PCB Electronic Manufacturing Services
Guidelines for Optimal PCB Design for Assembly (DFA)
Welcome to our comprehensive guide on PCB Design for Assembly (DFA). DFA is the process of designing printed circuit boards (PCBs) with a focus on optimizing ease of assembly and minimizing manufacturing costs. By following DFA guidelines, manufacturers can improve the efficiency and quality of the assembly process, resulting in a higher quality end product. In this guide, we will provide you with an introduction to DFA principles, design guidelines, assembly instructions, material selection, and quality assurance. Whether you are new to PCB design or an experienced engineer, this guide will help you to create designs that are optimized for assembly and manufacturability.
01
What is Design for Assembly?
Design for Assembly (DFA) is a methodology for designing products that are optimized for ease of assembly and manufacturability. It involves considering the assembly and manufacturing processes early on in the design phase, in order to reduce costs, increase efficiency, and improve product quality. Through DFA, designers can reduce the number of components, simplify the assembly process, and minimize the need for specialized tools or skills. Ultimately, DFA aims to create products that are more reliable, less expensive to produce, and easier and faster to assemble.
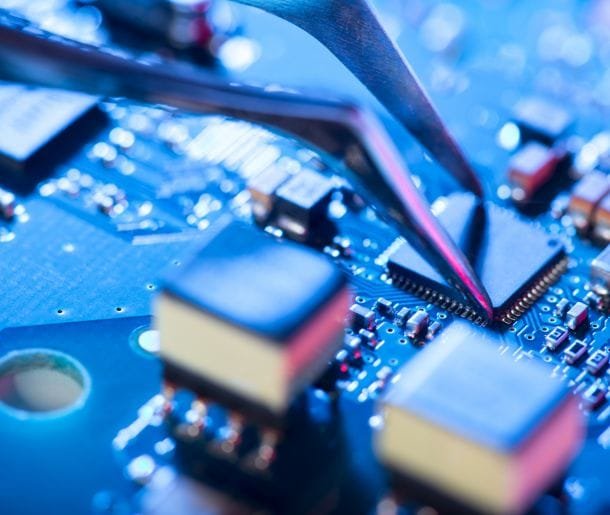
02
Why is DFA Important in PCB Design?
Design for Assembly is an important concept in PCB design that plays a vital role in improving the efficiency and quality of the assembly process. DFA involves designing a product in such a way that it can be easily assembled, reducing the time and cost of production. The importance of DFA cannot be overstated in the modern electronics industry, where time-to-market and cost are critical factors for success.
One of the key benefits of DFA is that it enables PCB designers to consider the assembly process during the design phase. By doing so, they can identify potential assembly issues and make design changes that will simplify the assembly process. This can result in significant time and cost savings, as well as improved product quality.
Another important aspect of DFA is that it can help to reduce the risk of errors and defects in the assembly process. By designing products that are easy to assemble, manufacturers can reduce the likelihood of human error, which can result in faulty products and costly rework. By improving the assembly process, manufacturers can also improve the consistency and quality of the final product.
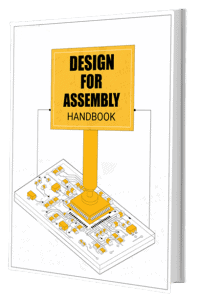
Design for Assembly Handbook Download
- Definition of DFA
- Principles of DFA for PCBs
- Reduction & Combination
- Standardization
- Minimization of Risk
- Simplification
- Clarity
- Understanding JHYPCB’s Assembly Capabilities
03
Design Guidelines
PCB assembly is a critical step in the overall electronic product manufacturing process. A well-designed PCB can significantly improve the overall efficiency, quality, and reliability of the final product. This section outlines the design guidelines for efficient DFA in PCB design.
Design principles for DFA in PCB design:
- Keep the PCB design simple and uncluttered. Avoid complex and dense designs that can make it difficult and time-consuming for assembly.
- Follow the PCB design guidelines provided by your manufacturer. This ensures that the PCB design is compatible with the manufacturing process and minimizes errors during the assembly process.
- Use standard components wherever possible. Standard components are readily available, easy to source, and familiar to the assembly personnel.
- Avoid the use of non-standard fasteners. They can be difficult to source and can cause delays in the assembly process.
- Minimize the use of through-hole components. Through-hole components require extra drilling, which increases the assembly time, cost, and complexity.
Design considerations for different assembly processes:
1. Surface Mount Technology (SMT) Assembly
SMT assembly is a popular and widely used assembly process for PCBs. The following design considerations should be taken into account for SMT assembly:
– Keep the minimum pitch between components to at least 0.5 mm.
– Use standard SMT component packages whenever possible.
– Avoid large components that can block access to nearby components.
– Use a uniform pad size and shape for all SMT components.
Pin-Through-Hole (PTH) assembly is a traditional assembly process that involves inserting components through holes drilled in the PCB. The following design considerations should be taken into account for PTH assembly:
– Use standard hole sizes, and ensure adequate clearance between the hole and the component lead.
– Ensure that the component leads are straight and have a uniform length.
– Avoid placing components too close to each other, which can lead to short circuits.
– Use a uniform pad size and shape for all PTH components.
Optimizing for assembly ease, cost, and quality:
- Minimize the number of components and assembly steps.
- Use machines and equipment that reduce manual labor and increase efficiency.
- Avoid design changes after the manufacturing process has begun, as they can cause delays and additional costs.
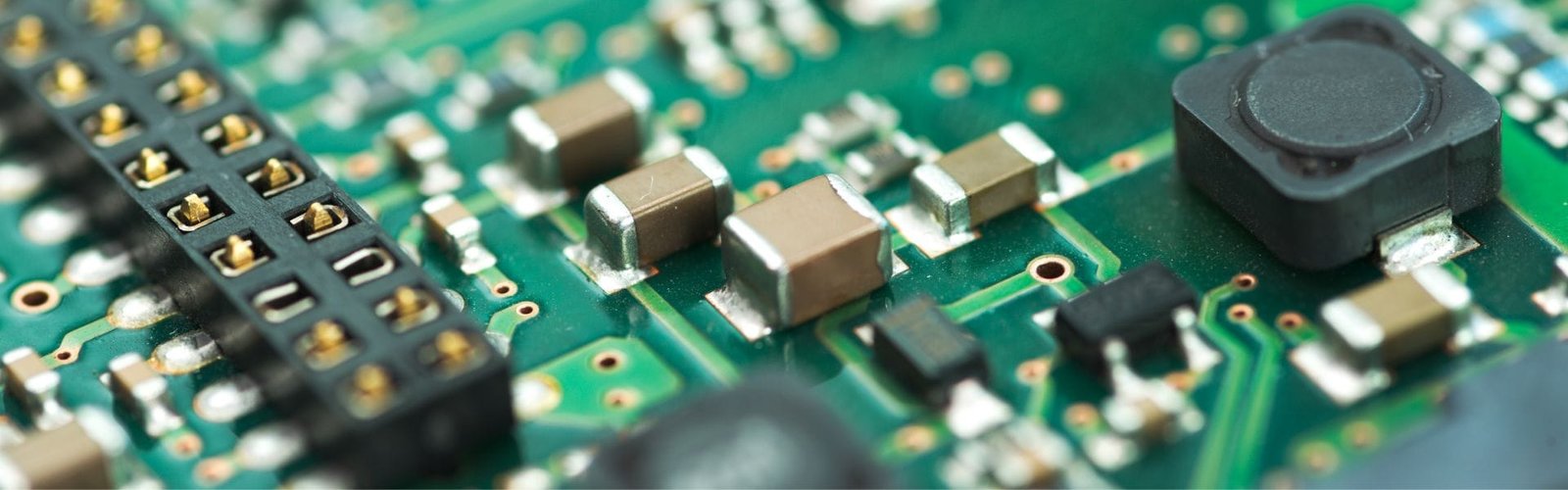
Assembly Guidelines
The assembly process is a critical step in PCB manufacturing. Proper setup and optimization of the assembly process can significantly impact the quality and efficiency of the final product. Here are some best practices for assembly process setup:
1. Preparing the Work Environment
Before starting the assembly process, it’s important to ensure that the work environment is suitable. This includes maintaining a clean and organized workspace, controlling temperature and humidity, and providing adequate lighting.
2. Components Procurement and Handling
The quality and reliability of the final product heavily depend on the quality of the components used. Therefore, it’s essential to procure high-quality components from reputable suppliers. In addition, proper handling techniques should be employed to prevent electrostatic discharge (ESD) and to avoid any damage to the components.
3. Process Flow Optimization
Process flow optimization is key to improving assembly quality and efficiency. It involves identifying and eliminating any bottlenecks in the process, reducing the setup time, and streamlining the workflow. Some best practices for process flow optimization include:
– Standardizing the assembly process: Standardizing the assembly process can make it easier to train staff and ensure consistency in the quality of the final product.
– Automated assembly: Using automated assembly equipment can help improve efficiency, reduce costs, and reduce the risk of errors.
– Optimizing the production line: Optimizing the production line by using lean principles can help identify areas of waste and inefficiency and implement improvements to increase overall efficiency.
Implementing these best practices for assembly process setup, components procurement and handling, and process flow optimization can help improve the quality and efficiency of the final product, resulting in increased customer satisfaction, reduced costs, and increased profitability.
Looking for a Reliable PCB Assembly Manufacturer?
Material Selection
When designing a printed circuit board, the selection of materials and components is crucial for the quality and reliability of the final product. The materials and components used in the design affect the electrical performance, mechanical stability, and durability of the PCB.
Component attributes and selection considerations:
When selecting components for a PCB, there are several attributes to consider, such as the form factor, electrical specifications, package type, and environmental requirements. The form factor refers to the physical shape and size of the component, which should fit well with the overall design of the PCB. Electrical specifications include the ratings for voltage and current, as well as the tolerance and temperature range. The package type refers to the way the component is packaged and mounted on the PCB, such as surface mount technology or through-hole mounting. Environmental requirements include the temperature range, humidity, and vibration conditions that the PCB will be subjected to in its operational environment.
BOM and supply chain optimization for efficient material sourcing:
The Bill of Materials is a list of all the materials and components needed to build the PCB. Optimizing the BOM and supply chain can help reduce costs and improve efficiency in material sourcing. One way to optimize the BOM is to minimize the number of unique components used, as this simplifies the procurement process and allows for bulk ordering. Another way to optimize the supply chain is to work with reliable suppliers who can provide high-quality components at competitive prices. It is also important to consider lead times and stock levels when selecting suppliers, as this can affect the overall production schedule and delivery time to customers.
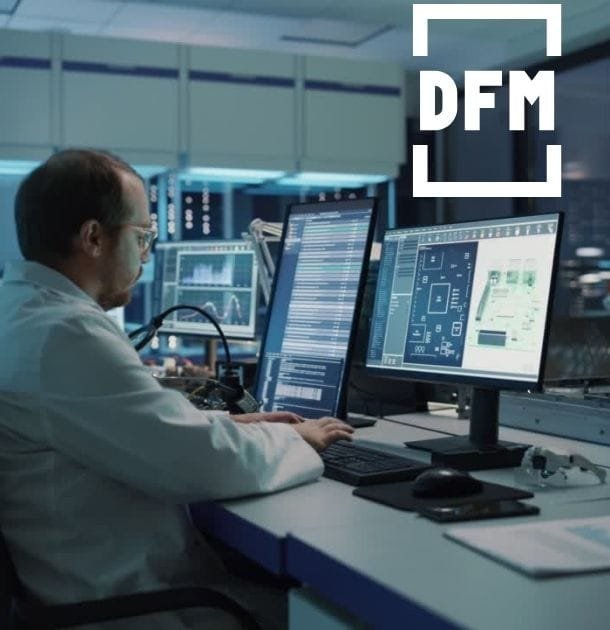
PCB Design For Manufacturability Guide
The purpose of this Design for Manufacturability (DFM) guide is to assist JHYPCB’s customers in designing PCBs that can be manufactured quickly and efficiently. These DFM guidelines define the various tolerances, rules, and testing procedures JHYPCB adheres to during PCB manufacturing.
In terms of both cost and efficiency, it is beneficial to all parties involved if these issues can be addressed during the design stage rather than during production. By providing this guide, we hope to avoid the potential scenario where our client has finished designing a board but must later revise their design due to facility limitations.
Quality Assurance
Quality assurance is a critical step in the PCBA manufacturing process, ensuring that the final assembled product meets the required quality standards. In this section, we will discuss the quality assurance process in PCBA, quality checks during the assembly process, and fault finding & troubleshooting strategies for improving assembly product quality.
Overview of Quality Assurance Process in PCBA
The quality assurance process in PCBA is a comprehensive approach to ensure that the assembled product meets the required quality standards. The quality assurance process includes various steps, such as initial inspection, in-process inspection, and final inspection.
-Initial Inspection: The first step in the quality assurance process is the initial inspection, where the manufacturer performs a visual inspection to verify that the components and PCBs are in good condition and meet the specified standards.
-In-Process Inspection: During the assembly process, several inspections are performed to ensure that the product is assembled correctly, including component placement inspection, soldering inspection, functional testing and inspection, and optical inspection.
-Final Inspection: The final inspection includes a visual inspection, functional testing, and optical inspection to ensure that the PCBA meets all the required quality standards.
Quality Checks During the Assembly Process
Performing quality checks during the assembly process is critical to ensure the assembled product meets all the quality standards. Here are some quality checks that should be performed during the assembly process:
-Component Placement Verification: Verify that each component is placed correctly and in the right orientation.
-Soldering Inspection: Perform a visual inspection to verify that each solder joint is smooth and shiny without any visible defects, such as solder bridging or insufficient solder.
-Functional Testing: Test each completed subassembly to ensure that it meets the required specifications.
-Optical Inspection: Perform an optical inspection to verify that all the components are placed correctly and that there are no visible defects.
Fault Finding & Troubleshooting Strategies for Improving Assembly Product Quality
A comprehensive fault finding and troubleshooting strategy is necessary to improve assembly product quality. Here are some strategies that can be used to improve assembly product quality:
-Identifying the root cause of the problem is critical to improving assembly product quality. Once the root cause of the problem is identified, a corrective action plan can be developed to prevent recurrence.
-Regularly maintaining the assembly equipment and verifying that it is performing correctly can minimize the chances of defects.
– Maintaining a detailed QC (Quality Control) record of each product can help reveal trends and problem areas that need corrective action.
-Providing regular training to assembly operators can help them understand the importance of quality and equip them with necessary skills to perform their duties effectively.
In Conclusion, the quality assurance process in PCBA is a critical step to ensure that the final assembled product meets all the required quality standards. By performing regular quality checks during the assembly process and implementing a comprehensive fault finding and troubleshooting strategy, manufacturers can improve assembly product quality and ultimately improve customer satisfaction.
Conclusion
In conclusion, PCB design is a complex process that requires careful consideration of several factors, including signal integrity, power distribution, and mechanical constraints. To ensure success, designers must follow best practices and principles to minimize errors and increase efficiency.
One of the critical factors to consider is Design for Assembly, where the design is optimized for ease of assembly and efficient manufacturing. DFA principles focus on minimizing the number of components, optimizing component placement, and ensuring access to components for testing and repair. By following these principles, designers can reduce assembly time, minimize errors, and reduce assembly costs.
Another vital aspect of PCB design is Design for Manufacturing. DFM guidelines ensure that the design can be efficiently manufactured, with minimal waste, and meet critical requirements such as quality, reliability, and cost-effectiveness. At JHYPCB, we offer DFM checks as part of our manufacturing process, ensuring that your design meets our manufacturing guidelines and reduces the risk of errors and delays.
In addition to our DFM services, we also offer Design for Assembly checks, where our team will review your design and suggest alterations to optimize assembly processes and efficiency. By taking advantage of our DFA and DFM checks, you can rest assured that your design will be manufactured to the highest quality standards.
At JHYPCB, we are committed to providing high-quality manufacturing services and support to help you achieve your design objectives.