Electronic Manufacturing Services
PCB Design for Manufacturability Guide
Optimizing Your PCB Design for Efficient and Cost-Effective Manufacturing with DFM
Designing a PCB is a complex process that must take into account various factors such as form factor, function, signal integrity, and cost. However, one key consideration that is often overlooked is design for manufacturability (DFM). DFM is a process that ensures the PCB design is optimized for manufacturing, reducing the risk of errors, delays, and high costs. In this guide, we will discuss the importance of DFM and how to optimize your PCB design for efficient and cost-effective manufacturing.
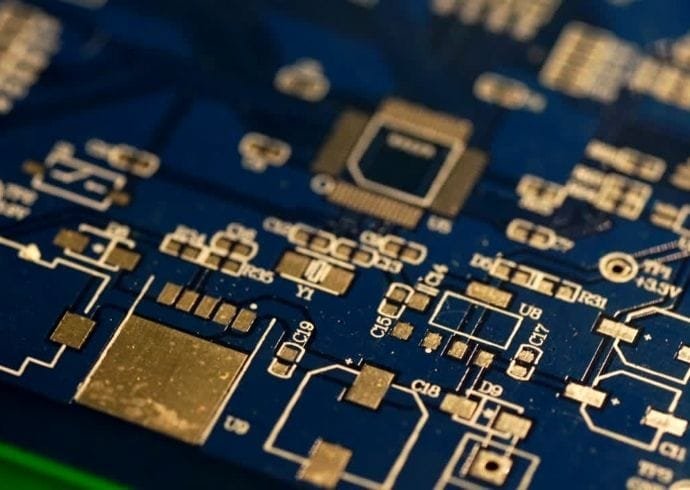
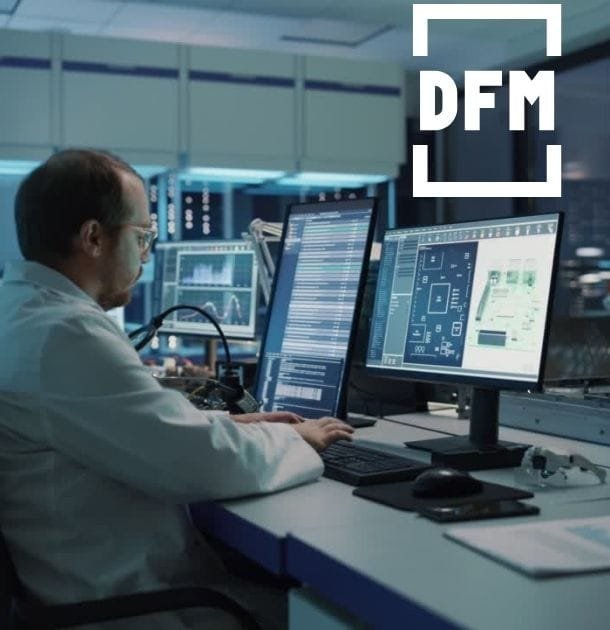
What is DFM and Why is it Important?
When it comes to designing a Printed Circuit Board, Design for Manufacturability is crucial for achieving high-quality manufacturing results. DFM refers to considering the manufacturing process during the design of a PCB.
DFM can help to reduce errors and issues during manufacturing. These issues include difficulty in processing on the assembly line, component mismatch, excessive or insufficient copper, missing solder pads, circuit jumpers, among others. Without DFM, these issues may only be discovered late in the production process, resulting in increased costs, delayed deliveries, and even complete rework.
The goal of DFM design is to ensure that all components can be correctly installed and connected during manufacturing to produce a high-quality PCB. It also aims to optimize production efficiency, save production costs, and increase delivery speed.
Things to Consider When Designing
When designing a printed circuit board, it is essential to consider the manufacturing process in order to ensure high-quality and efficient end products. The following are several things to consider during the design process:
1. Layout and Positioning
The positioning and layout of the components on the PCB needs to be taken into account. It is important to consider the interaction between components, such as avoiding interference between signals and power or forming ground loops between adjacent components. The layout and positioning of components should also be conducive to soldering.
2. Board Thickness and Trace Width
When designing a PCB, the trace width and board thickness must be correctly selected. The trace width should be wide enough to carry the required current, while the board thickness should be thick enough to ensure its strength and durability.
3. Spacing and Arrangement
The spacing and arrangement between components are critical to ensuring a signal chain free from interference. Electronic components should be arranged according to a certain set of rules, making it easy to route and solder.
4. Temperature and Humidity
Temperature and humidity during manufacturing may affect the quality and stability of the PCB. Therefore, it is important to factor these variables into the design process and select appropriate materials to improve the durability of the PCB.
5. Consideration of Abnormal Conditions
Finally, abnormal conditions related to the PCB must be considered, such as battery shorts, open circuits, or component damage. Design solutions for these scenarios should be put in place to avoid any potential issues with the final product.
Considering the above issues during the design process can help ensure reduced errors and issues during the manufacturing process.
What manufacturing requirements need to be followed during the PCB design process?
In the process of PCB design, there are several manufacturing requirements that must be followed to ensure the printed circuit board can be manufactured successfully. These requirements include tolerances and spacing, material and coating selection, minimum line width and spacing, layer stack-up and arrangement, and solder mask and pad size.
Tolerance and spacing: Tolerances and spacing are crucial aspects of PCB design, as they impact the functionality of the board. Tolerances and spacing requirements refer to the minimum and maximum distance that should exist between traces, components, and pads, which are essential in preventing shorts and other errors during board assembly and operation. Designers must consider the physical requirements of components on the board and ensure there is sufficient space between them. Furthermore, they must guarantee that the width and spacing of conductive traces adhere to the tolerances allowed by the PCB manufacturer.
Material and coating selection: Material and coating selection: The selection of PCB materials and coatings can significantly impact the quality of the finished product. This includes choosing the appropriate material for the PCB substrate, determining the thickness of the substrate, and selecting the appropriate solder mask and surface finish. It’s essential to select the right materials and coatings to ensure proper heat dissipation, durability, and corrosion resistance.
Minimum line width and distance: Minimum line width and distance: The minimum line width and distance refer to the minimum size of the traces and spaces that make up the PCB. The minimum line width and spacing will depend on the production capabilities of the PCB manufacturer. PCB designers must consider the manufacturing process capabilities when selecting the minimum spacing and line width.
Layer structure and arrangement: When designing a PCB, it’s important to consider both the layer stack-up and arrangement. The layer stack-up must be carefully arranged to ensure that the routing of individual layers does not interfere with each other. Additionally, the designer must consider the order in which the layers are arranged and how they are interconnected. The number and arrangement of layers depend on the type and complexity of the PCB, and designers should select the appropriate configuration to optimize the PCB’s overall performance and functionality.
Copper pad sizing: Copper pads are essential for component connection and soldering. The sizing of the pads should be carefully selected to ensure the right amount of solder is deposited during assembly.
How to improve the quality of PCB manufacturing?
To improve the quality of PCB manufacturing, there are several key factors to consider:
Single-layer vs. double-layer PCB design: Single-layer PCBs are simpler and less expensive to manufacture, but double-layer PCBs can provide greater functionality in a smaller package. Designers should carefully consider the trade-offs between these two options based on their specific manufacturing and performance needs.
Tolerance analysis and inspection: Designers should ensure that their PCB designs meet all necessary tolerances and specifications to avoid manufacturing defects. Utilizing inspection tools such as automated optical inspection (AOI) or X-ray inspection can also help catch any issues early in the manufacturing process.
Design for Manufacturing process optimization: By optimizing PCB designs for the specific manufacturing processes they will undergo, designers can minimize the risk of errors and increase manufacturing efficiency. This includes considering fabrication processes such as drilling, routing, and soldering.
Importance of material and coating selection: The materials and coatings used in PCB manufacturing can have a significant impact on the overall performance and reliability of the finished product. Designers should carefully select materials and coatings with the properties that match their specific applications.
Avoiding PCB defects: To avoid PCB defects, designers should consider using advanced design software tools to simulate the manufacturing process and catch any potential issues before they arise. Additionally, selecting a high-quality PCB manufacturer with a strong track record of quality assurance can help ensure that the final product is defect-free.
How to choose a PCB manufacturer that suits your needs?
When choosing a PCB manufacturer, there are several key factors to consider in order to ensure that you select a manufacturer that can meet your specific requirements. Here are some considerations to help you choose the right PCB manufacturer:
Reputation and History: You should research a manufacturer’s reputation and history to gauge the level of experience and quality they offer. Look for manufacturers who have a proven track record of delivering high-quality products and have been in business for a significant amount of time.
Capability and Equipment: It’s important to understand the manufacturer’s ability to produce the type and volume of PCBs that you require. Look for a manufacturer who has the right equipment and resources to manufacture your PCBs, including a variety of PCB types, materials, and sizes.
Customization: It’s also important to consider the manufacturer’s ability to customize your PCBs to your specific requirements. This could include custom shapes, drill patterns, and surface finishes.
Delivery Time and Shipping Method: Consider the delivery time and shipping method offered by the manufacturer. Determine whether they can meet your delivery time requirements and what type of shipping options are available, including expedited shipping.
Price and Quality: Finally, consider the price and quality of the manufacturer’s products. Look for a manufacturer who offers a fair price for their products while maintaining a high level of product quality. Don’t sacrifice quality for price, as this could lead to issues with your PCBs down the line.
Free DFM Check Servie
At JHYPCB, we understand the critical importance of DFM for the successful manufacturing of your printed circuit boards. That’s why we offer our comprehensive DFM Check service to ensure that your design is optimized for efficient and cost-effective production. Our team of experienced engineers will thoroughly review your design for manufacturability, identifying potential issues and providing solutions to ensure your PCB is manufactured to the highest standards of quality and reliability. Contact us today to learn more about how our DFM Check service can help streamline your PCB manufacturing process and optimize the performance of your products.
DFM Checklist
DFM Checklist | Type of Check | Description |
---|---|---|
Hole Checks | Plated Hole Size | Verify drilled hole sizes are within the manufacturer’s tolerances for drill size and aspect ratio |
Non-Plated Hole Size | Verify drilled hole sizes are within the manufacturer’s tolerances for drill size | |
Annular Ring | Verify the minimum annular ring is met, and that the ring is symmetrical around the via/hole | |
Hole-to-Copper Clearance | Verify the minimum distance between the hole wall and copper traces and planes | |
Signal and Mixed Layer Checks | Trace Width and Spacing | Verify the trace widths and spacing are adequate for the voltage and current demands |
Trace-to-Trace Clearance | Verify the minimum distance between adjacent copper traces on the same layer | |
Trace-to-Pad Clearance | Verify the minimum distance between copper traces and pads | |
Via-To-Trace Spacing | Verify the minimum distance between vias and copper traces | |
Power/Ground Checks | Decoupling Capacitor Placement | Verify the location of the decoupling capacitors and that they are placed as close to the power and ground pins as possible |
Power/Ground Plane Integrity | Verify the continuity and uniformity of the power and ground planes | |
Power/Ground Pin Sizing | Verify the power and ground pin sizes meet design requirements | |
Power/Ground Layer Separation | Verify the minimum distance between the power and ground layers | |
Solder Mask Checks | Solder Mask Dam Width | Verify the minimum width of the solder mask dam surrounding the pad |
Solder Mask Registration | Verify the alignment between the solder mask and the pad | |
Solder Mask Slivers | Verify the absence of small stray pieces of solder mask on the PCB | |
Silkscreen Checks | Silkscreen Text Size | Verify the size of the text on the silkscreen layer |
Silkscreen Spacing | Verify the distance between the text on the silkscreen layer and other copper features | |
Silkscreen Registration | Verify the alignment between the silkscreen and the intended component or feature on the PCB |
Helpful Resources
- Download - PCB Design for Manufacturing Guidelines
- Download - PCB DFM Checklist
- Unlocking The World Of PCBs: Your Ultimate PCB Terms And Glossary Guide
- PCB FAQs
- Complete Guide for PCB Material
- PCB Layers Explained: Multilayer PCB Stakcup
- What is a printed circuit board (PCB)?
- How Does PCB Impedance Control Work?