Aluminum substrate PCBs are gaining popularity in various industries due to their excellent thermal conductivity, high strength, and low cost. This blog post introduces the different types of aluminum substrate PCBs, their unique features, and applications in LED lighting, automotive, power electronics, and communications industries. We'll also explore their advantages over traditional PCBs.
What is Aluminum Substrate PCB?
Aluminum substrate PCBs, also known as aluminum PCBs or metal core PCBs, are becoming increasingly popular in various industries due to their unique characteristics and advantages over traditional PCBs. These PCBs are designed with a metal core, typically made of aluminum, which provides excellent thermal conductivity and high strength. This allows them to handle high power loads and operate at higher temperatures than traditional PCBs. This blog post will introduce you to the different types of aluminum substrate PCBs, their characteristics, applications, and advantages.
Types of Aluminum Substrate PCBs
Aluminum substrate PCBs are available in various types, including single-sided, double-sided, multilayer, and hybrid. Single-sided aluminum PCBs have a metal core on one side and a layer of copper on the other, while double-sided aluminum PCBs have metal cores on both sides with copper layers in between. Multilayer aluminum PCBs consist of multiple layers of metalcore and copper, while hybrid aluminum PCBs combine aluminum substrate with FR4 substrate to achieve better thermal management. Each type of aluminum substrate PCB has unique features and advantages, making them suitable for various applications in various industries.
Single-Sided Aluminum PCBs
Single-sided aluminum PCBs have a metal core on one side and a layer of copper on the other. The metal core is usually made of aluminum but can also be made of other metals like copper or brass. The copper layer is etched to create the circuit pattern, and the metal core provides a sturdy base for the components to be mounted.
One of the key advantages of single-sided aluminum PCBs is their excellent thermal conductivity. The metal core acts as a heat sink, dissipating heat away from the components and reducing the risk of thermal damage. This makes them ideal for high-power applications like LED lighting, power supplies, and motor control.
Single-sided aluminum PCBs are also known for their high mechanical strength, making them more durable than traditional FR4 PCBs. They can withstand harsh environmental conditions, such as high temperatures and humidity, making them ideal for industrial and automotive applications.
Another advantage of single-sided aluminum PCBs is their low cost compared to other metal core PCBs. This makes them an attractive option for cost-sensitive applications.
In summary, single-sided aluminum PCBs offer excellent thermal conductivity, high mechanical strength, and low cost, making them an ideal choice for high-power and harsh environment applications.
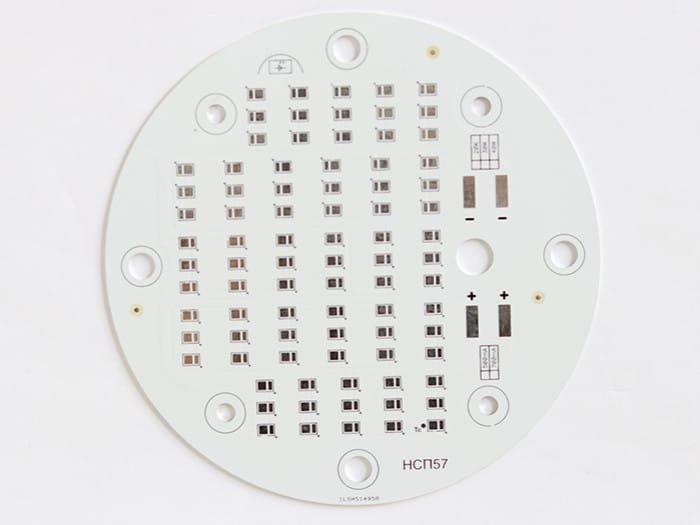
Double-Sided Aluminum PCBs
Double-sided aluminum PCBs have metal cores on both sides, with a layer of copper in between. The metal cores are usually made of aluminum but can also be made of other metals like copper or brass. The copper layers are etched to create the circuit pattern, and the metal cores provide a sturdy base for the components to be mounted.
One of the key advantages of double-sided aluminum PCBs is their excellent thermal management capabilities. The metal cores act as heat sinks, dissipating heat away from the components and reducing the risk of thermal damage. This makes them ideal for high-power applications like LED lighting, power supplies, and motor control.
Double-sided aluminum PCBs also offer higher component density than single-sided PCBs, as they have copper layers on both sides of the metal core. This allows for more circuitry to be packed into a smaller area, making them ideal for limited-space applications.
Double-sided aluminum PCBs also offer higher mechanical strength than traditional FR4 PCBs, making them more durable and reliable. They can withstand harsh environmental conditions, such as high temperatures and humidity, making them ideal for industrial and automotive applications.
In summary, double-sided aluminum PCBs offer excellent thermal management, higher component density, and superior mechanical strength, making them an ideal choice for high-power and harsh environment applications where reliability is crucial.
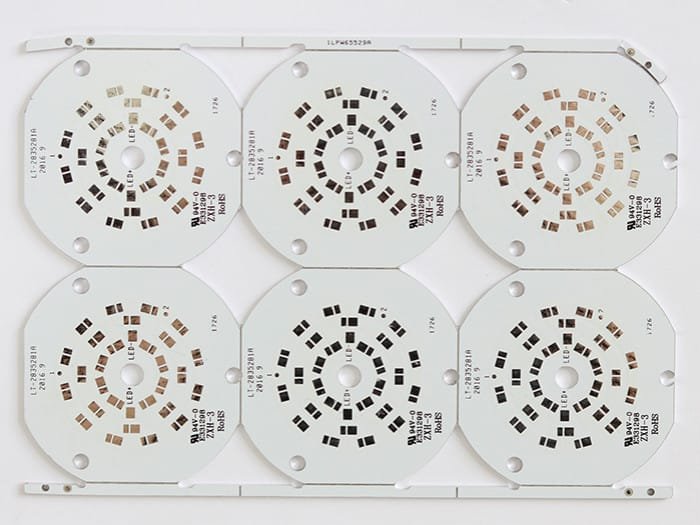
Multilayer Aluminum PCBs
Multilayer aluminum PCBs consist of multiple layers of metal core and copper, with insulating material in between. The metal cores are usually made of aluminum but can also be made of other metals like copper or brass. The copper layers are etched to create the circuit pattern, and the insulating material separates the layers and provides electrical isolation.
One of the key advantages of multilayer aluminum PCBs is their ability to handle complex circuit designs with high component density. The multiple layers allow for more circuitry to be packed into a smaller area, making them ideal for applications where space is limited.
In addition to their high component density, multilayer aluminum PCBs also offer excellent thermal management capabilities. The metal cores act as heat sinks, dissipating heat away from the components and reducing the risk of thermal damage. This makes them ideal for high-power applications like LED lighting, power supplies, and motor control.
Multilayer aluminum PCBs also offer superior mechanical strength to traditional FR4 PCBs, making them more durable and reliable. They can withstand harsh environmental conditions, such as high temperatures and humidity, making them ideal for industrial and automotive applications.
In summary, multilayer aluminum PCBs offer high component density, excellent thermal management capabilities, and superior mechanical strength, making them an ideal choice for complex circuit designs and high-power and harsh environment applications where reliability is crucial.
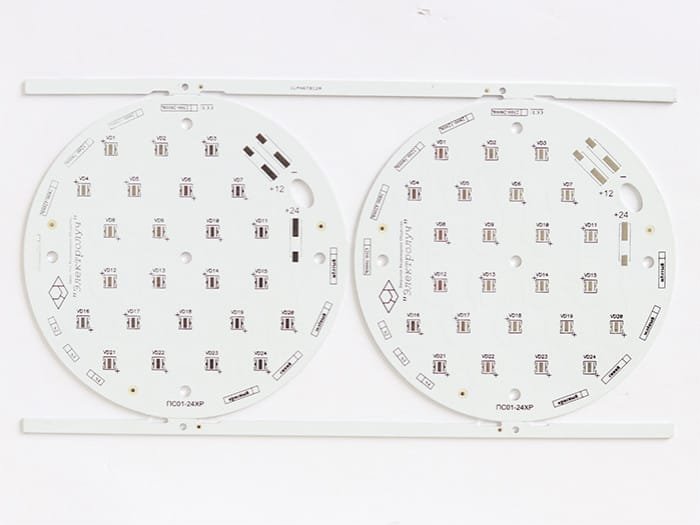
Hybrid Aluminum PCBs
Hybrid aluminum PCBs combine aluminum substrate with FR4 substrate to achieve better thermal management and electrical performance. The metal core is usually made of aluminum, while the FR4 substrate is used as an insulating material for electrical connections.
One of the key advantages of hybrid aluminum PCBs is their ability to handle high-frequency and high-speed applications with better electrical performance. The FR4 substrate offers better electrical properties than aluminum, allowing for more precise control of signal integrity and reducing the risk of electromagnetic interference.
In addition to their improved electrical performance, hybrid aluminum PCBs offer excellent thermal management capabilities. The metal core acts as a heat sink, dissipating heat away from the components, while the FR4 substrate provides insulation and electrical connections. This makes them ideal for high-power applications like LED lighting, power supplies, and motor control.
Hybrid aluminum PCBs also offer superior mechanical strength to traditional FR4 PCBs, making them more durable and reliable. They can withstand harsh environmental conditions, such as high temperatures and humidity, making them ideal for industrial and automotive applications.
In summary, hybrid aluminum PCBs offer improved electrical performance, excellent thermal management capabilities, and superior mechanical strength, making them ideal for high-frequency and high-speed applications where reliability and signal integrity are crucial.
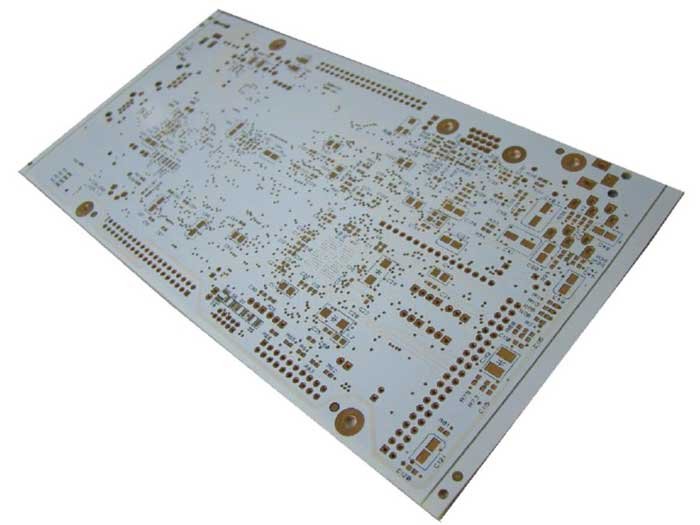
Flexible aluminum PCBs, also known as flex aluminum PCBs or flex-rigid aluminum PCBs, are a type of PCB that combines the flexibility of a flexible PCB with the thermal management and mechanical strength of an aluminum substrate. These PCBs consist of a flexible polyimide substrate coated with aluminum, providing excellent heat dissipation and superior mechanical strength.
Flexible aluminum PCBs are ideal for applications where flexibility and thermal management are important, such as in LED lighting, automotive electronics, and portable electronics. They offer several advantages over traditional flexible PCBs, including better thermal conductivity, higher mechanical strength, and greater design flexibility. The use of flexible aluminum PCBs can help improve the performance and reliability of electronic devices, particularly those that generate high heat levels.
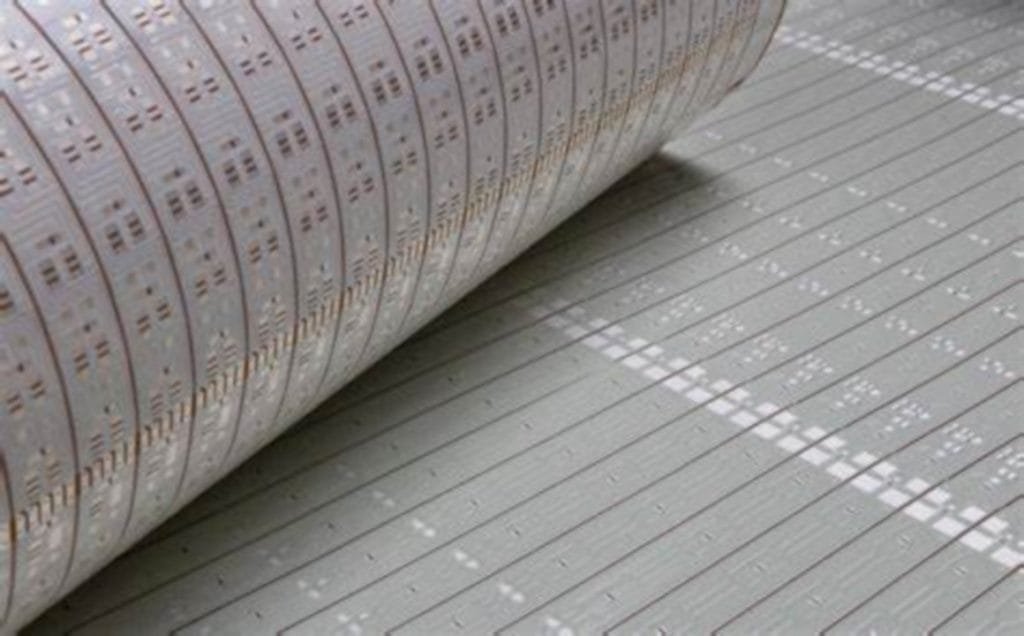
Characteristics of Aluminum Substrate PCBs
Thermal Management: One of the key characteristics of aluminum substrate PCBs is their excellent thermal management capabilities. The metal core acts as a heat sink, dissipating heat away from the components and reducing the risk of thermal damage. This makes them ideal for high-power applications where heat management is crucial.
High Durability: Aluminum substrate PCBs offer superior mechanical strength and withstand harsh environmental conditions, making them more durable and reliable than traditional FR4 PCBs. They can also withstand vibrations and mechanical shocks, making them ideal for automotive and industrial applications.
Better Electrical Performance: Aluminum substrate PCBs offer better electrical performance than FR4 PCBs, particularly in thermal conductivity and signal integrity. They also offer better electrical insulation, which helps reduce the risk of short circuits.
Lightweight: Aluminum substrate PCBs are lightweight, which makes them ideal for applications where weight is a concern, such as aerospace and portable electronics.
Design Flexibility: Aluminum substrate PCBs offer greater design flexibility compared to FR4 PCBs, particularly in terms of layout, size, and thickness. They can also be designed with various surface finishes to meet specific requirements.
In summary, aluminum substrate PCBs offer excellent thermal management, high durability, better electrical performance, lightweight, and design flexibility, making them ideal for high-power and harsh environments where reliability, signal integrity, and design flexibility are crucial.
Applications of Aluminum Substrate PCBs
LED Lighting: Aluminum substrate PCBs are commonly used in LED lighting applications due to their excellent thermal management capabilities. They help dissipate heat away from the LEDs, reducing the risk of thermal damage and improving overall performance.
Power Electronics: Aluminum substrate PCBs are also widely used in power electronics applications, such as power supplies, motor drives, and inverters. Their high thermal conductivity and superior mechanical strength make them ideal for high-power applications.
Automotive Electronics: Aluminum substrate PCBs are commonly used in automotive electronics applications due to their high durability and ability to withstand harsh environmental conditions, such as high temperatures, humidity, and vibrations.
Aerospace: Aluminum substrate PCBs are also used in aerospace applications due to their lightweight and high durability. They can withstand the extreme conditions of space and are used in applications such as satellites and space shuttles.
Medical Electronics: Aluminum substrate PCBs are used in medical electronics applications due to their high reliability and ability to withstand harsh sterilization processes.
In summary, aluminum substrate PCBs are widely used in LED lighting, power electronics, automotive electronics, aerospace, and medical electronics applications due to their excellent thermal management, high durability, and reliability.
Conclusion
In conclusion, aluminum substrate PCBs are an excellent choice for applications where thermal management, high durability, and superior electrical performance are critical. They offer a range of advantages over traditional FR4 PCBs, including better heat dissipation, higher mechanical strength, and greater design flexibility. Aluminum substrate PCBs are widely used in various applications, including LED lighting, power electronics, automotive electronics, aerospace, and medical electronics. With their ability to improve reliability and performance, aluminum substrate PCBs are a valuable addition to the electronics industry, and their use is likely to continue to grow.