Introduction
Rigid-flex PCBs are a hybrid of traditional rigid PCBs and flexible circuits, allowing for both flexible and rigid components to be combined in a single board. Rigid-flex PCBs have become increasingly popular due to their ability to reduce space requirements and increase reliability in complex electronic devices. This article will explore the applications and design considerations of rigid-flex PCBs.
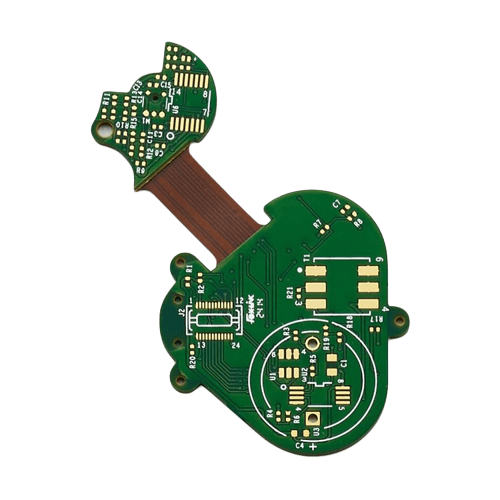
Rigid-Flex PCB Applications
Rigid-flex PCBs have become an increasingly popular solution in various industries due to their flexibility, durability, and reliability.
Rigid-flex PCBs have found significant applications in the medical device industry, where they are used in a variety of devices, including pacemakers, implantable devices, and wearable health monitors. These devices require flexible circuitry that can conform to the shape of the human body while maintaining the integrity of the circuit.
One of the primary applications of rigid-flex PCBs in the medical industry is in pacemakers and implantable devices. These devices require flexible circuitry to allow them to conform to the shape of the heart and surrounding tissues. Rigid-flex PCBs are an ideal solution for these applications as they provide the necessary flexibility and durability required for these devices.
Wearable health monitors have also become increasingly popular in recent years, with the rise of wearable technology. These devices require flexible circuitry that can withstand continuous bending and flexing without compromising the integrity of the circuit. Rigid-flex PCBs are an ideal solution for these applications as they can be designed to be thin, lightweight, and flexible, making them comfortable to wear for extended periods.
The use of rigid-flex PCBs in medical devices provides several advantages over traditional PCB designs. First and foremost, they offer the necessary flexibility required for implantable devices and wearable health monitors. Additionally, they can be designed to be thin and lightweight, making them ideal for devices that require portability and comfort. Finally, rigid-flex PCBs can increase the reliability of medical devices by reducing the need for interconnects and connectors, which can be a source of failure in traditional PCB designs.
Designing rigid-flex PCBs for medical devices requires careful consideration of several factors. The materials used for the rigid and flexible portions of the board must be compatible with each other and meet the requirements of the application. The designer must also consider the bending and flexing requirements of the board and ensure that the components are placed in a way that will not compromise the integrity of the circuit. Additionally, the designer must ensure that the circuit meets the electrical requirements of the application while still maintaining the necessary flexibility.
In conclusion, rigid-flex PCBs have become an essential part of the medical device industry, providing the necessary flexibility and durability required for implantable devices and wearable health monitors. Designing successful rigid-flex PCBs for medical applications requires careful consideration of several factors, including materials, component placement, bending and flexing, and electrical performance. With proper design and implementation, rigid-flex PCBs can provide a reliable and flexible solution for a wide range of medical devices.
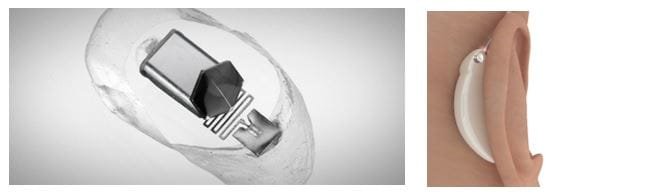
Rigid-Flex PCB Applications in Aerospace and Defense Industry
Rigid-flex PCBs are becoming an increasingly popular choice in the aerospace and defense industry due to their ability to withstand harsh environments and extreme conditions. These electronic components are used in a wide range of applications, including satellites, avionics, UAVs, weapons systems, communication systems, and surveillance systems.
In satellites, rigid-flex PCBs are used to provide the necessary flexibility and durability required for the complex systems onboard. They are also used in avionics to reduce the size and weight of electronic components while maintaining the integrity of the circuit. UAVs also benefit from rigid-flex PCBs as they allow for flexibility and durability in a small and lightweight package.
In the defense sector, rigid-flex PCBs are used in weapons systems to provide reliable and durable electronic components that can withstand harsh environments. They are also used in communication systems to reduce assembly time and cost while maintaining high levels of reliability. Surveillance systems benefit from rigid-flex PCBs due to their ability to withstand extreme temperatures and vibration.
The advantages of rigid-flex PCBs in the aerospace and defense industry include size and weight reduction, reliability in harsh environments, and reduction in assembly time and cost. However, designing rigid-flex PCBs for aerospace and defense applications requires careful consideration of several factors, including temperature range, vibration and shock resistance, EMI/EMC shielding, and high-speed design considerations.
In conclusion, rigid-flex PCBs are becoming an increasingly popular solution in the aerospace and defense industry due to their unique design that allows for flexibility, durability, and reliability. With proper design and implementation, rigid-flex PCBs can provide a reliable and flexible solution for a wide range of applications in this industry.
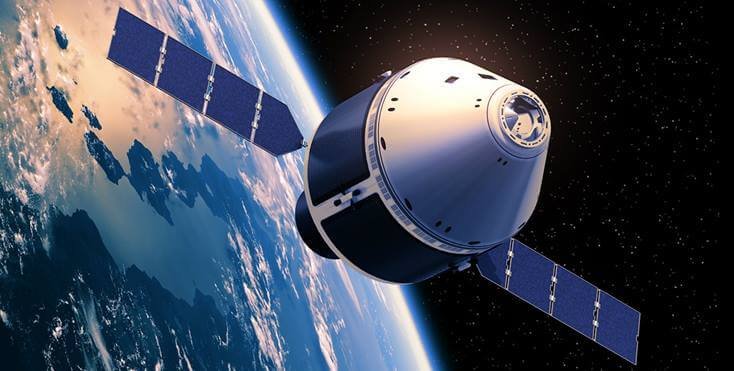
Industrial automation is an essential part of modern manufacturing processes, and the need for compact and reliable electronic components has led to the increasing use of rigid-flex PCBs. Rigid-flex PCBs allow for the integration of multiple functions into a single, compact unit, making them an ideal solution for industrial automation.
Rigid-flex PCBs are used in a wide range of applications in industrial automation, including motor control, human-machine interface (HMI), control and automation, and sensor applications. In motor control, rigid-flex PCBs are used to control and regulate the speed and torque of motors, providing precise control over the manufacturing process. HMIs are used to control and monitor machines and equipment, and rigid-flex PCBs offer a compact and durable solution for this application. Control and automation applications benefit from rigid-flex PCBs due to their ability to integrate multiple functions into a single unit, reducing the size and complexity of the overall system. Sensor applications also benefit from rigid-flex PCBs due to their ability to provide accurate and reliable measurements in a compact and durable package.
The benefits of using rigid-flex PCBs in industrial automation include space-saving design, increased durability, high-speed data transfer, and lower assembly cost and time. The compact design of rigid-flex PCBs allows for more efficient use of space, reducing the overall size of the control system. Rigid-flex PCBs are also more durable than traditional PCBs, with the ability to withstand vibration and shock. High-speed data transfer is possible with rigid-flex PCBs due to their low signal loss and interference. Finally, the use of rigid-flex PCBs can reduce assembly time and cost, as fewer components are needed to create a functional unit.
Designing rigid-flex PCBs for industrial automation applications requires careful consideration of several factors, including temperature range, vibration resistance, flexibility and bending radius, and EMC and EMI shielding. These factors must be considered to ensure the reliability and durability of the finished product.
In conclusion, rigid-flex PCBs offer a reliable and compact solution for a wide range of applications in industrial automation. The benefits of using rigid-flex PCBs include space-saving design, increased durability, high-speed data transfer, and lower assembly cost and time. With proper design and implementation, rigid-flex PCBs can provide a reliable and flexible solution for industrial automation.
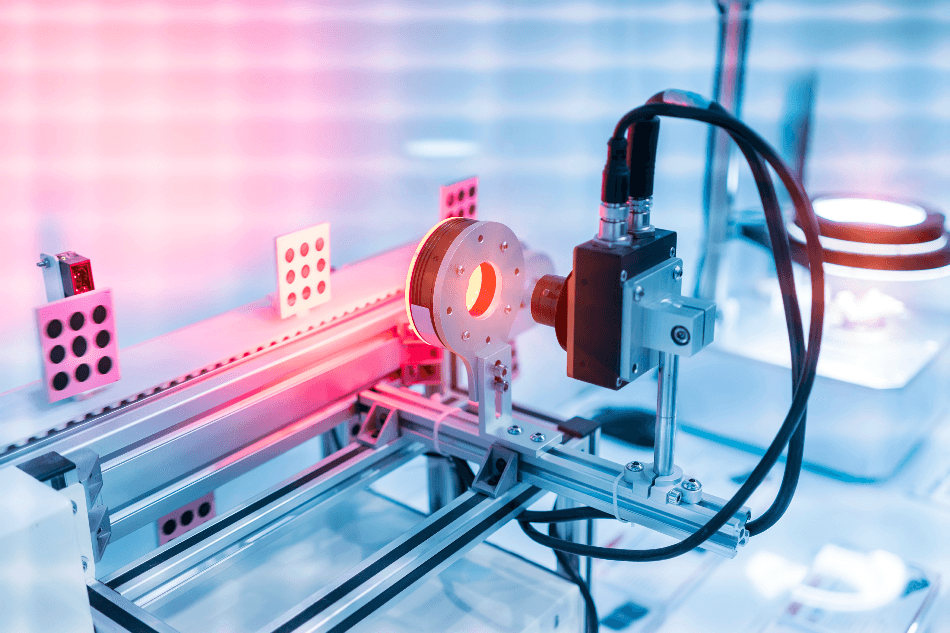
Consumer electronics have evolved significantly in recent years, with an increasing demand for high-performance, compact, and reliable devices. Rigid-flex PCBs have emerged as a popular choice for consumer electronics manufacturers due to their ability to offer high reliability and a compact design.
Rigid-flex PCBs are used in a wide range of applications in consumer electronics, including wearables, smartphones and tablets, portable gaming devices, and home appliances and IoT devices. In wearables, rigid-flex PCBs offer a compact and durable solution that can withstand the stresses of daily wear and tear. Smartphones and tablets benefit from rigid-flex PCBs due to their ability to reduce the size of the device and improve reliability. Portable gaming devices, such as handheld consoles, require a compact and durable design, making rigid-flex PCBs an ideal solution. Home appliances and IoT devices can also benefit from rigid-flex PCBs, as they offer a compact and reliable solution for control and automation applications.
The benefits of using rigid-flex PCBs in consumer electronics include improved reliability, space-saving design, enhanced durability, and lower assembly cost and time. The use of rigid-flex PCBs can improve the reliability of consumer electronics devices by reducing the number of interconnects and potential points of failure. The compact design of rigid-flex PCBs allows for more efficient use of space, reducing the overall size of the device. Rigid-flex PCBs are also more durable than traditional PCBs, with the ability to withstand vibration and shock. Finally, the use of rigid-flex PCBs can reduce assembly time and cost, as fewer components are needed to create a functional device.
Designing rigid-flex PCBs for consumer electronics applications requires careful consideration of several factors, including form factor and size, heat dissipation, flexibility and bending radius, and EMC and EMI shielding. These factors must be considered to ensure the reliability and durability of the finished product.
In conclusion, rigid-flex PCBs offer a reliable and compact solution for a wide range of applications in consumer electronics. The benefits of using rigid-flex PCBs include improved reliability, space-saving design, enhanced durability, and lower assembly cost and time. With proper design and implementation, rigid-flex PCBs can provide a reliable and flexible solution for consumer electronics manufacturers.
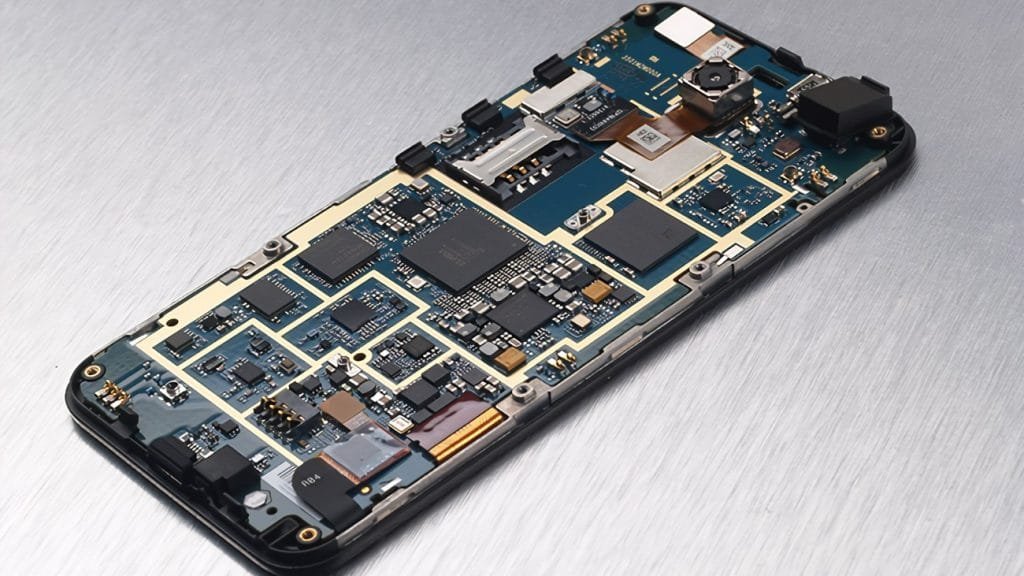
Advantages of Rigid-Flex PCBs
- Space-saving: Rigid-flex PCBs allow for complex circuits to be integrated into smaller devices, saving valuable space.
- Lightweight: The combination of rigid and flexible materials makes rigid-flex PCBs lightweight, making them an ideal solution for devices that require portability.
- Increased reliability: Rigid-flex PCBs reduce the need for interconnects and connectors, which can be a source of failure in traditional PCB designs.
- Improved signal integrity: The elimination of connectors in rigid-flex PCBs reduces signal loss and electromagnetic interference.
- Flexibility and durability: Rigid-flex PCBs can be bent, folded, and twisted without damaging the circuit, making them ideal for applications that require movement and flexibility.
Design Considerations for Rigid-Flex PCBs
- PCB Materials: Choosing the right materials is crucial for the success of a rigid-flex PCB. The materials used for the rigid and flexible portions of the board must be compatible with each other and meet the requirements of the application.
- Component Placement: Proper placement of components is essential for a successful rigid-flex PCB design. The designer must consider the bending and flexing requirements of the board and ensure that the components are placed in a way that will not compromise the integrity of the circuit.
- Bending and Flexing: Rigid-flex PCBs must be designed with the bending and flexing requirements of the application in mind. The designer must ensure that the board can withstand the expected amount of movement without damage to the circuit.
- Electrical Performance: Electrical performance is critical for any PCB design, and rigid-flex PCBs are no exception. The designer must ensure that the circuit meets the electrical requirements of the application while still maintaining the necessary flexibility.
Conclusion
In conclusion, rigid-flex PCBs have become increasingly popular due to their versatility and advantages over traditional PCB designs. They have found applications in various industries, including medical devices, aerospace, and consumer electronics. Designing a successful rigid-flex PCB requires careful consideration of materials, component placement, bending and flexing, and electrical performance. With proper design and implementation, rigid-flex PCBs can provide a reliable and flexible solution for a wide range of electronic devices.