Flexible printed circuit boards, FPCs, or Flexible PCBs, are becoming increasingly popular in the electronics industry due to their many advantages over traditional rigid PCBs. Flexible PCBs are thin, lightweight, and can be designed to fit into tight spaces, making them ideal for compact electronic devices. They are also more reliable and durable, able to withstand repeated bending and flexing without damage. Flexible PCBs are cost-effective and offer enhanced signal integrity and electrical performance. However, some disadvantages are associated with flexible PCBs, such as limited thickness and layer count, as well as higher costs for low-volume production. Despite these challenges, flexible PCBs continue to find new applications in various industries and are expected to play a significant role in the future of electronics.
Advantages of Flexible PCBs
Flexible PCBs offer several advantages over traditional rigid PCBs, including:
- Flexibility and adaptability to complex designs: Flexible PCBs can be designed to fit into complex and irregularly shaped spaces that rigid PCBs cannot. This makes them ideal for applications where space is premium, such as mobile devices or wearables.
- Improved reliability and durability: Flexible PCBs are less prone to mechanical failure than rigid PCBs because they can withstand repeated bending and flexing without damage. This makes them ideal for applications where the PCB will be subjected to constant movement or vibration. A Fraunhofer Institute for Reliability and Microintegration study found that flexible PCBs have a significantly longer lifespan than rigid PCBs. The study found that after 10,000 bending cycles, flexible PCBs maintained their electrical performance, while rigid PCBs suffered from cracks and failures.
- Reduced size and weight: Because they are thinner and more flexible than rigid PCBs, flexible PCBs can be made smaller and lighter. This is particularly important for mobile devices, where space and weight are critical design factors. According to a report by Grand View Research, the global flexible PCB market size was valued at USD 13.34 billion in 2020 and is expected to grow at a compound annual growth rate (CAGR) of 11.4% from 2021 to 2028. The increasing demand for compact and lightweight electronic devices largely drives this growth.
- Cost-effective manufacturing: Flexible PCBs can be manufactured using automated processes, reducing production costs compared to rigid PCBs. They also require fewer parts and components, which can further reduce costs. A report by Technavio found that using flexible PCBs in the automotive industry can significantly reduce production costs. The report states that flexible PCBs can be produced using automated processes, reducing production time and costs compared to traditional PCBs.
- Enhanced signal integrity and electrical performance: Because flexible PCBs can be designed with a more direct path between components, they can offer improved signal integrity and electrical performance over rigid PCBs. This can be particularly important in high-speed and high-frequency applications. A study by the University of California, Berkeley found that flexible PCBs can improve signal integrity and electrical performance in high-frequency applications. The study found that flexible PCBs had lower losses and better impedance matching than rigid PCBs, which can improve overall system performance.
The flexibility, adaptability, and durability of flexible PCBs make them an attractive choice for a wide range of applications, from consumer electronics to aerospace and defense.
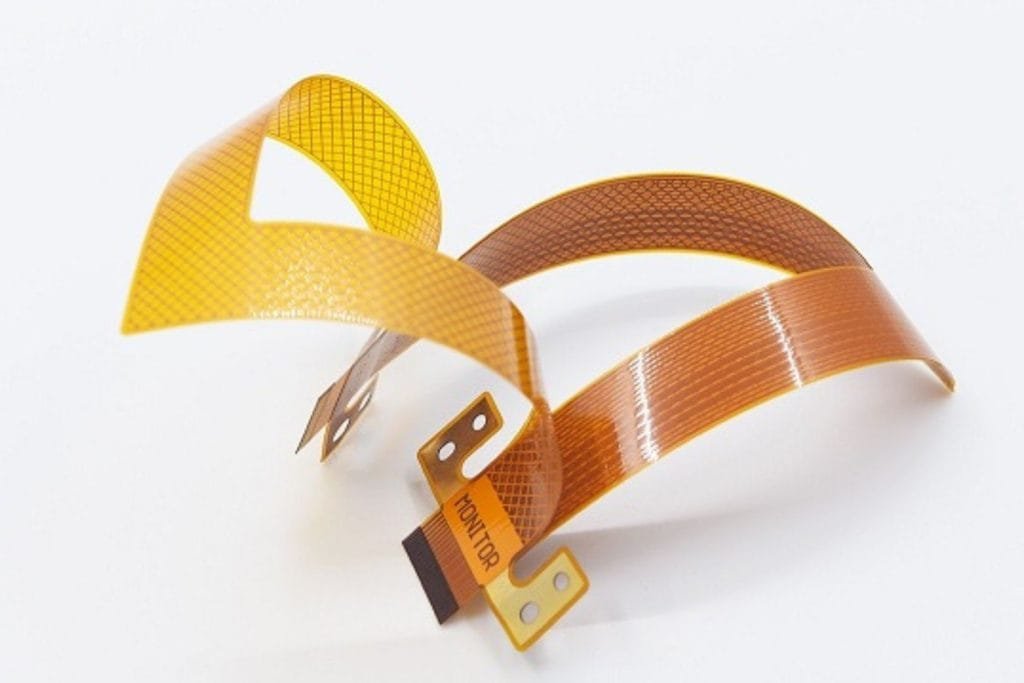
Disadvantages of Flexible PCBs
Flexible PCBs have many advantages over traditional rigid PCBs, such as greater flexibility, lighter weight, and increased durability. However, like any technology, they also have some disadvantages. Here are a few potential disadvantages of flexible PCBs:
- Cost: Flexible PCBs are typically more expensive than rigid PCBs. The additional cost is due to the higher manufacturing complexity and the special materials required to make the board flexible.
- Limited rigidity: While the flexibility of the PCB can be an advantage, it can also be a disadvantage. Flexible PCBs cannot support heavy components or provide the same level of mechanical stability as rigid PCBs.
- Limited thickness: Flexible PCBs are typically thinner than rigid PCBs, which can be an advantage in some applications. However, this can also limit the amount of copper used on the board, which can limit the board’s power handling capacity.
- More difficult to assemble: Flexible PCBs can be more difficult to assemble than rigid PCBs. The flexible material can make aligning and attaching components to the board challenging, especially for automated assembly processes.
- Environmental limitations: Flexible PCBs are not suitable for all environments. They may be susceptible to damage from moisture, dust, and temperature extremes.
- Limited layer count: Flexible PCBs typically have a lower layer count than rigid PCBs due to manufacturing constraints. This can limit the complexity of the circuits that can be created.
- Difficulty in repairing and reworking: Flexible PCBs can be more difficult to repair or rework than rigid PCBs due to the flexible material and the smaller size of the components used. This can increase the risk of damage to the board during repair or rework.
- Limited availability of materials and manufacturing processes: Compared to rigid PCBs, fewer materials and manufacturing processes are available for flexible PCBs. This can limit the options available for designers and increase the cost of manufacturing.
Considering these disadvantages is important when deciding whether to use a flexible PCB in your application. While flexible PCBs offer many advantages, they may not be the best choice for all projects.
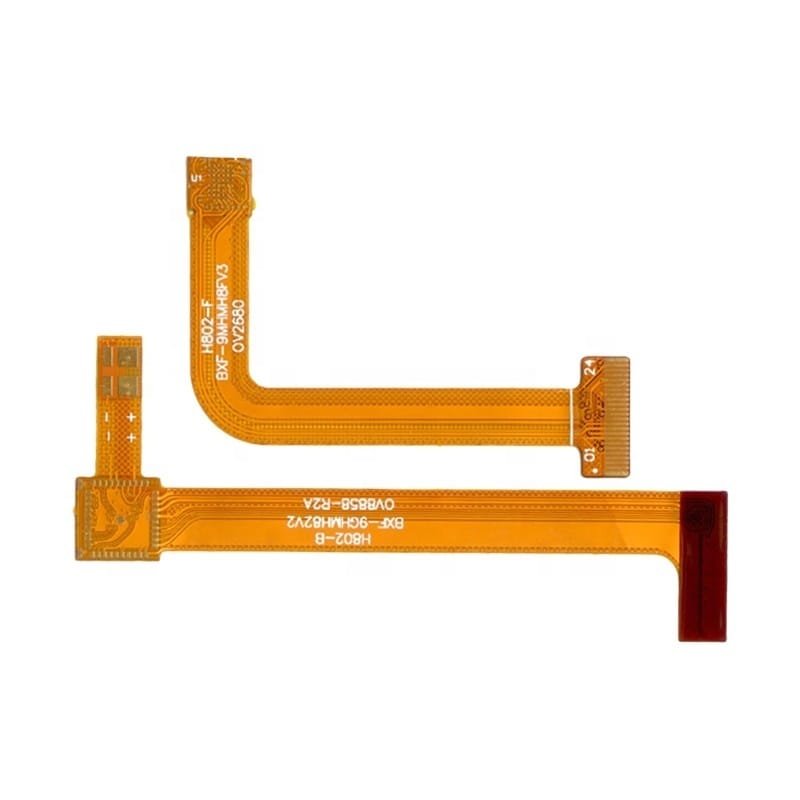
Applications of Flexible PCBs
Flexible PCBs are used in various applications where space, weight, and flexibility are important factors. Here are some common applications of flexible PCBs:
- Consumer electronics: Flexible PCBs are widely used in consumer electronics, such as smartphones, tablets, and wearables. They connect the various components of the device and can be bent or folded to fit into tight spaces.
- Automotive: Flexible PCBs are used in automotive applications to connect sensors, displays, and other electronic components. They are ideal for use in areas with limited space and where vibration and temperature extremes are common.
- Medical devices: Flexible PCBs are used in pacemakers, hearing aids, and medical implants. They are ideal for use in devices that need to be flexible and lightweight.
- Aerospace and defense: Flexible PCBs are used in aerospace and defense applications to connect satellites, rockets, and aircraft electronic components. They are ideal for use in areas with limited space and where weight is critical.
- Industrial automation: Flexible PCBs are used in industrial automation applications to connect sensors, controllers, and other electronic components. They are ideal for harsh environments with common temperature extremes, vibration, and dust.
- LED lighting: Flexible PCBs are used in LED lighting applications to connect the individual LED modules. They are ideal for use in lighting fixtures that need to be flexible and bendable.
Overall, flexible PCBs are ideal for any application that requires a flexible, lightweight, and durable PCB solution. They offer many advantages over rigid PCBs and are becoming increasingly popular in various industries.
Future prospects for flexible PCBs
The prospects for flexible PCBs in the electronics industry are very promising. Here are some reasons why:
- Growing demand for flexible and wearable electronics: The demand for flexible and wearable electronics is growing rapidly, driven by miniaturization, portability, and comfort. Flexible PCBs are an essential component of these devices and are expected to see increased demand in the future.
- Advancements in manufacturing technology: The manufacturing technology for flexible PCBs is rapidly advancing, making them easier and more cost-effective to produce. As a result, the price of flexible PCBs is expected to decrease, making them more accessible to a wider range of applications.
- Increased focus on lightweight and energy-efficient devices: The demand for lightweight and energy-efficient devices is increasing, particularly in industries such as aerospace, automotive, and renewable energy. Flexible PCBs can help to reduce the weight and improve the efficiency of these devices.
Development of new materials: Research is ongoing into the development of new materials for flexible PCBs, including materials that are more durable, more flexible, and more environmentally friendly. These materials are expected to further enhance the capabilities and applications of flexible PCBs in the future.
Overall, flexible PCBs are expected to play an increasingly important role in the electronics industry in the coming years as the demand for flexible, lightweight, and energy-efficient devices grows and as manufacturing technology and materials advance.