What Are Halogen-Free PCBs and Why Are They Important?
Printed circuit boards serve as the backbone of electronics, connecting components through conductive tracks and pads. PCBs have traditionally relied on brominated and chlorinated flame retardants for decades to meet fire safety standards. However, halogens like bromine and chlorine can produce toxic fumes when burned, posing environmental and health hazards. This has led to growing demand for eco-friendly “halogen-free” PCB materials.
Halogen-free PCBs replace brominated and chlorinated compounds with organic phosphorus-based flame retardants. This alternative system enables environmentally responsible PCB production without compromising fire safety or performance. As halogen-free PCB laminates and prepregs gain popularity, manufacturers must understand the benefits, material options, and design considerations of transitioning away from halogenated materials.
This blog post will provide a comprehensive overview of halogen-free PCB technology. We’ll define what halogen-free means, analyze the pros and cons, and discuss best practices for implementing halogen-free materials. Whether you’re an electronics producer looking to go green or a PCB designer wanting to learn about the newest eco-standards, this guide has you covered on the ins and outs of halogen-free PCBs. Read on to learn all about this important trend toward sustainable electronics production.
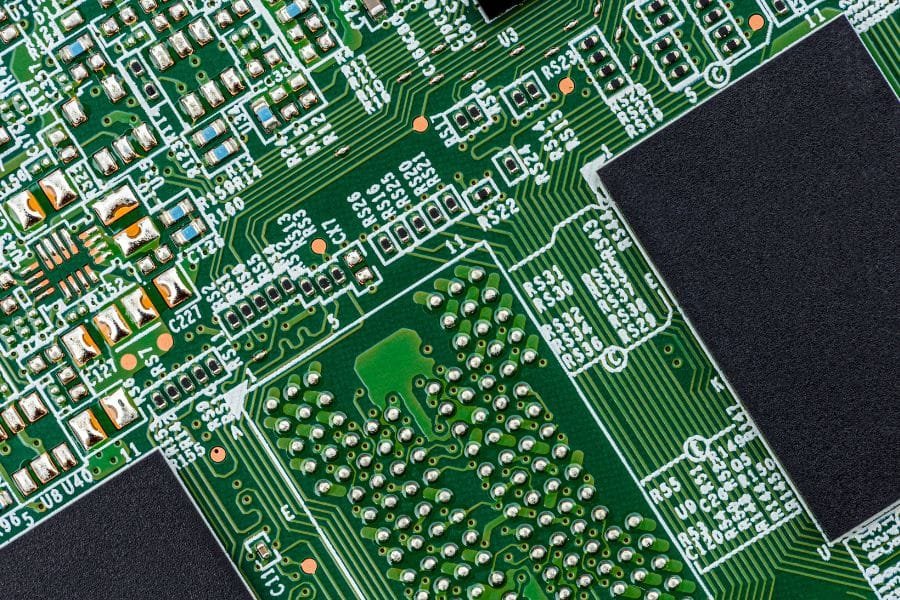
What Are Halogens and Why Avoid Them?
Halogens refer to the elements fluorine, chlorine, bromine, iodine, and astatine. Within the context of PCB manufacturing, the halogens of primary concern are chlorine and bromine. These two elements have been extensively used in PCB laminates as a flame retardant.
The brominated and chlorinated flame retardant systems used in traditional PCB materials come under variants such as polybrominated biphenyls (PBBs), polybrominated diphenyl ethers (PBDEs), and polyvinyl chloride (PVC). When burned, these halogenated compounds release hazardous substances, including dioxins, furans, and acid gases.
Exposure to the toxic fumes released by halogenated flame retardants can pose significant risks:
- Environmental hazards due to bioaccumulation up the food chain.
- Health issues like endocrine disruption, reproductive damage, cancer, or impaired neurological development.
- Corrosion of electronic equipment due to the spread of acid gas deposits.
With awareness of these concerns growing, electronics manufacturers are now transitioning to halogen-free materials to mitigate environmental, health, and reliability risks. Let’s explore the benefits of eliminating halogens in further detail.
Recommend Reading: Halogen-free Electronics
Key Benefits of Halogen-Free PCB Materials
Halogen-free PCB laminates and prepregs offer three main advantages over traditional halogenated materials:
Improved Fire Safety and Reduced Toxicity: Halogen-free PCBs must meet the same flammability standards as other PCBs. But when burned, halogen-free laminates do not emit corrosive fumes, smoke, or toxic gases. Removing halogens significantly reduces fire toxicity risks.
Compliance With Environmental Regulations: With growing environmental awareness, regulatory agencies globally are establishing stricter controls over halogen use. Halogen-free PCBs ensure compliance with initiatives like the WEEE and RoHS directives, which limit hazardous substances.
Enhanced Reliability and Compatibility: The corrosive gases released by burning halogenated materials can damage electronics through metal corrosion. Halogen-free PCBs avoid this problem, enhancing the reliability and lifespan of circuits.
By shifting to halogen-free materials, PCB designers and manufacturers gain an eco-friendly solution without compromising critical fire safety, performance, or longevity requirements.
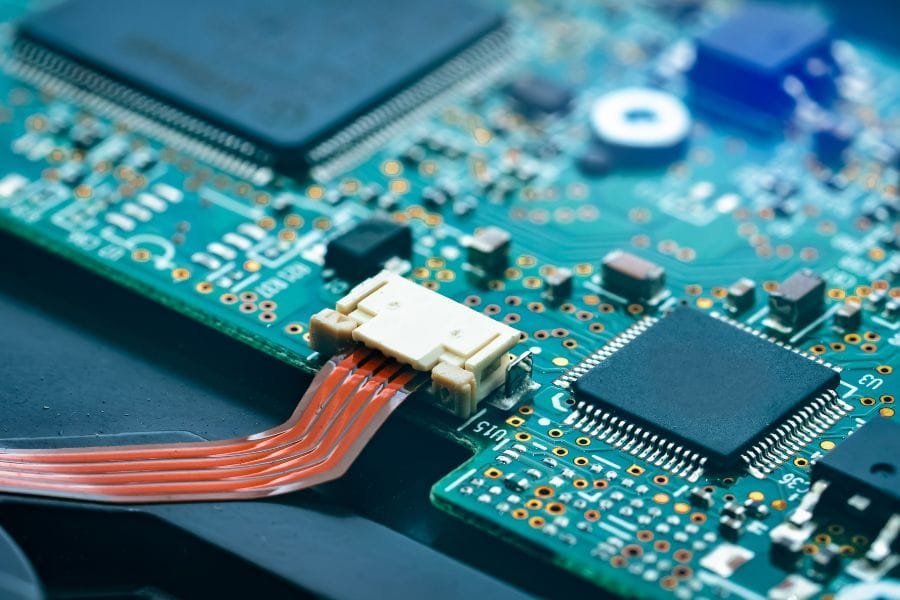
Halogen-Free Laminate and Prepreg Options
A variety of halogen-free resin systems have been formulated as eco-friendly substitutes for traditional halogenated laminates:
Epoxy: Halogen-free epoxy retains the superior mechanical and electrical properties of standard FR-4 epoxy laminates. Popular variants include Nelco’s N4000-13SI and Panasonic’s Panasonic MEGTRON 6.
Polyimide: Halogen-free polyimide laminates like DuPont’s Kapton offer extreme temperature tolerance and dielectric performance, though at a higher cost.
Hydrocarbon: These laminates use thermoplastic or thermoset hydrocarbons as the resin system for low cost and fairly good electrical characteristics. Rogers’ RT/duroid 5870 is a common halogen-free hydrocarbon material.
Cyanate Ester: Cyanate ester resins provide excellent heat resistance and low dielectric loss. Major brands include Isola, Taconic, and Arlon.
Other Options: Additional halogen-free alternatives continue to emerge, including PPE, PPO, silicone-based materials, and ceramic-filled composites.
On the prepreg side, major suppliers like Panasonic, Isola, Park/Nelco, and Rogers offer a wide selection of halogen-free prepreg materials to match various laminate types. These include epoxy, polyimide, and other resin systems.
With this range of material choices, PCB designers can select the optimal halogen-free laminate and prepreg for their performance, cost, and compliance needs.
Design Considerations for Halogen-Free PCBs
While halogen-free PCB materials provide environmental and health benefits, they can impact certain design and fabrication considerations:
Electrical Performance: The dielectric constant may be slightly higher in some halogen-free laminates, affecting impedance tolerances and signal integrity. This requires attention during layout.
Thermal Properties: The thermal conductivity of halogen-free materials can differ from traditional FR-4 laminates. Thermal analysis is advised to ensure sufficient cooling.
Mechanical Characteristics: Factors like CTE and modulus can vary across halogen-free laminates. Performance testing is recommended to optimize reliability.
Drillability and Routability: Halogen-free materials may require adjusted drill shapes, smaller bits, or lower feed rates. Consult your PCB manufacturer for advice.
Solder Mask Adhesion: Added surface preparation or use of adhesion promoters may be necessary to ensure good solder mask adhesion.
Testing: Additional testing like TDDB (Time-Dependent Dielectric Breakdown) helps validate the long-term reliability of new halogen-free materials.
Engineers can successfully leverage halogen-free laminates without compromising quality or manufacturability by collaborating early with your PCB manufacturer and adhering to any special design rules.
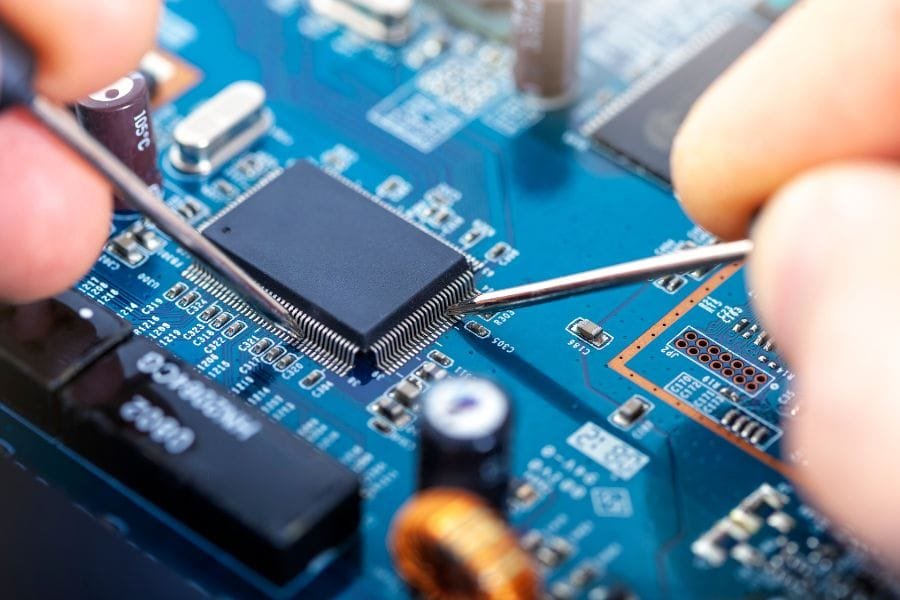
The Future of Halogen-Free PCB Technology
Halogen-free PCBs represent the future of environmentally sustainable electronics manufacturing. Here are some projections on where this technology is headed next:
Growth Projections: The halogen-free PCB market is forecast to grow steadily at around 3% CAGR over the next five years as global environmental regulations expand.
Legislative Initiatives: Tighter restrictions on halogen use are forthcoming in the EU’s RED and RoHS Directives, along with bans in specific U.S. states. This will further increase demand.
Industry Commitments: Major manufacturers like Apple, Samsung, Sony, and others have publicized commitments to phase out halogenated flame retardants and transition to greener alternatives.
Technology Innovations: R&D continues to enhance the electrical performance of halogen-free materials while reducing costs. This will improve adoption rates moving forward.
In summary, global trends point toward halogen-free PCBs becoming the new normal in responsible electronics production. PCB designers and fabricators should prepare now to take advantage of this shift toward more sustainable, environmentally progressive manufacturing practices.
Conclusion: The Benefits of Going Halogen-Free
Halogen-free PCB technology represents an important step forward for the electronics industry. Manufacturers can produce greener PCBs without compromising performance or fire safety by phasing out hazardous brominated and chlorinated flame retardants.
Halogen-free laminate and prepreg materials continue to improve properties and decrease costs. These innovative materials are poised to become the new standard with their reduced environmental impact and enhanced reliability.
PCB designers and fabricators should actively investigate halogen-free options for their boards. This will future-proof products against tightening regulations while meeting rising eco-standards from consumers. Consult your material suppliers and manufacturing partners to learn about the best halogen-free solution for your application.
The electronics industry has reached an inflection point where sustainability and business interests align. Now is the time to go halogen-free. With some thoughtful design adjustments, you can transition to safer, greener PCB materials that benefit both profits and the planet. Our team of engineers is always available to help assess your best path forward. Reach out today to start the discussion.