In the fast-paced world of electronic device design, the demand for compact, lightweight, and versatile circuit boards has never been greater. This is where Rigid-Flex PCBs come in, providing the perfect solution for complex, multi-functional designs requiring rigid and flexible components. But what exactly are Rigid-Flex PCBs, and what materials are used to make them? In this blog post, we will explore the world of Rigid-Flex PCB Materials, exploring their properties, advantages, disadvantages, and applications. Whether you’re a seasoned electronics professional or just starting in the field, understanding the materials that make up Rigid-Flex PCBs is essential for designing innovative, high-quality electronic devices. So, let’s get started!
What Are Rigid-Flex PCBs?
Rigid-Flex PCB is a type of circuit board that combines both rigid and flexible materials in a single board design. It consists of multiple layers of flexible circuit substrates that are laminated together with layers of rigid circuit boards, which creates a 3D structure. Rigid-flex PCBs are often used in electronic devices that require both rigid and flexible components to be integrated into a single design, allowing for more compact and efficient designs.
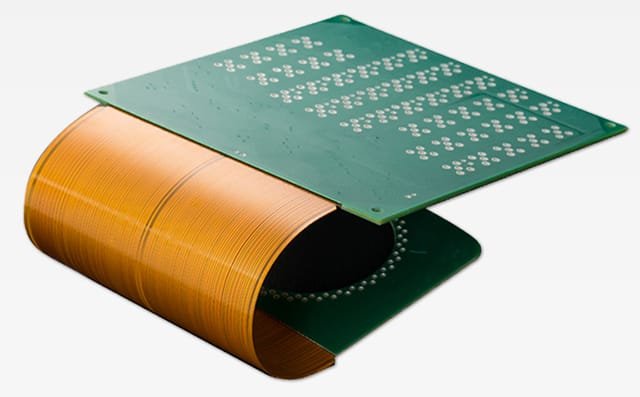
Commonly Used Materials in the rigid-flex PCBs Fabrication
Rigid-Flex PCBs are an innovative type of circuit board that combines both rigid and flexible materials in a single design. The materials used in Rigid-Flex PCBs must be carefully selected to provide the necessary rigidity and flexibility for the board to function properly. Here is a detailed explanation of the materials used in Rigid-Flex PCBs:
- Rigid materials: Rigid materials are typically used for components that require stability, such as connectors and ICs. The most commonly used rigid material in Rigid-Flex PCBs is FR-4, which is a type of fiberglass-reinforced epoxy laminate. FR-4 is known for its strength, stability, and electrical insulation properties. Other types of rigid materials that may be used in Rigid-Flex PCBs include ceramics, metals, and high-temperature plastics.
- Flexible materials: Flexible materials are typically used for components that require movement or bending, such as cables or sensors. The most commonly used flexible materials in Rigid-Flex PCBs are polyimide and polyester. Polyimide is known for its high-temperature resistance, flexibility, and durability, making it ideal for applications where the board will be exposed to high temperatures or harsh environments. Polyester is less expensive than polyimide and is often used in applications where the board will not be exposed to extreme temperatures or harsh environments. Other types of flexible materials that may be used in Rigid-Flex PCBs include thermoplastics, thermosets, and elastomers.
- Adhesive materials: Adhesive materials are used to bond the rigid and flexible layers together in Rigid-Flex PCBs. The adhesive material used in Rigid-Flex PCBs is typically an acrylic adhesive or a modified epoxy. The adhesive must provide a strong, reliable bond that can withstand the stresses of use and handling without breaking or degrading. The adhesive must also be compatible with both the rigid and flexible materials used in the board.
- Cover-Coats: When a flexible film like polyester or polyimide is combined with a suitable adhesive, the resulting product is a cover lay. Cover lay has three major roles to play in a rigid-flex PCB assembly. First, to provide comprehensive protection to the entire assembly. Second, to access circuitry areas like circuit pads for further processing. Third, to augment the reliability and resilience of the circuitry. Unlike the cover lay method, a thin coating of liquid acrylate epoxy and acrylate polyurethane is applied onto the circuitry surface. The liquid coating is applied using several methods, including screen printing. The coating is then thermally cured.
In addition to the specific materials used in Rigid-Flex PCBs, there are several key properties that are important for these materials to have. These properties include:
- Flexibility: The flexible layers of Rigid-Flex PCBs must be able to bend and move without cracking or breaking.
- Rigidity: The rigid layers of Rigid-Flex PCBs must provide stability and support to the board.
- Electrical insulation: All layers of the Rigid-Flex PCB must be electrically isolated from each other to prevent shorts and other electrical issues.
- Temperature resistance: Rigid-Flex PCBs may be exposed to high temperatures during manufacturing or operation, so the materials used must be able to withstand these temperatures without degrading or melting.
- Durability: Rigid-flex PCBs must be able to withstand the rigors of use and handling without breaking or losing their electrical properties.
In conclusion, Rigid-Flex PCBs are made up of a combination of rigid and flexible materials that are bonded together with adhesive materials. The specific materials used in Rigid-Flex PCBs will depend on the application and the requirements of the board, but all materials must have the necessary properties of flexibility, rigidity, electrical insulation, temperature resistance, and durability.
How to choose the right material for your specific project
When selecting Rigid-Flex PCB materials, there are several factors to consider to ensure that you choose the right material for your specific project. Here are some key factors to consider when selecting Rigid-Flex PCB materials:
Application requirements: The specific application requirements of the Rigid-Flex PCB will play a significant role in the selection of materials. Consider the environment in which the board will be operating, the level of flexibility and rigidity required, and the expected lifespan of the board.
Material properties: Each material has its own unique properties, such as flexibility, rigidity, thermal conductivity, and electrical insulation. Consider the properties of each material carefully to ensure they meet the requirements of the application.
Cost: The cost of materials will play a role in the selection process, particularly for high-volume production. Consider the costs associated with each material and determine which material provides the best balance of cost and performance.
Manufacturing process: The manufacturing process for Rigid-Flex PCBs may require specialized equipment and techniques. Consider the manufacturing process requirements for each material to ensure that it is compatible with your manufacturing process.
When choosing the right material for your specific project, it is important to consider all of these factors and make a decision based on the specific requirements of the application. Here are some tips for choosing the right material for your Rigid-Flex PCB project:
Determine the application requirements: Before selecting materials, determine the specific requirements of the application. Consider the environment in which the board will be operating, the level of flexibility and rigidity required, and the expected lifespan of the board.
Research materials: Research the different materials available for Rigid-Flex PCBs and consider the properties of each material. Look for materials that meet the specific requirements of the application and provide a good balance of performance and cost.
Consult with a PCB manufacturer: Consult with a PCB manufacturer who specializes in Rigid-Flex PCBs. They can provide guidance on material selection and help you choose the right material for your specific project.
Consider testing: Consider testing different materials to determine which material provides the best performance for your specific application. This can help you make an informed decision and ensure that you choose the right material for your project.
In conclusion, selecting the right Rigid-Flex PCB materials requires careful consideration of several factors, including application requirements, material properties, cost, and manufacturing process. By taking these factors into account and following these tips, you can choose the right material for your specific project and ensure the success of your Rigid-Flex PCB design.