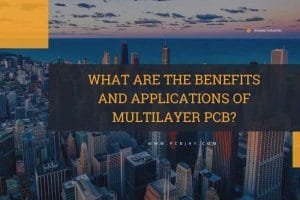
PCB Electronic Manufacturing Services
PCBS FOR THE LED LIGHTING INDUSTRY
With rich experience in LED lighting PCB manufacturing and assembly, JHYPCB is a professional manufacturer that provides comprehensive PCB solutions for the LED lighting industry. Our high-quality PCB products and excellent customer service make us a reliable partner for LED lighting businesses. Contact us now to learn more!
JHYPCB - Your Trusted Partner for High-Quality LED Lighting PCBs
JHYPCB is a professional PCB manufacturer and assembler, providing comprehensive solutions for the LED lighting industry. Our extensive experience in LED lighting PCB manufacturing and assembly enables us to produce high-quality, reliable products that meet the exact requirements of our clients.
At JHYPCB, we are committed to providing exceptional customer service and delivering top-quality products on time and within budget. Our team of experienced engineers and technicians has the knowledge and skills necessary to offer customized solutions that meet your specific needs.
We take pride in our state-of-the-art facilities and advanced equipment that enable us to produce a wide range of PCB products, from low-volume prototypes to large-scale production runs. With JHYPCB as your partner, you can expect personalized service, unparalleled quality, and timely delivery.
Contact us today to learn more about how we can help you with your LED lighting PCB needs.
PCB Applications in LED Lighting Industry
In the LED lighting industry, PCBs are a critical component that help connect LED chips and power sources, ensuring the proper functioning of LED lighting products. Depending on the specific application requirements, LED lighting PCBs can come in various types, such as single-sided, double-sided, multi-layered, and flex-rigid boards.
In addition to traditional circuit connectivity functions, LED lighting PCBs also require thermal management and optical performance, necessitating the use of special materials and surface treatment techniques. As the LED lighting market continues to rapidly expand, demand for high-power, high-reliability, and high-quality LED lighting PCBs is growing. JHYPCB can provide various solutions for LED lighting PCBs to meet customer needs in different application scenarios.
What are LED Lighting PCBs?
LED lighting PCBs are specialized printed circuit boards that are designed and used specifically for LED lighting applications. They play a crucial role in connecting LED chips with other electronic components, such as power supplies, drivers, and controllers, to ensure that the lighting system functions properly.
The primary purpose of LED lighting PCBs is to provide an efficient and reliable platform for delivering power and control signals to the LEDs. They also serve as thermal management solutions by dissipating heat generated by the LED chips and providing insulation for the electrical connections.
With the growing demand for energy-efficient and eco-friendly lighting solutions, LED lighting has become increasingly popular worldwide. As a result, there is a significant demand for high-quality LED lighting PCBs that can meet the industry’s stringent requirements for performance, efficiency, reliability, and cost-effectiveness.
LED PCBs have various specific application areas, some of which include:
Lighting: LED PCBs are widely used in residential, commercial, and industrial lighting systems. They offer efficient energy utilization and longer lifespan while reducing maintenance costs.
Automotive: LED PCBs can be used for automotive front lights, tail lights, interior lighting, and instrument cluster indicator lights. LED PCBs improve energy efficiency and enhance visibility.
Electronics: LED PCBs are also used in electronics such as computers, smartphones, tablets, etc. They provide smaller, lighter, more durable solutions with better energy efficiency.
Medical equipment: LED PCBs can be used in medical equipment like surgical room lighting, examination instruments, and UV sterilizers. They offer high brightness and uniform light as well as less heat generation.
Military and aerospace: LED PCBs can be used in military and aerospace equipment. They provide high reliability, durability, and temperature resistance. Additionally, they can provide high-intensity lighting at night or in low-light environments.
JHYPCB specializes in providing comprehensive LED lighting PCB solutions that cater to a wide range of applications, including strip lights, spotlights, downlights, high-bay lights, street lights, and more. Our extensive experience and advanced facilities enable us to produce customized PCBs that help our customers achieve their unique project goals while ensuring optimal performance and reliability.
The Relationship between PCBs and LED Chips
The relationship between PCBs and LED chips is crucial for the proper functioning of LED lighting products. PCBs provide a platform for connecting LED chips with other electronic components, such as power supplies, drivers, and controllers, enabling them to work together seamlessly.
PCBs play several critical roles in LED lighting applications. First, they serve as an interface between the LED chip and other electronic components, ensuring that the right amount of electrical power is delivered to the LED to achieve optimal performance.
Secondly, PCBs provide thermal management solutions that help dissipate heat generated by the LED chip during operation, which can significantly affect its performance and lifespan. Effective thermal management helps prevent overheating and thermal runaway, leading to more reliable and long-lasting LED lighting products.
Finally, PCBs can also play a significant role in controlling the color, brightness, and intensity of LED lighting products through advanced circuit designs and control systems.
Types and Characteristics of LED Lighting PCBs
LED lighting PCBs come in various types, each with its own unique characteristics that make them suitable for specific LED lighting applications. Below are some of the most common types of LED lighting PCBs and their features:
Single-Sided PCBs: These PCBs have a conductive layer on only one side, making them more cost-effective and easier to manufacture. They are ideal for low-power LED lighting applications, such as night lights, flashlights, and decorative lighting.
Double-Sided PCBs: These PCBs have a conductive layer on both sides, allowing for more complex circuit designs. They are suitable for medium-power LED lighting products, including LED panels, emergency lights, and tube lights.
Multi-Layered PCBs: These PCBs consist of multiple layers of conductive material separated by insulating layers, enabling even more complex circuit designs. They are commonly used in high-power LED lighting products that require efficient thermal management, such as large outdoor displays, stadium lights, industrial lighting, and automotive lighting.
Aluminum-Clad PCBs: These PCBs have an aluminum substrate that provides excellent thermal conductivity, making them ideal for high-power LED lighting applications that need efficient heat dissipation.
Flexible PCBs: These PCBs are made of flexible materials, making them ideal for LED lighting products that require a more creative and flexible design. They are commonly used in curved displays, tape lights, and other LED lighting products that require tight spaces or odd shapes.
At JHYPCB, we offer a wide range of LED lighting PCB solutions that cater to different applications and requirements. Our experienced team can help you choose the most suitable PCB type for your project and provide customized production services to meet your exact needs, ensuring optimal performance and reliability.
Requirements and Advantages of High-Power LED Lighting PCBs
High-power LED lighting applications require specialized PCB designs that can handle the high currents and temperatures generated by the LED chips. Below are some of the special requirements for high-power LED lighting PCBs:
Thermal Management: High-power LED lighting products generate significant amounts of heat, which can affect their performance and lifespan. Effective thermal management is critical to ensure optimal performance and reliability. High-power LED lighting PCBs should be designed with efficient heat dissipation structures, such as thermal vias or metal-core substrates.
Durability and Reliability: High-power LED lighting PCBs must be able to withstand the high currents and voltages generated by the LED chips while maintaining a stable electrical connection. They should also be resistant to environmental factors, such as moisture, dust, or vibration, that may impact their performance and longevity.
Circuit Design: The circuit design of high-power LED lighting PCBs should include features that allow for more efficient and reliable power delivery to the LED chips. This may include thicker copper traces and multiple power planes.
The advantages of high-power LED lighting PCBs include:
Higher Efficiency: High-power LED lighting PCBs can deliver more power to the LED chips, resulting in higher efficiency and brightness.
Longer Lifespan: Effective thermal management and durable construction can prolong the lifespan of high-power LED lighting products.
Customizability: High-power LED lighting PCBs can be customized to meet the specific needs of different applications, ensuring optimal performance and reliability.
JHYPCB's Advantages in the LED Lighting Industry
JHYPCB is a leading PCB manufacturer and assembler that specializes in providing comprehensive solutions for the LED lighting industry. Below are some of the factors that make us stand out from other PCB manufacturers:
- Quality Assurance: At JHYPCB, we have strict quality control procedures in place at every stage of the production process, from raw materials to finished products. We use only high-quality materials and advanced equipment to ensure that our PCBs meet the highest standards of quality and reliability.
- Production Process: Our large-scale automated production lines and advanced equipment enable us to produce PCBs efficiently and deliver them on time. We also maintain a rigorous quality control system throughout the entire production process, ensuring that all our products meet or exceed customer expectations.
- Engineering Team: Our team of experienced engineers provides customized services to meet the specific needs of our customers. From initial design concepts to final product delivery, we work closely with our customers to ensure that their LED lighting PCBs are designed to meet their exact specifications.
- Service Advantage: We offer fast budget quotes, quick design and prototyping services, and urgent order processing to ensure that our customers receive the PCB solutions they need when they need them. We also provide comprehensive technical support and after-sales service to help our customers achieve optimal performance and reliability.
- Environmental Responsibility: We are committed to environmental responsibility and sustainability. We use eco-friendly materials and production processes to reduce our environmental impact and ensure a greener future.
- Competitive Pricing: We offer competitive pricing without compromising on quality or service, making our LED lighting PCB solutions an affordable option for businesses of all sizes.
- Wide Range of Capabilities: We have the capacity to produce various types of LED lighting PCBs, including single-sided, double-sided, multi-layered, aluminum-clad, and flexible PCBs, among others. We can also provide customized solutions based on customer requirements.
- Fast Turnaround Time: With our advanced facilities and experienced team, we can deliver PCB solutions quickly and efficiently, minimizing lead times and ensuring timely delivery.
PCB Manufacturing and Assembly Process
PCB manufacturing and assembly process involves several steps that are critical to the final product’s quality and performance. Below is a detailed explanation of the main steps involved in PCB manufacturing and assembly.
PCB Design and Manufacturing Process
Schematic Design: The initial step in PCB design involves creating a schematic diagram that outlines the circuit’s functionality and components’ placement.
PCB Layout Design: This step involves transferring the schematic design into a physical layout design with specific dimensions, traces, and pads.
PCB Fabrication: After completing the layout design, the next step is to fabricate the PCB using various processes like drilling, plating, etching, and lamination.
Electrical Testing: Once the PCB has been fabricated, it undergoes electrical testing to check for continuity, shorts, and other potential issues.
Component Placement: Once the PCB passes the electrical testing, the components are placed on the board.
Soldering and Inspection: In this step, the components are soldered onto the PCB, and the final product undergoes inspection to ensure proper soldering and overall quality.
There are several surface treatment techniques used in PCB production, including:
Hot Air Solder Leveling (HASL): This technique involves coating the copper surface with tin-lead alloys, providing a uniform surface for component mounting.
Electroless Nickel Immersion Gold (ENIG): ENIG provides a gold-plated surface on the copper, resulting in better corrosion resistance and improved contact reliability.
Organic Solderability Preservatives (OSP): OSP is a surface finish that typically involves applying a thin layer of organic material to protect the copper surface from oxidation.
Surface Mount Technology assembly is the most common method used to assemble PCBs. The following are the main steps involved in SMT assembly:
Stencil Printing: The first step involves applying a layer of solder paste through a stencil onto the board’s surface.
Component Placement: The components are then placed on the board using automated pick-and-place machines.
Reflow Soldering: In this step, the board passes through a reflow oven that melts the solder paste, bonding the components to the board.
Inspection: After soldering, the board undergoes inspection to ensure proper component placement and soldering quality.
FAQs about LED PCB Manufacturing and Assembly
What is an LED PCB?
An LED PCB is a type of circuit board designed specifically for LED lighting applications. These PCBs provide a platform to mount, power, and control LEDs efficiently.
What are some common materials used in LED PCB manufacturing?
Some popular materials used in LED PCB manufacturing include FR-4, aluminum, copper, ceramic, and flexible materials like polyimide.
What is the difference between single-sided and double-sided LED PCBs?
Single-sided LED PCBs have components mounted on only one side, while double-sided PCBs have components mounted on both sides. Double-sided PCBs allow for more space to place components but can be more challenging to manufacture and repair.
How are LED PCBs assembled?
LED PCBs can be assembled using SMT (Surface Mount Technology), through-hole technology, or a combination of both. Once the components are placed on the board, they are soldered to the surface through reflow soldering or wave soldering processes.
What surface finishes are commonly used in LED PCB manufacturing?
Popular surface finishes used in LED PCB manufacturing include HASL, ENIG, and OSP, each with its own advantages and disadvantages depending on the specific application requirements and budget.
How do I choose the right LED PCB manufacturer for my project?
Choosing the right LED PCB manufacturer involves considering factors like quality, pricing, lead times, customization options, and customer service. It's important to do your research, read reviews and ask questions before selecting a manufacturer to ensure that they can meet your specific needs and requirements.
What are the benefits of using LED PCBs in lighting applications?
LED PCBs offer several advantages for lighting applications, including energy efficiency, longer lifespan, improved brightness and color rendering, reduced maintenance costs, and a smaller form factor.
What is the typical lead time for LED PCB orders?
The lead time for LED PCB orders can vary depending on various factors like order size, complexity, and the manufacturer's capacity. However, most PCB manufacturers offer standard lead times between 5-10 business days, with expedited options available for urgent orders.
Can I provide my own LED components for assembly?
Yes, many manufacturers allow customers to provide their own LED components for assembly. However, it's important to ensure that the components are compatible with the LED PCB design and meet the manufacturer's quality standards.
What kind of testing is performed on LED PCBs?
Various tests are performed on LED PCBs during manufacturing and assembly to ensure their quality and reliability, such as electrical testing, thermal imaging, and stress testing.