Aluminum PCB Manufacturing Services
Aluminum PCB: Why You Need It?
Due to the specific requirements of the product or project, there is a wide range of PCBs available on the market. Aluminum PCB is one of them. It is a bit different from the traditional FR-4 PCBs, has distinct features, and serves different purposes.
What is Aluminum PCB?
All PCBs require a base or core on which the components and other layers are situated. It plays a very important role because the specifications, features, and characteristics of the PCB greatly depend on the core it is made of.
An Aluminum PCB consists of an aluminum core, which is why it is different from traditional PCBs. Other than the core, everything else is almost the same. It is a type of metal core PCB because it uses a metal (aluminum) as the core, and it is one of the most demanded types of metal core PCBs on the market.
The core of the PCB gives the actual support to the components and the layers. It is placed at the bottom. As Aluminum is a metal, it is durable and an excellent conductor of heat and electricity.
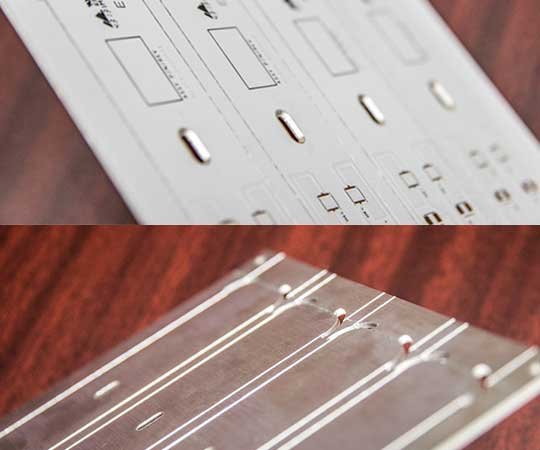
JHYPCB: An Experienced Aluminum PCB Manufacturer
Structure of an Aluminum Core PCB
The common structure of an Aluminum PCB consists of three layers.
- Conducting Layer
- Insulating Layer
- Aluminum Core
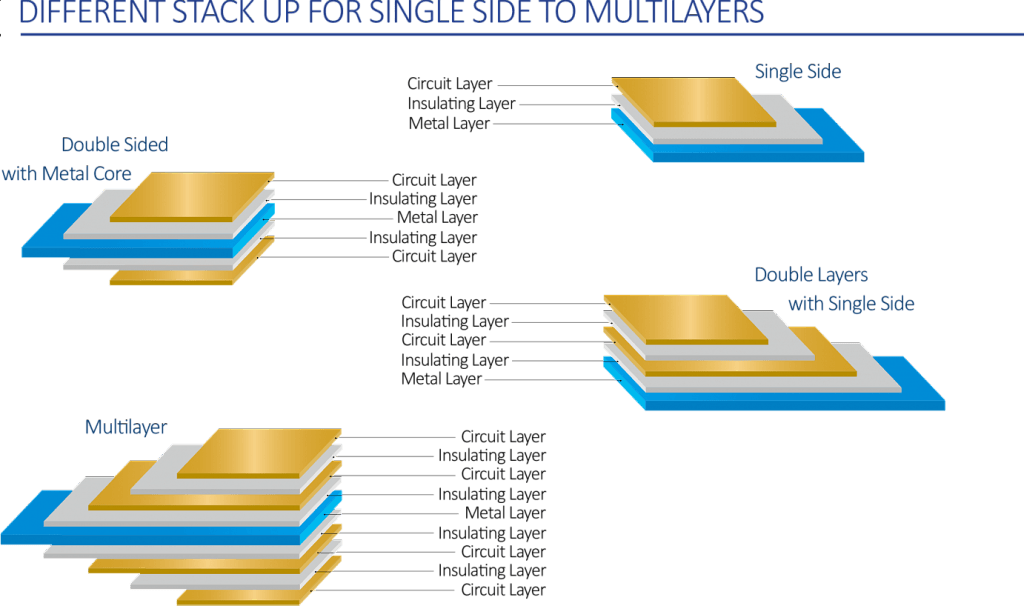
The first and topmost layer of the PCB is the Conducting Layer. It is responsible for the flow of electrons and completing the circuit. It is usually made of copper but can also be made of silver or any other excellent conductor of electricity, depending on the usage. This layer is just the same as any traditional PCB.
The second layer of an Aluminum PCB is the Insulating Layer. It is a very important layer in any metal core PCB because metals are good conductors of electricity. With that being said if there is no insulating layer, the conduction from the copper layer to the core can happen. Thus, an insulating layer prevents the conduction of electrons and ensures the core does not conduct electricity.
The insulating layer is undoubtedly a bad conductor of electricity, but it is a good conductor of heat. Therefore, it can easily transfer the heat produced by the components to the metal core for better and quick heat dissipation.
The last layer is the Aluminum core. It is of a suitable thickness of around 1mm or so, depending on the requirement of the buyer. It ensures excellent thermal conductivity, durability, high power bearing capacity, etc.
This is the common structure of single-layer aluminum PCBs. The layers can be multiple, and the layers increase at the top. There is an insulation layer between two conducting layers, and it can also be FR-4. However, the aluminum core is at the bottom regardless of the number of layers in the PCB.
Moreover, at the top conducting layer, surface finish, silkscreen, and solder mask are applied.
Heat Dissipation
The most important benefit of an aluminum PCB is heat dissipation. Due to the presence of aluminum, the heat from the components is dissipated much faster than traditional PCBs. With that being said, the components do not get overheated and last for a long time.
Lightweight and Economical Metal
Aluminum is much lighter than other suitable metal options for PCBs. It does not increase the overall weight of the product. Secondly, if you want a metal core PCB, then the most economical option is aluminum. Due to its cheap cost, the overall PCB cost is reasonable.
Exceptional Durability
Aluminum is known for its durability. It can bear wear and tear and hard environmental conditions. It is an ideal option in many extreme cases. It ensures optimal performance every time.
Great Power Density
The heat dissipation of Aluminum is exceptional. Therefore, it can bear high power and heat. Thus, its power density is high, and it can be used for high-power applications where normal PCBs cannot work.
Applications of Aluminum Base PCBs
Aluminum PCBs are in great demand as they allow you to use them in high-power applications. It is used in LED lighting, power supplies, automobiles, computers, power modules, relays, motor drives, and various consumer products.
An aluminum core PCB is suitable for those applications where high energy or heat is produced. The traditional PCBs cannot last for a long time due to heat, and the components wear off quickly. Thus, aluminum PCB is a necessity in such applications. But if there is no production of high heat, common FR-4 PCBs would be the best because the cost of aluminum PCB cannot be justified in that case.
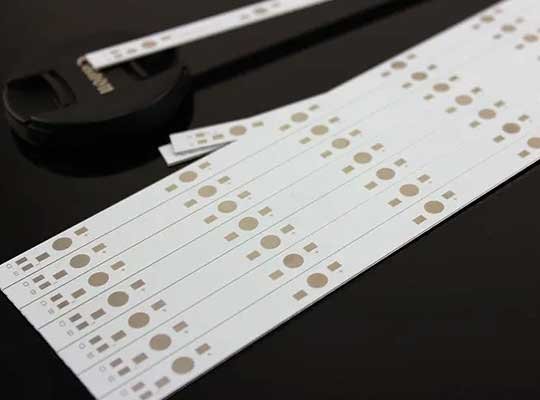
Performance of Aluminum Clad PCB
Aluminum PCBs offer several advantages over traditional FR4 (fiberglass) PCBs, particularly in terms of thermal performance. Aluminum PCBs have a metal core that provides superior heat dissipation compared to FR4 PCBs, making them ideal for applications that require high power or generate a lot of heat.
The performance of aluminum PCBs depends on various factors, including the thickness of the metal core, the thermal conductivity of the metal, and the thickness and quality of the dielectric layer between the metal core and the copper layers.
Aluminum PCBs offer exceptional performance across various aspects. Aluminum has properties similar to copper but is more cost-effective with equally good performance.
- Thermal Dissipation: The ability of a material to dissipate heat is crucial in circuit board performance. Aluminum has a thermal dissipation property that is 10 times higher than the standard FR-4 substrate used in PCBs. This property helps stabilize circuit board performance under high thermal stress.
- Thermal Expansion: Thermal expansion is the stretching and contraction of a PCB under temperature influence. Different materials have varying rates of expansion or contraction, which can affect performance. The coefficient of thermal expansion of aluminum is higher than FR-4, reducing the risk of PCB cracking and aiding in surface mount assembly.
- Dimensional Stability: Dimensional stability is a substrate’s ability to maintain its measurements during the curing process. Aluminum has better dimensional stability than fiberglass laminates, with only a 2-3% difference in size when heated between 30-150°C. Higher dimensional stability helps avoid insulation bulking and thermal bridge formation between signal traces.
- Stable Dielectric Constant: Aluminum-backed PCBs offer a stable dielectric constant that helps minimize loss-tangent and maintain signal integrity. The dielectric constant is inversely proportional to temperature, and aluminum’s heat management property reduces fluctuation by maintaining a stable temperature.
The Thickness of Aluminum Core PCB
The thickness of an aluminum PCB typically ranges from 0.5mm to 3.2mm, with 1.0mm and 1.6mm being the most common thicknesses. The thickness of the aluminum substrate itself usually ranges from 0.5mm to 2.0mm, while the thickness of the copper layer on the aluminum substrate can range from 18µm to 140µm.
The choice of aluminum PCB thickness depends on several factors, including the application, the required thermal management properties, and the available space for the PCB. Thicker aluminum PCBs provide better thermal conductivity and heat dissipation, making them suitable for high-power applications that generate a lot of heat. Thinner aluminum PCBs, on the other hand, are more lightweight and can be used in applications where weight is a critical factor.
It is important to note that the thickness of the aluminum PCB can also affect the cost of production. Thicker aluminum PCBs require more material and may be more difficult to manufacture, which can increase the cost. Therefore, it is important to carefully consider the required thickness based on the specific needs of the application to ensure optimal performance and cost-effectiveness.
JHYPCB: An Experienced Aluminum PCB Manufacturer
JHYPCB is a leading manufacturer of high-quality aluminum PCBs with years of experience in the industry. We have a proven track record of producing reliable and durable aluminum PCBs that meet the most demanding requirements of various industries, including the LED lighting, automotive electronics, and solar electronics industries.
JHYPCB utilizes advanced manufacturing technologies and techniques to ensure the precision and accuracy of aluminum PCBs. We have a team of experienced engineers and technicians who work closely with customers to provide customized solutions to meet their specific needs.
In addition to its commitment to quality, JHYPCB also places a strong emphasis on customer service. We provide fast turnaround times, competitive pricing, and excellent communication throughout the manufacturing process. This ensures that customers receive their aluminum PCBs on time and to their exact specifications.
Full Feature Aluminum Circuit Boards Manufacturing Service
At JHYPCB, we pride ourselves on being able to provide a wide range of aluminum PCB manufacturing services to meet the diverse needs of our customers. In addition to providing simple single-layer aluminum PCB manufacturing services, we also offer high multi-layer and more complex types of aluminum PCBs.
Our experienced team of engineers and technicians utilize the latest manufacturing technologies and techniques to produce high-quality aluminum PCBs with precision and accuracy. We can manufacture aluminum PCBs with various layer counts, up to 6 layers, depending on the requirements of our customers.
Furthermore, we can also manufacture other types of aluminum PCBs, including double-sided aluminum PCBs, flexible aluminum PCBs, and hybrid aluminum PCBs that combine aluminum and other substrate materials. This enables us to provide customized solutions to meet the specific needs of various industries, including the LED lighting, automotive electronics, and solar electronics industries.
At JHYPCB, we are committed to providing our customers with high-quality aluminum PCBs that meet their exact specifications. We offer competitive pricing, fast turnaround times, and excellent communication throughout the manufacturing process to ensure that our customers receive their aluminum PCBs on time and to their satisfaction. Whether you need a simple single-layer aluminum PCB or a complex multi-layer aluminum PCB, JHYPCB is the right choice for all your aluminum PCB manufacturing needs.
FAQs About Aluminum PCB
What is an aluminum PCB?
An aluminum PCB is a type of printed circuit board that has a metal core made of aluminum. The metal core provides improved thermal dissipation and other advantages compared to traditional FR4 PCBs.
What are the benefits of using aluminum PCBs?
Some benefits of using aluminum PCBs include improved thermal performance, better reliability, smaller form factor, and improved electrical performance.
What is the thermal dissipation of aluminum PCBs?
The thermal dissipation property of aluminum is 10 times higher than that of FR4 PCB substrate, making it more effective in dissipating heat away from the board.
What is the thermal expansion of aluminum PCBs?
The coefficient of thermal expansion of aluminum is higher than that of FR4, which reduces the risk of PCB cracking and aids in surface mount assembly.
What is the dimensional stability of aluminum PCBs?
Aluminum PCBs have better dimensional stability than fiberglass laminates, which helps avoid insulation bulking and thermal bridge formation between signal traces.
What is the dielectric constant of aluminum PCBs?
Aluminum-backed PCBs offer a stable dielectric constant that helps maintain signal integrity.
How are aluminum PCBs fabricated?
Aluminum PCBs are typically fabricated using a specialized process that involves etching copper traces onto the metal core and adding a dielectric layer between the metal core and the copper layers.
Are aluminum PCBs more expensive than FR4 PCBs?
Yes, aluminum PCBs are generally more expensive than FR4 PCBs due to the specialized fabrication process and the cost of the metal core material. However, the benefits of using aluminum PCBs may outweigh the higher cost for certain applications.
Can aluminum PCBs be used for high-frequency applications?
Yes, aluminum PCBs can be used for high-frequency applications. However, it is important to consider the thickness and dielectric constant of the dielectric layer when designing the PCB to ensure proper signal integrity.
Are there any special considerations for assembly and soldering of aluminum PCBs?
Yes, the metal core of aluminum PCBs can absorb heat and make it more difficult to solder components. Special soldering techniques and equipment may be required to ensure proper solder joints and avoid damage to the PCB.
What is the maximum operating temperature for an aluminum PCB?
The maximum operating temperature for an aluminum PCB depends on the specific design and the capabilities of the components used. However, aluminum PCBs can typically handle higher temperatures than FR4 PCBs, making them suitable for high-temperature applications.