An important element in the Printed Circuit Board assembly process is the Bill of Materials (BOM). BOM is a list that records the components needed to assemble the PCB, including information like part number, quantity, location, and description. In the PCB assembly process, BOM plays a crucial role. It helps the assembler to determine the necessary components to purchase while managing the entire production process and inventory level. It also ensures the quality and efficiency of PCB assembly.
An accurate and comprehensive BOM can help to reduce errors and costs while improving the efficiency and quality of PCB assembly. This is because the BOM provides a complete list of components, ensures the accuracy of component inventory, and prevents missing or mistaken components. In addition, during component procurement and installation, all information is recorded in the BOM, reducing errors and repetitive work.
In addition to its role in PCB assembly, BOM is also an important tool in supply chain management and procurement processes. It can help suppliers understand the required quantity and type of components, ensuring the quality and timeliness of components. Suppliers can better optimize their supply chain management and procurement processes by analyzing the BOM of components. Therefore, correct BOM creation and management are essential for any company or organization engaged in PCB manufacturing and assembly.
As a professional PCB manufacturing and assembly service provider, JHYPCB is fully aware of the importance and application of BOM in PCB assembly. We provide high-quality PCB manufacturing and assembly services and support our customers’ BOM creation and management needs. Our professional team can help customers create accurate and complete BOMs, ensuring timely updates and maintenance. We uphold the concept of “customer first, quality first” and provide customers with comprehensive services and support.
What is a BOM?
BOM stands for “Bill of Materials,” a comprehensive list of all the components, materials, and parts required to build a product. In the context of PCB assembly, BOM plays a critical role in helping to identify the components that need to be procured, manage the entire production process and inventory, and ensure the quality and efficiency of the PCB assembly.
What Components and Details Should be Included in the BOM?
JHYPCB requires a complete Bill of Materials before starting any assembly order, like any other PCB assembly facility. The BOM plays a crucial role in the assembly process, acting as an electronic shopping list that outlines all the necessary details about the parts required to assemble a given order, including item names, prices, quantities, availability, and assembly instructions.
We recommend including ten essential parts in every BOM to ensure a timely quote delivery.
The first essential component of a BOM is the item number which should be assigned uniquely to each part number. The number of lines in the BOM directly impacts the assembly cost. To reduce assembly costs, it is recommended to group parts with the same part number together on a single line. Moreover, it affects the total BOM cost because of price breaks that are available when buying in bulk from online suppliers. For instance, if line 4 requires 100 pieces of a certain part number, and line 7 has the same part number requiring 10 pieces, leaving them separate would affect the BOM cost. When separated, the total BOM price takes into account the price break for 100 pieces and adds it to the price break of 10 pieces. Depending on the price breaks for that part, it could result in paying more than double the price-per-unit for those extra 10 pieces. Conversely, if all 110 pieces were listed together under line 4, paying for all 110 pieces at the lower price-per-unit break point would have been possible.
The portion of the BOM that specifies the reference designators is crucial for the assembly process. Each item that will be present on the board must have a corresponding reference designator. Even if a particular part number is used for multiple components on the board, each instance must have a unique reference designator to avoid confusion during assembly. For instance, if part number XYZ is used thrice on the board, it must be labelled as XYZ1, XYZ2, and XYZ3 respectively.
It is important to ensure that the reference designators listed on the BOM match those given on the Gerber files to avoid errors during assembly.
This describes the function and purpose of each component, which helps to avoid confusion and ensure that the correct parts are used. This field is crucial to include in the BOM as it provides us with a fast overview of the component’s properties. Additionally, it enables JHYPCB to compare your description with the datasheet, which helps to eliminate any discrepancies that might have occurred during BOM generation.
The purpose of this column is to provide the total quantity of components required for a single board based on a specific BOM line. It is essential to ensure that this quantity matches the number of reference designators listed for that particular line; for instance, if a line contains a part number with three reference designators (C1, C2, and C3), then the total quantity for that line should also be 3.
This column on the BOM indicates the manufacturer of the specific part number listed on the line. It is important because different manufacturers may have similar or partially matching part numbers, and having this information allows us to easily and confidently select the correct manufacturer. It ensures accuracy in selecting the appropriate components for assembly and helps to avoid any potential errors or issues during production.
The “part number” column in the BOM is crucial because it specifies the exact part number of the component that needs to be placed on the board. It’s important to include a part number for even passive resistor or capacitor parts. Providing complete and accurate part numbers helps to eliminate any uncertainties or errors that could arise during production. To ensure accuracy, JHYPCB requires complete and valid part numbers. If a part number is incomplete, we’ll confirm the exact number with you before proceeding with production. Failure to provide a valid part number may result in delays in finalizing your quote.
While not an absolute necessity, including the “package type” column in your order can greatly assist our account managers in providing an accurate quote for you. This is especially true for components like BGA and QFN, which may incur additional charges. Having this detail readily available ensures we properly account for every part needed in your order. Moreover, a complete and accurate BOM expedites the quoting process, and verifies the part number when cross-checked with the package information.
Although not mandatory, including the “pads and through-holes” column in your BOM can make it easier for us to calculate the total number of each on your board. This information impacts the cost of PCB assembly, so having this detail allows us to provide a more accurate quote. Additionally, identifying part types quickly helps to streamline the quoting process and ensures a more efficient turnaround time.
This column is intended for recording any specific instructions or notes that pertain to a particular BOM line item. Common uses for this column may include marking certain parts with labels such as “Do Not Install” or “Consigned.” Additionally, instructions related to purchasing parts but not installing them – requiring them to be shipped back with the completed boards – could also be included in this column.
The column in question plays a crucial role in expediting the process of providing an accurate quote in a timely manner. Because part stock is constantly in flux – changing by the hour, every day – there is always a chance that a listed part will be out of stock by the time we complete your quote, even if it was available at the time of your initial BOM creation. To assist in this scenario, we strongly recommend providing alternate part numbers to substitute in the event of a stock issue. This enables us to finalize pricing for your BOM without the need for extensive back-and-forth communications to decide on alternative suggestions. It’s worth noting that JHYPCB will always include suggested part substitutions for the passive resistor and capacitor parts by default in the event of any stock issues.
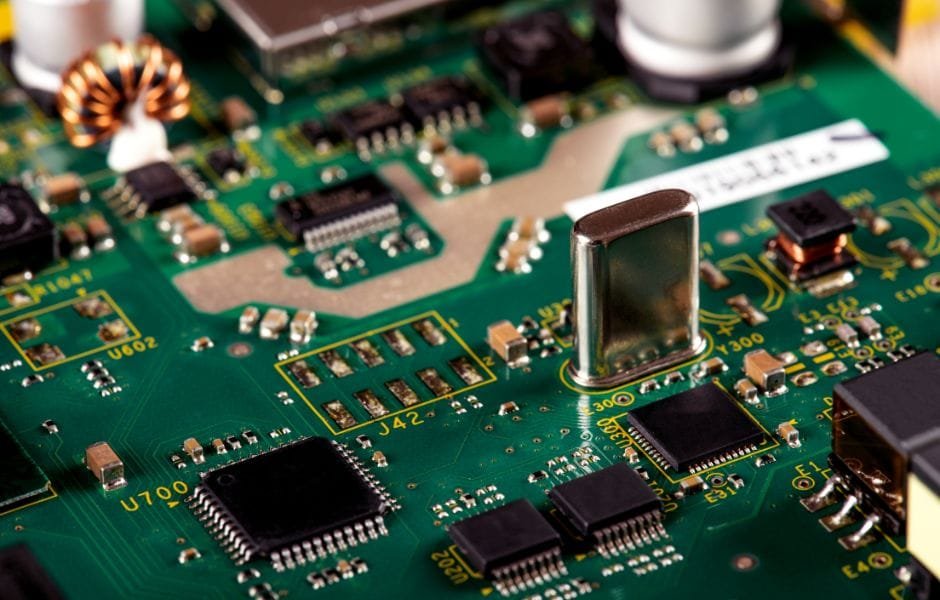
The Applications of BOM in PCB Assembly
The BOM is an accurate and detailed list of components required for successful assembly in electronic product design. It provides essential information about each component, including their unique identification numbers, reference designators, descriptions, quantities, manufacturers, manufacturer part numbers, packages, types, and special instructions.
The BOM is key for tracking the inventory of components during procurement, stock management, and material scheduling. It helps to ensure that the right components are ordered and available when needed. This is particularly important for just-in-time manufacturing, where components must be available at the right time to prevent production delays or line stops.
In addition to inventory tracking, the BOM is also important for managing PCB production and assembly processes. It gives PCB assemblers the exact information they need to understand the PCB design and correctly place components on the board. This ensures that the PCB assembly is done correctly and accurately the first time, which can save time and money in the long run.
Overall, the BOM is an essential tool for ensuring successful PCB assembly. It plays a critical role in managing the many details of electronic product design, procurement, inventory management, and production scheduling. Quality PCB manufacturers and assemblers, like JHYPCB, understand this importance and provide excellent BOM management services to their customers.
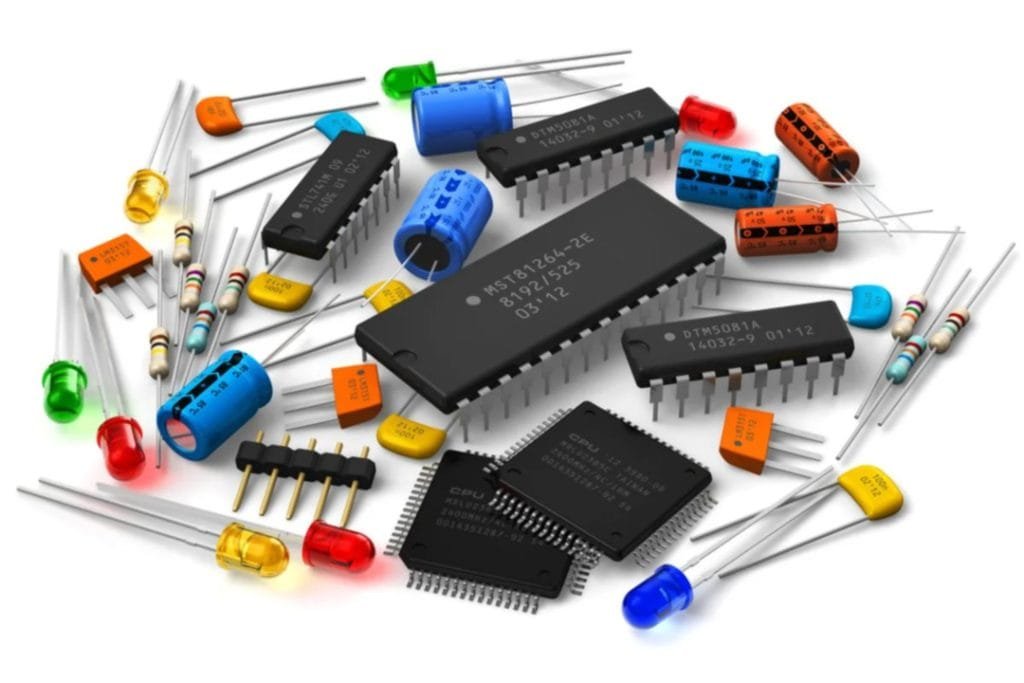
How to Create a BOM?
When it comes to a successful PCB assembly project, creating a comprehensive Bill of Materials is crucial. The BOM serves as a detailed list of all the components and materials required to build a product, including part numbers, reference designators, descriptions, quantities, manufacturers, manufacturer part numbers, packages, types, and any special instructions. It is a critical part of the assembly process because it precisely defines each component’s features and location, ensuring that the correct components are used in the right places. This section will discuss how to create one that meets your PCB assembly needs.
A - Collect all of the necessary information about the PCB design.
1. Collect all of the necessary information about the PCB design
– Details about the components that will be used
– Layout of the board
– Any special requirements or specifications
– Any other relevant information
2. Determine the necessary BOM information
– Decide which specific pieces of information should be included in the BOM
– Component name
– Part number
– Manufacturer
– Quantity
– Any necessary notes or special instructions
3. Create the BOM
– Use specialized software designed for BOM creation
– Or, create it manually using a standard spreadsheet program
4. Check all of the information for accuracy and up-to-date details before finalizing the BOM
– Double-check part numbers, quantities, and other relevant details
– Ensure there are no errors or omissions that could impact the final PCB assembly
B - Design the structure and format of the BOM
The structure and format of designing a BOM must consider the following aspects:
1. Choose an appropriate BOM structure based on project requirements: BOM can be organized based on the hierarchical structure of the circuit board, component grouping, or functional grouping. Hierarchical BOM arranges components based on their location on the circuit board, component-based BOM arranges components based on their respective components, and functional BOM arranges components based on their functions. Choosing a suitable structure based on project requirements can make the BOM table clearer and easier to understand.
2. Design the format and fields of the BOM table: Each BOM table should include the following basic fields: material number, material description, quantity, manufacturer, manufacturer part number, package, reference designator, notes, etc. Additionally, some custom fields can be added based on specific project requirements.
For the format design of BOM tables, electronic spreadsheet software (such as Excel, Google Sheets, etc.) can be used to create BOM tables, or online BOM tools (such as Octopart, Digikey, etc.) can be used to create and manage BOM tables. To better organize and manage BOM tables, it is recommended to save them in cloud storage services and control and back up their versions. Additionally, to ensure the accuracy and completeness of the BOM, it should be regularly checked and verified.
C - Updating and Maintaining BOM
Updating and maintaining the Bill of Materials is crucial in ensuring accuracy and completeness in the production process of PCB assembly. It is recommended to regularly review and update the BOM to reflect any changes in the design or components used. Real-time adjustments and monitoring should also be done during production to ensure the BOM is up-to-date.
It is important to apply management and tracking techniques such as version control to manage and track changes made to the BOM effectively. This ensures that any modifications to the BOM are properly documented, tracked, and approved before implementation, reducing the likelihood of errors and issues during the production phase. Overall, maintaining an accurate and updated BOM is essential for ensuring the efficiency and quality of PCB assembly.
D - Store and Manage BOM Files
To store and manage BOM files, there are a few key steps to follow:
Establish a BOM database or use existing software tools. This can help ensure that BOM data is entered consistently and accurately, making it easier to search and track changes over time. Many software options are available for BOM management, ranging from simple spreadsheets to more complex enterprise resource planning (ERP) systems.
Ensure the security and confidentiality of your BOM. This may involve limiting access to sensitive information, using password protection or other security measures to prevent unauthorized access, and carefully controlling who has permission to view or edit the BOM data.
By following these steps, you can help ensure that your BOM data is accurate, secure, and up to date, which can help you streamline your PCB assembly process and reduce the risk of errors or delays. Working with a trusted PCB manufacturer like JHYPCB can also help ensure high-quality PCB production and assembly services.
E - Notes for creating BOM
Creating a Bill of Materials is a crucial step in the PCB assembly process. Here are some important considerations to keep in mind when creating a BOM:
Accuracy: Ensuring that every component listed in the BOM is accurate and up-to-date is essential. Any errors or omissions in the BOM can result in costly delays or errors during the assembly process.
Detail: The BOM should be as detailed as possible to avoid misunderstandings or confusion in the assembly process. Each component should be clearly labeled with its properties and specifications, such as part number, manufacturer, and quantity.
Practicality: The BOM should be easy to implement and maintain. Choosing a format that works best for the project team and is compatible with the assembly software and equipment is important.
Updates: It is crucial to keep the BOM up-to-date and make necessary changes as the project evolves. Regular review and updates can help avoid further errors and ensure the assembly process runs smoothly.
BOM example and Template
A Bill of Materials, or BOM, is a comprehensive list of the components required to build a product. Below is a simple BOM example for a PCB design project:
Example Bill of Materials-JHYPCB
A well-organized BOM can help optimize PCB assembly and production processes. Having an accurate BOM ensures that the correct components are ordered and that production is not delayed due to component shortages or inaccurate orders. The BOM can also optimize the assembly process by grouping similar components and ordering them logically. This can help reduce assembly time and minimize errors during the assembly process.
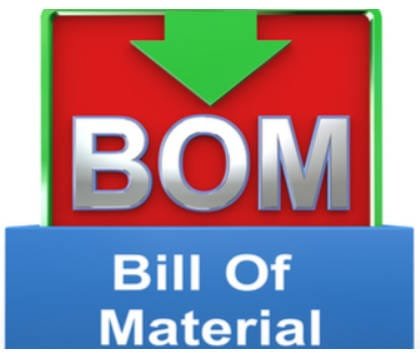
Bill of Materials Example / Template
How Does JHYPCB Review BOM and Gerber Files?
JHYPCB has a team of capable engineers who are always ready to meet your technical requirements and produce high-quality products. We require your bill of materials and Gerber files to start the review process. Our experienced team reviews your BOM and circuit board Gerber files before production to ensure the smooth flow of the process.
Reviewing the BOM, we look for discrepancies, such as duplicate part numbers, mismatches between the part number and description, or incomplete part numbers. Based on the BOM, we find authorized component dealers and their prices. We communicate any BOM issues to you through the comment column in the BOM. This helps us ensure that all components are ready before manufacturing begins.
We also check Gerber files to identify any design issues that may have occurred. We do this to locate any missing solder pads, problems with the footprint or silk screen, drill problems, drills outside the board or flipped, etc. This ensures that the final product is high quality and meets your specifications.
You must provide us with all the necessary files in a specific format to expedite processing. For the bill of material, we require it to be in Microsoft Excel format, with all the mandatory fields completed. It should have data on item number, quantity, reference designator(s), manufacturer’s component number, manufacturer’s name, component description, and package type (if not listed in the description).
Gerber files should be submitted in a specific format, RS-274X or RS-274D formats. We require Gerber files for each layer of the PCB and a drill file for holes. These files should be grouped in a zip folder. ODB++ format is also acceptable. Our skilled staff carefully reviews your Gerber files for manufacturability (DFM check) as per approved IPC guidelines. Early DFM verification enables us to find errors at the beginning of the production process and correct them early on, leading to on-time delivery and superior quality.
In conclusion, JHYPCB focuses on providing high-quality products that meet your technical specifications. We review your BOM and Gerber files to ensure the manufacturing process runs smoothly, with any issues communicated to you promptly. Cooperation between you and JHYPCB ensures successful project delivery.
If you are looking for a reliable and efficient component sourcing service, please consider our component procurement service. We can help you find high-quality components at competitive prices, saving you time and effort in the procurement process. Contact us for more information.
Related Reading:
- Guidelines For Optimal PCB Design For Assembly (DFA)
- Designing For Testability For PCB Manufacturing And Assembly
- Unlocking The World Of PCBs: Your Ultimate PCB Terms And Glossary Guide
- What is a printed circuit board (PCB)?
- Trustworthy Suppliers: Your Key to Successful Component Sourcing
- PCB Component Sourcing: Exploring Global Markets for Better Options and Prices
- Supply Chain Management: How to Optimize Cost and Delivery Time for PCB Components