What is LED PCB?
At the heart of most modern lighting solutions lies a humble yet brilliant invention – the LED printed circuit board or LED PCB. These compact boards have revolutionized the way we illuminate our world, paving the way for energy-efficient, long-lasting, and versatile lighting systems.
An LED PCB is essentially a thin, rigid PCB board made of fiberglass or composite materials, with a maze-like pattern of copper traces etched onto its surface. These conductive pathways act as wires, allowing electricity to flow and power the light-emitting diodes (LEDs) mounted on the board.
Unlike traditional incandescent or fluorescent bulbs, LEDs are solid-state devices that produce light through electroluminescence. When an electrical current passes through the semiconductor material within the LED, it emits photons, resulting in a bright, energy-efficient glow.
LED PCBs come in various shapes and sizes, tailored to meet the specific requirements of different lighting applications. From sleek, linear strips for accent lighting to compact circular boards for downlights, these versatile boards enable designers to integrate LED technology seamlessly into their creations.
One of the key advantages of LED PCBs is their exceptional energy efficiency. LEDs consume significantly less power than conventional lighting sources, translating into lower energy bills and a reduced carbon footprint. Additionally, their solid-state construction renders them highly durable, capable of withstanding vibrations, shocks, and temperature fluctuations without compromising performance.
Beyond their practical benefits, LED PCBs have opened up a world of possibilities for creative lighting designs. With their ability to emit a wide range of colors, including dynamic RGB effects, these boards have become a canvas for artists, architects, and lighting professionals to paint their visions with light.
As technology continues to evolve, LED PCBs are poised to play an increasingly pivotal role in shaping the future of lighting. From smart home automation systems to large-scale architectural illumination, these unassuming boards are casting a brilliant light on the path towards a more energy-efficient and visually stunning world.
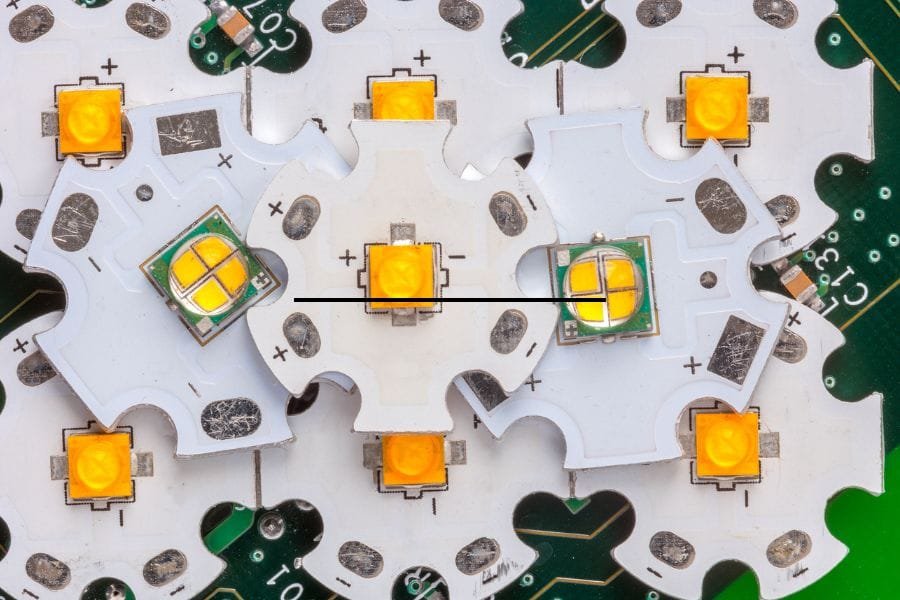
Bending the Rules: Flexible LED PCBs vs Rigid PCBs
While traditional rigid LED PCBs have paved the way for energy-efficient lighting solutions, a new breed of circuit boards is pushing the boundaries of what’s possible. Flexible LED PCBs, as the name suggests, are redefining the concept of lighting design by introducing an unprecedented level of versatility and creative freedom.
Unlike their rigid counterparts, which are constrained by their inflexible nature, flexible LED PCBs are crafted from specialized materials that allow them to bend, twist, and conform to virtually any shape imaginable. This game-changing characteristic opens up a world of possibilities for lighting designers and architects.
At the heart of a flexible LED PCB lies a thin, pliable substrate, often made from polyimide or other flexible polymers. These substrates replace the traditional fiberglass or composite materials found in rigid PCBs, allowing for a degree of flexibility that was previously unattainable.
The conductive traces on a flexible LED PCB are also engineered to withstand repeated bending and flexing without compromising their integrity. Specialized manufacturing techniques, such as laser direct imaging (LDI) and liquid photoimageable solder masks, ensure precise circuit etching and uniform coatings, even on these malleable surfaces.
But the advantages of flexible LED PCBs extend far beyond their ability to bend. Their lightweight and ultra-thin profiles make them ideal for applications where space is at a premium, such as wearable devices, automotive interiors, and architectural installations.
Moreover, flexible LED PCBs can withstand vibrations, impacts, and temperature fluctuations with ease, making them a reliable choice for harsh environments or dynamic applications where rigid boards may fail.
While rigid LED PCBs have their place in traditional lighting fixtures and static installations, flexible LED PCBs are opening up new frontiers in lighting design. From contoured accent lighting and curved signage to interactive art installations and wearable illumination, these innovative circuit boards are breathing new life into the world of lighting.
As technology continues to evolve, the line between rigid and flexible LED PCBs is blurring, with hybrid solutions like rigid-flex designs offering the best of both worlds. But one thing is certain: the future of lighting design is flexible, and those who embrace this new wave of innovation will be at the forefront of shaping the way we illuminate our world.
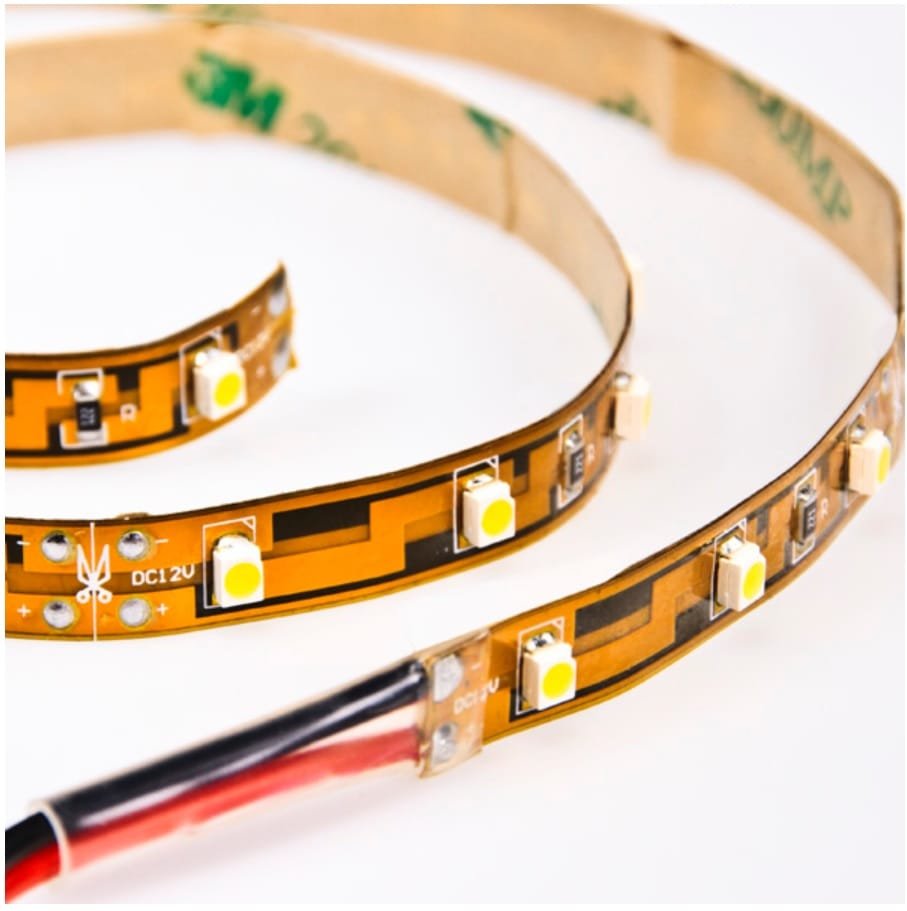
Advantages of Flexible LED PCBs
As the world of lighting technology continues to evolve, one innovation stands out as a true game-changer – flexible LED PCBs. These versatile circuit boards are redefining the boundaries of lighting design, offering a myriad of advantages that have the potential to revolutionize the way we illuminate our spaces.
- Unleashing Design Creativity
One of the most significant advantages of flexible LED PCBs is the unparalleled design freedom they offer. With their ability to bend, twist, and conform to virtually any shape, these malleable boards open up a world of possibilities that were once limited by the rigidity of traditional PCBs. Lighting designers and architects can now bring their most daring visions to life, creating curvaceous installations, organic shapes, and fluid lighting patterns that seamlessly integrate into their environments. - Lightweight and Ultra-Thin
Flexible LED PCBs are not only bendable but also remarkably lightweight and ultra-thin, making them ideal for applications where space is at a premium. From sleek wearable devices and compact automotive interiors to space-constrained architectural installations, these slim boards can illuminate even the tightest of spaces without compromising on aesthetics or functionality. - Durability in Motion
Unlike their rigid counterparts, flexible LED PCBs are engineered to withstand the rigors of dynamic environments. Their ability to flex and bend allows them to absorb vibrations, impacts, and repeated movements without compromising their integrity. This durability makes them well-suited for applications such as wearable technology, moving displays, and kinetic art installations, where traditional rigid PCBs may be prone to failure. - Energy Efficiency and Environmental Friendliness
Inheriting the energy-efficient nature of LED technology, flexible LED PCBs offer significant energy savings compared to conventional lighting solutions. By consuming less power, they not only reduce operational costs but also contribute to a smaller carbon footprint, aligning with the growing demand for sustainable and eco-friendly products. - Seamless Integration
The versatility of flexible LED PCBs extends beyond their physical properties. These innovative boards can be seamlessly integrated into a wide range of products and applications, from sleek wearable devices and contoured automotive lighting to architectural installations and interactive art pieces. Their ability to conform to various shapes and surfaces allows for a seamless fusion of form and function, creating cohesive and visually striking designs.
As the world continues to embrace the endless possibilities of flexible LED PCBs, lighting designers and architects are poised to push the boundaries of creativity further than ever before. With their unique advantages, these luminous boards are not just illuminating our spaces but also shedding light on the future of lighting design itself.
Applications of flexible LED PCBs
As flexible LED PCBs continue to revolutionize the lighting industry, their application potential is truly boundless. From high-tech wearables and cutting-edge automotive designs to breathtaking architectural installations and avant-garde art pieces, these malleable circuit boards are leaving their luminous mark across diverse sectors.
1. Wearable Technology: Shining a Light on Innovation The wearable technology sector has embraced flexible LED PCBs with open arms, recognizing their unique ability to seamlessly blend illumination with ergonomic design. Fitness trackers, smartwatches, and even apparel now feature sleek, contoured lighting elements that not only enhance visibility but also add a touch of futuristic flair.
In the world of fashion, designers are pushing the boundaries of creativity by integrating flexible LED strips into clothing, accessories, and even footwear, transforming ordinary garments into stunning runway statements. From mesmerizing light displays on dresses to pulsating patterns on shoes, the possibilities are limitless.
2. Automotive Illumination: Driving Innovation Forward The automotive industry has long recognized the importance of lighting in enhancing safety, visibility, and aesthetic appeal. With flexible LED PCBs, car manufacturers are reimagining interior and exterior lighting, creating dynamic, eye-catching designs that were once mere concepts.
Contoured ambient lighting, sleek turn signal indicators, and even interactive displays are now a reality, thanks to the versatility of these bendable circuit boards. From illuminated door sills that welcome passengers with a warm glow to sweeping light signatures that define a vehicle’s unique identity, flexible LED PCBs are elevating the automotive experience to new heights.
3. Architectural Marvels: Sculpting Light and Space In the realm of architecture and interior design, flexible LED PCBs are enabling a seamless fusion of light and form. Architects and designers can now integrate lighting seamlessly into their creations, transforming surfaces, walls, and even ceilings into luminous canvases.
Imagine a lobby adorned with a sinuous, glowing reception desk that seemingly defies gravity, or a modern staircase with each step emitting a soft, inviting glow. These awe-inspiring installations are made possible by the malleability of flexible LED PCBs, allowing light to sculpt and accentuate architectural elements in ways that were once inconceivable.
4. Artistic Expressions: Illuminating Creativity For artists seeking to push the boundaries of their medium, flexible LED PCBs offer a brilliant new canvas. Interactive installations, kinetic sculptures, and immersive light displays are just a few examples of how these versatile circuit boards are transforming the art world.
Imagine a mesmerizing light sculpture that undulates and shifts with each movement, or a large-scale projection that seamlessly conforms to the contours of its surroundings. These captivating creations not only challenge traditional notions of art but also inspire viewers to reimagine the interplay between light, form, and space.
As flexible LED PCBs continue to illuminate our world, their impact extends far beyond mere illumination. They are catalyzing innovation, sparking creativity, and redefining the boundaries of design across diverse industries and disciplines. With each new application, these luminous circuit boards are casting a brilliant light on the future of lighting technology and beyond.
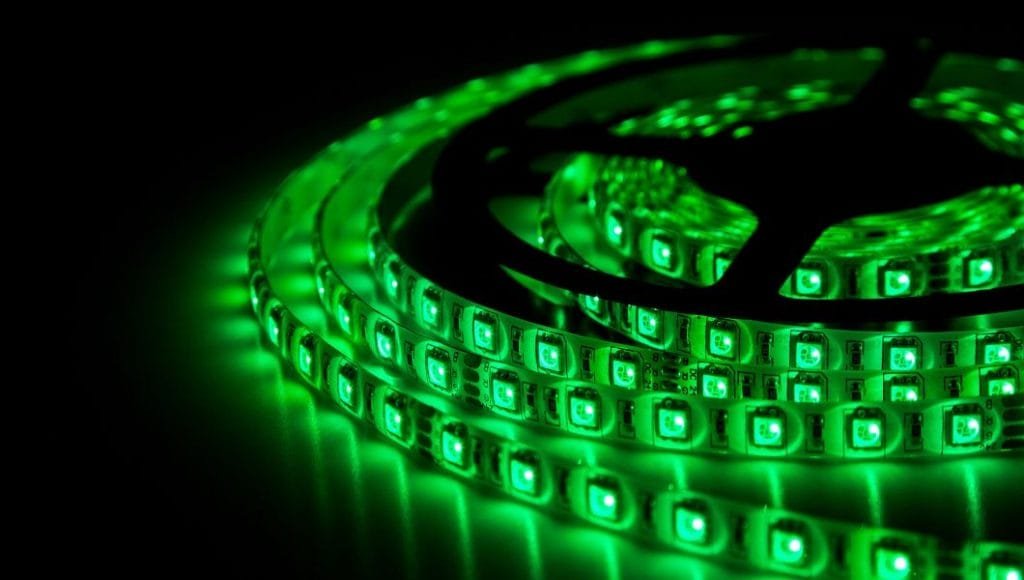
Mastering the Art of Flexible Design: Considerations for LED PCBs
While flexible LED PCBs offer unparalleled creative freedom, their unique properties also demand a thoughtful and meticulous approach to design. From material selection to thermal management, several factors must be carefully considered to ensure optimal performance, reliability, and longevity. Let’s delve into the critical design considerations that govern the world of flexible LED lighting solutions.
Material Selection: Finding the Perfect Flex
At the heart of any flexible LED PCB lies a carefully chosen substrate material that enables its malleable nature. Polyimide, a high-performance polymer, is a popular choice due to its exceptional flexibility, thermal stability, and resistance to harsh environments.
However, the substrate is not the only material consideration. The copper traces, which carry the electrical current, must be designed to withstand repeated bending without cracking or compromising conductivity. Specialized techniques, such as strategically patterned copper layouts and optimized trace thicknesses, are employed to achieve this flexibility.
Component Placement: Balancing Flexibility and Functionality
The placement of components on a flexible LED PCB is a delicate dance between accommodating the board’s flexing capabilities and ensuring optimal functionality. Dense clusters of components can inhibit flexibility and increase the risk of solder joint failure, necessitating a thoughtful distribution of elements across the board.
Manufacturers often employ stress-relief techniques, such as strategic component positioning and flexible solder joint designs, to mitigate the effects of bending and flexing. Additionally, the use of specialized adhesives and encapsulation materials can help secure components in place, preventing them from becoming dislodged during dynamic applications.
Thermal Management: Keeping Cool Under Pressure
One of the inherent challenges of flexible LED PCBs is their propensity for heat buildup, particularly in dense, high-power applications. Unlike their rigid counterparts, which can dissipate heat through larger copper planes or metal cores, flexible boards must employ alternative thermal management strategies.
Designers may incorporate strategically placed copper areas or embedded heat-spreading materials to facilitate heat dissipation. In some cases, active cooling solutions, such as miniature fans or heat sinks, may be employed to ensure optimal thermal performance and longevity.
Reliability Testing: Ensuring Long-lasting Illumination
The dynamic nature of flexible LED PCBs introduces unique reliability challenges that must be addressed through rigorous testing. Accelerated life testing, which simulates real-world bending and flexing conditions, is crucial to identify potential failure points and validate the board’s durability over its intended lifespan.
Environmental testing, such as humidity, temperature cycling, and vibration testing, further ensures that the flexible PCB can withstand the rigors of its intended application environment. Manufacturers often employ advanced inspection techniques, such as X-ray and optical inspection, to scrutinize the integrity of solder joints and component connections before and after reliability testing.
Design for Manufacturability (DFM): Bridging Concept and Reality
As with any PCB design, flexible LED PCBs must adhere to strict design for manufacturability (DFM) guidelines to ensure seamless and cost-effective production. These guidelines cover critical aspects such as trace spacing, bend radius limitations, and component clearances, all of which are tailored to the unique requirements of flexible circuit manufacturing.
Close collaboration between designers and experienced flexible PCB manufacturers is essential to navigate these DFM guidelines and optimize the design for efficient fabrication, assembly, and long-term performance.
By carefully considering these design factors, lighting engineers and manufacturers can unlock the full potential of flexible LED PCBs, creating innovative and reliable lighting solutions that push the boundaries of what’s possible in illumination.
The Making of Flexible LED PCBs
Behind every brilliant and bendable flexible LED PCB lies a meticulous manufacturing process that blends cutting-edge technology with time-honored craftsmanship. From the precise etching of conductive pathways to the delicate assembly of miniature components, each step is a testament to the skill and expertise required to bring these luminous circuits to life.
Imaging Precision: Where Light Meets Circuitry
The journey begins with a process called laser direct imaging (LDI), where a high-precision laser beam dances across the flexible substrate, etching intricate patterns that will become the conductive traces. This advanced imaging technique ensures unparalleled accuracy, allowing for the creation of even the most complex circuit designs on the malleable surface.
Handling with Care: The Art of Material Mastery
As the circuit takes shape, skilled technicians must handle the delicate flexible materials with the utmost care. Specialized techniques are employed to prevent any shifting, stretching, or damage to the thin substrates and fragile copper layers during the various manufacturing stages.
Alignment Artistry: Layering Perfection
In the case of multilayer flexible PCBs, the alignment of each individual layer becomes a critical endeavor. Sophisticated equipment and meticulous procedures are utilized to ensure precise registration, preventing any misalignments that could compromise the board’s integrity and performance.
Etching Expertise: Revealing the Conductive Pathways
Once the layers are aligned, a carefully controlled etching process removes the excess copper, revealing the intricate network of conductive traces. Specialized etchants and techniques are employed to prevent over-etching, preserving the delicate copper pathways that will carry the electrical current.
Solder Mask Artistry: Protecting the Paths
To safeguard the conductive traces and facilitate component assembly, a liquid photoimageable solder mask is applied with precision. This protective coating not only insulates the circuitry but also provides a uniform surface for subsequent assembly processes.
Assembling Illumination: Placing Every Component
With the circuit pathways secured, skilled technicians meticulously place each component, from tiny surface-mount LEDs to intricate integrated circuits. Specialized assembly techniques, such as flexible solder joint designs and advanced pick-and-place machines, ensure accurate and reliable component placement on the bendable substrate.
Inspection and Testing: Ensuring Luminous Perfection
Before these flexible LED PCBs can illuminate the world, they must undergo rigorous inspection and testing processes. Advanced optical and X-ray techniques scrutinize every aspect of the board, from solder joint integrity to component placement accuracy. Dynamic flexing tests validate the board’s ability to withstand repeated bending without compromising performance.
This intricate manufacturing journey, from imaging to assembly and testing, is a true celebration of human ingenuity and technological mastery. Each flexible LED PCB that emerges from this process is a testament to the dedication and skill of the engineers, technicians, and artisans who have poured their expertise into its creation.
As these luminous circuits make their way into innovative products and installations, they carry with them the craftsmanship and attention to detail that have become hallmarks of the flexible PCB manufacturing industry. It is this commitment to excellence that continues to push the boundaries of what’s possible in lighting technology and beyond.
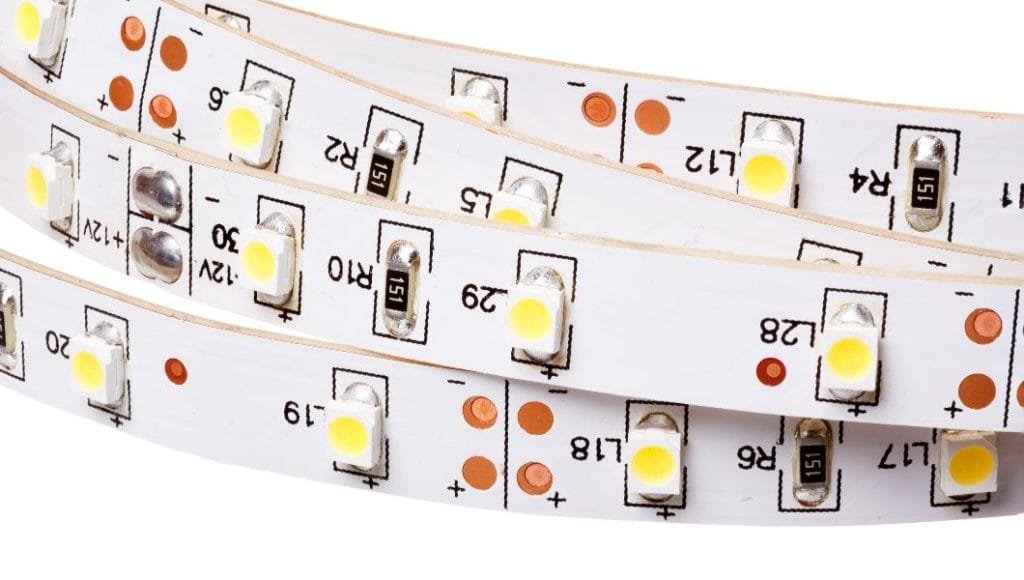
The Brilliant Future of Flexible Illumination
As the world continues to embrace the boundless potential of flexible LED PCBs, the horizon is alight with exciting possibilities. These innovative circuit boards are not only reshaping the landscape of lighting design but also paving the way for groundbreaking applications that blur the lines between illumination, technology, and art.
Interactive Artistry: Illuminating Experiences
In the realm of artistic expression, flexible LED PCBs are enabling a new era of immersive and interactive installations. Imagine stepping into a captivating light sculpture that responds to your movements, with each step causing a ripple of luminous patterns to radiate across its contoured surfaces.
These kinetic artworks, powered by the malleability and responsiveness of flexible LED circuits, have the ability to transform spaces into living, breathing canvases of light and color. Visitors become active participants, their presence and actions shaping the ever-evolving display, blurring the boundaries between observer and creator.
Shapeshifting Displays: Redefining Visual Experiences
The world of digital displays is poised for a revolution, and flexible LED PCBs are at the forefront of this transformation. Envision a seamless, wraparound display that conforms to the contours of a vehicle’s interior, providing drivers and passengers with an immersive visual experience that transcends traditional flat screens.
Or imagine a storefront that captures the attention of passersby with a dynamic, undulating display that seems to defy the laws of physics. These shapeshifting displays, enabled by the flexibility and resilience of specialized LED PCBs, promise to redefine the way we interact with digital content, creating engaging and visually stunning experiences that were once the stuff of science fiction.
Wearable Illumination: Lighting Up Personal Expression
The intersection of fashion and technology has given rise to a new breed of wearable illumination, and flexible LED PCBs are at the heart of this sartorial revolution. From haute couture gowns adorned with intricate light patterns to athletic apparel that glows in sync with the wearer’s movements, the possibilities are limitless.
Beyond mere aesthetics, these luminous garments have the potential to enhance safety, visibility, and even personal expression. Imagine a cycling jacket that automatically illuminates in low-light conditions, or a performance costume that responds to the dancer’s movements with a dazzling display of light and color.
As flexible LED PCBs continue to push the boundaries of what’s possible, new and unforeseen applications will undoubtedly emerge. From smart cities adorned with dynamic, energy-efficient lighting to groundbreaking medical devices that harness the power of illumination for healing and diagnostics, the future is bright with possibilities.
However, one thing is certain: the marriage of flexibility, illumination, and innovation will continue to inspire and captivate, ushering in a new era of lighting technology that transcends mere illumination and transforms the way we experience and interact with light itself.
Selecting a Flexible LED PCB Manufacturer
As the demand for flexible LED PCBs continues to soar, finding a reliable and capable manufacturing partner has become paramount for companies looking to bring their innovative lighting solutions to life. With the unique complexities involved in producing these malleable circuits, not all PCB manufacturers are equipped to deliver the level of quality and expertise required.
To ensure your flexible LED PCB project shines bright, it’s crucial to partner with a manufacturer that possesses a deep understanding of the intricacies involved in this specialized domain. Here are some key factors to consider when evaluating potential flexible PCB suppliers:
- Extensive Flexible Circuit Expertise
Flexible PCBs are a breed apart from their rigid counterparts, requiring specialized knowledge and techniques throughout the manufacturing process. Look for a partner with a proven track record in producing high-density, high-reliability flexible circuits across a range of applications. Their experience should span everything from material selection and circuit design to assembly and testing procedures tailored for flexible boards. - Dedicated Flexible PCB Manufacturing Capabilities
While some PCB manufacturers may offer flexible circuit production as an ancillary service, it’s best to partner with a company that has dedicated flexible PCB manufacturing capabilities. This ensures that your project receives the focused attention and specialized resources it deserves, minimizing the risk of delays or quality issues that can arise from a lack of dedicated expertise. - Stringent Quality Assurance Processes
The dynamic nature of flexible LED PCBs introduces unique reliability challenges that must be addressed through rigorous quality assurance processes. Seek out a manufacturer that employs advanced inspection techniques, such as X-ray analysis and optical inspection, specifically optimized for flexible circuits. Additionally, inquire about their accelerated life testing procedures, which simulate real-world bending and flexing conditions to validate long-term durability. - Advanced High-Density Interconnect (HDI) Capabilities
As flexible LED PCB designs continue to push the boundaries of complexity and miniaturization, the ability to produce high-density interconnect (HDI) boards becomes increasingly valuable. Look for a partner with proven expertise in HDI manufacturing techniques, such as laser direct imaging (LDI), micro-via formation, and precise layer alignment processes, ensuring your high-density flexible circuits meet the highest standards of quality and performance. - Collaborative Design and Engineering Support
Designing for flexibility requires a specialized skillset and an intimate understanding of the unique challenges and considerations involved. Partner with a manufacturer that offers comprehensive design and engineering support services, enabling close collaboration throughout the development process. Their expertise can help optimize your design for manufacturability, ensuring seamless production and long-term reliability. - Vertically Integrated Production Capabilities
Vertical integration, where a manufacturer controls multiple stages of the production process, can be a significant advantage in the flexible PCB realm. By having capabilities spanning everything from substrate fabrication to assembly and testing under one roof, vertically integrated suppliers can offer streamlined operations, tighter quality control, and enhanced supply chain visibility.
As the world of lighting technology continues to evolve, choosing the right flexible LED PCB manufacturing partner has become a strategic decision that can make or break a product’s success. By carefully evaluating potential suppliers against these key criteria, companies can ensure they have a trusted ally capable of bringing their most ambitious and innovative lighting solutions to brilliant reality.
Related Reading:
- LED PCB Design Guide: Tips and Best Practices for Manufacturers
- The Best Materials for LED PCB Boards
- Expand Your LED Lighting With Custom LED PCBs
- Designing Aluminum PCBs for Efficient Thermal Management
- Applications of Aluminum PCB: A Comprehensive Overview
- The Ultimate Guide to Aluminum PCB Manufacturing Process
- The Importance of Choosing the Right Aluminum PCB Manufacturer
- An Introduction to Aluminum Substrate PCB Types
- A Comparison of Aluminum Core PCBs and Copper Core PCBs
- Comparative Analysis of Aluminum PCB and FR-4 PCB
- What Are The Types of Metal Core PCBs?