo reduction and deposit metallic silver.
Step 4: Post-Treatment
The boards are rinsed thoroughly and often undergo an anti-tarnish treatment to prevent oxidation. This locks in the conductive silver finish.
The immersion silver process temperature is close to room temperature. Agitation of the plating solutions accelerates deposition. The parameters are precisely controlled to obtain a uniform silver thickness of around 2-5 microinches.
The key benefit versus electrolytic silver plating is the lack of complex fixturing and electrical supplies. The immersion technique allows silver to be deposited directly onto intricate PCB geometries. The process also avoids issues like dog bone formation seen with electrolytic plating.
Reliability of Immersion Silver
For PCB finishing, reliability is a top concern. Immersion silver provides excellent reliability that matches or exceeds most other platings. Here are some of the factors that contribute to the reliability of immersion silver:
- Corrosion Resistance
Silver inherently resists tarnishing and oxidation. The immersion silver deposit maintains the conductive surface without corrosion issues. Anti-tarnish treatments applied after plating further enhance corrosion resistance. - Solderability Retention
Testing shows solderability stays relatively consistent for 1-2 years with immersion silver. Reflow heat aging induces minimal degradation compared to other common finishes. This ensures reliable soldering even after shelf storage. - Thermal Cycling Performance
Immersion silver withstands repeated exposure to soldering temperatures with very little impact. Thermal cycling tests demonstrate excellent joint integrity after hundreds of cycles. - Ductility
Unlike immersion gold, silver is a ductile metal. This allows the finish to endure thermal and mechanical stresses without cracking issues. The finish retains adhesion and conductivity.
By leveraging the natural properties of silver, immersion silver PCB finishing displays reliability and longevity suitable for electronics manufacturing. The finish withstands application environments while maintaining conductance and solderability.
Immersion Silver Vs. ENIG: What is the difference?
ENIG is an extremely common PCB finish that utilizes electroless nickel followed by an immersion gold deposit. However, it does have some reliability concerns versus immersion silver:
- Gold Embrittlement – The immersion gold layer in ENIG can develop micro-cracks over time, especially when exposed to thermal cycling. This occurs because gold is a brittle metal. The cracks degrade solder joint integrity and increase resistivity. Immersion silver does not suffer embrittlement issues.
- Corrosion Resistance – The nickel underlayer in ENIG can be attacked by sulfur and halogens, leading to corrosion and formation of resistive nickel sulfides/oxides. Immersion silver is less prone to subsurface corrosion.
- Wear Resistance – The thin gold layer in ENIG can begin wearing off over rub testing, exposing the nickel underlayer. Immersion silver exhibits better wear resistance during contact and assembly.
- Solder Leaching – Slight dissolution of the nickel underlayer during soldering can produce a “purple plague” effect – interfering with wetting. Immersion silver avoids leaching issues.
- Cost – While immersion silver was once more expensive than ENIG, improving process efficiency has made its cost comparable or even lower than some ENIG processes.
The table below clearly shows the differences between immersion silver and immersion gold plating.
Items | Immersion Silver | Immersion Gold |
---|---|---|
Shelf life | Up to 12 months | Up to 12 months |
Sensitivity to handling | Require gloves to be used, or fingerprints and minor scratches may be left. | It is recommended to use gloves, but careful handling does not deteriorate components |
Packageless sustainability | Comparatively poor, require to be used for the assembly nearly immediately after being unpacked | Comparatively average, but still require to be put in use fast |
Surface planarity | Great | Excellent |
Safety | Safe for the environment and labor | Safe for the environment and labor |
Suitability for lead-free assembly techniques | Yes | Yes |
Chemical properties/resistance | Is vulnerable to some inorganic acids | Is not vulnerable to most acids |
Plating | Good plating, but highly depends on the conditions of the process/can be insufficient | Superior plating over both the copper pads and via holes |
Solderability | Great | Excellent |
RoHS Directive compliance | Fully compliant | Fully compliant |
Magnetic properties | Do not show undesirable magnetic properties | Has undesirable magnetic properties because of Nickel |
Rework | Can be relatively easily reworked multiple times and repaired | Is expensive and difficult to rework. Typically, is not repaired/is difficult to repair |
Cost | An affordable method | A most expensive method |
Immersion Silver Vs. Immersion Tin: What is the difference?
Immersion tin has gained some popularity recently as a lead-free surface finish option. However, immersion silver has some advantages over immersion tin:
- Whiskering – Immersion tin is prone to growing tin whiskers over time which can cause electrical shorts. Immersion silver does not present this risk.
- Oxidation – Tin oxidizes readily, developing a non-conductive SnO2 layer. This reduces solderability over time. Silver resists oxidation better.
- Corrosion – Tin provides relatively poor corrosion resistance, especially in humid environments. Silver is largely corrosion proof.
- Solder Leaching – The tin layer can dissolve into the solder during reflow, reducing reliability. Leaching is minimal with immersion silver.
- Thermal Cycling – Tin finishes tend to crack under thermal stress which raises circuit resistance. Immersion silver retains better integrity.
- Shelf Life – Immersion tin shelf life is about 1 year until oxidation occurs. Immersion silver lasts 1-2 years with good solderability.
JHYPCB's Immersion Silver Capabilities
JHYPCB has extensive capabilities for immersion silver PCB fabrication, backed by years of experience and process refinement. Here are some details on our immersion silver expertise:
- Years of Experience
We have offered immersion silver plating for over 10 years. Our team has accumulated in-depth knowledge of the process, optimal parameters, and applications. - Process Controls
Stringent process controls govern the immersion silver line including solution maintenance, pre-treatment, plating thickness, and post-treatment. This ensures consistency. - Capacity
Our immersion silver line can handle small prototyping orders up to medium volumes of thousands of boards per month. We can scale capacity to match customer demand. - Quality Testing
We validate plating quality through tests like solderability, porosity, thickness, and adhesion. Only boards passing our stringent criteria ship out. - Customer Applications
Customers from sectors like telecom, automotive, IoT, and consumer electronics rely on our immersion silver plating services for their PCB needs.
By leveraging our technical expertise, quality focus, and experience with immersion silver, JHYPCB is capable of meeting the most demanding PCB fabrication requirements. Contact us to discuss how our immersion silver capabilities can benefit your next project!
FAQs on Immersion Silver
What is the typical thickness of an immersion silver deposit?
The thickness is usually between 2-5 microinches (50-125 nm). This provides good conductivity without using excess silver.
Does immersion silver contain silver nanoparticles?
No, immersion silver involves reduction of silver ions to form a uniform metallic silver layer, not discrete nanoparticles.
How many reflow cycles can immersion silver withstand?
Testing shows immersion silver retains excellent solderability after 500+ reflow cycles, significantly higher than most other finishes.
Is immersion silver suitable for epoxy-based SMT components?
Yes, it has good adhesion to epoxy compounds and avoids the black pad issue seen with ENIG finishes.
What is the generally accepted shelf storage life for immersion silver PCB finish?
The generally accepted shelf storage life for immersion silver is 6 to 12 months in dry conditions, which is the same as for HASL (hot air solder leveling) PCB finish. Proper storage avoiding heat, humidity, and contamination can help maximize the shelf life of immersion silver boards before soldering.
Does immersion silver meet automotive and aerospace industry standards?
Yes, it meets or exceeds common specs like IPC and MIL standards for electronics fabrication.
Is immersion silver process environmentally friendly?
Yes, it is free of cyanides and other hazardous chemicals making it a greener plating option.
What percentage of PCBs are created using immersion silver surface finish?
Approximately one-tenth of all PCBs are created using immersion silver PCB surface finish. So immersion silver accounts for about 10% of the total PCB surface finishing market. The popularity of immersion silver has been growing steadily in recent years due to its reliability, conductivity, and cost-effectiveness.
What is the chemical reaction that occurs during immersion silver plating?
The chemical reaction that takes place during immersion silver plating is:
Cu2+ + 2Ag+ → 2Ag + Cu2+
In this redox reaction, copper ions (Cu2+) in the PCB substrate are reduced while the silver ions (Ag+) in the plating solution are oxidized. The silver ions gain electrons from the copper substrate and are reduced to metallic silver (Ag) which deposits on the PCB surface. The copper ions are oxidized to Cu2+ and enter the plating solution to maintain the reaction.