Flex circuits, also known as flexible printed circuits or FPCs, are specialized electronic interconnects constructed using flexible materials. Unlike traditional rigid printed circuit boards (PCBs), flex circuits can bend, twist, and conform to complex shapes, making them ideal for use in various applications, from medical devices to consumer electronics. However, the success of a flex circuit depends heavily on the materials used in its construction. The choice of the flexible substrate, conductive materials, adhesive materials, and coverlay materials can significantly impact the circuit’s performance, reliability, and durability. In this blog post, we will explore the different materials used in flex circuits and their importance in creating successful and reliable electronic interconnects.
Flexible Substrate Materials
Flexible substrate materials are a crucial component of flex circuits, as they provide the foundation for the circuit’s construction and flexibility. Several materials are commonly used in the production of flex circuits, each with unique characteristics and advantages. Here are some of the most common flexible substrate materials used in flex circuits:
- Polyimide (PI): This is the most commonly used material in flex circuit production. It offers excellent thermal stability, chemical resistance, and mechanical properties, making it suitable for various applications.
Material Polyimide (PI) Thermal Stability Excellent Chemical Resistance Excellent Mechanical Properties Good Electrical Insulation Good Maximum Operating Temperature ~260°C Cost Moderate - Polyester (PET): This is a lower-cost alternative to polyimide, with good mechanical properties and electrical insulation. However, it is less thermally stable than polyimide and has a lower maximum operating temperature.
Material Polyester (PET) Thermal Stability Good Chemical Resistance Good Mechanical Properties Good Electrical Insulation Good Maximum Operating Temperature ~150°C Cost Low - Liquid Crystal Polymer (LCP): This material offers superior mechanical strength and dimensional stability compared to polyimide and polyester. It is ideal for high-temperature applications, such as in the aerospace and automotive industries.
Material Liquid Crystal Polymer (LCP) Thermal Stability Excellent Chemical Resistance Excellent Mechanical Properties Excellent Electrical Insulation Excellent Maximum Operating Temperature ~300°C Cost High
Each of these materials has its advantages and disadvantages, and the choice of material depends on the application’s specific requirements. The flexible substrate material’s thickness, surface finish, and other properties can also affect the overall performance of the flex circuit. Therefore, carefully considering the substrate material is crucial to ensure the success and reliability of the flex circuit.
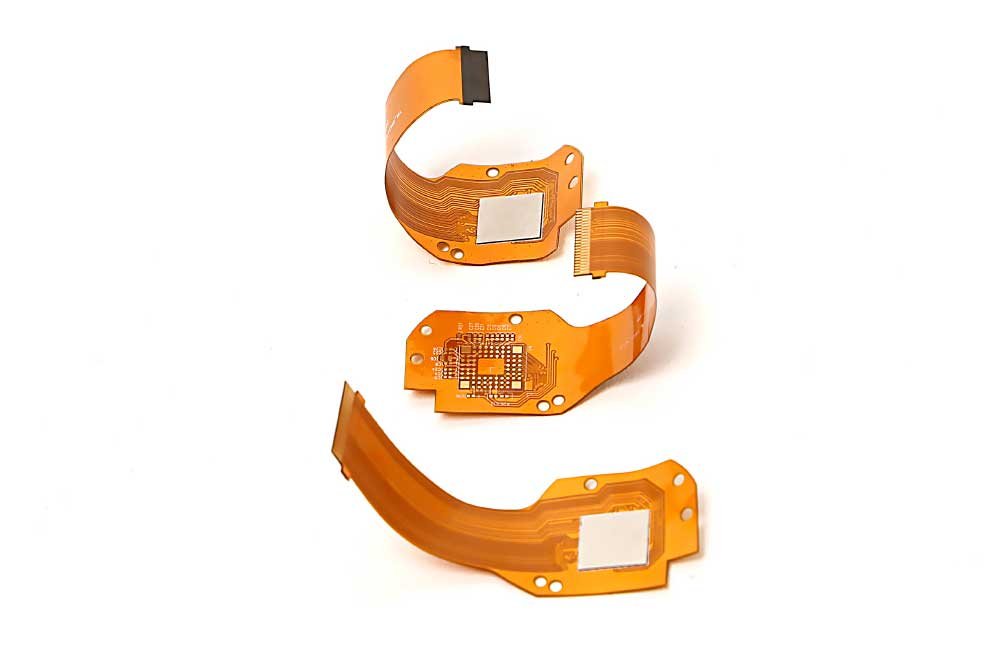
Conductive Materials
Conductive materials are used in flex circuits to provide electrical connectivity between components and traces on the flexible substrate. Several types of conductive materials can be used to construct flex circuits, each with unique properties and advantages. Here are some of the most common conductive materials used in flex circuits:
- Copper: Copper is the most commonly used conductive material in flex circuits due to its high conductivity, low cost, and ease of manufacturing. It is typically applied as a thin layer of copper foil or electroplated onto the flexible substrate.
- Silver: Silver is a highly conductive material that offers superior conductivity to copper. However, it is also more expensive and difficult to work with due to its high reactivity with oxygen and other materials.
- Gold: Gold is often used in flex circuits for its excellent corrosion resistance and stable electrical conductivity. It is typically applied as a thin layer using electroplating or other deposition methods.
- Conductive Polymer: Conductive polymers, such as PEDOT: PSS (poly(3,4-ethylenedioxythiophene): polystyrene sulfonate), are a newer type of conductive material that offers flexibility, transparency, and compatibility with organic materials. They are often used in flexible displays, sensors, and other applications that require high flexibility and low weight.
Here is a table comparing the properties of the four conductive materials commonly used in flex circuits:
Material | Copper | Silver | Gold | Conductive Polymer |
---|---|---|---|---|
Conductivity | High | Very High | High | Medium |
Corrosion Resistance | Good | Poor | Excellent | Poor |
Cost | Low | High | Very High | Medium |
Manufacturing Complexity | Low | Medium | High | Medium |
Bonding to Substrate | Good | Good | Good | Poor |
Maximum Operating Temperature | ~150°C | ~300°C | ~200°C | ~80°C |
Each of these conductive materials has its unique advantages and disadvantages, and the choice of material depends on the application’s specific requirements. The thickness, surface finish, and other properties of the conductive material can also affect the overall performance of the flex circuit. Therefore, careful consideration of the conductive material is crucial to ensure the success and reliability of the flex circuit.
Adhesive Materials
Adhesive materials are used in flex circuits to bond layers of the flexible substrate and components together. The adhesive must have good adhesion to the substrate and components while providing mechanical stability, electrical insulation, and resistance to temperature and environmental conditions. Here are some common adhesive materials used in the construction of flex circuits:
- Acrylic Adhesives: Acrylic adhesives are a popular choice for bonding flex circuit components due to their high strength, temperature, and chemical resistance. They can also be designed to have low outgassing properties, which is important in applications where contamination must be minimized.
- Epoxy Adhesives: Epoxy adhesives are widely used in flex circuits for their high strength, excellent adhesion to a wide range of substrates, and good chemical resistance. They are often used in applications that require high-temperature resistance and high vibration-resistance.
- Polyimide Adhesives: Polyimide adhesives are designed for flex circuits and provide excellent adhesion to polyimide substrates. They have good thermal stability and are resistant to various chemicals.
- Pressure-Sensitive Adhesives (PSAs): PSAs are adhesives that can be applied to one or both sides of the flexible substrate as a thin film. They provide good adhesion to various surfaces and are easy to apply. However, they typically have lower strength and temperature resistance than other adhesive types.
- Silicone Adhesives: Silicone adhesives are commonly used in applications that require flexibility and vibration resistance. They have good temperature resistance and are resistant to a wide range of chemicals.
Here is a table comparing some of the properties of the different adhesive materials used in flex circuits:
Adhesive Material | Acrylic | Epoxy | Polyimide | PSA | Silicone |
---|---|---|---|---|---|
Temperature Resistance | -40°C to +150°C | -55°C to +150°C | -269°C to +260°C | -40°C to +120°C | -55°C to +200°C |
Chemical Resistance | Good | Good | Excellent | Fair | Good |
Mechanical Strength | High | High | High | Low to Medium | Low to Medium |
Curing Time | Fast to Medium | Medium to Slow | Fast to Medium | N/A | Fast to Medium |
Thickness | 25-125 μm | 25-75 μm | 12-25 μm | 12-50 μm | 25-75 μm |
Dielectric Strength | 1-2 kV/mil | 0.5-1.5 kV/mil | 1-2 kV/mil | 0.5-1.5 kV/mil | 0.5-1.5 kV/mil |
The choice of adhesive material depends on the application’s specific requirements, including temperature resistance, chemical resistance, and mechanical stability. The thickness, viscosity, and curing time of the adhesive can also affect the overall performance of the flex circuit. Therefore, careful consideration of the adhesive material and its properties is crucial to ensure the success and reliability of the flex circuit.
Coverlay Materials
Coverlay materials are typically used as protective layers on the flex circuit to provide additional mechanical protection, insulation, and environmental resistance. Here are some common types of coverlay materials used in flex circuits:
Polyimide Coverlay: Polyimide coverlay is a popular choice for flex circuits due to its high-temperature resistance, good chemical resistance, and mechanical strength. It is typically used in applications that require long-term reliability and stability, such as aerospace, automotive, and medical devices.
Polyester Coverlay: Polyester coverlay is a lower-cost alternative to polyimide coverlay, with good mechanical and chemical properties. It is typically used in applications that require moderate temperature and chemical resistance, such as consumer electronics and appliances.
Liquid Photoimageable Coverlay (LPI): LPI is a type of coverlay applied as a liquid coating and then cured using ultraviolet (UV) light. It offers high resolution, good substrate adhesion, and flexibility. It is typically used in applications that require precise alignment and high reliability, such as automotive and aerospace electronics.
Thermoplastic Coverlay: Thermoplastic coverlay is a flexible plastic film that can be heat-bonded to the substrate using a heated roller. It offers good mechanical strength and flexibility and can be easily removed. It is typically used in applications that require low cost and short lead times, such as consumer electronics.
Here are some key properties of the common types of coverlay materials used in flex circuits:
Coverlay Material | Polyimide | Polyester | LPI | Thermoplastic |
---|---|---|---|---|
Temperature Resistance | -269°C to +400°C | -40°C to +150°C | -40°C to +150°C | -40°C to +150°C |
Chemical Resistance | Excellent | Good | Good | Fair |
Mechanical Strength | High | Medium | Medium | Low to Medium |
Thickness | 12-50 μm | 25-75 μm | 25-50 μm | 12-50 μm |
Surface Finish | Matte, Glossy, Textured | Matte, Glossy | Matte, Glossy | Matte, Glossy |
The choice of coverlay material depends on the application’s specific requirements, including temperature and chemical resistance, mechanical strength, and cost. The thickness and surface finish of the coverlay can also affect the overall performance of the flex circuit. Therefore, careful consideration of the coverlay material and its properties is crucial to ensure the success and reliability of the flex circuit.
Conclusion
In conclusion, flex circuits are an important technology that enables the creation of lightweight, compact, and highly functional electronic devices. The materials used in flex circuits play a critical role in determining the circuit’s performance, reliability, and cost-effectiveness. The key materials used in flex circuits include a flexible substrate, conductive, adhesive, and coverlay materials.
Flexible substrate materials such as polyimide, PET, and PEN offer different combinations of temperature resistance, mechanical strength, and flexibility to suit various applications. Conductive materials such as copper and silver provide good electrical conductivity and adhesion to the substrate. Adhesive materials such as acrylic, epoxy, and polyimide provide strong bonding and environmental protection. Coverlay materials such as polyimide, polyester, LPI, and thermoplastic provide additional mechanical protection and insulation.
Future developments in flex circuit materials will likely focus on improving their performance in areas such as temperature and chemical resistance, mechanical strength, and flexibility. Additionally, there is a growing demand for eco-friendly and sustainable materials that can reduce the environmental impact of electronic devices.
The continued advancement of flex circuit materials is expected to drive innovation in various industries, including aerospace, automotive, medical, and consumer electronics.