Managing PCB costs is a crucial aspect of product development and pricing for technology companies. While it’s tempting to simply choose the cheapest PCB manufacturing options, that often leads to quality issues that negatively impact performance and reliability down the line. The key is finding ways to lower costs without sacrificing quality and functionality.
When setting pricing for a new product, the bill of materials (BOM) cost for the PCB assembly is a major factor. Any savings in PCB expenses can directly translate to a more competitive and attractive price point. However, quality issues that arise from overly cost-driven PCB sourcing can result in increased warranty costs, reworks, and other expenses over the product life cycle. The goal should be optimizing cost savings while maintaining quality standards.
This article will provide practical strategies for technology product managers, engineers, and procurement teams to reduce PCB costs without compromising quality. Key areas covered include optimizing PCB design, selecting the right supplier, strategic purchasing techniques, and more. The guidance provided focuses on balancing cost control and quality assurance when bringing new products to market.
Optimize PCB Design to Lower Costs
There are several design considerations that can help reduce PCB manufacturing costs without negatively impacting quality:
- Simplify the design and avoid unnecessary features – The more complex the PCB design, the more expensive it will be to manufacture. Eliminate any excessive or non-essential components and consolidation functions where possible. However, be careful not to compromise the necessary functionality.
- Use standardized components – Opt for common, widely available parts that PCB assembly shops will have in stock. Custom or rare components add procurement costs and risk.
- Design for manufacturability – Use design rules provided by manufacturers to avoid potential issues in fabrication and assembly. This includes proper trace widths, spacing, etc.
- Reduce layer counts – Lowering the number of conductive copper layers reduces material costs. But ensure essential traces and connections are maintained.
- Adjust board size and thickness – Smaller and thinner PCBs require fewer materials. But watch for impacts on durability and heat dissipation.
- Watch component placement – Well-organized component placement and efficient use of space reduce the PCB footprint size.
By focusing on simplicity and standardization in the design process, PCB costs can be decreased without compromising quality or product performance. Work closely with your manufacturer to identify areas of cost optimization in the design.
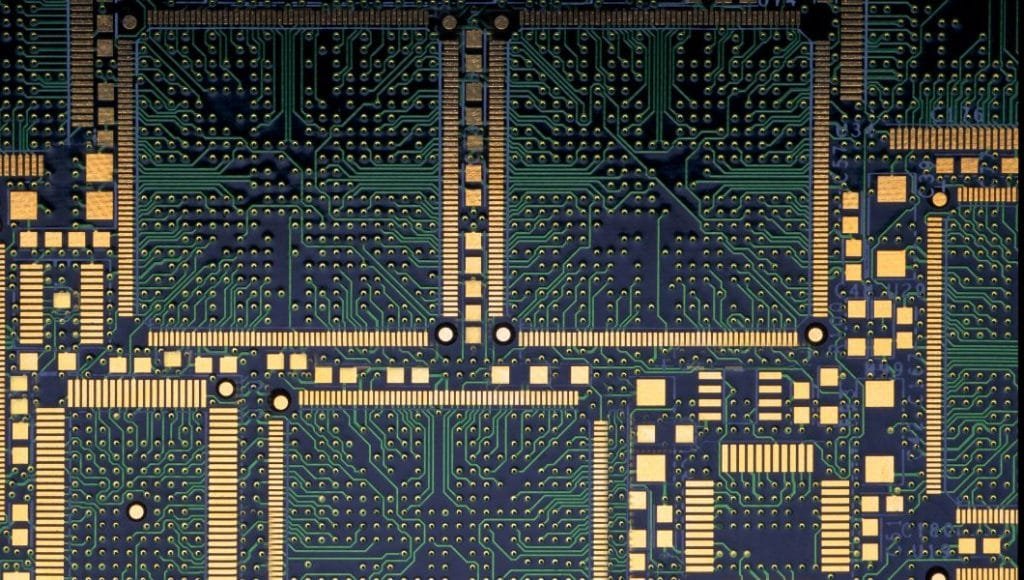
Choose the Right PCB Manufacturer
Selecting the right PCB manufacturer for an optimal balance of cost and quality is key. Here are some tips for evaluating and choosing manufacturing partners:
- Get quotes from multiple manufacturers – Compare pricing on identical board specifications to identify cost differences. But look at total landed costs, not just unit prices.
- Assess quality certifications and capabilities – Review quality control standards, manufacturing equipment, qualifications, and expertise related to your product needs. This includes factors like minimum trace widths, layer counts, materials, etc.
- Validate delivery reliability – Look at lead times and on-time delivery rates. Delays from unreliable manufacturers lead to increased costs.
- Evaluate communication and customer service – Responsive and collaborative manufacturers help optimize designs and solve problems. Language barriers and poor communication create inefficiencies.
- Consider manufacturing complexity – The simplest board designs can leverage high-volume manufacturers that rely on economies of scale. More complex PCBs require manufacturers with specialized equipment and expertise.
- Ask about change order charges – Design tweaks after initial orders often incur additional fees. Understand change order pricing in advance.
By selecting PCB manufacturing partners with balanced pricing, capabilities, quality, and service, overall costs can be minimized without sacrificing board quality or deliverability.
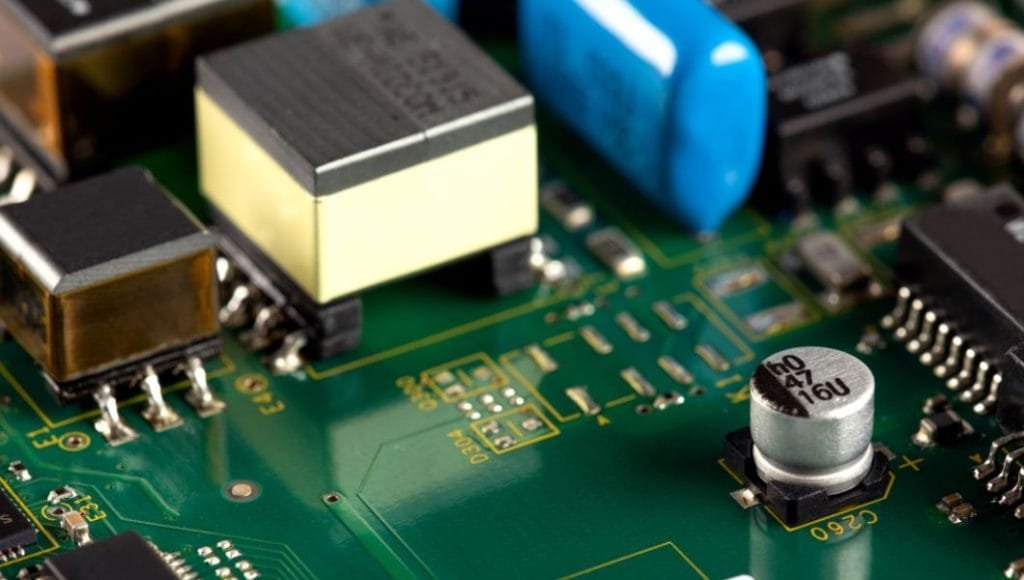
Strategic Purchasing
There are some best practices when it comes to purchasing strategies that can help reduce PCB costs:
- Order in bulk volumes to get quantity discounts – PCB pricing often follows a tiered structure where unit costs decrease at higher order quantities. Coordinate with manufacturing forecasts to enable bulk orders.
- Leverage long-term agreements and partnerships – Negotiated long-term contracts with “most favored customer” pricing and volume-based discounts can save significantly over spot purchases. Develop strategic supplier partnerships.
- Account for PCB size variations – Larger PCB sizes in a panelized layout can lower the cost per unit. Grouping small PCBs on panel sheets optimizes material utilization.
- Factor in complexity – Simpler board designs with fewer layer counts, drilling, and looser tolerances decrease costs. Carefully evaluate manufacturing requirements.
- Watch material costs – Commodity pricing for key components like resin, copper, gold, etc. fluctuates. Review cost drivers and stay aware of market trends.
- Allow flexibility around lead times – If possible, flexible delivery timelines can help manufacturers slot orders into production plans for maximum efficiency.
With strategic purchasing techniques, sourcing teams can reduce PCB procurement costs substantially without impacting the quality or delivery of boards.
Conclusion
In summary, there are a variety of techniques product teams can leverage to reduce PCB costs without sacrificing quality:
- Simplify designs and use common components
- Work with manufacturers on design for manufacturability
- Strategically choose manufacturing partners
- Negotiate bulk order discounts and long-term contracts
- Optimize purchasing plans based on order size, materials, and complexity
The key is taking a holistic approach and collaborating closely with your PCB manufacturers. By implementing the strategies covered in this guide, companies can effectively manage PCB expenses while ensuring excellent product quality.
For more information or help on reducing your PCB costs, contact the manufacturing experts at JHYPCB. We provide high-quality, low-cost PCB fabrication and assembly services. Feel free to reach out to us at sales@pcbjhy.com to discuss your specific PCB sourcing needs.
Related Reading:
- How to Reduce PCB Costs Without Sacrificing Quality
- Building High-Quality PCBs – A Comprehensive Guide
- Material selection and performance of multilayer PCBs: how to balance cost and performance
- How to Reduce Manufacturing Costs for Rigid-Flex PCBs?
- High Tg PCB Cost and Pricing: Factors Affecting the Price and How to Save Money
- Affordable PCB Prototyping: Options Worldwide