Flexible PCB Materials
EMI Shielding Film in FPC Applications
EMI, which can also be coined as RFI in the radio frequency range, is an interference that is caused by an external source and affects the electrical circuit on printed circuit boards. It is induced through electromagnetic induction, electrostatic coupling, or conduction. This interference can lead to a decline in the performance of your PCB assembly and can even render it non-functional.
Table of Contents
Add a header to begin generating the table of contents
What is EMI Shielding Film in FPC?
EMI Shielding Film in FPC refers to the use of a film or coating material on a flexible printed circuit (FPC) to provide electromagnetic interference (EMI) shielding. EMI shielding is vital in electronic devices as it prevents the interference of electromagnetic signals and various electronic components that can disrupt their proper functioning. The films used for EMI shielding are typically made of metal or metal-coated materials, which act as a barrier to EMI signals and prevent them from penetrating or escaping the device. The FPC serves as the substrate onto which the EMI shielding film is applied, and this combination can be used in various applications, including smartphones, tablets, and other electronic devices.
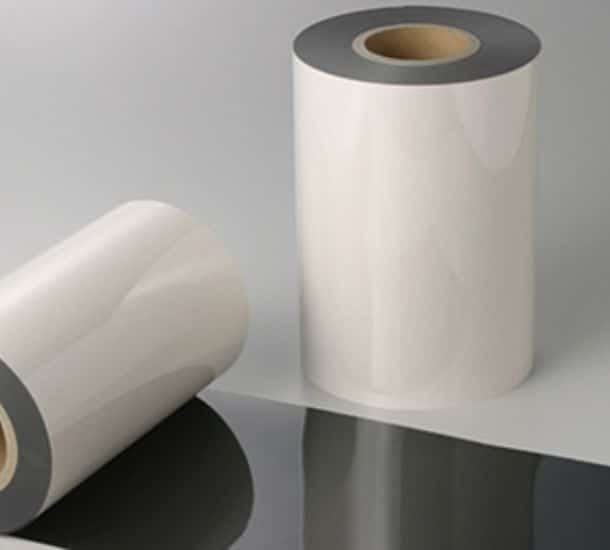

Importance of EMI Shielding Film in FPC
Why EMI Shielding Film in FPC?
EMI interference can significantly impact electronic equipment, leading to signal issues, function instability, system failure, or data loss. Shielding electromagnetic radiation during PCB or FPC design is crucial for maintaining reliability. That’s where EMI Shielding Film for FPC comes in, as a key component in preventing electromagnetic interference. With components tightly packed in compact devices like smartphones, tablets, and wearables, EMI Shielding Film creates a barrier that keeps EMI signals in check, improving device performance and reducing interference. Without it, electronic devices can suffer from reduced signal strength, decreased range, and malfunction.
Characteristics of EMI Shielding Film in FPC
EMI shielding film is a key component of flexible printed circuits that provides effective electromagnetic interference shielding. Some of the main characteristics of EMI shielding film in FPC include:
High shielding effectiveness: EMI shielding film in FPC is designed to provide high levels of shielding effectiveness against electromagnetic radiation. This helps to prevent interference with electronic devices and improves device performance.
Flexible and thin: EMI shielding film in FPC is flexible and thin, making it ideal for use in compact, lightweight electronic devices. It can also be easily integrated into FPCs without adding significant weight or bulk.
Durable and resistant: EMI shielding film in FPC is typically highly durable and resistant to wear and tear, as well as exposure to various environmental or chemical factors. It can also withstand exposure to high temperatures, making it suitable for use in high-performance electronic devices.
Easy to manufacture: EMI shielding film in FPC is relatively easy to manufacture using a variety of processes, including sputtering, vacuum deposition, and printing. This makes it a cost-effective material for use in mass production of electronic devices.
Applications of EMI Shielding Film in FPC
EMI Shielding Film in FPC has broad applications in many electronic products, including consumer electronics, aerospace and defense, and medical devices. As modern electronic equipment becomes smaller and more compact, the importance of EMI Shielding Film in FPC in maintaining signal integrity continues to grow. For example, smartphones, tablets, and laptops widely use EMI Shielding Film in FPC to eliminate electromagnetic interference and maintain high-performance integrity. In addition, medical devices often require EMI shielding to avoid interference with other devices or to prevent unintentional radiation.
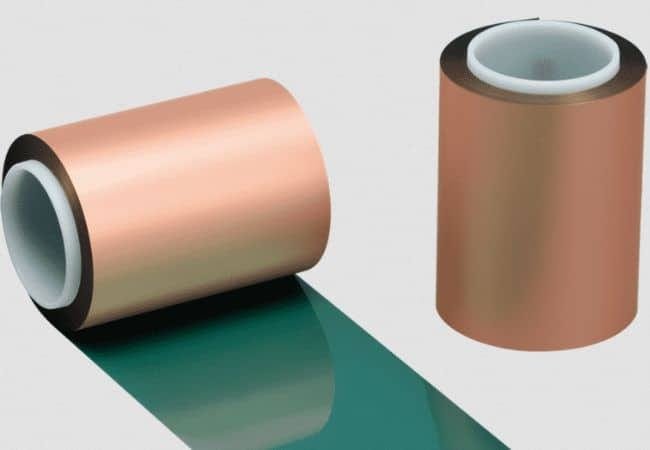
Manufacturing Process of EMI Shielding Film in FPC
The EMI Shielding Film in FPC is typically manufactured using a coating and laminating process. The base material is coated with a conductive metal layer, such as copper, nickel, or silver, and a polymer layer is used as the adhesive layer. The thickness of the conductive layer and adhesive layer can be adjusted to achieve the required shielding performance and adhesion strength for a specific design. After the lamination process, the final step is to perform the quality control and testing of the product, which includes measuring the shielding effectiveness, thickness, and flexibility of the film. These tests ensure that the product meets quality standards and conforms to specific design requirements. Throughout the entire process, it is necessary to maintain a clean and dust-free production environment to prevent contamination and potential production defects. The manufacturing process of EMI Shielding Film in FPC requires precise craftsmanship but it is highly efficient, cost-effective, and can produce high-quality and reliable products.
Applications of EMI Shielding Film in FPC
EMI Shielding Film in FPC, as a high-strength electromagnetic shielding film, can play an important role in various electronic device applications. Here are the main application areas:
Mobile and communication devices: EMI Shielding Film in FPC can be used to produce flexible circuit boards for cell phones, tablets and other communication devices. In these devices, EMI Shielding Film can ensure that the electromagnetic signals between different components do not interfere with each other, ensuring the proper operation of the devices.
Automotive electronics: EMI Shielding Film in FPC can be widely used in automotive electronics, including in-vehicle entertainment systems, navigation systems, and airbag electronic systems, etc. By covering the circuit board with EMI Shielding Film, external electromagnetic interference can be resisted, improving the performance and reliability of automotive electronics.
Industrial control systems: EMI Shielding Film in FPC helps improve the operating efficiency of industrial control equipment. In control systems, motors and sensors may be involved in complex electromagnetic interference issues, but using EMI Shielding Film in FPC effectively avoids these problems and ensures the normal operation of the equipment.
Medical equipment: EMI Shielding Film in FPC can be used to produce medical devices, such as scanning equipment, monitoring devices, and surgical instruments. In these devices, EMI Shielding Film plays a crucial role in protecting the electronic components inside the device and helps enhance the safety and reliability of the equipment.
Choosing the Best EMI Shielding Method for FPCs
EMI shielding is essential to absorb radio and other EMI waves, but with increasing complexity of electronics, choosing the best method is becoming critical. Traditional copper plating is rigid and prone to cracking, while conductive silver ink is expensive and has longer processing time. Metal housing, commonly used on rigid PCBs, is not suitable for miniaturization. In contrast, EMI Shielding Film is increasingly popular due to its shielding performance, flexibility, and cost-effectiveness. With the thinnest overall thickness, EMI Shielding Film is an excellent choice for both flexible PCB and rigid-flex board designs. It ensures high-frequency signal transmission, offering flexibility, and cost-effectiveness without compromising on board quality.
FAQs on EMI Shielding Film in FPC
What is FPC?
FPC stands for Flexible Printed Circuit. It is a type of circuit board that is designed to be flexible, allowing it to conform to the shape of the device or system it is used in. FPCs are commonly used in electronic devices where space and weight are limited, such as in smartphones, tablets, and wearables. They can also be used in applications where the circuit board needs to be able to bend or flex, such as in a hinge mechanism.
What are the benefits of FPC?
There are several benefits of using FPCs:
Space-saving: FPCs are thin and flexible, making them ideal for applications where space is limited.
Weight-saving: FPCs are lightweight, which is advantageous for portable devices.
High-density assembly: Since FPCs can be produced in very small sizes and with highly accurate registration, they are ideal for high-density assembly.
Flexibility: FPCs can be bent or shaped to fit the available space or to allow the circuit to move in a certain way.
High-reliability: FPCs have a low failure rate and are highly reliable due to their design and the materials used.
Cost-effective: FPCs can be produced in large volumes using efficient manufacturing processes, making them affordable.
What are the materials for Flex Circuits?
The materials used in Flex Circuits include various flexible substrates such as Polyimide, Polyester, and PTFE, as well as conductive materials such as copper and other metals. Adhesives and coverlay or solder mask materials and stiffener are also used to protect the circuit and provide insulation. The selection of materials depends on the specific requirements of the application, including factors such as operating temperatures, flexibility, durability, and chemical resistance.
What are the types of Flexible Circuits?
There are several types of Flexible Circuits:
Single-sided flexible circuits: These consist of a single conductor layer on a flexible substrate.
Double-sided flexible circuits: These have conductive layers on both sides of a flexible substrate.
Multilayer flexible circuits: These have more than two conductive layers separated by insulating layers.
Rigid-flex circuits: These combine flexible and rigid substrates to form a hybrid circuit.
Sculptured flexible circuits: These have a 3D configuration to fit specific product designs.
What is EMI shielding film in FPC?
EMI shielding film in FPC is a type of thin film that is applied onto a flexible printed circuit board (FPC) to prevent electromagnetic interference.
What are the benefits of using EMI shielding film in FPC?
The benefits of using EMI shielding film in FPC include improved signal transmission, reduced crosstalk, enhanced electromagnetic compatibility (EMC), and increased reliability of electronic devices.
How is EMI shielding film applied onto FPCs?
EMI shielding film is typically applied onto FPCs using a lamination process. The shielding film is first punched or cut into the desired shape and then heat-pressed onto the FPC construction.
What materials are typically used to construct EMI shielding film in FPCs?
The most common materials used to construct EMI shielding film in FPCs are aluminum and copper, as they are effective conductors of electricity and can block electromagnetic interference.
What is the typical thickness of EMI shielding film used in FPCs?
The typical thickness of EMI shielding film used in FPCs ranges from 0.025mm to 0.1mm.
How effective is EMI shielding film in FPCs at blocking electromagnetic interference?
EMI shielding film in FPCs is highly effective at blocking electromagnetic interference, as it provides a conductive layer that minimizes the penetration of electric and magnetic fields.
Can EMI shielding film be used in flexible and bendable FPC designs?
Yes, EMI shielding film can be used in flexible and bendable FPC designs, as it is designed to be flexible and conform to the shape of the FPC.
Can EMI shielding film be customized to fit specific FPC designs?
Yes, EMI shielding film can be customized to fit specific FPC designs, as it can be cut into different shapes and sizes.
What factors should be considered when selecting EMI shielding film for FPCs?
Factors that should be considered when selecting EMI shielding film for FPCs include the thickness, material, conductivity, flexibility, and durability of the film.
Is EMI shielding film more cost-effective than other forms of EMI shielding in FPCs?
Yes, EMI shielding film is generally more cost-effective than other forms of EMI shielding in FPCs, as it is relatively inexpensive to produce and easy to apply onto FPCs.
Explore Our PCB Fabrication Services
Related Reading
- PCB Layers Explained: Multilayer PCB Stakcup
- PCB Substrate: A Comprehensive Guide To PCB Base Materials
- A Comprehensive Guide To Copper Clad Laminate (CCL) Used In PCB Fabrication
- Flexible Copper Clad Laminate (FCCL)
- PCB Prepreg: Definition, Types, Applications, Thickness, And Related Questions Answered.
- The Ultimate Guide To Flex PCB Stiffener
- FPC Coverlay in Flex Circuits: All You Need to Know