Leading PCB Manufacturing & Assembly Manufacturer in China
Unlocking the World of PCBs: Your Ultimate PCB Terms and Glossary Guide
PCB Glossary of Terms
Welcome to our PCB glossary page! If you’re new to the world of printed circuit boards, this page is the perfect place to start learning. We’ve compiled a list of over 500 PCB-related terms for you to explore, organized alphabetically for your convenience. At JHYPCB, we specialize in the fabrication and assembly of high-quality printed circuit boards for a variety of industries and applications. Our state-of-the-art facilities and experienced team of engineers and technicians ensure that your PCBs are produced to the highest standards of quality, reliability, and precision. Whether you’re a seasoned engineer or just starting out, our glossary has something for everyone. We’ve provided some basic information about printed circuit boards and the services we offer. We’ve also included a short directory listing all the first letters of the PCB terms, with links to each section on the page. Next to each term, you’ll find a brief definition to help you quickly locate the information you need.
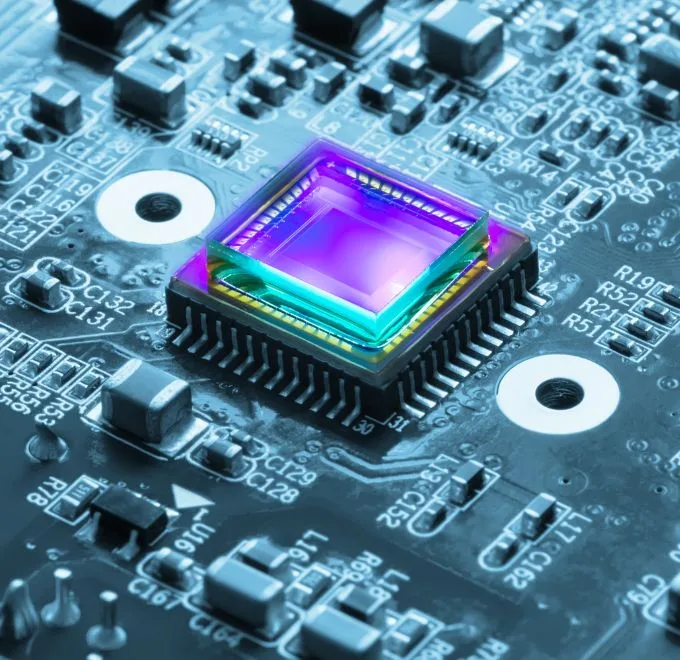
A
Term | Definition |
---|---|
Assembly | The process of populating a printed circuit board with electronic components |
Annular ring | The area of exposed copper around a drilled hole on a PCB |
AOI (Automated Optical Inspection) | A system used to check the quality of PCB assembly, using cameras to inspect PCBs for defects |
AC (Alternating Current) | An electric current that changes direction periodically |
Altium Designer | A software tool used for designing electronic systems, including PCBs |
Artwork | The design file of a PCB in its final form that is ready to be sent to a manufacturer for fabrication |
Adhesive bonding | A process of using an adhesive to bond two or more materials together |
Ambient temperature | The temperature of the surrounding environment, can impact the performance of PCB components |
Analog circuit | A circuit that uses continuous signals, such as a voltage or current, to transmit information |
Arduino | An open-source hardware and software ecosystem used for building electronics projects and prototyping. |
Attenuation | The reduction in amplitude of a signal as it travels through a circuit or transmission medium |
Automatic router | A software tool used to automatically create the routing paths on a PCB |
Air gap | The distance between two conducting objects or regions |
Aspect ratio | The ratio of the thickness of a PCB to the diameter of its smallest hole |
Automated through-hole insertion | A process for inserting through-hole components onto PCBs using a machine |
Aqueous cleaning | A process of cleaning PCBs using a water-based solution |
Acid etching | A process of using a chemical solution to remove unwanted copper from a PCB |
Anti-aliasing | A technique used in digital signal processing to reduce distortions and artifacts in a signal |
ANSI (American National Standards Institute) | The organization that coordinates the development of US voluntary national standards |
Aperture | An opening in a mask or stencil used for applying solderpaste or etching copper on a PCB |
Assembly drawing | A drawing that shows how the various components of a PCB assembly fit together |
Automated optical alignment | A process of aligning electronic components on a PCB using machine vision systems |
Automated optical measurement | A process of measuring the dimensions and position of components on a PCB using machine vision systems |
Automated X-ray inspection | A process of inspecting the internal structure of PCBs using X-ray systems |
Align | The positioning of two objects in a specific orientation |
Anodizing | A process of coating a metallic surface with a protective oxide layer |
Analog-to-digital converter | A device that converts an analog signal, such as voltage or current, into a digital signal |
Andon | A visual display board used to indicate the status of a manufacturing line |
Aluminum PCB | A type of PCB that uses an aluminum substrate instead of the traditional fiberglass |
Ambient light sensor | A sensor on a PCB that can detect the level of ambient light in an environment |
Ampere | A unit of electric current in the International System of Units (SI) |
Automatic test equipment | A system used to test and diagnose faults in electronic components |
Axial lead | A type of lead used on through-hole electronic components |
Automated optical placement | A process of placing electronic components onto a PCB using machine vision systems |
Automated optical inspection | A process of inspecting PCBs for defects using machine vision systems |
Antistatic mat | A mat used to reduce the buildup of static electricity when working with electronic components |
Area array | A type of electronic component package where the leads are arranged in a two-dimensional array |
Active component | A component that can supply or control power in an electronic circuit |
Aperture mask | A mask used to apply solderpaste or etch copper on a PCB |
Arc | An electrical discharge that occurs when the voltage difference between two points exceeds a certain level |
Autotrace | A software tool used to automatically trace the outline of a PCB design |
B
- Bandwidth – The frequency range that a circuit or device can handle or operate within.
- Blind Via – A hole drilled through outer layer(s) of a PCB, but does not go all the way through.
- Bus – A communication pathway that transfers data between components of a system.
- BOM (Bill of Materials) – A document that lists all of the components used to assemble a PCB.
- Bypass Capacitor – A capacitor that is placed between power and ground to filter out noise.
- Buffered – A circuit that uses a buffer to drive signals without drawing significant current.
- Breakout Board – A PCB that is used to break out signals from a connector to individual headers or terminals.
- Backdrill – The process of removing a portion of a through-hole via from the opposite side of the PCB.
- Blind and Buried Vias – Vias that are drilled and plated within the layers of a PCB without extending to the outer layers.
- Bonding – The process of attaching a wire or electrical connection to a PCB or component using a thermal process.
- Bottom Layer – The lowest layer of a multi-layer PCB that is closest to the board substrate.
- Bright Tin Plating – A type of plating used to provide a bright, corrosion-resistant surface to PCB traces.
- Ball-Grid Array (BGA) – A type of surface-mount technology package used to connect a device to a PCB.
- Blueprint – A schematic or diagram that provides a visual representation of a PCB or circuit design.
- Blind Microvia – A type of blind via that is smaller than traditional through-hole vias.
- Bus Matrix – A matrix that controls communications between peripherals and subsystems.
- Box Build – Term used to describe the final assembly of an electronic product or system.
- Board-In – A type of mounting method where the PCB is mounted securely inside a housing.
- Base Material – The substrate material that makes up the foundation of a PCB.
- Bed-of-Nails – A test fixture that uses a grid of pins to electrically test a PCB.
- Backplane – A PCB used to interconnect multiple printed circuit boards together.
- Blind Via Hole – A drilled hole that only passes through some of the layers in a multi-layer PCB.
- Bond Pad – A metalized area on a PCB where a wire is attached in wire bonding.
- Brown Out – A state where power supply voltage drops for a short period of time.
- Barrel Plating – A process where metal is electroplated in a hole or via.
- Bypassing – The process of providing a low-impedance path for high-frequency signals.
- Balanced Line – A pair of wires carrying opposite signals that are designed to reject noise and interference.
- Bare Board – The PCB without any components or electronic parts attached.
- Blind Via Technology – The process of drilling small diameter holes in a multilayer PCB between two layers.
- Breakout – A PCB that is used to access signals or connections that are not available on the main PCB.
- Blind Hole – A hole that does not pass through a PCB completely.
- Baseline Noise – The term used to describe the amount of random noise present in a signal.
- Ballast Resistor – A resistor used to limit current flow in a circuit.
- Body Bias – The process of adjusting the voltage of a device’s body to optimize its performance.
- Bottom Terminated Component (BTC) – A type of surface-mount technology component.
- Buried Via – A via that is drilled and plated between internal layers of a PCB.
- Board Stiffener – A mechanical support added to PCB for additional rigidity.
- Bifurcation – A division of a signal into two separate paths.
- Board Thickness – The distance between the top and bottom surfaces of a PCB.
- Build Plan – The process of planning a PCB build, from design to final assembly.
- Base Material Surface Finish – The finish applied to the base material before PCB manufacturing.
- Bus Architecture – The structure and design of a bus system in an electronic device.
- Blind Slot – A slot that does not pass through a PCB completely.
- Bill of Material Template – A standardized format for creating a Bill of Material.
- Barrel Fill – The amount of electrolyte deposited into the via hole during the plating process.
- Back Annotation – The process of updating the schematic with changes made to the PCB.
- Bulk Metal Foil Resistor – A high-precision, high-stability resistor.
- Balanced Transmission Lines – A pair of transmission lines that carry signals of equal amplitude and opposite phase.
- Board Density – Amount of circuitry and components on a PCB per unit area.
- Blind and Buried Via Design – The process of designing vias that are not visible from the surface of a PCB.
C
- CAM file – A file used by the manufacturer to create a PCB layout.
- CAM – Computer-Aided Manufacturing (CAM) refers to the use of computer software and hardware to analyze and transfer electronic designs created in CAD (Computer-Aided Design) format to the manufacturing process. CAM helps to streamline and automate the production process, resulting in faster and more efficient PCB assembly production.
- Conductive Pattern – Conductive Pattern refers to the arrangement or layout of the conductive material on the base laminate, which serves as the pathway for electrical energy flow. This includes the conductors, lands, and through connections within the design.
- Capacitance – The property of a circuit that stores an electrical charge.
- Carbon Composition Resistor – A resistor made of carbon.
- Carrier – A standalone component that holds an integrated circuit.
- Cascade Configuration – The arrangement of transistors in a common-emitter circuit.
- CAD – CAD, which stands for Computer-Aided Design, is a software program that utilizes advanced algorithms to create models and drawings of printed circuit boards (PCBs), providing a visual representation of the conductor layout and signal paths.
- Component – A component is an electronic device that performs a specific electrical function and is typically mounted to a circuit board. Common examples of components include resistors, capacitors, inductors, and integrated circuits (ICs).
- Component Sourcing – Component sourcing is the process of finding and purchasing electronic components from suppliers to be used in the production of electronic products. This can include researching the best suppliers for specific components, negotiating prices, and managing the logistics of acquiring and delivering the components to the manufacturing facility. Effective component sourcing is important for ensuring timely and cost-effective PCB assembly production.
- CCL – CCL stands for Copper Clad Laminate, which is a fundamental material used to make PCBs. It consists of a reinforcing material, which can be either glass fiber or wood pulp paper, that has been impregnated with resin. Copper layers are then bonded to either one or both sides of the reinforcing material through a lamination process.
- CEM-1 – A type of epoxy-based printed circuit board laminate material.
- CEM-3 – A type of fiberglass-based printed circuit board laminate material.
- Circuit – The path that an electrical current flows through.
- Cutoff Frequency – The frequency at which a filter begins to attenuate a signal.
- Copper Clad Laminate – The material used to make PCBs.
- Current Density – The amount of current flowing through a circuit per unit of area.
- Capacitance Test – A test to measure the capacitance of a capacitor.
- Capillary Flow – The movement of liquid solder during reflow soldering.
- Conditional Locations – Peripheral locations that are only valid under certain conditions.
- Counterbore – A flat-bottomed hole created by drilling and then enlarged by milling or reaming.
- Copper Weight – The thickness of the copper layers on a PCB.
- Co-planarity – The property of electronic components that are designed to have their leads or balls uniformly level.
- Component Assembly – The process of installing components on a PCB.
- Conformal Coating – A protective coating that is applied to a PCB.
- Controlled Impedance – The process of controlling the impedance of a transmission line.
- Copper Foil – Copper Foil refers to a layer of copper that is applied to both the outer and inner layers of a multilayer PCB to create the conductive pathways. The copper foil can either be pre-bonded by the CCL or FCCL manufacturer to a base material core, or it can be pressed into a multilayer board to create a copper conductor. The thicknesses of copper foil vary but commonly include 1/3oz, 1/2oz, 1oz, 1.5oz, 2oz, and so on.
- Copper Clad – Copper Clad refers to a material used in printed circuit board manufacturing, which consists of a laminate core that is bonded with a thin layer or sheet of copper foil. This copper foil serves as the base material for the printed circuits.
- Copper Etching – The process of removing copper from a PCB.
- Capacitor – A device used to store an electrical charge.
- Ceramic Capacitor – A capacitor made of ceramic material.
- Current Rating – The maximum amount of current a circuit or component can handle.
- Cutoff – The frequency at which a filter begins to attenuate a signal.
- Current Divider Rule – A rule used to calculate the current flowing in each branch of a circuit.
- Clamping Circuit – A circuit that limits the voltage between two points.
- Component Placement – The process of placing components on a PCB.
- Conductance – The reciprocal of resistance, measured in Siemens.
- Conductor – A material that allows electricity to flow through it.
- Conformal Coating Thickness – The thickness of a conformal coating applied to a PCB.
- Controlled Impedance Test – A test to ensure that a transmission line has the desired impedance.
- Core – The innermost layer of a multi-layer PCB.
- Core Thickness – The thickness of the laminate base without copper.
- Cover Layer – Same as Coverlay. The outer layer(s) of insulating material is applied over the conductive pattern on the surface of a flexible and rigid-flex printed circuit board.
- Coverlay – A flex circuit coverlay has a similar function to a solder mask employed in rigid printed circuit boards. However, it is designed to be flexible and durable to cater to the demands of a flexible PCB. Typically, coverlay comprises a base of Polyimide (PI) material, adhesive, and release paper. During the assembly process, the manufacturer tears off the release paper and aligns the remaining materials onto the FPC, completing the coverlay process.
- Cut lines – The cut line is going to be used to program the router path and it represents the board outside edge.
- Crystal Clock – A clock that uses a crystal oscillator.
- Ceramic Substrate – A substrate made of ceramic material.
- Current Source – A circuit that produces a current regardless of the load applied to it.
- Circuit Board – A board that contains electronic components.
- Clean Room – A controlled environment used for manufacturing or testing.
- Creepage Distance – The distance between two conductive parts separated by an insulator.
- Capacitor Bank – A collection of capacitors connected in parallel or series.
- Ceramic Capacitance – The capacitance of a ceramic capacitor.
- Chip Capacitor – A miniature capacitor.
- Coil – A device that produces a magnetic field when current flows through it.
- Common Mode Impedance – The impedance between two conductors and a common reference.
- Controlled Impedance Line – A transmission line designed to have a constant impedance.
- Core Material – The material used to make the core of a PCB.
- Cross-Section – A drawing that shows the internal structure of a PCB.
- Cutoff Frequency Response – The frequency response of a filter at the cutoff frequency.
- Custom IC – An integrated circuit that is custom-designed for a specific application.
- Clamping Voltage – The voltage across the clamping circuit.
- Characteristic Impedance – Characteristic Impedance is an ohmic measurement of the resistance, inductance, conductance, and capacitance of a transmission line. In PCBs, the value of the characteristic impedance is determined by several factors, including the trace’s width and thickness, the spacing between the conductor and the ground plane(s), and the dielectric constant (Dk or Er) of the insulating material.
- Clad or Cladding – Cladding, or clad, refers to a thin layer or sheet of metal foil that is bonded to a laminate core in order to create a base material for use in printed circuits. This base material is commonly used in the production of PCBs.
D
DFM (Design for Manufacturability): A design approach that considers manufacturing and assembly requirements to increase production efficiency and decrease the rate of faulty products.
- DFA – DFA (Design for Assembly) is a design principle that aims to consider the subsequent assembly and manufacturing processes when designing a product. The goal of DFA is to minimize manufacturing costs and assembly complexity while maximizing production efficiency and manufacturing quality of the PCB. In carrying out DFA design, potential difficulties and defects that may arise during the assembly process must be taken into consideration, and corresponding design adjustments must be made to optimize the production and assembly efficiency of the PCB.
- Date Code – Date Code is the week time of PCB manufacturing. The format can be WWYY or YYWW. Y means Year and W means Week.
- Delivery Format – Delivery Format refers to the specifications through which you request the manufacturer to fabricate and deliver your PCB design. At JHYPCB, we provide two delivery formats options: Unit Delivery (for single-piece PCBs) and Panel Delivery (where panels are either provided by the customer or manufactured by us). If you opt for panel delivery, it is advisable to check with us if your panel design complies with our manufacturing capabilities, which includes Rigid PCB, HDI board, MCPCB, and Flexible & Rigid-flex Circuit.
- Deburring – Process of removing burrs after drilling.
DIP (Dual In-line Package): A type of electronic component packaging with two parallel rows of pins on either side of the package.
DRC (Design Rule Check): A software tool used to validate that the design of a PCB conforms to specific rules and guidelines.
DDR (Double Data Rate): A type of synchronous dynamic random access memory (SDRAM) that can transfer data twice as fast as SDRAM.
DRAM (Dynamic Random Access Memory): A type of RAM that stores each bit of data on a separate capacitor, which must be refreshed constantly to prevent data loss.
DUT (Device Under Test): The electronic device being tested in a measurement or test scenario.
DC (Direct Current): Electrical current that flows in one direction only.
DFM&DFT (Design for Manufacturing and Design for Testability): A design approach that considers both manufacturing and test requirements to increase production efficiency and ensure proper testing of the PCB.
DCO (Digital Controlled Oscillator): A type of oscillator that uses a digital control signal to adjust the frequency of the oscillator.
DMTL (Dry Film Photoresist): A type of photoresist material used to create the pattern for PCB traces during the etching process.
DRC (Design Rule Checking): A software tool used to verify that the design of a PCB conforms to specific rules and guidelines.
DSN (Design For Signal Integrity): A design philosophy aimed at ensuring signal integrity and reducing noise in high-speed digital circuits.
DDR SDRAM (Double Data Rate Synchronous Dynamic RAM): A type of SDRAM that can transfer data twice as fast as SDRAM.
Dwell Time: The time that a board is exposed to the developer during the etching process.
DUV (Deep Ultraviolet): A type of ultraviolet light used in photolithography to create patterns on the boards.
DMM (Digital Multimeter): A tool used to measure voltage, current, and resistance in electrical circuits.
DRC Verification: The process of using a software tool to verify that a design conforms to specific rules and guidelines.
DC-DC Converter: A type of power supply that converts one level of DC voltage to another.
D/C (Date Code): A code that identifies the manufacturing date of a component.
Diode: A component that allows current to flow in one direction only.
Driver: A device that provides the necessary signal voltage or current to drive a component or subsystem.
Dielectric Material: An insulating material between two conductive layers in a PCB.
Decoupling Capacitor: A capacitor that smooths out voltage changes in the power supply line.
Differential Pair: A pair of traces on a PCB that carry complementary signals and are designed to minimize signal crosstalk and noise.
Digital Signal Processor (DSP): A specialized microprocessor designed to process digital signals.
Drilling: The process of creating holes in a PCB for mounting components or for interconnection between layers.
Design for Reliability: A design approach that aims to ensure reliability and prevent failures in electronic systems.
Directive Antenna: An antenna that has a preferred direction for radiation or reception of RF signals.
D-SUB Connector: A type of electrical connector with two or more parallel rows of pins or sockets.
Differential Impedance: The ratio of the voltage differential to current differential in a transmission line.
- Dielectric Constant – Dielectric constant (Dk) is a physical property of a material which describes the ability of the material to store electrical energy in an electric field. It is also known as the relative permittivity and is dimensionless. The dielectric constant of a material is defined as the ratio of the electrical permittivity of the material to the electrical permittivity of a vacuum. The higher the dielectric constant of a material, the more electrical energy it can store in an electric field. In the context of PCB design, the dielectric constant of the substrate material used for the PCB can have a significant impact on the electrical performance of the circuit, particularly the characteristic impedance of transmission lines.
- Differential Signal – Differential Signal refers to a signaling method that uses a pair of traces with opposite binary states to transmit data. In this method, the data is conveyed as the polarity difference between the two traces on the printed circuit board.
- Double-sided PCB – Double-sided PCB is a type of circuit board that has metalized patterns on both sides of the board. It allows for the creation of more complex circuit designs with multiple layers of conductive traces and components, thereby reducing the size of the overall PCB. This type of PCB is commonly used in electronic devices that require increased circuit density and complexity, such as mobile phones, computers, and industrial control systems.
- Drill File – The Drill File, also known as the Excellon Drill File, contains X and Y coordinates with tool sizes that can be viewed in any text editor. This file is crucial in determining the final hole sizes in your PCB design.
- Dry Film – Dry Film is a type of photo imagable material that is applied onto a bare copper panel to create a protective layer. This material is then exposed to 365 nm UV light through a negative photo tool, which causes the exposed areas of the film to harden. The unexposed areas of the film are then removed by washing the material with a developer solution containing 0.8% sodium carbonate.
- Dry-Film Resists – Dry-film resists are a coating material that is specially formulated for use in producing printed circuit boards and chemically machined parts. These resists are ideal for use in all photomechanical operations and can withstand a range of electroplating and etching processes.
- Dry-Film Soldermask – Dry-film resist is a coating material that is laminated onto the printed circuit board to protect it from solder or plating. It is commonly used as a solder mask coating material.
E
- EAGLE – A popular PCB design software tool developed by Autodesk.
- Edge Bevel – A bevel operation performed on edge connectors of rigid PCB board to improve their wear and ease of installation.
- EDA – Electronic Design Automation, refers to software tools used for designing electronic systems.
- EDP – Electro-Deposited Photoresist, a process of creating a thin film photoresist layer for PCB fabrication.
- EFVS – Electromagnetic Field Visualization System, used for visualizing electromagnetic fields in PCBs.
- EMC – Electromagnetic Compatibility, a characteristic of a device that allows it to operate without interference.
- EMF – Electromotive Force, the voltage that drives current flow in an electric circuit.
- EMI – Electromagnetic Interference, the interference caused by electromagnetic radiation.
- EMS – Electronic Manufacturing Services, refers to the manufacturing services provided for electronic devices.
- EMC testing – Electromagnetic Compatibility testing, a process of testing the electronic device for its electromagnetic compatibility.
- Embedded System – A computer system that is integrated into a device or product.
- ESL – Emitter Coupled Logic, a type of digital circuit that uses transistors to create high-speed logic gates.
- ESD – Electrostatic Discharge, the sudden discharge of static charge that can damage electronic components.
- EMI Shielding – The use of shields to protect electronic components from electromagnetic interference.
- ENEPIG – Electroless Nickel Electroless Palladium Immersion Gold, a surface finish used in PCB fabrication.
- ENIG – Electroless Nickel Immersion Gold, another surface finish used in PCB fabrication.
- ESL/ESD – Electrostatic Sensitive Device/Electrical Static Discharge, damage caused by static charge during handling or manufacturing of electronic devices.
- Eye Diagram – A graph that shows the signal integrity of a digital signal by plotting waveforms against time.
- EDA software – Software used for designing and simulating electronic circuits and systems.
- Electrical Test – A test performed on PCBs to ensure their electrical function before deployment.
- Ethernet – A widely used networking standard with a physical layer based on twisted-pair cabling.
- Electro Deposited (ED) Copper – Electro Deposited (ED) Copper is a type of copper material prepared by electroplating technique. In the process of manufacturing printed circuit boards, electrolytic copper is a commonly used ED copper material, which is deposited by passing current through the negative electrode in the electrolyte to generate Cu2+ from the copper anode oxidation, and then depositing it into a copper layer on the anode. This method can make copper materials with different thicknesses, and can distribute copper materials evenly on the surface of the entire circuit board. ED copper is one of the important raw materials for making high-performance PCBs.
- Electroplating – Electroplating is a process of depositing a thin layer of metal onto a conductive surface through the use of an electrolyte solution and an electric current. In this process, the surface to be plated is first cleaned to remove any impurities, and then placed in an electrolyte solution containing metal ions of the plating material. A direct current (DC) power source is used to pass an electrical current through the solution and the metal ions are attracted to the surface, forming a coating. The thickness and properties of the coating can be controlled by adjusting the parameters of the electroplating process. Electroplating is widely used in many industries, such as automotive, aerospace, electronics, and jewelry, to enhance the surface properties and appearance of the finished product.
- Epoxy – Epoxy is a type of polymer that is commonly used in adhesives, coatings, and composites. It is created through a chemical reaction between an epoxy resin and a hardening agent, also known as a curing agent. Epoxy is known for its high strength, durability, and resistance to chemical and environmental damage, making it a popular choice in a variety of industries. It can be used in everything from construction materials to electronics manufacturing to automotive applications.
- Etching – Etching refers to the process of chemically or chemically and electrolytically removing sections of conductive material that are not required for a specific application.
- Excellon Drill File – It’s a type of drill file that will be accepted.
F
- Fab: The term “Fab” is short for “fabrication,” which is synonymous with “manufacturing” and “production” in the context of printed circuit boards.
- Fab Notes: Fab Notes, or Fabrication Notes, refer to a set of notes that are either included with the PCB data files (such as Gerber files) as a separate text document or may be shown on the PCB design itself in the form of a drawing. These notes contain specific details and requirements related to the PCB fabrication process.
- Fabrication Drawing: A Fabrication Drawing is a tool used to assist in the construction of a printed circuit board. It provides detailed information such as the location, size, and tolerances of holes to be drilled, dimensions of the board edges, as well as notes on the required materials and methods to be used in the fabrication process. It is often abbreviated as “fab drawing.”
- FAI: FAI stands for First Article Inspection, which is a comprehensive, independent, and documented physical and functional inspection procedure. The SMT first article assembly process is a critical step in the entire circuit board assembly process.
- FAB House: Fabrication house.
- Fan-out: A die-to-die interconnect method.
- Faraday Cage: A container used to shield electronic components from electromagnetic interference.
- Fault: A deviation from the expected behavior of a digital circuit.
- FCC: Federal Communications Commission.
- Feedthrough: A hole in a PCB that allows a signal or power to pass through to another layer.
- Ferrite bead: A passive electronic component used to suppress high-frequency noise.
- Ferrite Core: A core made of ferrite material used in inductors and transformers.
- FFT: Fast Fourier Transform.
- Fiducial: A marker or feature used for alignment in PCB assembly.
- Filling: A process used to fill unused space in a PCB.
- Final Inspection: The last step in the PCB production process where the board is inspected before shipment.
- Firmware: Software that is permanently stored in non-volatile memory.
- Flash Memory: A type of non-volatile memory that can be erased and reprogrammed electrically.
- Flex PCB: A flexible printed circuit board.
- Flip Chip: A semiconductor device that is flipped upside-down and mounted directly onto a substrate.
- Flip Chip BGA: A flip chip device mounted onto a ball grid array substrate.
- Flip Chip CSP: A flip chip device mounted onto a chip scale package substrate.
- Flood: A process used to cover the entire PCB with a single layer of copper.
- Footprint: The physical arrangement and size of a component on a PCB.
- Force: The measure of the strength of an electrical connection.
- FPCB: Flexible printed circuit board.
- FR-1: A type of flame-retardant paper-based PCB material.
- FR-2: A type of flame-retardant phenolic-based PCB material.
- FR-3: A type of flame-retardant epoxy-based PCB material.
- FR-4: A type of flame-retardant woven glass epoxy-based PCB material.
- Frequency: The number of cycles per second of a periodic waveform.
- Fusing Current: The current at which a fuse blows.
- Fuse: An electrical safety device that protects against overcurrent.
- Feedback: The process of returning a portion of the output signal to the input to control an amplifier’s gain.
- Ferrite: A ceramic material used to suppress high-frequency noise.
- Flux: A chemical substance used to clean, solder, and prevent oxidation of the metal during the soldering process.
- Frequency Response: How an electronic component or circuit responds to input signals of different frequencies.
- Front-End: The part of a circuit that processes the input signal.
- Filter: A circuit that attenuates or removes certain frequencies from a signal.
- Fastener: A device used to secure components to a PCB.
- Footprint Library: A collection of pre-designed component footprints.
- Fine Pitch: A small distance between pins on a component or pads on a PCB.
- Flash Program Memory: Non-volatile memory that is programmed in-system.
- Focus: Adjusting the sharpness of an image.
- Formal Verification: A method of verifying that a circuit design meets its specifications.
- Forward Bias: The condition where a diode allows current to flow from the anode to the cathode.
- Frame: A structure that supports and protects a PCB.
- Frequency Multiplier: A circuit that multiplies the frequency of an input signal.
- Functional Test: A test that assesses the functionality of a PCB.
- Fused Deposition Modeling (FDM): A 3D printing process that uses heated material to create structures layer by layer.
- FPC (Flexible Printed Circuit): A thin, flexible PCB.
- FFS (Form, Fit, and Function): The concept of ensuring that a replacement part or component is identical to the original in terms of its form, fit, and function.
- FET (Field-Effect Transistor): A transistor that uses an electric field to regulate the flow of current.
- FCCL: FCCL stands for Flexible Copper Clad Laminate, which is a composite material consisting of a flexible polymer substrate and a thin layer of conductive copper foil. FCCL is widely used in the manufacturing of flexible printed circuit boards (PCBs) due to its excellent flexibility, electrical conductivity, and thermal stability. It provides a reliable interconnection platform for electronic components and devices that require repeated bending, folding, and rolling, such as smartphones, laptops, cameras, and medical equipment.
- FCT: Functional Circuit Testing (FCT) is a testing process used to verify that a printed circuit board or other electronic assembly functions correctly according to its design specifications. FCT can be performed using specialized test equipment and software that can simulate various operating conditions and inputs to the PCB or assembly. This ensures that the device meets the required performance and reliability standards before it is released to the market.
- Fiducial Mark: Fiducial marks are essential for successful Surface-mount technology (SMT) assembly of a PCB or PCB set. These marks can take the form of drilled holes or etched dots, serving as reference points for the assembly machine’s camera to locate and position components accurately. It is crucial that the diameter of the fiducial marks be around 1.6mm and free from solder mask. When using fine-pitch components, there should be at least two sets of fiducial marks for optimal accuracy.
- Film Artwork: A positive or negative piece of film containing a circuit, solder mask, or nomenclature pattern.
- Finished Copper: Finished Copper refers to the weight or thickness of the copper layer that will be present on the surface of your PCB. Our services offer support for both HDI PCB and heavy copper PCB designs. The minimum thickness of finished copper that can be achieved through our services is 1/3oz, while the maximum thickness that can be attained is 10oz.
- Fixture: A Fixture is a specialized tooling device that facilitates the connection of a printed circuit board to a spring-contact probe test pattern. This device is commonly used within the PCB assembly industry for various purposes, such as programming, functional testing, and calibration.
- Flying Probe: The Flying Probe test is a method used in printed circuit board testing to check for open circuits, shorts, and other manufacturing defects in the circuitry. It involves the use of a specialized machine with multiple probes, which move in very precise patterns to make contact with pads and other locations on the PCB. The machine then sends a test signal through the probes and measures the resulting signals to detect any faults in the circuitry. This method is often used in cases where the PCB design is complex or where other testing methods are not practical.
G
- Ground Plane – A copper layer on a PCB that serves as a low-resistance path to ground.
- Gerber File – A standard file format used to describe PCB designs to manufacturing equipment.
- Gold Fingers – A coating of gold over the exposed edge connections of a PCB.
- Glob Top – A type of encapsulation used to protect and insulate wire-bonded semiconductor chips.
- Green Solder Mask – A type of solder mask commonly used on PCBs, known for its green color.
- Glass Transition Temperature (Tg) – The temperature at which a non-crystalline material undergoes a transition from a hard and brittle state to a soft and rubbery state.
- Ground Bounce – A type of noise caused by the inductance and resistance of the ground plane in a PCB.
- Guard Trace – A trace placed around signal traces to protect them from interference.
- Grid – A network of intersecting horizontal and vertical lines used to create a reference for component placement and routing on a PCB.
- Glass Epoxy – Glass Epoxy is a commonly utilized substance in the manufacturing of PCBs. The material consists of a fiberglass base which is saturated with an epoxy filler and then covered with a layer of copper laminate. This resultant material provides the necessary foundation for the production of high-quality PCBs.
H
Holes: These are drilled or punched openings on a PCB used for mounting components or providing electrical connectivity between layers.
Hot Air Leveling (HAL): A process that involves coating a PCB with a layer of molten solder and blowing hot air over it to create a smooth, even surface. This process is used to protect exposed copper areas and improve solderability.
- HASL: HASL, short for Hot Air Solder Leveling, is a surface treatment technology for printed circuit boards. It involves immersing the board in a bath of molten solder, then quickly passing it past jets of hot air to coat the exposed copper layer with a thin layer of solder. This process provides a protective layer against corrosion and oxidation, and allows for easy soldering of electronic components onto the PCB.
High-Frequency PCB: These are specialized PCBs engineered for use in applications with high-frequency electronics. They are designed to minimize signal loss, impedance, and noise by using sophisticated materials and construction techniques.
Hybrid PCB: A PCB that combines two or more different technologies on a single board. For example, a hybrid PCB may combine a traditional FR4 substrate with a ceramic substrate or even incorporate flexible circuits.
Hole Plugging: The process of filling a drilled hole in a PCB with conductive or non-conductive epoxy material to maintain the integrity of the board’s insulation and reduce the risk of soldering defects.
- Half-Hoes PCB: Half-Holes PCB, also known as Castellations PCB or Castellated-Hole PCB, refers to a type of printed circuit board technology in which rows of holes are routed along the edges of the board. These holes have a higher level of plating and are sometimes called “half-holes” because they are not through-holes that penetrate the entire thickness of the board.
- Halogen-Free: JPCA-ES-01-2003 is a standard set by the Japanese Printed Circuit Association (JPCA) for Halogen-Free PCB material. This standard specifies that Halogen-Free PCB material must contain no more than 0.09% (by weight) of chlorine (Cl) and bromine (Br) in the composition of the material. Halogens such as Cl and Br are commonly used in PCB materials as flame retardants, but they can release toxic gases when the PCB is subjected to high temperatures, such as during soldering or in case of fire. Halogen-Free PCBs are therefore considered to be safer and more environmentally friendly alternatives, especially in applications where human health and safety are of concern.
- HDI: HDI stands for High-Density Interconnect, which refers to a type of multi-layer printed circuit board that is constructed with ultra-fine geometry and conductive micro-via connections. In addition to these micro-vias, HDI PCBs often feature both buried and blind vias, and are produced using a process called sequential lamination. This advanced PCB technology allows for a much higher density of connections than traditional PCBs, making them ideal for use in complex electronic devices where space is at a premium.
- Heavy Copper:
Heavy copper PCBs refer to the types of PCBs where the external or internal copper layers are thicker than the standard, typically with weights of 2oz, 2.5oz, 3oz, or more. These PCBs are specifically designed to handle high current, voltage and power requirements, making them ideal for applications where reliability and durability are crucial.
One of the key advantages of using heavy copper PCBs is their ability to carry high currents without overheating or breaking down. This makes them perfect for demanding applications such as power supplies, motor controllers, and other high-power electronic devices.
By using heavy copper traces, these PCBs can withstand the rigors of high temperatures, harsh environments, and extreme operating conditions. As a result, they provide superior performance and reliability over standard PCBs.
- Hole Density: The density of holes, which refers to the number of holes on a per dm² board surface basis, typically averages around 600 holes/dm² for a standard double-sided PCB. However, with increasingly smaller component sizes and denser circuits being placed onto ever-shrinking board surfaces, the hole density has also increased. This density is directly related to the cost of drilling the PCB. The more holes that need to be drilled, the longer the board stays on the drilling machine and the more drill bits need to be used. As long as the hole density stays under 1,000 holes/dm², this factor will not affect the cost significantly.
- Hole Void: A void in the metallic deposit of a plated-through hole exposing the PCB base material.
I
Insulation Resistance – The resistance offered by an insulating material to electric current.
Intermittent Connection – A disconnected or poor connection that occurs only at certain times, making it difficult to detect and diagnose.
- IPC: IPC stands for Association Connecting Electronics Industries, formerly known as “Institute of Printed Circuits,” which was established in the fall of 1957. This organization is the sole trade association that unites every significant actor in the electronics industry, including designers, PCB manufacturers, PCB assembly companies, suppliers, and original equipment manufacturers. IPC sets the industry’s standards, provides technical training and certification, conducts research and development, and advances advocacy initiatives to ensure safe and reliable electronic products.
IPC-7351 – This is the generic requirements for surface mount design and land pattern standardization.
Impedance – The total opposition offered by a circuit to the flow of alternating current, including both resistance and reactance.
Inductance – The property of an electric circuit that opposes changes in current flow, causing a delay in the build-up of a steady-state current.
- Integrated Circuit (IC) – A miniaturized electronic circuit consisting of active and passive components, such as resistors, capacitors, and transistors, that are integrated on a single semiconductor chip to perform a specific function.
- ICT: In-Circuit Testing (ICT) is a process of testing printed circuit boards using specialized test equipment to ensure that the components on the board are assembled correctly and function as intended. During ICT, the board is probed using test fixtures and specialized software that can detect the presence or absence, value and orientation of different components, as well as identify any faults such as open circuits, short circuits, and other defects. ICT is an important step in the manufacturing process of PCBs as it helps to identify and correct any production errors before the boards are shipped to customers.
- IEEE: IEEE (Institute of Electrical and Electronics Engineers) is the world’s largest technical professional organization dedicated to advancing technology for the benefit of humanity. IEEE has more than 400,000 members in over 160 countries and is a leading authority on a wide range of areas, including aerospace, computers, telecommunications, biomedical engineering, electric power, and consumer electronics. The organization publishes over 30% of the world’s literature in the electrical and electronics engineering and computer science fields and hosts more than 1300 conferences annually, allowing members to network and stay up-to-date on the latest technological innovations.
- Imaging: In the PCB fabrication process, “imaging” refers to the process of transferring a circuitry pattern onto the panel (which is typically made of copper-clad laminate material) by exposing the panel to light through a mask or photo tool in a process called photolithography. The areas of the panel that are exposed to light are subsequently etched away, leaving behind the circuitry pattern that will be used in the manufacturing of the physical board. In short, imaging is the process of creating the pattern that the copper will follow when the non-copper areas are etched away.
- Inner layers: In the manufacturing of multi-layer PCBs, the internal layers of the board are referred to as “inner layers”. These are layers of copper circuitry pattern that are applied to the non-conductive substrate material and which are sandwiched between the outer layers of the board. The inner layers are typically connected to other layers through drilled holes known as “vias.” The inner layer conductive pattern is created using the photolithography process and must be aligned precisely with the other conductor patterns on different inner layers and outer layers of the board for the correct functioning of the final PCB. The inner layers are a crucial part of a multilayer PCB, allowing for a greater amount of circuitry to be installed in smaller board sizes.
- Intermetallic Compounds (IMC): When the melted solder paste (alloy) comes into contact with either the PCB finish or the lead finish of components, a minuscule quantity of Sn present in the solder joins with the metal of the finish or the underlying copper to generate a metallurgical compound.
J
- Jumper – A short printed circuit board connector used to bridge or bypass a circuit path.
- Jack – An electrical connector that is used for audio, video, or data signals.
- Jig – A tool or device used to hold, position, or guide components during the assembly of a printed circuit board.
- JFET – Junction Field Effect Transistor, a type of transistor that is controlled by an electric field.
- Jumper wire – A short piece of electrical wire used to jump over a break in a printed circuit board trace.
- Joint – The point where two or more conductive elements (such as wires, components, or circuit board traces) are connected together.
- Joule – The unit of measure for energy in the International System of Units (SI), often used to express the amount of energy that can be dissipated by a resistor in a printed circuit board circuit.
- JTAG: JTAG stands for “Joint Test Action Group.” It is an industry standard that defines a way to verify designs and test printed circuit boards after manufacture. The JTAG standard was codified by the Institute of Electrical and Electronics Engineers (IEEE) in 1990 as IEEE Standard 1149.1-1990, entitled “Standard Test Access Port and Boundary-Scan Architecture.” It is widely used for both testing and debugging hardware and software. Additionally, JTAG allows reading out values from internal registers of chips or systems.
K
- Kelvin – A unit of measurement for temperature, often used in relation to thermal management in PCB design.
- Keepout – A designated area on the PCB where no components or other traces are allowed, usually used to avoid electrical interference or thermal issues.
- Key – A feature on a component or PCB that ensures that it is only inserted in the correct orientation.
- Keyboard – A type of PCB used as an input device for computers or other electronic devices.
- Kicad – An open-source software package used for PCB design and layout.
- Kill switch – A switch or button on a PCB used to cut off power in an emergency or to safeguard sensitive components.
- Kiloohm – A unit of measurement for electrical resistance equal to one thousand ohms.
- Kapton – Kapton, also known as polyimide, is a high-performance film developed by Dupont in the late 1960s. It has a unique set of properties that make it highly suitable for a wide range of applications. One of the key advantages of Kapton is its ability to remain stable across a broad temperature range, from -269 to +400 degrees Celsius. In the flexible circuit manufacturing industry, Kapton is commonly used as the dielectric material in flexible copper clad laminate (FCCL), coverlay, and stiffener for FPC and rigid-flex PCB.
Flexible circuit manufacturers have the option to use either adhesive or adhesiveless FCCL to build their flexible circuits. Adhesiveless FCCL provides a number of benefits, including improved thermal stability, better electrical performance, and reduced manufacturing costs. Adhesive FCCL, on the other hand, offers some advantages as well, such as better peel strength and improved handling characteristics during the manufacturing process. To determine which option is best for a particular application, it is important to work with experienced and knowledgeable professionals in the industry.
L
- Laminate – A substrate material made by impregnating layers of cloth or paper with resins, often used as the base material for PCBs.
- Laminate Thickness – Laminate thickness refers to the thickness of the insulating material that makes up a printed circuit board. This insulating material, or laminate, is typically made up of layers of fiberglass reinforced with epoxy resin. The thickness of the laminate is an important factor in determining the overall thickness and mechanical strength of the PCB. The laminate thickness is typically measured in mils or millimeters. The typical laminate thickness for a standard PCB ranges from 0.4mm to 3.2mm, depending on the application and the specifications of the PCB design.
- Layer – A single conductive or non-conductive material that makes up one part of a PCB stackup.
- Layout – The design of the physical arrangement of components and routing on a PCB.
- LED – A light-emitting diode, often used as a low-power indicator on PCBs.
- Load – The amount of current drawn by a circuit, often used to determine the electrical specifications for a PCB.
- LPI – Liquid Photo-Imageable solder mask, a type of material used to mask PCBs during the soldering process.
- LGA – Land-grid array, a type of surface-mount component package with a grid of pins on the underside.
- LDO – Low-dropout regulator, a type of voltage regulator used to maintain a stable output voltage on a PCB.
- Line width – The width of copper traces on a PCB, often determined by the electrical specifications of the circuit.
- Lead Time – The amount of time it takes for a PCB to be fabricated and delivered. This includes the time needed for the design review, manufacturing, testing, inspection, and shipping. PCB lead time can vary depending on the complexity of the design, the number of layers, the type of materials used, the volume of the order, and the manufacturing location. In general, PCB lead time can range from a few days to several weeks or even months. PCB manufacturers typically provide lead time estimates to customers based on their specific requirements and priorities.
- Laminating Press – Laminating Press is the process by which the CCL core(s) of a printed circuit board (PCB) are melted together through heat and pressure with copper layers and prepreg layers to manufacture multilayer printed circuit boards.
- Layer-to-Layer Spacing – The thickness of dielectric material between adjacent layers or conductive circuitry in a multilayer printed circuit board.
- Legend – A format of lettering or symbols on the printed circuit board: e.g. part number, serial number, footprint, and patterns. See Nomenclature or Silk Screen.
- Loss Tangent – Tangent is a measure of how much of the power of a signal is lost as it passes along a transmission line on a dielectric material.
M
- Mounting – The process of attaching electronic components to a PCB. There are different types of mounting processes, including through-hole mounting and surface-mounting.
- Mask – A thin layer of protective material used to cover and protect certain areas of a PCB during the manufacturing process.
- Multilayer – A PCB design that incorporates multiple layers of conductive material separated by insulating layers. Multilayer PCBs are often used in complex electronic devices.
- Microstrip – A type of transmission line that consists of a thin strip of conductive material on a PCB. Microstrip lines are used to transfer high-frequency signals.
- Matte Finish – The surface finish on a PCB that has a non-reflective, matte appearance. This finish is often used in high-density PCBs to reduce the risk of solder bridging between small components.
- Mask Clearance – The distance between the edge of a solder mask and the copper pads or traces on a PCB. Proper mask clearance helps prevent solder bridging and other issues during the assembly process.
- Manual Routing – The process of manually routing traces between components on a PCB. This is typically done using a computer-aided design (CAD) software tool.
- Minimum Pitch – The minimum distance between adjacent leads or pads on a PCB. This is an important specification in surface-mount technology as it affects the ability to place components accurately on a PCB.
- Metal Core PCB – A type of PCB with a metal core, typically made of aluminum or copper, that provides thermal conductivity and helps dissipate heat generated by high-power components.
- Moisture Sensitivity Level (MSL) – A rating system that indicates the degree of moisture sensitivity of a surface-mount component. MSL rating is important for avoiding damage to components during the assembly process.
- Micro BGA: µBGA, or Micro BGA, is the abbreviation of micro ball grid array.
- Micro Circuits: Very fine lines 2mil and less, and small micro vias 3 mils and less.
- Micro-Via: Micro-Via, also called Microvia, is usually defined as a conductive via used to connect adjacent layers of a multilayer PCB, typically less than 6mil in diameter, including 3mil, 4mil, and 5mil. It may be formed by laser ablation, plasma etching, or photo processing.
- Mil: One-thousandth of an inch 0.001:” (0.0254 mm). [From abbreviation of milli-inch].
- Minimum Traces & Spacing: Minimum traces and spacing refer to the smallest allowable distance that can be maintained between two adjacent copper traces on a printed circuit board and between the copper traces and other board elements such as pads, vias, and through-holes.
This parameter is critical in the PCB design process as it determines the electrical performance and reliability of the final product. If the traces or spaces are too small, it can lead to issues such as signal interference, crosstalk, and electrical shorts. Therefore, it’s important to adhere to the minimum traces and spacing guidelines specified by the PCB manufacturer and the industry standards.
N
Netlist: A list of all the electrical connections and components in a PCB design.
NPTH: Non-Plated Through Hole, a type of hole in a PCB that is not coated with a conductive material.
NC Drill file: Numerical Control Drill file, a file that provides instructions to a drilling machine for drilling the holes in a PCB.
NRE: Non-Recurring Engineering, the one-time costs associated with designing and implementing a new PCB.
Nominal: The nominal size of a component or trace on a PCB is the intended or expected size, which may differ slightly from the actual size due to manufacturing tolerances and variations.
- Negative: In the context of PCB fabrication, the term “negative” typically refers to the process of creating a PCB pattern on a light-sensitive layer called a “resist.” In the negative process, the opaque areas of the pattern are represented by clear regions on a film negative, while the transparent areas of the pattern are represented by opaque regions on the film. The film negative is then used to create an image of the pattern on the resist layer through a process of exposure and development, with the opaque areas of the film blocking the light and leaving behind the pattern on the resist. This negative image of the pattern is then used as the basis for the subsequent steps in the PCB fabrication process, such as etching or plating.
- Number of Holes: In PCB fabrication, the number of holes is an important factor that affects the cost and complexity of the process. Holes are typically used for component mounting and for making electrical connections between different layers of the PCB. The number of holes on a PCB depends on the design and usage of the board.
For example, a simple single-layer PCB for a hobby project may have only a few holes, while a complex multi-layer PCB used in a high-end electronic device may have hundreds or thousands of holes. The number and size of the holes can impact the cost of the PCB because they often require extra machining steps and can impact the yield of the fabrication process. Therefore, optimizing the hole count and placement is an important consideration in PCB design to balance cost, functionality, and manufacturability.
O
OSP (Organic Solderability Preservatives): A thin layer of organic material that is applied to the copper pads of a PCB to protect it from oxidation and ensure good solderability during assembly.
Over-etching: The phenomenon that occurs when the etchant used in the manufacturing process removes too much copper from the PCB design, causing the desired circuitry to be damaged or destroyed.
Overhang: A type of possible manufacturing defect, where a portion of the conductive material on the PCB extends beyond the edge of the PCB dielectric. This can cause short circuits or other issues during assembly and operation.
Outline: The shape or dimensions of a PCB, typically defined by a board outline or profile (These may include routing and drilling information, cutouts, slots or other features).
ODB++ (Open Database-Plus-Plus): A widely used PCB data exchange format that includes design data, manufacturing data and testing data. ODB++ was developed by Mentor Graphics Corporation.
- Outer layer: The outer layer refers to the top and bottom layers of the board that are visible and carry the majority of the electrical components of the circuit. These layers are typically made of copper and are etched to create the traces and pads that connect the components. The outer layer is also where the silk screen and solder mask are applied to label the components and protect the traces and pads from oxidation and other chemical reactions.
P
- Pad – A plated hole on a PCB used for component mounting
- Pad Size – Pad size refers to the diameter of the circular metal area that is used for mounting and connecting electrical components. The size of the pad can vary depending on the size of the component being connected and the requirements of the PCB design.
It is important to choose the appropriate pad size for each component to ensure that it is securely mounted and that there is sufficient surface area for good electrical contact. A pad that is too small can lead to poor connections or broken components, while a pad that is too large can take up too much space on the PCB and limit the number of components that can be included. The pad size is typically specified in the PCB design software or by the manufacturer of the component being used.
- PCB – Printed Circuit Board, an electronic circuit board made of laminated layers of conductive material
- Panelization – The process of arranging multiple PCB designs onto a larger panel for manufacturing and assembly
- Photoresist – A light-sensitive chemical used to create patterned layers on a PCB during the manufacturing process
- Pick and place – The process of automatically placing surface-mounted components onto a PCB using specialized machinery
- Polyimide – A type of high-temperature-resistant material often used in flexible PCBs, or as a substrate for rigid-flex PCBs
- Plating – The process of depositing a layer of metal onto a surface, often used to create conductive traces on a PCB
- Power integrity – The ability of a PCB to reliably deliver power to all of the components on it without voltage drops or other issues
- PTH – Plated Through-Hole, a type of hole on a PCB that is plated with metal to provide electrical connectivity between different layers
- Panel router – A machine that cuts or routes the profile of a PCB out of a larger panel.
- Part Number – “Part Number” refers to a coding system used to identify and label specific parts. It is typically assigned and managed by manufacturers or suppliers and can contain information about the characteristics of the part, the manufacturing date, batch number, and other details. Using the correct Part Number in product design and manufacturing ensures that the correct part is purchased and used.
- Pattern – The configuration of conductive and nonconductive materials on a panel or printed board. Also, the circuit configuration on related tools, drawings, and masters.
- Pattern Plating – The selective plating of a conductive pattern.
- PCB Assembly – PCB assembly, also known as electronics assembly, refers to the process of mounting and soldering electronic components onto a printed circuit board (PCB). This process involves placing electronic components on a PCB, such as resistors, capacitors, transistors, integrated circuits, and other electronic devices, and then soldering them onto the board so they can function together as a single device. PCB assembly can be a complex process that requires specialized equipment and skilled technicians.
- Peel Strength – Peel strength refers to the force required to peel a flexible material, such as a solder mask or adhesive, away from a surface, typically a copper pad on a printed circuit board. It is an important mechanical property to consider in the design and manufacturing of PCBs, as the peel strength of these materials can impact their durability, reliability, and performance. A high peel strength is typically desirable to ensure that the components and materials stay firmly attached to the board during operation and over time. The peel strength is usually measured in units of force per unit width, such as newtons per millimeter (N/mm) or pounds per inch (lb/in).
- Photoresist – A light-sensitive material that is used to establish an image by exposure to light and chemical development.
- PI – Polyimide, abbreviated as PI, is an insulation and mechanical support film material of FCCL (Flexible Copper Clad Laminate), and one of the main materials for Flexible Printed Circuits (FPC). It has excellent high temperature stability, mechanical performance, chemical inertness, and electrical properties, and can meet the manufacturing requirements of High Density Interconnect (HDI) printed circuit boards. Polyimide is usually made into a thin film to meet the flexibility and thinness requirements of FPC.
- Plated-Through Hole – A hole in a circuit board that been plated with metal (usually copper) on its sides to provide electrical connections between conductive patterns layers of a printed circuit board. Also refer to PTH.
- Polyimide – Refer to ‘PI’
- Prepreg – Prepreg (PP) is a commonly used term in the composite materials industry, which refers to a type of composite material consisting of fiberglass fabric that has been impregnated with resin. This process, known as pre-impregnation or pre-pegging, creates a material that is partially cured and ready to be further processed. The resulting product is commonly referred to as B-Stage, bonding sheet, or simply preg, and is widely used in various applications that require high-performance, lightweight materials with excellent mechanical and thermal properties.
- PSA – PSA is the acronym for Pressure Sensitive Adhesive, a type of adhesive that is commonly used in the electronics industry to bond stiffeners to specific regions of the flex circuit. The most commonly utilized PSA materials for bonding stiffeners onto FPCs are 3M467 and 3M9077 transparent double-sided tape. These materials are renowned for their exceptional bonding strength, durability, and ease of use, making them ideal for a wide range of electronic applications.
- PTFE – PTFE, or polytetrafluoroethylene, is a synthetic fluoropolymer of tetrafluoroethylene. It is known for its non-stick properties and is used widely as a non-stick coating for cookware, as well as for gaskets, seals, and bearings in industrial applications. Because of its high melting point, chemical resistance and low friction, PTFE is also an important material in the aerospace and telecommunications industries. It is known by the brand name Teflon, which is owned by the company DuPont.
Q
Quality Control (QC): This refers to the processes and techniques used to ensure that a PCB meets the required specifications and standards.
Quick-Turn PCB: A quick-turn PCB is a PCB that is manufactured quickly, usually within a few days or even hours. They are often used for prototyping or for urgent PCB production needs.
Quasistatic Inductance: Quasistatic inductance is a property of a PCB that determines its ability to store energy in a magnetic field between two conductive surfaces.
Quiet Zone: This is the area around the PCB where interference from other devices or electromagnetic waves is minimized to ensure proper signal transmission.
Quadrax: A type of high-speed interconnect cable that consists of four insulated conductors surrounding a central conductor. It is commonly used in applications where high transmission speeds are required, such as in data centers or telecommunications.
Quality Management System (QMS): A QMS is a set of policies, procedures, and processes used to manage and improve the quality of a PCB throughout its entire life cycle, from design to manufacturing and beyond.
- QFN: QFN stands for Quad Flat No-Leads Package, which is utilized to physically and electrically attach integrated circuits to printed circuit boards. Flat no-leads, also known as micro leadframe (MLF) and SON (small-outline no leads), is a type of surface-mount technology that is one of several package technologies used to make connections between ICs and PCB surfaces without requiring through-holes.
R
Resistance: The degree to which a material opposes the passage of electric current. Resistance is measured in ohms and is a key property of electronic components such as resistors.
Resistor: A passive electronic component that introduces resistance into a circuit. Resistors are used to limit current flow, adjust signal levels, and perform other crucial functions in electronic circuits.
RoHS: Stands for Restriction of Hazardous Substances. This is a directive that sets standards for the use of certain hazardous substances in electronic and electrical equipment sold in the European Union.
Routing: The process of creating the paths that connect the various components on a PCB. Routing typically involves numerous trade-offs and optimizations to ensure that the circuit functions optimally while minimizing layout complexity and cost.
Routing Density: The amount of copper trace or via that exists in a unit area of a printed circuit board. Routing density is an important consideration in the design of PCBs, as it can have a significant impact on signal integrity, noise, and other factors.
- Reflow: Reflow is a process used in the manufacturing of electronic circuit boards. The process involves the application of heat to solder paste, which then melts and joins the various components on the circuit board together. The components are placed on the circuit board using a pick-and-place machine, and the solder paste is applied using a stencil. The board is then heated in a reflow oven to a temperature high enough to melt the solder, but not high enough to damage the components. This ensures that the components are securely and reliably connected to the circuit board.
- RF: Radio frequency (RF) refers to the frequency range typically from 20 kHz to 300 GHz that electromagnetic signals are transmitted and received. It is the oscillation rate of an alternating electric current or voltage, or an electromagnetic field or mechanical system. This range is generally considered to be between the lower limit of infrared frequencies and the upper limit of audio frequencies. Signals in the RF spectrum can be easily radiated into space as radio waves from an oscillating current passing through a conductor. The specific frequency range of RF can vary, depending on the source, but generally falls within this range.
- Rigid-flex: Rigid-flex PCB is a type of circuit board that combines both rigid and flexible circuit boards together. This allows for the board to be used in more complex applications and provides greater flexibility in design. Rigid-flex PCBs are commonly used in electronics applications such as aerospace, military and medical devices, where space is limited and durability is important. They offer a number of benefits including reduced overall weight and space requirements, increased flexibility in design, and improved reliability due to the elimination of mechanical connectors.
- Rolled Annealed (RA) Copper: Rolled Annealed (RA) Copper is a widely used material in the manufacturing of flex circuits and rigid-flex PCBs due to its favorable grain structure and smooth surface, which make it perfect for dynamic, flexible circuits. Additionally, RA copper is often utilized in high-frequency applications, where a smooth copper surface is preferred to minimize insertion loss. In contrast, Electro Deposited (ED) Copper is another type of copper commonly used in the industry that offers different advantages and may be better suited for certain applications.
S
SMT (Surface Mount Technology): a method of mounting electronic components onto the surface of a PCB using automated assembly equipment.
Solder: a metal alloy used to join electronic components to a PCB.
- Solder Paste: Solder Paste is a conductive adhesive that is used to join electronic components together during the PCB fabrication process. It is typically made of a mixture of metal oxides and additives, which creates a paste-like substance that can be applied to the surfaces of the components to be joined. The solder paste is then heated and melted by a soldering iron, allowing it to flow into the spaces between the components and create a strong and secure connection.
The properties of the solder paste play a crucial role in determining the reliability and performance of the joint. Factors such as the composition of the solder paste, the temperature at which it is applied, and the duration of the heat application all impact the strength and durability of the joint. Proper selection and application of solder paste are essential for ensuring the quality and reliability of electronic circuits.
- Solder Paste Printer: Solder paste printer is usded to deposit solder paste onto the pads of bare printed circuit boards.
Solder mask: a layer of polymer that is applied to a PCB to protect the copper traces and prevent solder from shorting out adjacent components.
Signal trace: a conductive pathway on a PCB that carries electrical signals between components.
Silkscreen: a layer of ink that is applied to a PCB to identify component locations, polarity, and other important information.
Shielding: the process of enclosing a component or circuitry within a metal enclosure to reduce electromagnetic interference (EMI).
Stripline: a type of transmission line used on a PCB to carry high-frequency signals over long distances.
Serpentine routing: a method of laying out PCB traces in a zig-zag pattern to reduce the overall length of a trace and improve signal integrity.
- Short Circuit: A Short Circuit refers to an irregular connection between two points in a circuit with a low resistance. This results in an excess of current, which can be harmful if not managed properly.
- Single-Sided PCB: A single-sided PCB is a board that contains conductive traces on only one side of the board. The components and connections are then placed and soldered onto the same side of the board, avoiding the need for a second layer of circuits.
In single-sided PCBs, all the connections and components are placed on one side of the board, and the other side has a plain insulating material, usually fiberglass. This type of PCB is ideal for simpler electronic devices and applications with fewer components and simple circuits. Single-sided PCBs are easier and more affordable to design and manufacture, making them a cost-effective option for small to medium-scale production.
- SMOBC: Solder Mask Over Bare Copper (SMOBC) is a technique used in the fabrication of printed circuit boards. The end result of this method is copper as the final metallization under the solder mask, with no protective metal present. The areas of the board that are not coated are instead covered by solder resist, which serves to expose only the terminal areas of the components. This process eliminates tin-lead from being placed under the components.
- Solderability Testing: Solderability testing is the process of evaluating the ability of a metal or other surface to be successfully soldered. It involves testing the surface of a material to determine its ability to form a good bond with solder. The testing can be done by dipping the material in a bath of molten solder or by using other methods, such as thermal shock testing or wetting balance measurement. The results of the testing will determine whether a particular material or surface is suitable for use in soldering and can identify potential issues with the quality of the solder joint.
- SOP: Small Outline Package (SOP) is a type of surface-mount electronic component package. It typically has gull-wing leads on two sides of the package and a thermal pad on the bottom. The leads are bent outwards to allow for easy mounting on a circuit board. SOPs are used in a variety of applications, including microcontrollers, memory chips, and other integrated circuits. The smaller size of SOPs compared to other package types make them popular in applications where board space is at a premium.
- Stack-up: PCB stack-up is the arrangement of multiple layers of copper and insulating materials in a Printed Circuit Board. The stack-up defines the thickness, number, type, and order of the layers in the PCB, and it has a significant impact on the performance and reliability of the PCB. A typical PCB stack-up consists of alternating layers of copper and dielectric materials. The copper layers are used to create the traces and pads for the circuit, and the dielectric layers are used to isolate the copper layers from each other. The purpose of the stack-up is to control the impedance, signal integrity, and electromagnetic interference (EMI) characteristics of the PCB. A well-designed stack-up can improve the performance of high-speed digital and RF circuits, while a poorly designed stack-up can cause signal distortion, crosstalk, and other problems.
- Stencil: SMT stencil, also known as solder paste stencil, is a tool used in the surface mount technology assembly process for applying solder paste to the pads of a printed circuit board prior to the placement of surface-mount components. The stencil is typically made of a thin sheet of metal, such as stainless steel, and has cutouts that match the pattern of the pads on the PCB. When solder paste is spread onto the stencil and squeegeed across it, the paste is forced into the cutouts and deposited onto the pads of the PCB. The stencil helps ensure that the right amount of solder paste is applied to each pad, and that the paste is accurately placed for optimal component soldering during the reflow process.
- Stiffener: A flexible PCB stiffener is a material that is commonly used in the fabrication of flexible printed circuit boards to provide mechanical support and rigidity to areas of the board that require it. A flexible PCB stiffener is typically a thin sheet or strip of rigid material, such as FR4 or polyimide, that is laminated to the flexible circuit board to stiffen portions of the board that need additional support. By adding a stiffener to certain areas of a flexible PCB, it can help maintain the component’s position during assembly and improve the reliability of the board during use, particularly in high-stress environments. Flexible PCB stiffeners are also useful in preventing accidental flexing or damage to the board during handling, transportation, or assembly processes.
T
Through-Hole: A type of PCB assembly technology where components are inserted through drilled holes in the PCB and then soldered in place on the opposite side.
Test Point: A small contact area on a PCB that is used for testing or troubleshooting purposes.
Trace: A thin line etched onto a PCB to connect different components or conductive elements.
Thermal Relief: A technique used to reduce the amount of heat generated by through-hole component soldering by minimizing the amount of copper surrounding the component’s pin location.
Tombstone: A soldering defect that occurs when one end of a surface-mount component lifts up and bridges the gap between the component and the PCB, resembling a tombstone.
- Td: Thermal Decomposition Temperature (Td) is the temperature at which a material starts to decompose or break down due to thermal energy. It is an important parameter to consider when selecting materials for high-temperature applications, such as in electronic devices that generate a lot of heat. The Td of a material can be determined by thermal analysis techniques such as thermogravimetric analysis (TGA) or differential scanning calorimetry (DSC). Knowing the Td of material allows designers to select appropriate materials that will maintain their properties and performance when exposed to high temperatures.
- Tg: Glass Transition Temperature (Tg) is the temperature at which a material transitions from being rigid and brittle (in a glassy state) to being pliable and elastic (in a rubbery state) upon heating. It is an important characteristic of polymers and polymer-based materials like those commonly used in electronic devices. Tg is critical to the processing and use of these materials, as it can affect their mechanical, thermal, and electrical properties. For example, above Tg, the material may lose its dimensional stability, become more susceptible to thermal expansion, and have a change in electrical conductivity due to changes in its molecular arrangement. Tg is typically measured using techniques such as differential scanning calorimetry (DSC) or dynamic mechanical analysis (DMA).
- Turnkey Service: The Turnkey Service provided includes not only PCB fabrication but also component sourcing and PCB assembly. This comprehensive service is designed to streamline the manufacturing process and provide a convenient one-stop solution for customers. By entrusting the entire process to the service provider, customers can save time and effort while ensuring consistency and reliability in the products they receive.
U
Unit of Measure: The system of measurement used to design and measure the size and spacing of components and conductive elements on a PCB.
Ultraviolet Light: A type of light used in the etching process to expose the photoresist coating on a PCB to create a circuit pattern.
Undercutting: A chemical process used in PCB manufacturing to remove extra copper from the surface of a PCB, causing it to look like it has some part missing or has been cut out.
Underfill: A liquid epoxy or polyimide material used to fill the gap between the PCB and a surface-mounted component to provide additional mechanical stability.
Unpopulated Board: A PCB that has some or all of the components missing, often used for engineering development or testing purposes.
- UL: UL (Underwriters Laboratories, Inc.) is a leading organization that specializes in conducting independent product safety testing and certification. With a rich history and reputation for excellence, UL is dedicated to promoting safe living and working environments by providing rigorous testing and certification programs for various products, systems, and services. Its commitment to safety and quality has made it a trusted source of information and guidance for manufacturers, retailers, consumers, and regulatory authorities around the world.
- UV Curing: Polymerizing, hardening, or cross linking a low molecular weight resinous material in a wet coating ink using ultra violet light as an energy source.
V
- Via – A through-hole that connects two or more copper layers in a PCB
- Voltage regulator – An electronic circuit that regulates the voltage level of a power supply
- Via tenting – A process of covering a via on a PCB with soldermask to prevent accidental shorts
- Virtual ground – A reference point in a circuit that is not actually connected to ground
- V-Cut: V-cut,or V-cutting also named as V-grooving, please refer to V-Scoring for details.
- V-Grooving: V-grooving also named as V-cut (or V-cutting), please refer to V-Scoring for details.
- V-Scoring: V-Scoring, also known as V-grooving or V-cutting, involves creating a “V” shaped groove on both the top and bottom of a bare PCB, while maintaining a minimal amount of material to keep the boards intact. Instead of creating a route path along the board’s edge, V-scoring allows for the boards to be separated after the PCB assembly process. This is an alternative method for panelizing the PCBs.
- Via-in-Pad: Via-in-Pad (VIP) is a PCB technology where a via is placed directly underneath a component’s solder pad. This technique is used for high-density designs where space is at a premium. VIP allows for more efficient use of board space by reducing the number and size of vias needed to connect the component’s pin to other parts of the board. VIP can also improve thermal performance by allowing a more direct path for heat to escape from the component. However, the process of manufacturing via-in-pad can be more complex and costly than traditional via manufacturing techniques.
W
- Wave soldering – A process for soldering electronic components to a PCB using a wave of molten solder
- Wire-to-board connector – A type of electrical connector that connects wires to a PCB
- Working distance – The distance between the surface of a PCB and the tool or object being used during assembly or inspection
- Wire jumpers – Thin wires used to make connections between points on a PCB
- Washboarding – A PCB design flaw where the copper traces appear wavy due to excessive moisture or humidity during processing or storage
X
X-Ray Inspection – This is a non-destructive testing method used to inspect the internal structure of PCBs and identify defects such as misalignments, voids, or soldering issues.
X-Y Table – This is a computer-controlled positioning device used in PCB fabrication processes to accurately drill holes or place components on a board.
X-Y-Z Axes – In PCB fabrication, the X, Y, and Z axes represent the three spatial dimensions used to describe the placement of components on a circuit board.
Xilinx – Xilinx is a leading provider of programmable logic devices (PLDs), which are used to implement complex digital circuits on a PCB.
X Out – This refers to a PCB that has been rejected and marked with an “X” to indicate that it should not be used.
Y
Yield – Yield refers to the percentage of good PCBs produced during a manufacturing process. A high yield means that most of the PCBs produced are usable, while a low yield indicates a higher rate of defects or failures.
Y-Axis – In PCB fabrication, the Y-axis refers to the vertical axis used to describe the placement of components on a circuit board.
Yellowing – Yellowing is a cosmetic defect that can occur on the solder mask or silkscreen layer of a PCB over time due to exposure to UV light or other environmental factors.
Yocto Project – The Yocto Project is an open-source framework used to build custom Linux operating systems for embedded devices, including those that use PCBs.
Young’s Modulus – Young’s modulus is a measure of a material’s stiffness or elasticity, and is often used to describe the mechanical properties of PCB substrates and other components.
Z
Zero-Ohm Resistor: A surface-mount resistor with a resistance value of zero ohms, typically used to jumper traces on a printed circuit board.
Z-Plane: A plane on a printed circuit board that runs perpendicular to the board’s surface. This plane is commonly used for providing a reference ground for high-frequency circuits.
Zener Diode: A type of diode that is designed to operate in reverse-bias mode. A Zener diode is commonly used as a voltage regulator or as a protection device against voltage spikes.
ZIF Connector: A connector type that allows easy insertion and removal of wires or cables without the need for soldering. ZIF stands for Zero Insertion Force, as no significant force is required to insert or remove the cable.