Metal Core PCB Manufacturing Service
Single Sided Metal Core PCB
JHYPCB is a trusted metal core PCB manufacturer in China. We offer single-layer MCPCB, double-side MCPCB, and multilayer MCPCB manufacturing services.
Metal core PCBs, or MCPCBs, including single layer metal core PCB, double layer metal core PCB and multilayer metal core PCB, are widely used in high-power LED lighting applications, automotive electronics, and other fields. JHYPCB is a trusted metal core PCB manufacturer in China. We offer metal core PCB prototyping, single-layer MCPCB, double-side MCPCB, and multilayer MCPCB manufacturing services.
What is Single Sided Metal Core PCB?
Single Layer Metal Core PCBs (MCPCBs) are a type of printed circuit board that consists of a metal base layer, a dielectric layer, and a copper layer. The metal base layer is typically made of aluminum, copper, or steel and provides excellent thermal conductivity and heat dissipation. The dielectric layer is a thin insulating layer that separates the metal base layer from the copper layer, and the copper layer is the conductive layer that carries the electrical signal. Single Layer Metal Core PCBs are commonly used in various applications, such as high-power LED lighting, automotive electronics, and power supplies, due to their excellent thermal conductivity and heat dissipation properties.
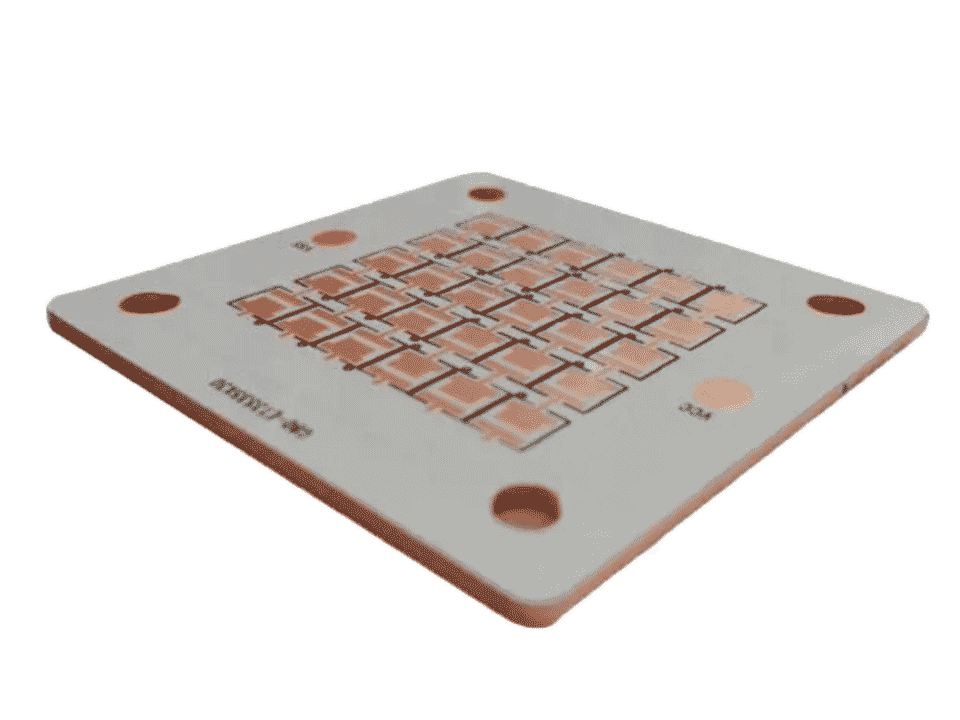
What is Single Sided PCB?
Single-sided PCB is a type of printed circuit board that has conductive traces, pads, and components on only one side of the board. The other side of the board is usually coated with a non-conductive material, such as a solder mask, to prevent accidental short circuits.
Single-sided PCBs are typically used for simpler electronic circuits that require fewer components and do not require high-density routing. They are often used in consumer electronics, such as calculators, remote controls, and radios.
Single-sided PCBs are less expensive to produce than double-sided or multi-layer PCBs because they require fewer manufacturing processes and use fewer materials. They are also easier to design and manufacture since there is no need to worry about routing traces and components on both sides of the board.
However, single-sided PCBs have some limitations. They are not suitable for complex circuits that require high-density routing, as they only have one layer of routing. Additionally, single-sided PCBs are not ideal for circuits that require high-frequency operation, as they may suffer from interference and noise.
Single Layer Metal Core PCB Structure
Single Layer Metal Core PCBs consist of a metal base layer, a dielectric layer, and a copper layer. The metal base layer is typically made of aluminum, copper, or steel and provides excellent thermal conductivity and heat dissipation. The dielectric layer is a thin insulating layer that separates the metal base layer from the copper layer, and the copper layer is the conductive layer that carries the electrical signal.
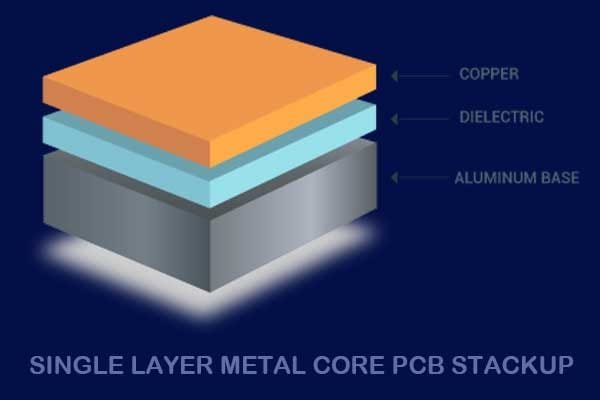
Working Principle of Single Layer MCPCBs
The working principle of Single Layer Metal Core PCBs is relatively simple. The metal base layer acts as a heat sink, drawing heat away from the electronic components mounted on the copper layer. This allows the electronic components to operate at a lower temperature, which improves their performance and increases their lifespan.
Single Layer Metal Core PCB Assembly
The Single layer metal core PCB can be used with surface mount and chip & wire components, providing much lower thermal resistance than FR4 PCB. The metal core is cheaper than ceramic substrates and allows much larger areas than ceramic substrates.
Single Layer Metal Core PCB vs. FR4 PCB
Single Layer Metal Core PCBs and traditional FR4 PCBs have several differences.
- Structure:
Single-Layer Metal Core PCBs have a metal base layer, a dielectric layer, and a copper layer. The metal base layer provides excellent thermal conductivity and heat dissipation, and the copper layer is the conductive layer that carries the electrical signal. In contrast, FR4 PCBs consist of a fiberglass substrate, a copper layer, and a solder mask layer. The fiberglass substrate provides insulation, and the copper layer carries the electrical signal. - Thermal Conductivity:
Single Layer Metal Core PCBs have significantly better thermal conductivity and heat dissipation properties than traditional FR4 PCBs. This makes them ideal for high-power applications, such as high-power LED lighting and power supplies. - Reliability:
Single Layer Metal Core PCBs have better reliability than FR4 PCBs. They are less prone to thermal expansion and contraction, which can cause the PCB to warp and affect the performance of the electronic components. Additionally, they are resistant to high temperatures and electromagnetic interference, which makes them suitable for use in harsh environments. - Manufacturing Process:
The manufacturing process for Single Layer Metal Core PCBs is more complex than for traditional FR4 PCBs. Single Layer Metal Core PCBs require a metal base layer, which needs to be cut to the required size and shape. They also require a more complex manufacturing process, which can make them more difficult to manufacture. - Cost:
Single Layer Metal Core PCBs are generally more expensive than traditional FR4 PCBs. This is due to the more complex manufacturing process and the cost of the metal base layer.
What are the Benefits of Single Layer Metal Core PCB?
Single Layer Metal Core PCBs offer several benefits over traditional FR4 PCBs, including:
- Thermal Conductivity: Single Layer Metal Core PCBs have excellent thermal conductivity and heat dissipation properties. The metal base layer provides a high thermal conductivity path, allowing the heat generated by electronic components to dissipate more effectively. This reduces the operating temperature of the electronic components, which can improve their performance and reliability.
- High-Power Applications: Due to their excellent thermal conductivity and heat dissipation properties, Single Layer Metal Core PCBs are ideal for high-power applications, such as high-power LED lighting and power supplies. They can handle high currents and dissipate heat effectively, reducing the risk of thermal damage to the electronic components.
- Improved Reliability: Single-Layer Metal Core PCBs are more reliable than traditional FR4 PCBs. They are resistant to thermal expansion and contraction, which can cause the PCB to warp and affect the performance of the electronic components. They are also resistant to high temperatures and electromagnetic interference, which makes them suitable for use in harsh environments.
- Compact Design: Single Layer Metal Core PCBs have a compact design, which can save space and reduce the overall size of the electronic device. This can be especially important for applications where space is limited.
- Improved Circuit Performance: Single Layer Metal Core PCBs can improve the performance of the electronic circuit. The metal base layer provides a low-impedance ground plane, which can reduce noise and improve signal integrity. This can result in better overall circuit performance.
- Cost-Effective Solutions: Despite being more expensive than traditional FR4 PCBs, Single Layer Metal Core PCBs offer cost-effective solutions for high-power applications. They can reduce the need for additional heat sinks or fans, which can save costs and improve the overall efficiency of the electronic device.
What are the Disadvantages of Single Layer Metal Core PCB?
Although Single Layer Metal Core PCBs offer several advantages, they also have a few disadvantages:
- Complexity: The manufacturing process for Single Layer Metal Core PCBs is more complex than for traditional FR4 PCBs. The metal base layer needs to be cut to the required size and shape, and the metal core PCBs require a more complex manufacturing process. This can result in a longer lead time and higher manufacturing costs.
- Cost: Single Layer Metal Core PCBs are generally more expensive than traditional FR4 PCBs due to the cost of the metal base layer and the more complex manufacturing process. This can make them less attractive for low-cost applications.
- Limited Layer Count: Single Layer Metal Core PCBs have a limited layer count, usually only one or two layers. This can limit their application in complex electronic circuits that require more than two layers.
- Design Limitations: The design of Single Layer Metal Core PCBs can be limited due to the metal base layer. The metal base layer can make it difficult to add vias or plated-through holes, which can limit the routing options for the circuit. This can make it challenging to design complex circuits that require multiple layers or routing options.
- Thermal Expansion: Although Single Layer Metal Core PCBs are less prone to thermal expansion and contraction than traditional FR4 PCBs, they can still experience thermal expansion. This can cause the PCB to warp and affect the performance of the electronic components.
Single Layer Metal Core PCB Applications
Single Layer Metal Core PCBs have a wide range of applications in various industries due to their excellent thermal conductivity, heat dissipation properties, and improved circuit performance. Some of the common applications of Single Layer Metal Core PCBs include:
- LED Lighting: Single Layer Metal Core PCBs are commonly used in LED lighting applications, such as streetlights, high-bay lights, and downlights. The high thermal conductivity of the metal base layer allows for effective heat dissipation, which can improve the lifespan and reliability of LED lighting.
- Power Electronics: Single Layer Metal Core PCBs are used in power electronics, such as power supplies, motor controllers, and inverters. The high power handling capability and excellent thermal conductivity of the metal base layer allow for effective heat dissipation, reducing the risk of thermal damage to the electronic components.
- Automotive: Single Layer Metal Core PCBs are used in the automotive industry for various applications, such as lighting systems, power electronics, and engine control units. The high thermal conductivity of the metal base layer allows for effective heat dissipation, improving the reliability and lifespan of the electronic components.
- Medical Devices: Single Layer Metal Core PCBs are used in medical devices that require high reliability and performance, such as MRI machines, ultrasound machines, and patient monitoring systems. The high thermal conductivity of the metal base layer allows for effective heat dissipation, reducing the risk of thermal damage to the electronic components.
- Aerospace: Single Layer Metal Core PCBs are used in the aerospace industry for various applications, such as avionics, satellite communication, and navigation systems. The high reliability and improved circuit performance of Single Layer Metal Core PCBs make them ideal for use in harsh aerospace environments.
- Consumer Electronics: Single Layer Metal Core PCBs are also used in consumer electronics, such as laptops, smartphones, and tablets. The improved circuit performance and compact design of Single Layer Metal Core PCBs can improve the overall performance and lifespan of consumer electronic devices.
Single Layer Metal Core PCB Manufacturing and Design
The manufacturing process for Single Layer Metal Core PCBs is more complex than for traditional FR4 PCBs. The metal base layer is first cut to the required size and shape, and then a thin layer of dielectric material is applied to the surface. The copper layer is then applied to the dielectric layer, and the circuit is etched into the copper layer using a photolithographic process. Finally, the PCB is coated with a protective layer to prevent oxidation.
When designing Single Layer Metal Core PCBs, it is important to consider thermal management. The components should be placed in such a way that heat is evenly distributed across the metal base layer. This can be achieved by using a thermal pad, which helps to transfer heat from the component to the metal base layer. It is also important to ensure that the PCB is properly grounded to minimize electromagnetic interference.
Metal Core PCB Manufacturer in China
If you’re looking for reliable and high-quality PCB manufacturing services, look no further than our company in China. We offer a range of PCB solutions to meet your needs, including single-sided metal core PCB, double-sided metal core PCB, multilayer metal core PCB, FR4 PCB, and flexible PCB.
Our team of experienced professionals is dedicated to providing you with the best possible service and ensuring that your PCBs meet the highest quality and performance standards. We use only the highest quality materials and advanced manufacturing processes to ensure that your PCBs are manufactured to your specifications and delivered on time and within budget.
So, we’ve got you covered whether you need a simple single-sided PCB or a complex multilayer metal core PCB. Contact us today to learn more about our PCB manufacturing services and discuss your requirements. We look forward to working with you and helping you bring your electronic designs to life.