Flexible PCB Materials
What is Adhesive / Bonding Sheet in Flexible Circuit Board?
Flexible circuits utilize a bonding sheet, also known as sheet adhesive, pure adhesive, or adhesive, that comprises of adhesive applied on a release paper.
Table of Contents
Add a header to begin generating the table of contents
Bonding Sheet, Sheet Adhesive, Pure Adhesive, FPC Adhesive?
Bonding Sheet, also known as Sheet Adhesive, Pure Adhesive, or simply Adhesive, is a crucial component in the fabrication of flexible circuits. It refers to a stand-alone adhesive coated on release paper that is primarily used to bond flexible inner layers or rigid cap layers in multilayer lamination.
The main purpose of the Bonding Sheet is to provide a strong and reliable bond between different layers of a flexible circuit, ensuring its integrity and durability. Without it, the flexible circuit would easily break down or delaminate, leading to malfunction or failure.
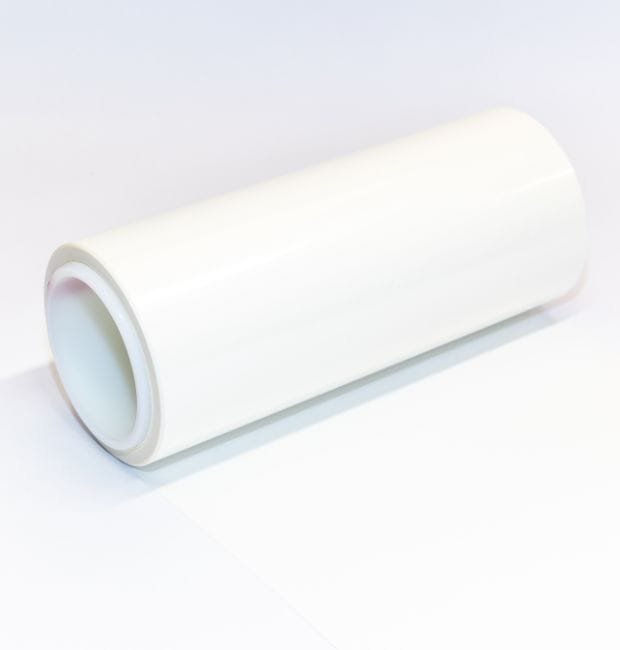
Applications of Bonding Sheet
Bonding Sheet is widely used in the fabrication of flexible circuits, particularly in the following applications:
Bonding flexible inner layers: Bonding Sheet is used to bond flexible inner layers of a flexible circuit together, forming a multilayer structure. This is critical in the production of flexible circuits that need to fit into a small space or have a complex shape.
Bonding rigid cap layers: A bonding Sheet is also used to bond a rigid cap layer to a flexible circuit in multilayer lamination. This provides additional mechanical strength and protection to the flexible circuit, making it more resistant to bending, twisting, or impact.
Bonding flexible circuits to rigid-flex boards: A bonding Sheet is essential in bonding flexible circuits to rigid-flex boards, which are used in applications that require both flexibility and rigidity, such as aerospace, medical devices, and consumer electronics.
Bonding stiffeners and heat sinks: A bonding Sheet can be used to attach stiffeners and heat sinks to a flexible circuit, providing additional support and dissipating heat more effectively.
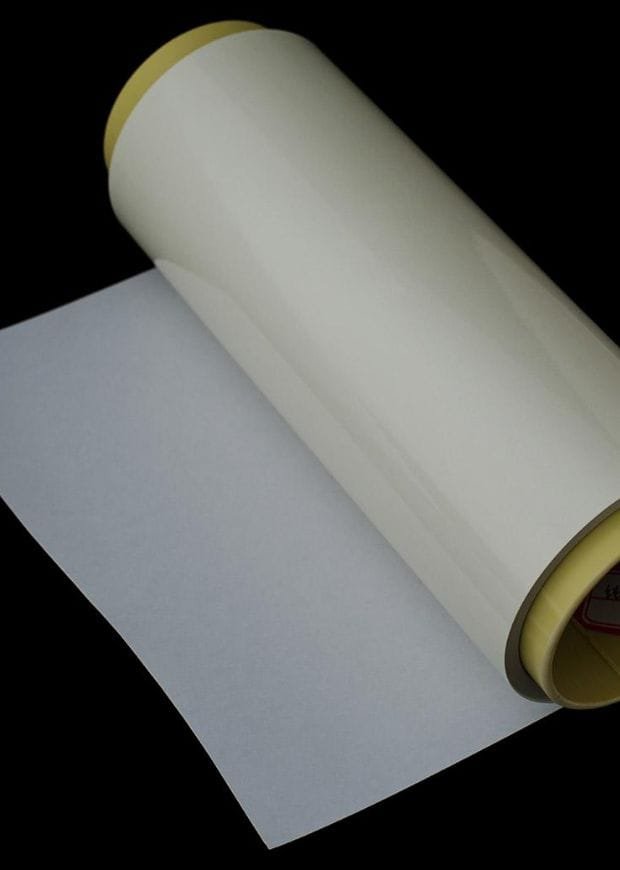
Features and Benefits of Bonding Sheet
Bonding Sheet offers various features and benefits that make it the preferred option for bonding flexible circuits.
Adhesive properties: The bonding Sheet has excellent adhesive properties, providing a strong and reliable bond between different layers of a flexible circuit. It also provides excellent adhesion to a wide range of substrates, including metals, plastics, and composites.
Compatibility with various materials: The bonding Sheet is compatible with various types of materials, including polyimide, polyester, and other flexible substrates. This makes it a versatile option for different types of flexible circuits.
Ease of use: The bonding Sheet is easy to use, as it comes with a release paper that can be easily removed when needed. It also has a long shelf life, allowing for easy storage and handling.
Cost-effectiveness: A bonding Sheet is a cost-effective option for bonding flexible circuits, as it eliminates the need for complex and expensive bonding processes, such as vacuum lamination or pressure bonding.
Types of Bonding Sheet
There are various types of Bonding Sheet, each suitable for specific applications.
Pure Adhesive: This is the most common type of Bonding Sheet, consisting of a pure adhesive coated on a release paper. It provides excellent bonding strength and is suitable for most applications.
Toughened Adhesive: This type of Bonding Sheet contains toughening agents that improve the impact resistance and durability of the adhesive. It is suitable for applications that require higher mechanical strength and resistance to shock or vibration.
Modified Acrylic Adhesive: This type of Bonding Sheet contains modified acrylics that provide excellent adhesion to a wide range of substrates, including low surface energy materials. It is suitable for applications that require excellent bonding strength and compatibility with different materials.
What’s the Adhesive Material in the Bonding Sheet?
In FPC manufacturing, a variety of adhesives are used, including polyesters (PET), polyimides (PI), acrylics and modified epoxies. Each type has its own set of advantages and disadvantages, which depend on the specific application. For example, polyester adhesives are inexpensive, but they do not perform well in high temperature environments and have relatively low bond strength. They are often used when the substrate material is also polyester and in applications where temperature extremes or significant forces are not present.
In contrast, polyimide adhesives are more expensive, but they perform exceptionally well in high temperature environments and are frequently used in demanding multi-layer circuit applications in the defense, aerospace, and satellite sectors. Other factors, such as cost and ease of use, must also be considered when choosing an appropriate adhesive. A summary of the advantages and disadvantages of each type of adhesive is provided in the table below.
Property | Polyimide | Polyester | Acrylic | Modified Epoxy |
---|---|---|---|---|
Peel Strength (lb/in.) | 2.0-5.5 | 3-5 | 8-12 | 5-7 |
After Soldering | No Change | No Change | 1-1.5x higher | variable |
Low Temperature Flex | all pass IPC-650 2-8.18@5+ | |||
Adhesive Flow | <1mil | 10mils | 5mils | 5mils |
CTE | <50ppm | 100-200 | 350-450 | 100-200 |
Moisture Absorption | 1-2.5% | 1-2% | 4-6% | 4-5% |
Chemical Resistance | good | fair | good | fair |
Dielectric Constant @100 kHz | 3.5-4.5 | 4-4.6 | 3-4 | 4 |
Electrical Strength (kV/mil) | 2-3 | 1-1.5 | 1-3.2 | 0.5-1 |
FAQs on Bonding Sheet
What is a Bonding Sheet and what is its purpose?
A Bonding Sheet is a thin, double-sided adhesive film that is used to bond various materials together in the electronics manufacturing industry. Its purpose is to provide a reliable and strong bond that can withstand the stresses of use and environmental factors.
What are Bonding Sheets made of?
Bonding Sheets can be made of a variety of materials, including acrylic, PET, PI, modified epoxies, and thermoplastic. The type of material used depends on the specific application and performance requirements.
What are the advantages of using Bonding Sheets?
Bonding Sheets offer several advantages over other bonding methods, including ease of use, versatility, and the ability to provide a strong and reliable bond. They are also less messy than liquid adhesives and can be applied quickly and easily.
How do you choose the right Bonding Sheet?
Choosing the right Bonding Sheet depends on several factors, including the materials being bonded, the surface preparation, the application requirements, and the cost. It is important to select a Bonding Sheet that is compatible with the materials being bonded and that has the necessary performance characteristics.
How do you handle and store Bonding Sheets safely?
Bonding Sheets should be stored in a cool, dry place away from direct sunlight and heat sources. They should be handled with care and stored in their original packaging to prevent contamination and damage. It is also important to wear protective gloves and eyewear when handling Bonding Sheets to avoid skin or eye irritation.
Bonding Sheet is typically supplied on rolls that are 24 inches (610mm) wide by 250 feet (76m) long and come with nominal 3 inch (76mm) cores. However, narrower widths or cut sheets can also be obtained by special order. Proper storage of FPC bonding sheets requires the original packaging to be retained and the product to be kept at temperatures between 4 and 29 degrees Celsius (40-85 degrees Fahrenheit) with maximum humidity below 70%. It is important to ensure that the product is kept dry, clean, and well-protected, and not frozen in order to maintain its intended performance.
What is the thickness of bonding sheet
In the process of coverlay and bonding sheet unit conversion, flex PCB manufacturers often use 1mil = 25μm (micron) as the standard. When selecting adhesive thickness, it is important to consider the trace thickness and remaining copper rate to ensure the bonding sheet's adhesive can fully cover and bond the copper features. Therefore, thickness parameters such as 12μm (0.5mil), 25μm (1mil), 50μm (2mil), 75μm (3mil), and 100μm (4mil) are all worth considering when selecting coverlay and bonding sheet.
Are bonding sheets environmentally friendly?
The environmental friendliness of bonding sheets depends on the specific material they are made of. Some bonding sheet materials, such as silicone and acrylic adhesives, are commonly used because they have low environmental impact. However, other bonding sheet materials, such as those containing ozone-depleting chemicals or hazardous substances, can have negative environmental impacts if not properly handled and disposed of. It is important to carefully select and handle bonding sheets to minimize their environmental impact.
How do bonding sheets compare to other methods of adhesive bonding?
Bonding sheets have some advantages over other methods of adhesive bonding, such as liquid adhesives or tapes. One significant advantage is that bonding sheets offer consistent adhesive coverage, which can lead to more reliable and consistent bonding. Additionally, bonding sheets can be used to bond irregular or difficult-to-reach surfaces, such as curved or uneven surfaces. Bonding sheets are also easy to handle and apply, requiring little to no special equipment.
Another advantage of bonding sheets is their versatility. They can be used in a wide range of applications and industries, from electronic assembly to automotive manufacturing to construction.
However, bonding sheets may not be suitable for all applications. In some cases, liquid adhesives may offer stronger bonding than bonding sheets. Additionally, bonding sheets may not be suitable for high-temperature applications or applications requiring a high degree of chemical resistance. Ultimately, the best method of adhesive bonding depends on the specific requirements of the application.
Can bonding sheets be removed or repositioned once they are applied?
In general, bonding sheets are not designed to be easily removable or repositionable once they have been applied. They are intended to provide a strong, permanent bond between two surfaces. However, it is possible to remove or reposition bonding sheets if necessary, although it may require some effort and may not always be successful. Care should be taken when attempting to remove or reposition bonding sheets to avoid damaging the surfaces they are attached to. If you need a material that can be easily removed or repositioned, you may want to consider using a different adhesive or fastening method.
What is the cost of bonding sheets and how do they compare to other adhesive bonding methods?
The cost of bonding sheets can vary depending on factors such as the size, thickness, and material of the sheet, as well as the quantity purchased. In general, bonding sheets are considered a cost-effective alternative to traditional adhesive bonding methods such as liquid adhesives or tapes. They offer a number of advantages, including good consistency, wide applicability, and ease of handling, which can help to reduce labor costs and improve productivity. Additionally, because they are pre-cut to size, there is less waste compared to liquid adhesives, which can be a cost savings as well. However, it is important to note that bonding sheets may not be suitable for all applications, particularly those requiring high-strength bonding or resistance to high temperatures or chemicals, where more specialized adhesive bonding methods may be necessary.
Explore Our PCB Fabrication Services
Related Reading
- What Is A Printed Circuit Board (PCB)?
- PCB Layers Explained: Multilayer PCB Stakcup
- A Comprehensive Guide To Copper Clad Laminate (CCL) Used In PCB Fabrication
- Flexible Copper Clad Laminate (FCCL)
- PCB Materials Complete Guide To PCB Copper Foil
- Resin Coated Copper (RCC)
- PCB Prepreg: Definition, Types, Applications, Thickness, And Related Questions Answered.
- PET vs. PI: the Differences Between these Materials for Flex PCBs
- Comprehensive Guide to Manufacturing Flex PCB with Stiffener
- What are the Different Types of Flexible Circuits?
- What are the Materials for Flex Circuits?
- Flexible PCBs: Advantages And Disadvantages