PCB Electronic Manufacturing Services
PCBs for Home Appliances
JHYPCB provides high-quality and reliable PCB manufacturing and assembly services for the home appliances industry. We are committed to meeting customer needs, ensuring product quality, and production efficiency.
High-Quality PCB Manufacturing and Assembly Services Supplier for Home Appliances
JHYPCB is a leading manufacturer and assembler of high-quality PCBs for Home Appliances. With years of experience in this field, we have accumulated extensive knowledge in producing and assembling PCBs that meet the highest industry standards. Our advanced technology and equipment allow us to deliver custom-made solutions that cater to various appliance manufacturers’ specific needs. We specialize in providing PCB solutions for air conditioners, washing machines, refrigerators, and more. At JHYPCB, we are committed to delivering top-notch products and services that guarantee exceptional quality and reliability. Contact us today to see how we can help bring your home appliance PCB projects to life.
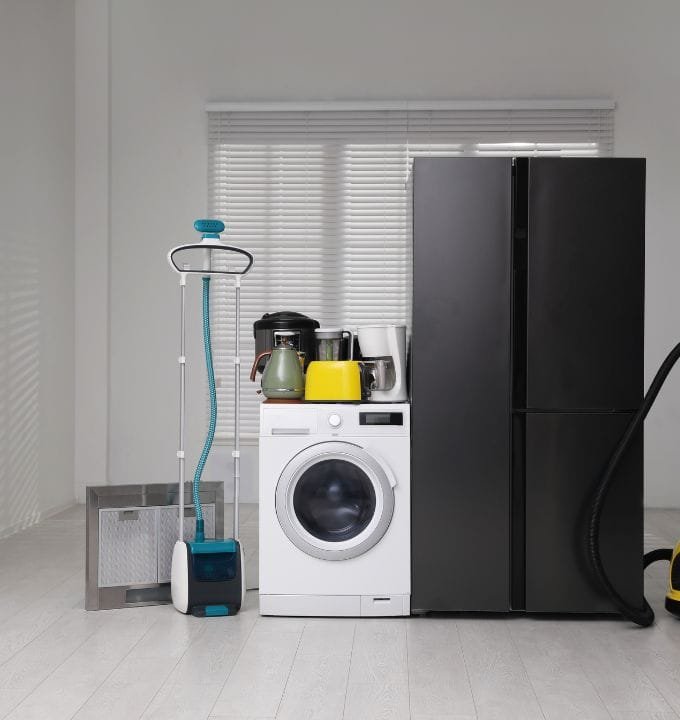
The Role of PCBs in Modern Home Appliances
PCBs play a crucial role in regulating and automating various home appliance functions, ensuring efficiency, reliability, and safety. As a trusted manufacturer and assembler of high-quality PCBs, JHYPCB provides custom solutions that meet the unique requirements of home appliance manufacturers, ensuring optimal performance and customer satisfaction.
Air Conditioners: Modern air conditioning systems employ complex electronic controls to regulate temperature, airflow, and humidity, which require advanced PCBs. PCBs control the compressor, fan motor, thermostat, and other components of air conditioners, ensuring optimal performance and energy efficiency.
Washing Machines: Washing machines rely on advanced PCBs to automate the washing process, adjusting the water level, detergent amount, and wash cycle based on the load size, fabric type, and soil level. PCBs also monitor the drum’s speed, balance, and position, ensuring smooth operation and preventing damage to the machine.
Refrigerators: Refrigerators use various types of PCBs to control different functions such as temperature, defrosting, and lighting. The main PCB regulates the compressor, evaporator fan, and condenser fan motors, while the dispenser PCB controls the ice maker, water dispenser, and display panel. PCBs ensure efficient cooling and prevent food spoilage by maintaining consistent temperatures.
Microwaves: Microwaves rely on PCBs to control the magnetron, which generates microwave energy to heat food, as well as the display panel and keypad. PCBs also monitor the voltage, current, and temperature of the magnetron, ensuring safe and reliable operation.
Vacuum Cleaners: Vacuum cleaners use motor control PCBs to regulate the suction power and brush roll speed, providing efficient cleaning for different surfaces. Other PCBs control the cord reel, switch, and LED indicators, ensuring convenient operation and indicating maintenance reminders.
Home Appliance PCB Applications
- Washer/dryer
- Ovens/ranges
- Dishwasher
- Refrigerator/freezer
- Home security systems
- Smart home
- Hard drives
- Keyboards
- LED lighting
- Monitors
- Microwaves
- Coffee makers
- Power supplies
- Printers
- Projectors
PCBs Types Used in Home Appliances
Single-Sided PCBs: Single-sided PCBs have copper conductors on only one side of the board. They are suitable for simple circuits with few components, such as power supplies or lighting systems. Single-sided PCBs have limited routing options, requiring larger board sizes and more significant spacing between traces. They are also commonly used in toys, calculators, and other low-cost consumer electronics.
Double-Sided PCBs: Double-sided PCBs have copper conductors on both sides of the board, allowing for more complex circuits and higher component densities. They also offer greater flexibility in routing and can use through-hole or surface-mount technology (SMT) components. Double-sided PCBs are widely used in home appliances, automotive electronics, and industrial controls.
Multilayer PCBs: Multilayer PCBs have multiple layers of copper conductors separated by insulating materials, allowing for even denser circuits with fewer wires crossing over each other. Multilayer PCBs are commonly used in high-performance applications such as smartphones, computers, and other consumer electronics. They are also used in medical devices, aerospace, and military applications.
Rigid-Flex PCBs: Rigid-flex PCBs combine the benefits of rigid and flexible PCBs, allowing for complex circuits that require both support and flexibility. Rigid-flex PCBs consist of multiple layers of flexible and rigid substrates connected through plated through-holes. They are commonly used in medical devices, aerospace, and military applications, as well as portable electronic devices such as smartphones and tablets.
High-Frequency PCBs: High-frequency PCBs are designed to operate at frequencies above 1 GHz, requiring specialized materials and construction techniques to minimize signal loss and interference. High-frequency PCBs are commonly used in wireless communication systems, radar equipment, and satellite navigation systems. They are also used in medical imaging equipment, aerospace technology, and automotive radar systems.
PCB manufacturing process
Preparation: We start by preparing the raw materials, including copper-clad laminates, solder mask ink, and silkscreen ink. We also review the design files to ensure that all specifications are met.
Printing: The next step is to print the circuit pattern on the copper-clad laminate using specialized printers. This process is called “photoetching,” and it involves exposing the copper layer to UV light through a photomask. The areas not covered by the mask become the circuit traces.
Drilling: After printing, we drill holes in the board for through-hole components and vias. We use automated drilling machines to ensure accuracy and consistency.
Plating: Once the holes are drilled, we plate the board with a thin layer of copper to form the conductive paths between the layers. This process involves electroplating the board with copper in a chemical bath.
Solder Mask and Silkscreen: We apply a solder mask over the copper traces to prevent short circuits and protect the board from environmental factors. We also add a silkscreen layer to the board to indicate component placement, PCB revision, and other important information.
Quality Control: At each stage of the manufacturing process, we conduct rigorous quality control checks to ensure that every board meets our stringent standards. We test for defects such as shorts, opens, and impedance variations.
Final Inspection: The final stage of the process is a thorough inspection of the finished PCBs. We verify that the boards meet all specifications and requirements and that they are free of defects.
PCB assembly services
Sourcing Components: We work with trusted suppliers to source high-quality components for the PCB assembly process. Our procurement team carefully selects components based on customer specifications and requirements, ensuring that they meet the necessary performance, reliability, and environmental standards.
Stenciling and Placement: We use advanced pick-and-place machines to accurately place surface-mount components on the board. The machine uses a camera system to verify component locations and orientation, ensuring precise placement. Before placement, we apply solder paste to the board using a stencil to ensure that the components are correctly aligned and placed.
Reflow Soldering: After component placement and solder paste application, the board is passed through a reflow oven. The oven heats the board to the required temperature for the solder paste to melt and flow, fusing the components to the board.
Hand Assembly: Through-hole components are individually hand-soldered to the board after being inserted into the drilled holes. We use automated soldering machines to ensure consistent quality and reliability.
Testing: Once assembled, the board undergoes rigorous testing to ensure that it functions correctly and meets all customer requirements and specifications. We use a variety of testing methods, including visual inspection, functional testing, and in-circuit testing (ICT).
Quality Control: Throughout the assembly process, we conduct strict quality control checks to ensure that every board meets our high standards for quality and reliability. We employ advanced testing tools and techniques to detect defects such as shorts, opens, and incorrect component values.
Packaging and Shipping: We carefully package the finished boards to protect them during shipping and ensure safe delivery to our customers. We use industry-standard packaging materials and methods, including antistatic bags, foam inserts, and corrugated boxes.
In summary, JHYPCB provides comprehensive PCB assembly services, combining advanced technology with expert hand assembly techniques to deliver high-quality, reliable PCB assemblies. Our strict quality control processes ensure that every assembly meets or exceeds our customers’ expectations, and our efficient packaging and shipping methods ensure safe delivery to all destinations.