With electronics becoming more compact and powerful, managing heat dissipation is critical for ensuring proper function and reliability. Using PCBs designed for high-temperature operation is key for thermal management. High Tg (glass transition temperature) PCB materials allow circuits to withstand high temperatures without mechanical or electrical failure. Unlike standard FR-4 PCB substrates limited to low Tg ratings, specialized high Tg PCB materials enable operation in hot environments up to over 300°C. Applications such as automotive electronics, aerospace avionics, oil and gas drilling, and industrial equipment rely on the thermal stability and heat resistance of high Tg PCBs. Choosing the right high Tg PCB material depends on factors like maximum temperature requirements, dielectric properties, thermal conductivity, and cost constraints. Materials like polyimide, Isola, Arlon, PTFE, and ceramic substrates provide higher Tg ratings than FR-4 but involve tradeoffs. This guide provides a comparison of popular high Tg PCB materials in terms of thermal, mechanical, electrical, and cost characteristics. With an understanding of key technical specifications and tradeoffs, engineers can select an optimal high Tg PCB material that balances performance needs with budget for their specific application.
Materials for High Tg PCBs
- FR-4
FR-4 is the standard substrate used for the majority of PCBs. It’s a composite of woven fiberglass cloth with an epoxy resin binder. However, FR-4 has a relatively low glass transition temperature of around 130°C, limiting its use for high-heat applications. The resin binder softens as the temperature exceeds Tg, causing mechanical failures. FR-4 is only suitable for PCBs operating up to about 100°C. - Polyimide
Polyimide is a high-performance plastic material well suited for high-temperature PCBs up to and beyond 300°C. The aromatic polymer structure of polyimide gives it thermal stability, high mechanical strength, and excellent chemical resistance. Polyimide PCBs maintain integrity across a wide temperature range from cryogenic to over 300°C. However, polyimide boards are more expensive than FR-4. - Isola High Tg FR-4
Isola manufactures specialty high Tg FR-4 materials enhanced for moderate temperature resistance up to 150-180°C. These improved FR-4 variants leverage proprietary resin systems to increase thermal performance at a lower cost compared to polyimide. Isola high Tg FR-4 products provide an incremental upgrade for basic high-temperature needs. - Arlon Thermoplastic
Arlon thermoplastic PCBs use a liquid crystal polymer material capable of withstanding temperatures up to 290°C. The liquid crystal polymer maintains its mechanical strength and electrical properties at high temperatures. Arlon boards offer thermal performance approaching that of polyimide but at a lower cost point. This makes Arlon a more budget-friendly solution for moderate high-temperature environments. - PTFE
PTFE (polytetrafluoroethylene) substrates provide the highest glass transition temperature among plastic PCB materials, rated over 260°C. PTFE is an extremely non-reactive fluoropolymer plastic resistant to nearly all chemicals. It has high dielectric strength and excellent electrical insulating properties. PTFE PCBs present exceptional thermal stability for the most demanding high-temperature needs. However, PTFE boards are also the most expensive high Tg option. - Ceramic PCBs
For unrelenting high-heat environments beyond 300°C, ceramic PCBs present the ultimate thermal solution. Ceramic substrates like aluminum oxide maintain mechanical and electrical integrity up to 1000°C. Technical ceramic PCBs offer unparalleled heat resistance combined with electrical insulation. But ceramics are also brittle and the PCB fabrication process is challenging. This makes ceramic boards costly, and reserved for only the most extreme thermal requirements.
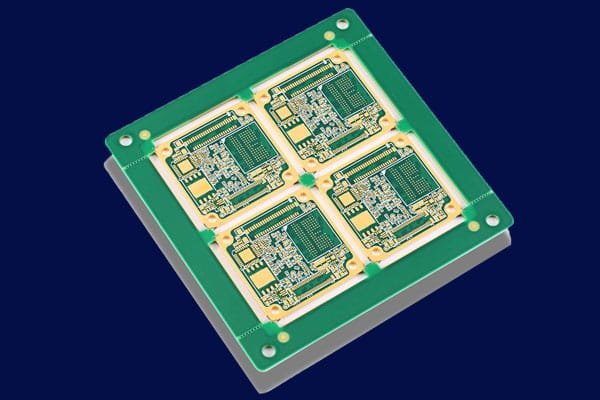
Comparison and Selection Guide
When selecting a high Tg PCB material, there are several key properties and specifications to consider:
- Glass Transition Temperature Rating – The Tg directly indicates the maximum temperature a material can withstand before softening. This is the primary specification to match with thermal requirements.
- Thermal Conductivity – How well a material conducts heat is important for thermal management. Higher thermal conductivity allows more efficient heat dissipation.
- Dielectric Constant and Loss Tangent – These electrical properties affect signal integrity at high frequencies. Materials should provide stable electrical performance across temperature variations.
- Coefficient of Thermal Expansion – The amount a material expands with increasing temperature. Low CTE provides crucial dimensional stability and prevents warping.
- Flame Resistance – Materials must meet flammability standards to avoid fire hazards, especially at elevated temperatures. High Tg materials are typically inherently flame resistant.
- Flexural Strength – The ability to withstand mechanical stresses without damage. High flexural strength prevents cracking or warping.
- Cost – High Tg materials are more expensive than standard FR-4, so cost is an important practical consideration.
Tips and best practices for working with high Tg PCB materials
- Precautions and guidelines for handling and processing high Tg PCB materials:
- High Tg materials are more brittle and sensitive to thermal shock than standard FR-4 materials, so it is important to handle them with care to avoid damage during manufacturing processes.
- When drilling, routing, or milling high Tg PCBs, it is important to use sharp tools and avoid high speeds to reduce the risk of delamination or cracking.
- High Tg materials can also be more sensitive to chemical exposure, so it is important to use the correct chemicals and follow recommended processing times and temperatures.
- Recommended manufacturing processes for each material type:
- Each high Tg material has its own recommended manufacturing process, so it is important to work with a supplier who can provide guidance and support based on the specific material being used.
- Generally, high Tg PCBs require higher temperatures and longer processing times than standard FR-4 materials. For example, a typical curing cycle for a high Tg material may be 180-200°C for 2-4 hours, whereas a standard FR-4 may only require 150-170°C for 1-2 hours.
- Tips for optimizing design and layout to maximize the performance of high Tg PCBs:
- High Tg materials are typically chosen for their improved thermal and mechanical properties, so it is important to optimize the design and layout to take advantage of these benefits. For example, using copper planes and thermal vias to dissipate heat, or increasing the thickness of the board to improve rigidity and reduce warping.
- It is also important to consider the impact of high Tg materials on the design rules for the board. For example, high Tg materials may require larger trace widths or spacing to prevent issues with signal integrity or reliability.
- Finally, it is important to work closely with the PCB manufacturer to ensure that the design is optimized for the specific high Tg material being used, as each material may have its own unique requirements and limitations.
By following these tips and best practices, you can help ensure the successful manufacturing and performance of high Tg PCBs.
Conclusion
In conclusion, selecting the right high Tg PCB material depends on your specific application requirements. Both FR-4 and polyimide offer unique advantages, and the choice between the two will depend on factors such as temperature, mechanical strength, chemical resistance, dielectric properties, and cost. It is essential to work with an experienced PCB manufacturer who can help you select the right material for your application and provide high-quality, reliable PCBs that meet your specifications.