LED strip PCBs, also known as flexible LED boards or flex PCBs, enable versatile and energy-efficient lighting in a slim, bendable form factor. These boards mount long strands of surface-mount LEDs onto a thin, flexible circuit material to create customizable LED strips.
With LED strip PCBs, lighting designers and engineers can configure long runs of LEDs in their choice of shapes, densities, and lengths. The thin flexible construction allows installing these LED strips in places where rigid PCBs won’t fit.
Key benefits of LED strip PCB technology include:
- Ultra-slim profile for concealed lighting
- Can be bent and shaped to fit unique spaces
- Even the distribution of LEDs at the desired density
- Flexible branches and segments
- Robust and highly efficient lighting
- Easy installation and portability
- Lower energy use compared to neon
In this article, we’ll explore how to design and manufacture reliable, high-performance LED strip PCB assemblies tailored to your unique lighting needs.
design considerations for LED strip PCBs
Engineering effective LED strip PCBs require attention to these key design aspects:
- Circuit Layout – Optimize trace routing for reliability under bending and to minimize cross-talk.
- Board Shape – Consider desired shape, width, and thickness for application.
- Copper Thickness – Balancing conductivity vs. flexibility using thinner copper.
- Component Placement – Strategic LED spacing, minimizing component density.
- Thermal Management – Copper fills, openings, and MCPCB to prevent LED overheating.
- Flexibility – Account for minimum bend radius in layout.
- Connectors – Robust connectors to handle repeated flexing.
The goal is to create a layout optimized for the planned shape, brightness, and flexibility needed. Partnering with an expert PCB manufacturer during design ensures your board meets reliability and performance targets.
Manufacturing process for LED strip PCBs
Producing reliable LED strip PCBs requires specialized fabrication and assembly techniques:
- Material Selection – Choosing robust flexible substrate materials like polyimide.
- Imaging – Precise laser etching to prevent reduced line width on flex boards.
- Layer Alignment – Critical for multi-layer flex PCBs to prevent layer shifting.
- Etching Process – Optimized to prevent over-etching of thin copper traces.
- Solder Mask – Liquid photo-imageable solder mask for uniform application on flex boards.
- Component Assembly – Delicate process to avoid damaging flexible materials.
- Conformal Coating – Protects assembled PCBs from moisture, dust, and chemicals.
- Testing – Validating proper functioning during dynamic bending conditions.
LED strip PCB manufacturing leverages customized equipment and processes tailored for thin, bendable PCB materials. Partnering with an expert manufacturer like JHYPCB ensures your LED strips achieve the highest reliability and longevity.
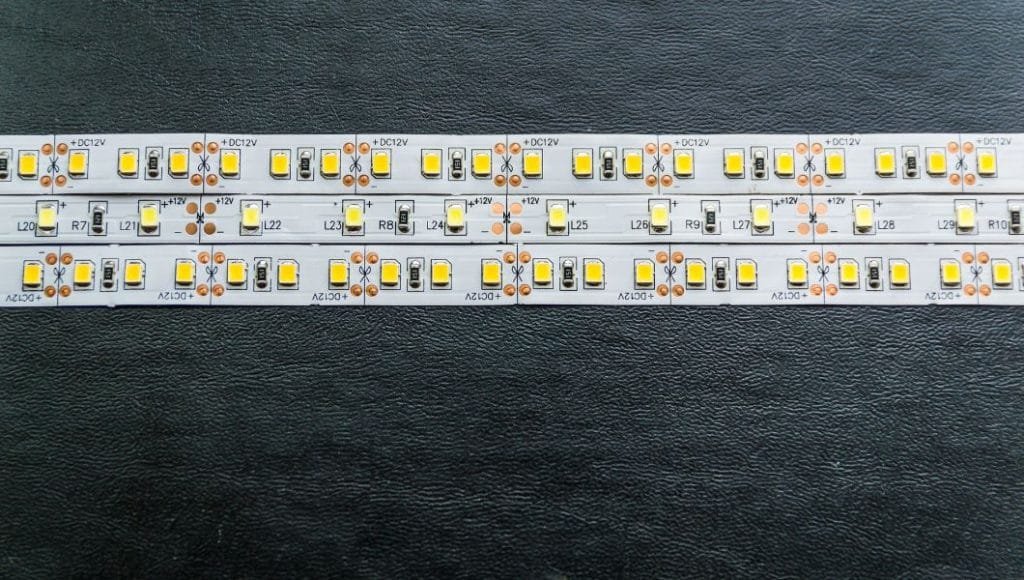
Quality control for LED strip PCBs
Robust quality control practices are essential when producing LED strip PCBs:
- Visual Inspection – Cameras and automated optical inspection detect any physical defects.
- Functional Testing – Validating proper operation of circuits under both static and dynamic bending.
- Dielectric Strength Testing – Applying high voltage to measure insulation resistance.
- Environmental Stress Screening – Assessing performance under simulated environmental conditions.
- Adhesion Testing – Pull and peel testing to validate robust component attachment.
- Life Cycle Testing – Bend testing through expected minimum bend cycles.
- Reviews of Critical Parameters – Dimensions, copper thickness, placement accuracy, etc.
At JHYPCB, every PCB undergoes over 500 quality checkpoints focused on the unique requirements of flexible boards. This stringent process control ensures our LED strips will work reliably over years of service.
Customization of LED strip PCBs
A key advantage of LED strip PCBs is the ability to customize the design for your specific lighting application needs:
- Shape – Create straight strips, right-angle bends, or curving shapes.
- Branches – Add wire or PCB branches for multi-directional lighting.
- LED Density – Configure spacing between LEDs for desired luminance.
- LED Types – Select from top LED manufacturers in preferred luminous intensity.
- Control Components – Integrate resistors, ICs, and connectors tailored for your system.
With custom LED strip PCBs, lighting designers can dial in the exact shape, brightness, color temperature, and controls required. This enables the creation of application-specific LED strips optimized for accent lighting, display cases, cove lighting, and more.
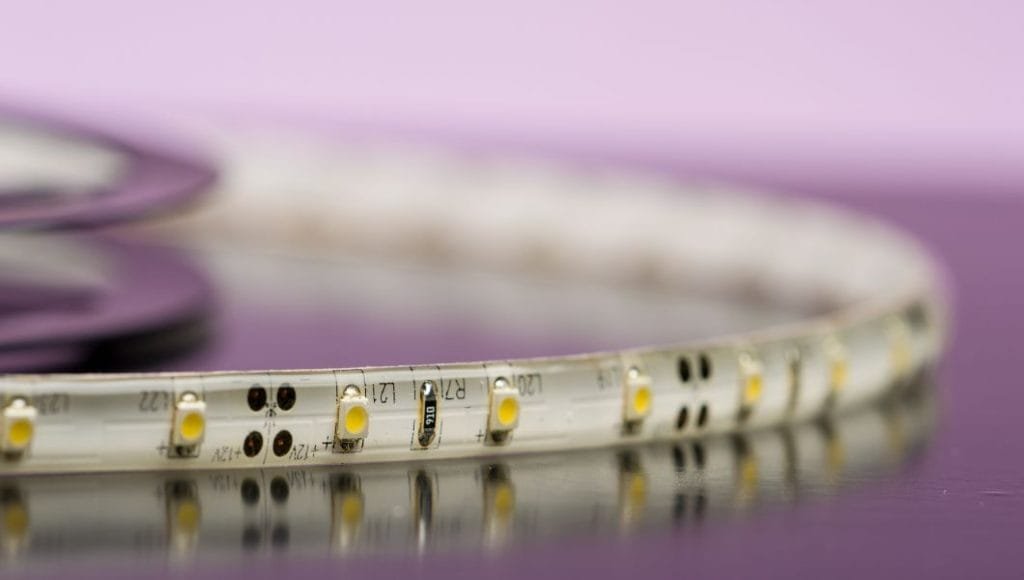
Applications of LED strip PCBs
Thanks to their slim, flexible, and customizable nature, LED strip PCBs are being adopted across many lighting applications:
- Accent & Mood Lighting – For highlighting architectural features, displays, and mood settings.
- Retail Display Lighting – Providing eye-catching illumination in merchandising displays.
- Task & Cabinet Lighting – Unobtrusive undershelf and task illumination.
- Signage – Outlining signage characters through flexible LED strips.
- Automotive Lighting – Contoured interior lighting using flexible LED boards.
- Emergency Lighting – Long-lasting LED strip lighting for egress paths.
The adaptability of LED strip PCBs enables lighting designers to enhance ambiance and visibility in diverse environments. Their energy efficiency also makes them ideal for sustainable lighting transformations.
Get Started
Ready to create customized LED strip PCB lighting solutions? The engineering experts at JHYPCB can help you design, prototype, and manufacture reliable flex LED boards tailored to your specific application requirements.
With over 10 years of experience producing complex flexible PCBs, we have the specialized capabilities to handle demanding LED strip PCB projects. Our optimized fabrication processes and rigorous quality control ensure the delivery of thoroughly tested boards.
Whether you need functional prototypes for concept validation or high-volume production for product release, JHYPCB has you covered. Our large production capacity enables cost-effective scaling to any quantity needs.
Contact us today to discuss your custom LED strip PCB project. We’ll work closely with you to design boards to meet your technical, functional, and budgetary goals. Bring your unique LED lighting vision to life with JHYPCB’s expertise!