Flex PCB is a flexible printed circuit board widely used in various fields due to its unique advantages. However, when designing and manufacturing Flex PCBs, it is often necessary to consider the issues of flexibility and stability. To solve these problems, the Flex PCB stiffener was developed to improve the rigidity of the flexible circuit board and maintain its shape. In this article, we will delve into the topic of Flex PCB stiffeners and explore their various aspects, including types, design principles, manufacturing methods, applications, and advantages and disadvantages. This ultimate guide aims to provide readers with a comprehensive understanding of Flex PCB stiffeners and their role in the electronics industry.
Types of Flex PCB stiffener
Flex PCB stiffeners are essential components in flexible printed circuit boards that improve rigidity and stability, making them suitable for various applications. The selection of the appropriate stiffener material depends on the required degree of rigidity, the application environment, and the manufacturing process. This section will explore the different types of Flex PCB stiffeners, including plastic materials like FR4, PI, and PET, and metal materials such as copper, aluminum, and steel. By understanding the characteristics and properties of each material, designers can select the optimal stiffener for their specific application.
A. Plastic materials
- FR4:
FR4, also known as glass-reinforced epoxy laminate, is a composite material commonly used as a stiffener for Flex PCBs. It is made from layers of woven glass cloth impregnated with an epoxy resin binder. FR4 offers excellent dimensional stability, mechanical strength, and electrical insulation properties. It can withstand high temperatures, making it suitable for harsh environments. - PI:
Polyimide (PI) is a thermoplastic material with excellent mechanical properties, high tensile strength, modulus, and creep resistance. It has a high resistance to temperature, chemicals, and radiation, making it suitable for applications that require high-temperature resistance, such as in the aerospace industry. - PET:
Polyethylene terephthalate (PET) is a thermoplastic polymer with good mechanical properties and thermal stability. It is commonly used in Flex PCBs as a low-cost alternative to other materials. PET is flexible and easy to handle, making it ideal for use in applications that require repeated flexing.
B. Metal materials
- Copper:
Copper is widely used in Flex PCB stiffeners due to its excellent electrical conductivity and thermal stability. It is easy to process and cheap, making it an ideal choice for high-volume applications. Copper stiffeners are typically used in applications that require high levels of electromagnetic interference (EMI) shielding. - Aluminum:
Aluminum is a lightweight metal with excellent thermal conductivity and a high strength-to-weight ratio. It is commonly used in Flex PCB stiffeners due to its ease of processing, low cost, and high thermal stability. Aluminum stiffeners are often used in applications requiring mechanical support and heat dissipation. - Steel:
Steel is a durable and strong material that offers high rigidity and stability to Flex PCBs. It is commonly used in applications that require high levels of mechanical strength, such as in the automotive industry. Steel stiffeners can be made in various thicknesses and shapes, making them suitable for different applications.
By understanding the properties and characteristics of each type of Flex PCB stiffener, designers can select the optimal material for their specific application. The selection of the appropriate stiffener material depends on the required degree of rigidity, the application environment, and the manufacturing process.
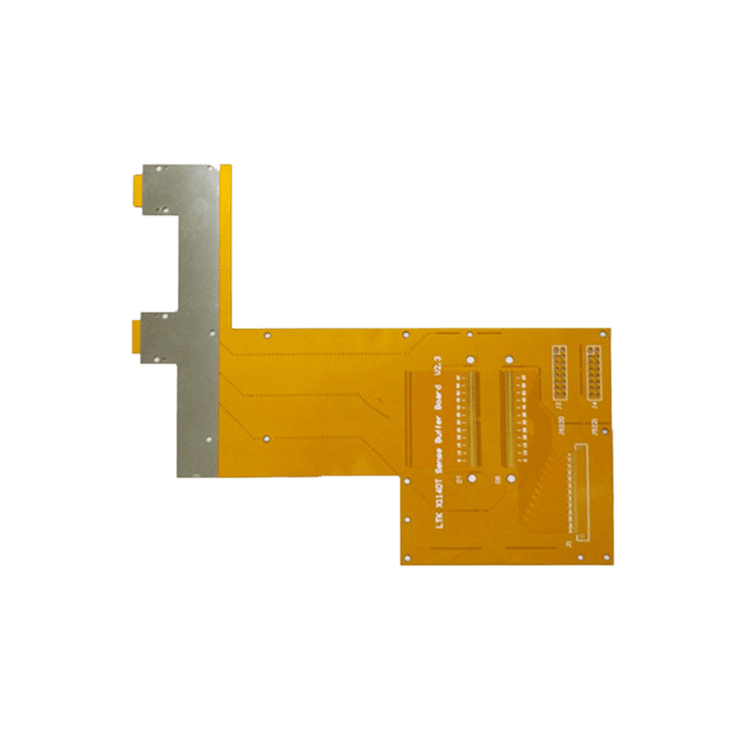
Design principles of Flex PCB stiffener
Designing Flex PCBs with appropriate stiffeners is crucial for ensuring their mechanical stability and durability. The stiffener’s design should consider the PCB’s mechanical properties, the application environment, and the manufacturing process. In this section, we will explore the design principles of Flex PCB stiffeners, including stiffener placement, size, shape, and the importance of considering thermal expansion and contraction. By following these design principles, designers can ensure their Flex PCBs’ optimal performance and reliability in various applications.
- Determine stiffness requirements
The first step in designing a Flex PCB stiffener is to determine the required level of stiffness. This depends on the application, and the degree of bending or flexing the PCB is expected to undergo. The designer should consider factors such as the size and weight of the components, the application environment, and any required certifications. This will help determine the necessary stiffness of the PCB and the type of material that should be used for the stiffener. - Select appropriate materials
Once the stiffness requirements are determined, the next step is to select the appropriate material for the stiffener. This depends on several factors, including the stiffness required, the manufacturing process, and the operating environment. The designer should consider materials such as FR4, PI, PET, copper, aluminum, and steel and choose the most suitable material for the specific application. - Define the location and shape of the stiffener.
The location and shape of the stiffener play a critical role in the mechanical stability of the Flex PCB. The stiffener should be placed in a way that supports the components and prevents any bending or flexing that could cause damage. The designer should consider the PCB’s size and shape, the components’ placement, and any required cutouts or openings in the stiffener for connectors or other components. - Consider the connection method with the PCB.
The connection method between the stiffener and the Flex PCB is crucial for ensuring mechanical stability. The designer should consider factors such as the type of adhesive used, the curing time, and the curing temperature. Additionally, the designer should ensure that the connection method does not cause any stress on the PCB, which could lead to failure or damage.
By following these design principles, designers can ensure that the Flex PCB stiffener is optimized for the specific application and that the Flex PCB has the required mechanical stability and durability.
Manufacturing methods of Flex PCB stiffener
Manufacturing Flex PCB stiffeners require specialized techniques and processes to ensure that the stiffeners are reliable and meet the required specifications. The manufacturing process depends on the material used for the stiffener and the complexity of the design. In this section, we will explore the various manufacturing methods used for Flex PCB stiffeners, including molding, stamping, and chemical etching. By understanding the manufacturing methods, designers can choose the most suitable method for their specific application and ensure the optimal performance and reliability of their Flex PCBs.
- Cutting
Cutting is a common manufacturing method used for creating Flex PCB stiffeners. This process involves cutting the material to the desired size and shape using a cutting tool or laser. This method is suitable for materials such as FR4, PI, and PET, and can produce stiffeners of various shapes and sizes. - Forming
Forming is a manufacturing method used for creating Flex PCB stiffeners from metal materials such as copper, aluminum, and steel. This process involves using a machine press or other forming tools to bend or shape the material into the desired shape. This method is ideal for creating complex shapes and can produce stiffeners with precise dimensions. - Injection molding
Injection molding is a manufacturing method used for creating plastic Flex PCB stiffeners. This process involves injecting molten plastic into a mold cavity and then cooling and solidifying the plastic to create the desired shape. Injection molding is suitable for creating stiffeners with complex shapes and can produce high volumes of stiffeners quickly and efficiently.
By using these manufacturing methods, designers can create Flex PCB stiffeners that meet the required specifications and ensure the optimal performance and reliability of their Flex PCBs. The choice of manufacturing method depends on factors such as the material used, the complexity of the design, and the required volume of production.
Applications of Flex PCB stiffener
Flex PCB stiffeners are widely used in various applications where mechanical stability and durability are crucial. The stiffeners support the components and prevent any bending or flexing that could cause damage or failure. This section will explore the various applications of Flex PCB stiffeners, including aerospace, medical, automotive, and consumer electronics. By understanding the applications, designers can choose the appropriate stiffener for their specific application and ensure their Flex PCBs’ optimal performance and reliability.
- Applications in embedded systems
Flex PCB stiffeners are commonly used in embedded systems, which are computer systems designed to perform specific tasks within a larger system. Embedded systems are often used in industrial control, medical equipment, and automotive systems. Flex PCB stiffeners support the embedded system’s components, ensuring they remain in place and do not bend or flex during operation. - Applications in consumer electronics
Flex PCB stiffeners are also widely used in consumer electronics like smartphones, tablets, and wearables. These devices often have compact designs and are subject to frequent handling and use, which can cause bending or flexing of the PCB. Flex PCB stiffeners provide mechanical support to the PCB, preventing any damage or failure due to bending or flexing. - Applications in automotive electronics
Automotive electronics require high mechanical stability and durability as they are subjected to harsh operating environments and conditions. Flex PCB stiffeners, such as engine control units, airbag systems, and navigation systems, are commonly used in automotive electronics. The stiffeners support the components and prevent any bending or flexing that could cause damage or failure.
By using Flex PCB stiffeners in these applications, designers can ensure their systems’ optimal performance and reliability, even under harsh conditions. The choice of stiffener depends on the specific application and the required mechanical stability and durability level.
The advantages and disadvantages of Flex PCB stiffener
Flex PCB stiffeners offer various benefits, including mechanical stability, durability, and improved electrical performance. However, they also have some drawbacks that designers must consider when choosing the appropriate stiffener for their application. This section will explore the advantages and disadvantages of Flex PCB stiffeners. By understanding these factors, designers can make informed decisions about using stiffeners in their applications.
Advantages
Flex PCB stiffeners offer several advantages, including:
- Mechanical stability: Flex PCB stiffeners provide mechanical support to the PCB, preventing any bending or flexing that could cause damage or failure.
- Durability: Flex PCB stiffeners improve the durability of the PCB, reducing the risk of damage due to handling or environmental factors.
- Improved electrical performance: Flex PCB stiffeners can improve the electrical performance of the PCB by reducing signal distortion and noise.
- Customization: Flex PCB stiffeners can be customized to meet the specific requirements of the application, including size, shape, and material.
- Cost-effective: Flex PCB stiffeners are cost-effective compared to other methods of providing mechanical support, such as rigid PCBs or metal brackets.
Disadvantages
Flex PCB stiffeners also have some disadvantages, including:
- Increased weight and size: Flex PCB stiffeners add weight and size to the PCB, which may not be desirable in some applications.
- Limited flexibility: Flex PCB stiffeners can limit the flexibility of the PCB, making it difficult to bend or fold.
- Material compatibility: The choice of stiffener material may be limited by the materials used in the PCB and the specific application requirements.
- Manufacturing complexity: The manufacturing process for Flex PCB stiffeners can be complex, requiring specialized techniques and equipment.
By considering these advantages and disadvantages, designers can choose the appropriate Flex PCB stiffener for their application, ensuring their system’s optimal performance and reliability.
Conclusion
In summary, Flex PCB stiffeners are widely used in various applications where mechanical stability and durability are crucial. They provide mechanical support to the PCB, preventing any bending or flexing that could cause damage or failure. The advantages of Flex PCB stiffeners include improved mechanical stability, durability, electrical performance, customization, and cost-effectiveness. However, some disadvantages include increased weight and size, limited flexibility, material compatibility, and manufacturing complexity.
The development of Flex PCB stiffeners will likely continue to focus on improving their mechanical stability and durability while minimizing their weight and size. The use of new materials, such as graphene and carbon nanotubes, may also be explored to enhance the stiffness and electrical performance of Flex PCB stiffeners. Additionally, advancements in manufacturing techniques and equipment may make it easier and more cost-effective to produce customized and complex-shaped Flex PCB stiffeners. Overall, the future of Flex PCB stiffeners looks promising as they continue to play a critical role in ensuring electronic systems’ optimal performance and reliability.
Welcome to JHYPCB!
As a world-renowned manufacturer of flex PCBs, we offer prototype and mass-production services for single-sided, double-sided, and multilayer flexible PCBs and flex PCBs with stiffeners. Our excellent manufacturing technology and high-quality materials ensure that our products are of top quality, and we also offer fast prototyping and production services.
If you need high-quality, reliable flex PCBs, don’t hesitate to contact our sales team at sales@pcbjhy.com. We will provide personalized manufacturing solutions to provide the perfect solution for your project.
Whatever type of flex PCB you need, JHYPCB can provide you with the best solution. We look forward to working with you!