Printed circuit boards are the backbone of electronic devices and products. From computers and smartphones to industrial equipment, PCBs provide the foundation for mounting and connecting electronic components. For any electronics manufacturer, choosing the right PCB is crucial to product performance, durability, and cost.
In recent years, a particular type of PCB called high Tg PCB has emerged as an option for designers and engineers. High Tg stands for high glass transition temperature, which refers to the high heat resistance of the substrate material used in these PCBs. Compared to standard FR-4 PCBs, high Tg PCBs can withstand much higher temperatures without issue.
If you’re wondering whether a high Tg PCB or traditional PCB is right for your next project, this article will help you understand the key differences and make the best choice. We’ll compare high Tg and standard PCBs in terms of their specifications, capabilities, applications, and other factors you need to consider. With the right information, you can evaluate both options and select the optimal board for your specific needs and operating environment.
Choosing the right PCB is crucial for product performance, safety, and cost. By understanding high Tg vs. standard PCB differences, electronics manufacturers can make informed decisions on the best board for their application. A high-quality, well-suited PCB provides the robust foundation for successful modern electronic products.
Definition of high Tg vs. standard PCBs
To understand the key differences between these two types of printed circuit boards, we first need to define what makes high Tg and standard PCBs unique.
Standard PCBs refer to the typical circuit boards used in mainstream electronics. The substrate material in these boards is almost always FR-4, a glass-reinforced epoxy laminate that has served as the standard PCB substrate for decades. FR-4 offers a balance of electrical performance, mechanical stability, and cost-effectiveness. However, it comes with relatively low heat tolerance.
High Tg PCBs get their name from the high glass transition temperature of their substrate materials. Rather than using traditional FR-4, high Tg PCBs utilize advanced substrate materials such as polyimide, I-Tera MT, and others. These substrates have a high glass transition temperature, which is the point at which the material transitions from a hard, glassy state to a soft, rubbery state. The higher this temperature, the better the material retains its stiffness, stability, and electrical insulating properties under high heat conditions.
In practical terms, high Tg PCB substrates like polyimide can withstand temperatures exceeding 250°C without damage, while standard FR-4 PCBs begin to suffer performance loss above 130°C. This boosted heat resistance makes high Tg PCBs ideal for demanding applications with high power density, thermal cycling, or use in extreme environments.
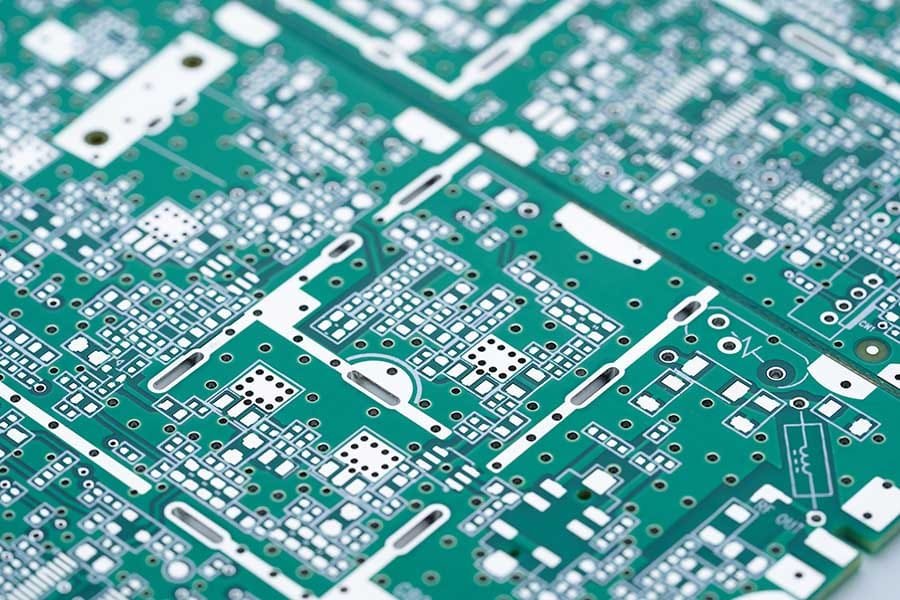
Key differences between high Tg and standard PCBs
High Tg PCBs and Standard PCBs differ in various aspects, including their material composition, thermal performance, and cost. Here are some of the key differences between the two types of PCBs:
- Material composition: High Tg PCBs are made from materials that have a higher glass transition temperature (Tg) than standard PCBs. This means that they can withstand higher temperatures without losing their mechanical or electrical properties. High Tg PCBs typically use materials such as FR4-High Tg, FR5, and Rogers materials, while standard PCBs typically use FR4.
- Thermal performance: High Tg PCBs have better thermal performance than standard PCBs, thanks to their higher Tg value. This means that they can dissipate heat more effectively, reducing the risk of damage to the components and ensuring the reliable operation of the circuit. High Tg PCBs also have a lower coefficient of thermal expansion (CTE) than standard PCBs, which further improves their thermal stability.
- Cost: High Tg PCBs are generally more expensive than standard PCBs due to the higher cost of materials and the more stringent manufacturing process required. However, the cost difference may be justified by the superior performance and reliability of High Tg PCBs, especially in applications that require high-temperature operation or have high thermal stress.
- Mechanical strength and reliability: Mechanical strength and reliability are also important differences between high Tg PCB and standard PCB. High Tg PCB materials have higher glass transition temperatures and better mechanical properties, which make them more resistant to thermal stress, moisture, and other environmental factors. They also have better resistance to delamination, warping, and cracking, which can occur due to mechanical stress during operation or handling. This makes high Tg PCBs more reliable and durable, especially for applications that require high levels of mechanical stability and long-term performance. Standard PCBs, on the other hand, may not have the same level of mechanical strength and reliability, which can affect their performance and lifespan in certain applications.
- Temperature Resistance
One major difference is the maximum operating temperature each board can withstand. As mentioned, high Tg PCBs can handle over 250°C in many cases, while standard FR-4 PCBs start to experience issues above 130°C. The higher heat tolerance makes high Tg PCBs suitable for high-power applications that generate significant heat. - Dielectric Constant
The dielectric constant (Dk) differs between substrate materials and affects signal propagation through the board. Most high Tg substrates have a lower Dk than standard FR-4, which helps minimize interference and crosstalk at high frequencies.
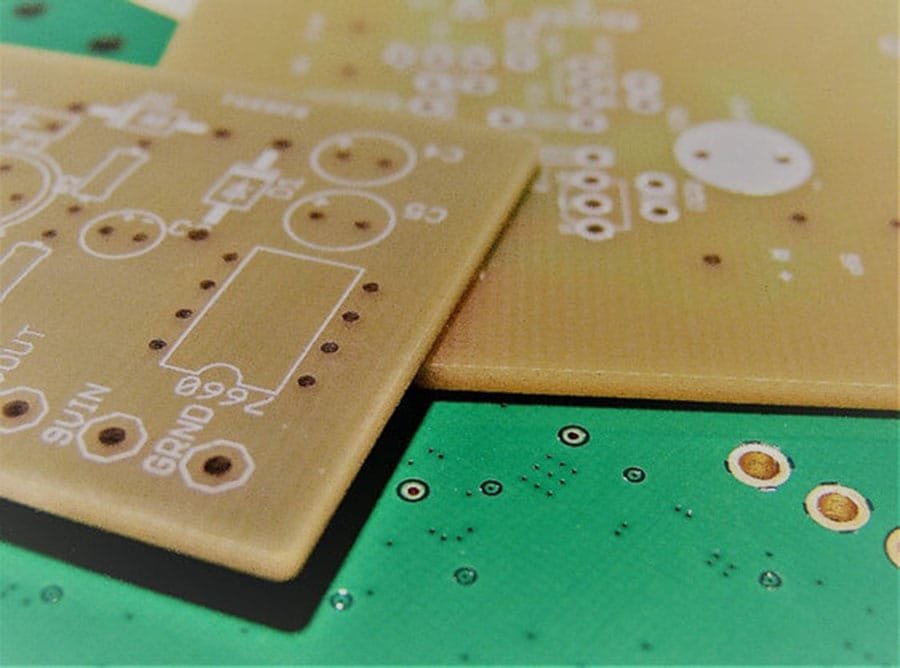
Applications and situations where high Tg PCBs are recommended or required
With an understanding of the key differences, we can now explore which types of applications stand to benefit most from utilizing high Tg PCBs.
- High-Temperature Environments
Any application involving sustained high temperatures above 130°C should utilize a high Tg board. The higher heat resistance ensures reliable performance even as operating temps rise. This includes automotive electronics near hot engines, aerospace avionics, and military hardware exposed to extreme environments. - High-Power Electronics
Electronic devices and systems with high-power components that generate substantial heat are also good candidates for high Tg PCBs. The enhanced thermal conductivity allows more effective transfer of heat away from sensitive components. Examples include industrial power supply equipment, RF amplifiers, laser systems, and more. - Thermal Cycling Resistance
Applications, where PCBs undergo repeated thermal cycling between hot and cold temperatures, should consider high Tg boards. The extreme temperature shifts can gradually damage FR-4 boards. High Tg PCBs resist this thermal cycling and extend product lifetimes as a result.
In essence, any application where heat is a major factor – whether extremely high temps or cyclic heating/cooling – can benefit from the robust thermal capabilities of high Tg PCB substrates.
Applications where standard PCBs are sufficient
While high Tg PCBs offer advantages for demanding environments, standard FR-4 PCBs remain a suitable option for many everyday applications in commercial electronics.
- Consumer Electronics
Standard FR-4 boards are ubiquitously used in consumer electronics like smartphones, computers, home appliances, and more. These applications don’t generate extreme heat loads, making high Tg PCBs unnecessary. FR-4 provides electrical performance at the right cost. - Low-Power Electronics
Similarly, applications with only low-power components have modest heating profiles. They can rely on affordable FR-4 PCBs without issue. This includes IoT devices, battery-powered electronics, sensing equipment and more. - Cost-Sensitive Applications
When budget and cost control are primary concerns, standard FR-4 PCBs help keep manufacturing expenses in check. High volume consumer goods and electronics trying to minimize BOM cost are suitable for traditional boards. - General Commercial Use
For most commercial and industrial electronic products that don’t experience thermal extremes, standard PCBs are the economical choice that still deliver reliable function. Elevators, vending machines, security systems and more fit this description.
Benefits of High Tg PCBs
High Tg PCBs offer several benefits over standard PCBs, including:
- High-Temperature Resistance: High Tg PCBs are designed to withstand high temperatures without losing their mechanical strength and electrical properties. This makes them ideal for use in applications that generate high heat, such as power electronics, automotive, and aerospace industries.
- Better Mechanical Strength: The use of high Tg materials in PCBs significantly improves the mechanical strength of the boards, making them more resistant to bending, warping, and cracking. This leads to better durability and reliability, reducing the need for maintenance and replacement.
- Improved Electrical Performance: High Tg PCBs have better electrical properties than standard PCBs, including lower dielectric constant and loss tangent. This improves signal integrity and reduces signal distortion, ensuring optimal performance.
- Increased PCB Lifespan: High Tg PCBs have a longer lifespan due to their superior mechanical strength and temperature resistance. This translates into reduced maintenance costs and longer service life.
- Enhanced Design Flexibility: High Tg PCBs allow for more flexibility in the design of complex and high-density circuits. This is due to their improved mechanical strength and reduced risk of warping or cracking during the manufacturing process.
- Suitable for high-frequency and high-speed applications: High Tg PCBs are particularly suitable for high-frequency and high-speed applications. This is because they have a low dielectric constant and low dielectric loss, which enables them to maintain signal integrity and reduce signal attenuation. In addition, the high glass transition temperature (Tg) of the PCB material ensures that the board retains its mechanical and electrical properties even at high temperatures, which is important for high-speed applications where the board may be subject to thermal stress. High Tg PCBs are commonly used in telecommunications, computing, aerospace, and automotive industries, where high-frequency and high-speed applications are prevalent.
When to Choose High Tg PCBs over Standard PCBs
When considering whether to choose high Tg PCBs over standard PCBs for a project, there are a few key factors to consider:
- Operating temperature: If the project involves high-temperature applications or environments, high Tg PCBs may be necessary to ensure reliable performance.
- High-speed and high-frequency applications: High Tg PCBs have a lower signal loss and less distortion, making them suitable for high-speed and high-frequency applications.
- Mechanical strength and reliability: High Tg PCBs have better mechanical strength and are more reliable, which makes them suitable for applications that require long-term durability.
- Complex designs: High Tg PCBs are more resistant to warping and twisting, which makes them suitable for complex designs that require multiple layers.
- Budget: High Tg PCBs are generally more expensive than standard PCBs, so budget considerations may also factor into the decision.
Factors to Consider When Choosing between High Tg PCB and Standard PCB
When choosing between High Tg PCB and Standard PCB, there are several factors to consider:
- Operating temperature: High Tg PCBs are suitable for applications that require high operating temperatures, typically above 130°C, whereas Standard PCBs are not recommended for use above 130°C.
- Mechanical strength: High Tg PCBs have greater mechanical strength and are more reliable, making them a better choice for applications that require higher levels of durability and reliability.
- Signal integrity: High Tg PCBs have a lower coefficient of thermal expansion (CTE) than standard PCBs, which helps to maintain signal integrity at high temperatures.
- Cost: High Tg PCBs are generally more expensive than standard PCBs due to their advanced material properties and manufacturing processes. Therefore, the cost is an important factor to consider when choosing between the two.
- Manufacturing process: High Tg PCBs require more advanced manufacturing processes, including higher temperature lamination and longer press cycles, which can affect production time and cost.
- Design considerations: High Tg PCBs require careful consideration of design factors such as trace width and spacing, via size, and pad size to ensure optimal performance and reliability.
- Application requirements: The specific application requirements, such as frequency, speed, and reliability, should be carefully evaluated to determine if High Tg PCBs are the right choice.
High Tg PCB Fabrication and manufacturer in China
If you’re looking for a reliable and high-quality PCB solution for your next project, consider choosing high Tg PCBs. With their enhanced thermal and mechanical properties, high Tg PCBs offer improved performance and reliability in harsh environments, high-speed applications, and more.
At our company, we specialize in the manufacturing of high Tg PCBs, using top-of-the-line materials and state-of-the-art manufacturing processes to ensure the highest quality results. With years of experience and a commitment to customer satisfaction, we have the expertise and capability to provide you with the perfect high Tg PCB solution for your unique needs.
Don’t settle for standard PCBs when you can choose high Tg PCBs for improved performance and reliability. Contact us today to learn more about our high Tg PCB manufacturing services and how we can help you take your project to the next level.