What are High Tg PCBs?
High Tg PCBs, or high glass transition temperature PCBs, are a specialized type of PCB designed to withstand high temperatures.
Unlike normal PCBs which use standard FR-4 laminates, High Tg PCBs are made with high-performance thermoset insulating materials that have a glass transition temperature over 170°C. The glass transition temperature (Tg) is the point where the laminate transitions from a hard, glassy state to a soft, rubbery state when heated.
The higher Tg confers superior thermal performance and stability to High Tg PCBs compared to standard PCBs. This allows High Tg PCBs to operate in high-temperature environments up to 300°C without the integrity of the board being compromised.
Some of the key benefits and applications of High Tg PCBs include:
- Use in avionics and aerospace applications where operation at high altitudes requires tolerance of extreme temperature swings from -55°C to over 125°C.
- Automotive engine control units and monitoring systems under the hood which require robust performance in temperatures exceeding 150°C.
- Oil and gas drilling equipment that is exposed to high ambient temperatures.
- Industrial automation systems and robotics in high-temperature manufacturing processes.
- Medical devices and instrumentation need sterilization at over 170°C.
The specialized materials and fabrication of High Tg PCBs make them more expensive than standard PCBs. However, their ability to function reliably in high-temperature environments makes them indispensable for critical applications.
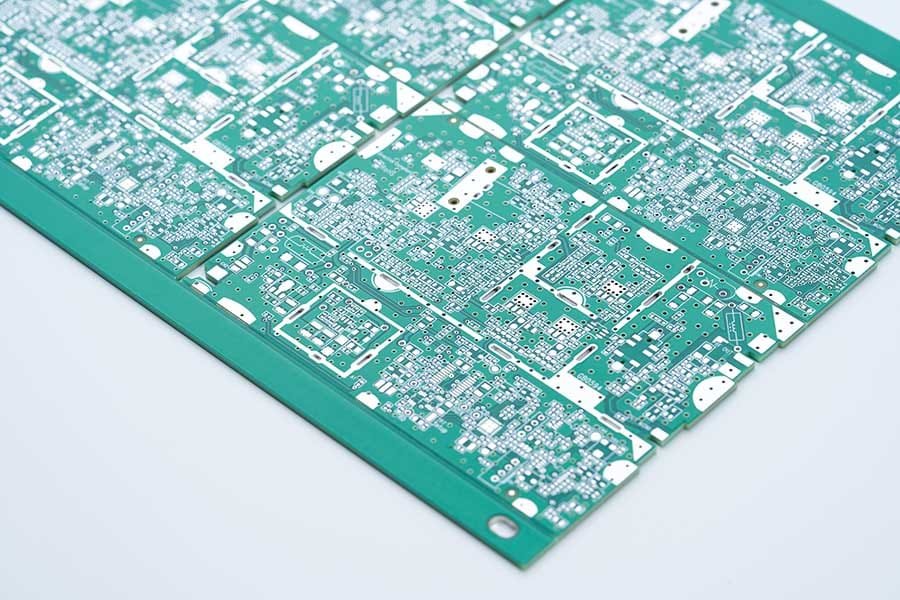
High Tg PCB Manufacturing Process
The process of producing High Tg PCBs involves material selection, cutting and drilling, layer stacking, lamination, drilling and plating, etching and solder mask application, silkscreen printing, and final inspection. Each step in the process is critical, and careful attention to detail is required to ensure the quality and reliability of the final product.
Step 1: Material Selection
High Tg PCBs require high-performance thermoset resins with high glass transition temperatures as well as reinforced laminates. Some commonly used materials include polyimide, BT epoxy, expanded PTFE composites, and ceramic-filled hydrocarbon laminates.
The laminate materials provide high heat resistance while reinforced substrates improve structural integrity at elevated temperatures. Compatible copper foils and prepregs are also required as raw materials.
Step 2: Material Cutting and Drilling
Once the materials have been selected, they are cut and drilled to create the desired circuit board shape. High-precision equipment is used to ensure that the circuit board is cut and drilled accurately.
Step 3: Layer Stacking
After the materials have been cut and drilled, they are stacked to create the final PCB. A typical High Tg PCB can have multiple layers, depending on the complexity of the circuit board design.
Step 4: Lamination
The layers of the circuit board are then laminated together using heat and pressure. During the lamination process, the layers are compressed, and the resin is activated, which causes the layers to bond together.
Step 5: Drilling and Plating
After the layers have been laminated together, the holes are drilled in the circuit board, and the plating process is performed. The plating process involves adding a layer of copper to the interior of the drilled holes to ensure that they are conductive.
Step 6: Etching and Solder Mask Application
Next, the circuit board is etched to remove any unnecessary copper. The etching process involves using chemicals to remove the excess copper, leaving only the required copper traces. After etching, a solder mask is applied to the circuit board to protect the copper traces and pads from damage during the soldering process.
Step 7: Silkscreen Printing
Finally, the circuit board is silkscreen printed with the required text and markings. This step is optional, but it is often performed to provide additional information about the circuit board, such as component labels and warning messages.
Once the production process is complete, the circuit board is inspected to ensure that it meets the required specifications. The inspection process includes visual inspection, electrical testing, and dimensional measurement.
Related Reading:
- A Guide to Multilayer PCB Manufacturing Process
- The Ultimate Guide to Aluminum PCB Manufacturing Process
- A Comprehensive Guide to Rigid Flex PCB Fabrication & Manufacturing Process
- Metal Core PCB Manufacturing Process Step by Step
- The Specialized Manufacturing Process for Heavy Copper PCBs
- How Single-Sided PCBs are Made: An In-Depth Look into the Manufacturing Process
Key Factors to Look for in a High Tg PCB Manufacturer
Choosing the right High Tg PCB manufacturer is crucial to ensure the quality and reliability of the circuit board. The following are key factors to consider when selecting a High Tg PCB manufacturer:
- Experience in High Tg PCB manufacturing: Look for a manufacturer with a proven track record in producing High Tg PCBs. They should have experience working with a range of materials and technologies and be able to provide references and samples.
- Quality of equipment and materials used: The manufacturer’s equipment and materials should be of high quality and regularly maintained to ensure consistent production quality.
- Robust Quality Systems: The manufacturer must have rigorous quality control and testing systems in place specifically for verifying High Tg PCBs meet the highest standards. Cleanroom assembly, comprehensive inspection, thermal stress testing and electrical/mechanical testing should all be standard.
- Competitive Pricing: While High Tg PCB costs are higher than standard PCBs, partner with a manufacturer that offers fair and reasonable pricing in line with their capabilities and service commitment. Avoid extremely high or low-ball prices.
- On-Time Delivery: While High Tg PCBs require longer manufacturing lead times, experienced partners will have streamlined workflows to deliver orders on-time. Quick-turnaround capabilities are also essential for prototyping needs.
- Compliance with industry standards and regulations: The manufacturer should follow industry standards and regulations to ensure the safety and reliability of their products.
- Technical expertise and customer support: The manufacturer should have a team of skilled technicians and engineers who can provide technical support and assist with any issues that may arise during the production process.
High Tg PCB Manufacturer in China
High Tg PCB manufacturing is a critical process that requires expertise and attention to detail to ensure the quality and reliability of the circuit board. By choosing a reputable High Tg PCB manufacturer, businesses can benefit from high-performance circuit boards that can withstand harsh environments and operate reliably over an extended period.
As a PCB manufacturer based in China, we are committed to providing high-quality high-Tg PCB prototype and mass production services to our customers worldwide. We use the latest technology and equipment to ensure that our High Tg PCBs meet the highest standards of quality, reliability, and performance.
If you are looking for a reliable and experienced High Tg PCB manufacturer, look no further than JHYPCB. Our team of experts is dedicated to delivering exceptional customer service and technical support, from initial design to final production.
Whether you need a prototype or a large volume of high-Tg PCBs, we can help. Contact us today at sales@pcbjhy.com to learn more about our services and how we can help you meet your High Tg PCB manufacturing needs. We look forward to hearing from you and working with you on your next project.