Table of Contents
Introduction
In the ever-evolving world of electronics, Printed Circuit Boards (PCBs) serve as the backbone of modern devices. Among the various types of PCBs, rigid PCBs stand out for their durability and reliability. At JHYPCB, a leading PCB manufacturer in China, we understand the critical role that rigid PCBs play in ensuring the functionality and performance of electronic products.
This article delves into the intricacies of rigid PCB electrical performance, a crucial aspect that determines the overall efficiency of electronic devices. We’ll explore key parameters such as impedance, capacitance, and inductance, which significantly impact the electrical characteristics of rigid PCBs. Moreover, we’ll discuss optimization techniques that can enhance the performance of your PCBs, ultimately leading to more reliable and efficient electronic products.
Whether you’re an electronics engineer, a product designer, or simply curious about the inner workings of PCBs, this comprehensive guide will provide valuable insights into rigid PCB electrical performance. By the end of this article, you’ll have a solid understanding of how to optimize your rigid PCBs for superior electrical performance.
What is Rigid PCB Electrical Performance?
Rigid PCB electrical performance refers to the board’s ability to effectively and accurately transmit electrical signals between components. This performance is crucial for the overall functionality and reliability of electronic devices. At JHYPCB, we place great emphasis on optimizing the electrical performance of our rigid PCBs to ensure the best possible outcomes for our clients.
Several key factors influence rigid PCB electrical performance:
- Impedance: This measures the resistance to electrical signal flow through the PCB. Proper impedance control is essential for maintaining signal integrity and minimizing distortion. Factors affecting impedance include:
- Trace width and thickness
- Dielectric constant of the PCB material
- Distance between signal traces and ground planes
- Capacitance: This refers to the PCB’s ability to store electrical charge. While some capacitance is necessary, excessive capacitance can lead to signal degradation and crosstalk. Factors influencing capacitance include:
- Distance between traces
- Dielectric constant of the PCB material
- Copper pour areas
- Inductance: This measures the PCB’s resistance to changes in electrical current. High inductance can cause signal distortion and reduce overall signal quality. Factors affecting inductance include:
- Trace geometry
- Distance between traces
- Presence of vias and other discontinuities
Optimizing these parameters is crucial for achieving superior rigid PCB electrical performance. At JHYPCB, we utilize advanced design techniques and high-quality materials to ensure that our rigid PCBs meet or exceed the electrical performance requirements of our clients’ applications.
Poor electrical performance in rigid PCBs can lead to various issues, including:
- Signal distortion
- Electromagnetic interference (EMI)
- Crosstalk between adjacent traces
- Reduced overall device functionality
By focusing on rigid PCB electrical performance optimization, we at JHYPCB help our clients create more reliable, efficient, and high-performing electronic devices. In the following sections, we’ll explore various techniques and considerations for enhancing the electrical performance of rigid PCBs.
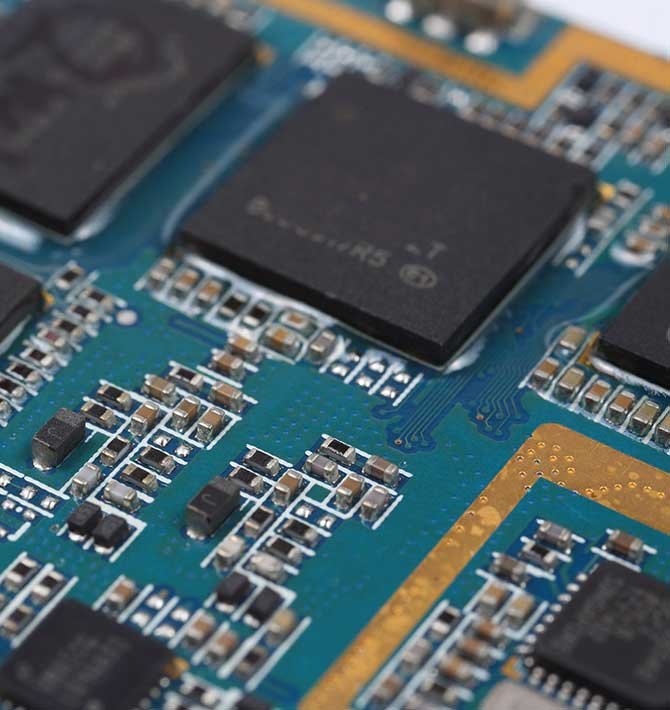
Material Selection for Optimal Rigid PCB Electrical Performance
The choice of materials significantly impacts the electrical performance of rigid PCBs. Let’s explore the most common options and their characteristics:
FR-4: The Industry Standard
- Characteristics: FR-4 is a cost-effective, flame-retardant material widely used in consumer electronics.
- Electrical Properties:
- Dielectric Constant: 4.4 – 4.6
- Loss Tangent: 0.02 – 0.04
- Best For: General-purpose applications where high-frequency performance is not critical.
High-Frequency Laminates
- Rogers Materials
- Characteristics: Excellent for high-speed and high-frequency applications.
- Electrical Properties:
- Dielectric Constant: 2.2 – 6.15
- Loss Tangent: 0.001 – 0.003
- Best For: RF and microwave circuits, aerospace, and defense applications.
- Teflon (PTFE)
- Characteristics: Superior high-frequency performance.
- Electrical Properties:
- Dielectric Constant: 2.05 – 2.10
- Loss Tangent: 0.0002
- Best For: Extremely high-frequency applications and low-loss designs.
- Isola Materials
- Characteristics: Balanced performance for high-speed digital and RF applications.
- Electrical Properties:
- Dielectric Constant: 3.3 – 3.7
- Loss Tangent: 0.004 – 0.015
- Best For: High-speed digital circuits and moderate RF applications.
Key Factors in Material Selection
- Dielectric Constant: Lower values allow for faster signal propagation.
- Loss Tangent: Lower values reduce signal attenuation.
- Thermal Stability: Crucial for maintaining consistent electrical performance across temperature ranges.
- Cost: Balance performance requirements with budget constraints.
Selecting the right material is crucial for optimizing rigid PCB electrical performance. Consider your application’s specific needs when choosing between FR-4 and high-frequency laminates.
Testing and Evaluation Methods for Rigid PCB Electrical Performance
To ensure optimal rigid PCB electrical performance, various testing and evaluation methods are employed. Here are the most effective techniques:
1. Time Domain Reflectometry (TDR)
- Purpose: Measures impedance along transmission lines.
- How it Works: Sends an electrical pulse and analyzes reflections.
- Benefits:
- Quick and accurate impedance measurements
- Identifies discontinuities in PCB traces
- Limitations: Requires specialized equipment
2. Vector Network Analysis (VNA)
- Purpose: Comprehensive characterization of PCB electrical performance.
- Measures:
- Impedance
- Insertion loss
- Return loss
- Phase shift
- Benefits:
- Provides detailed frequency domain analysis
- Essential for high-frequency applications
- Limitations: Can be time-consuming and expensive
3. Time Domain Transmission (TDT)
- Purpose: Analyzes signal integrity through transmission lines.
- Measures:
- Propagation delay
- Rise time degradation
- Crosstalk
- Benefits:
- Relatively fast and cost-effective
- Directly relates to digital signal performance
- Limitations: May not provide as much detail as VNA for some parameters
4. Eye Diagram Analysis
- Purpose: Evaluates overall signal quality in digital systems.
- Measures:
- Jitter
- Noise margins
- Timing violations
- Benefits:
- Visual representation of signal integrity
- Easily interpretable results
- Limitations: Primarily for digital circuits
5. S-Parameter Measurements
- Purpose: Characterizes high-frequency behavior of PCBs.
- Measures:
- Scattering parameters
- Insertion loss
- Return loss
- Benefits:
- Essential for RF and microwave circuit design
- Provides a complete description of the network
- Limitations: Requires advanced equipment and expertise
Choosing the Right Testing Method
Select testing methods based on:
- Your application’s specific requirements
- Frequency range of operation
- Available budget and equipment
- Time constraints
For comprehensive rigid PCB electrical performance evaluation, a combination of these methods often yields the best results. At JHYPCB, we employ a range of these techniques to ensure the highest quality and performance in our PCB manufacturing process.
Techniques for Optimizing Rigid PCB Electrical Performance
At JHYPCB, we employ various advanced techniques to optimize the electrical performance of rigid PCBs. These methods ensure that our clients receive high-quality PCBs that meet their specific requirements. Here are some key optimization techniques:
- Trace Routing Optimization
- Minimize trace length to reduce signal loss
- Avoid sharp corners and use 45-degree angles for turns
- Maintain consistent trace widths for impedance control
- Use differential pair routing for high-speed signals
- Layer Stacking Strategies
- Place critical signal layers between power and ground planes for shielding
- Use high-quality dielectric materials to reduce signal loss
- Implement symmetrical layer stacking for improved mechanical stability
- Impedance Matching Techniques
- Calculate and control trace widths for specific impedance values
- Use impedance-controlled traces for high-speed signals
- Implement termination techniques to reduce reflections
- Power Distribution Network (PDN) Optimization
- Use proper decoupling capacitor placement
- Implement low-inductance power planes
- Utilize stitching vias to reduce plane inductance
- Signal Integrity Enhancement
- Apply proper via design and placement
- Use guard traces to reduce crosstalk
- Implement return path optimization techniques
By applying these rigid PCB optimization techniques, we at JHYPCB ensure that our clients’ PCBs achieve optimal electrical performance. These methods are particularly crucial for high-speed and high-frequency applications where signal integrity is paramount.
Common Issues and Troubleshooting Methods for Rigid PCB Electrical Performance
Despite careful design and manufacturing processes, rigid PCBs may sometimes experience electrical performance issues. At JHYPCB, we’re equipped to diagnose and resolve these problems efficiently. Here are some common issues and their troubleshooting methods:
- Signal Integrity Problems
- Issue: Signal distortion or loss
- Troubleshooting:
- Perform time-domain reflectometry (TDR) analysis
- Check for impedance mismatches
- Analyze trace lengths and routing
- Electromagnetic Interference (EMI)
- Issue: Unwanted radiation or susceptibility
- Troubleshooting:
- Conduct EMI scanning
- Review shielding and grounding strategies
- Analyze component placement and orientation
- Power Integrity Issues
- Issue: Voltage drops or power supply noise
- Troubleshooting:
- Perform power integrity simulations
- Review decoupling capacitor placement
- Analyze power plane design
- Thermal Management Problems
- Issue: Excessive heat generation affecting performance
- Troubleshooting:
- Conduct thermal imaging analysis
- Review component placement for heat distribution
- Analyze copper weight and thermal via placement
- Manufacturing Defects
- Issue: Inconsistent electrical performance due to manufacturing issues
- Troubleshooting:
- Perform automated optical inspection (AOI)
- Conduct flying probe or in-circuit testing
- Review manufacturing process controls
At JHYPCB, we employ a comprehensive approach to troubleshooting rigid PCB electrical performance issues:
- Advanced Testing Equipment: We use state-of-the-art testing tools like vector network analyzers (VNA) and high-speed oscilloscopes for accurate diagnostics.
- Simulation Software: Our team utilizes advanced electromagnetic and circuit simulation software to identify potential issues before manufacturing.
- Expert Analysis: Our experienced engineers analyze test results and provide detailed reports with recommended solutions.
- Iterative Improvement: We work closely with our clients to implement improvements and verify enhanced performance through retesting.
By addressing these common issues and employing robust troubleshooting methods, we ensure that our rigid PCBs meet the highest standards of electrical performance. Our commitment to quality and customer satisfaction drives us to continuously refine our processes and deliver exceptional PCB solutions.
Common Issues Troubleshooting Methods
Common Issues | Troubleshooting Methods |
---|---|
Noise | Signal analysis |
Signal loss | Impedance testing |
Crosstalk | Visual inspection |
Poor design | Signal simulation |
Inadequate testing | Signal integrity analysis |
Improper manufacturing processes | Manufacturing process review |
In summary, common issues can impact the electrical performance of Rigid PCBs, and effective troubleshooting methods are essential for diagnosing and fixing these issues. By using a combination of tools and techniques, it is possible to improve the PCB’s overall electrical performance and ensure the reliable operation of electronic devices.
Conclusion: Mastering Rigid PCB Electrical Performance
Optimizing rigid PCB electrical performance is crucial for the success of any electronic product. Throughout this comprehensive guide, we’ve explored various aspects of rigid PCB electrical performance, from material selection to troubleshooting methods.
Key takeaways include:
- Material Selection: Choosing the right PCB material is fundamental to achieving optimal electrical performance. Consider factors such as dielectric constant, loss tangent, and thermal stability when selecting materials for your specific application.
- Testing and Evaluation: Employ a combination of testing methods, including TDR, VNA, and eye diagram analysis, to thoroughly assess your PCB’s electrical performance.
- Optimization Techniques: Implement advanced techniques such as trace routing optimization, layer stack-up design, and impedance matching to enhance your PCB’s electrical characteristics.
- Troubleshooting: Be prepared to identify and resolve common issues like signal integrity problems, EMI/EMC issues, and power distribution challenges using appropriate tools and methods.
As technology continues to advance, the demands on rigid PCB electrical performance will only increase. Staying informed about the latest developments in PCB design and manufacturing is essential for engineers and designers in the electronics industry.
At JHYPCB, we are committed to delivering high-quality rigid PCBs that meet the most stringent electrical performance requirements. Our team of experts utilizes cutting-edge techniques and technologies to ensure that every PCB we produce performs optimally in its intended application.
Whether you’re designing a simple consumer device or a complex industrial system, understanding and optimizing rigid PCB electrical performance is key to creating reliable, efficient, and high-performing electronic products.
For more information on our rigid PCB manufacturing services or to discuss your specific PCB needs, please contact our team at JHYPCB. We’re here to help you achieve the best possible electrical performance for your PCB designs.
Your Reliable PCB Manufacturer
If you are looking for a reliable and experienced PCB manufacturer to produce high-quality Rigid PCB, flexible PCB, or rigid-flex PCB, look no further. Our company has a long-standing reputation for providing top-notch PCB manufacturing services, including single-sided, double-sided, and multi-layered boards.
We understand that every project is unique and requires a customized solution, which is why we work closely with our clients to ensure that their specific requirements are met. Whether you need a small batch or a large-scale production run, we have the expertise and technology to deliver high-quality PCBs that meet your specifications.
Contact us today to learn more about our services and how we can help you with your PCB manufacturing needs. Our team of experts is ready to assist you every step of the way, from design and layout to production and delivery. We look forward to working with you and delivering the best possible PCB solutions for your business.