China Metal Core PCB Fabrication
Metal Core PCB - MCPCB
Whether you need metal core PCB prototypes or large production runs, you can count on our metal core PCB services.
Metal Core PCB - MCPCB Manufacturer
We are your go-to PCB partner and supplier if you are looking for a trusted PCB manufacturer. At JHYPCB, we offer metal core PCB prototype manufacturing and MCPCB fabrication quantities for aluminum core and heavy copper PCBs.
What is Metal Core PCB?
A metal core PCB, or MCPCB, is a printed circuit board with a metal core, typically aluminum, as its base material. The metal core provides improved thermal conductivity compared to traditional PCBs, which makes MCPCBs well-suited for high-power applications that generate a lot of heat.
MCPCBs are commonly used in applications such as LED lighting, power converters, motor control, and automotive electronics. The improved thermal performance of MCPCBs allows for higher power densities and increased reliability, which is especially important in harsh environments or applications that require long lifetimes.
One of the main advantages of MCPCBs is their ability to efficiently dissipate heat, which helps prevent overheating and prolongs the lifespan of the components on the board. Additionally, MCPCBs are often smaller and lighter than traditional ones, which can be beneficial in applications with limited space. They also provide good electromagnetic shielding and can reduce electromagnetic interference (EMI) and radio frequency interference (RFI).
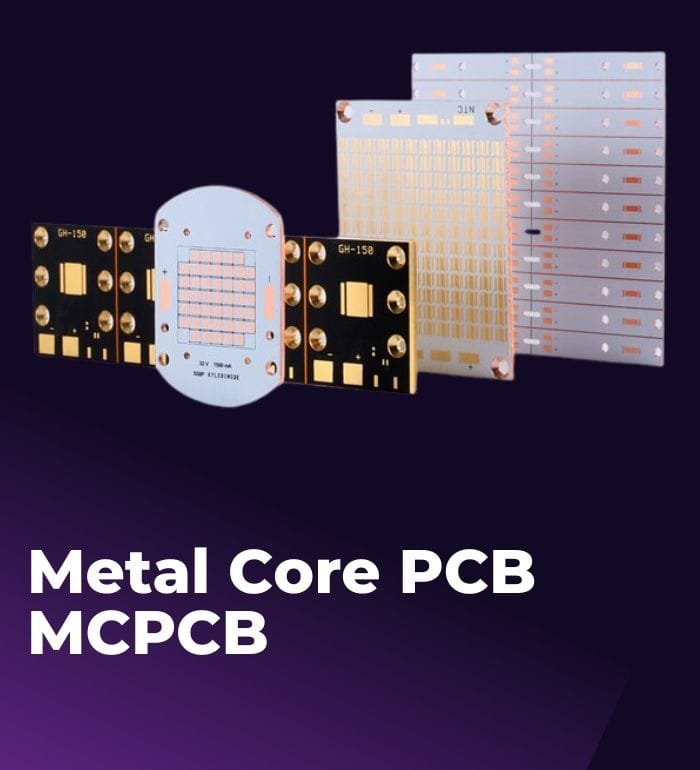
What are the advantages of metal core PCB?
Excellent thermal management: MCPCBs have superior thermal conductivity, making them suitable for high-power applications that generate significant heat. They dissipate heat more efficiently, resulting in enhanced reliability and longer lifetimes for electronic devices.
- Enhanced stability and reliability: MCPCBs offer better stability and reliability than traditional PCBs due to their improved thermal management capabilities. This results in reduced maintenance requirements and longer lifetimes for electronic devices.
- Ideal for high-power applications: MCPCBs are well-suited for high-power applications that require efficient thermal management and reliable performance. These include LED lighting, power converters, motor control, and automotive electronics.
- Customizable and versatile: MCPCBs can be designed to meet specific requirements and customized for different applications, making them a flexible and versatile option for electronic devices in various industries.
- Good EMI shielding performance: MCPCBs provide excellent electromagnetic interference (EMI) shielding performance, reducing the impact of external electromagnetic radiation on sensitive electronic components. This results in improved performance and reliability for electronic devices.
What Are The Applications of Metal Core PCB?
Metal core PCBs are used in a wide range of applications that require high-power and/or reliable performance, particularly those that generate significant heat. Some common applications of MCPCBs include:
- LED lighting: MCPCBs are commonly used in LED lighting applications due to their efficient thermal management capabilities and ability to handle high power densities.
- Power converters: MCPCBs are ideal for power converters because of their ability to handle high-power densities, which results in better performance and reliability.
- Motor control: MCPCBs are commonly used in motor control applications because of their ability to handle high currents and high temperatures.
- Automotive electronics: MCPCBs are used in automotive electronics because of their ability to handle high-temperature environments and their enhanced reliability.
- Audio amplifiers: MCPCBs are used in audio amplifiers due to their ability to dissipate heat and improve the reliability of the amplifiers.
- Industrial control systems: MCPCBs are used in industrial control systems because of their ability to handle high-power densities and harsh environments.
- Medical devices: MCPCBs are used in medical devices for their excellent thermal management properties, ability to handle high-power densities and improved reliability. They are commonly used in medical imaging equipment, patient monitoring systems, and surgical instruments.
- Communication equipment: MCPCBs are used in communication equipment for their ability to handle high-frequency signals, provide electromagnetic interference (EMI) shielding, and improve thermal management. They are commonly used in wireless routers, base stations, and satellite communication systems.
- Network equipment: MCPCBs are used in network equipment to handle high data transfer rates, provide EMI shielding, and improve thermal management. They are commonly used in network switches, routers, and servers.
What Are The Metal Core PCB Materials?
Aluminum and copper are commonly used in metal core PCBs due to their excellent thermal conductivity and electrical conductivity properties, respectively. The use of these materials helps to dissipate heat generated by high-power components on the PCB, leading to improved performance and reliability.
Aluminum Core PCBs: Aluminum has a thermal conductivity of approximately 200 W/mK, which is much higher than that of traditional FR4 PCBs (approximately 0.2-0.3 W/mK). This high thermal conductivity allows heat to be efficiently transferred away from the high-power components on the PCB, preventing overheating and potential damage to the components. Aluminum is also lightweight, inexpensive, and easy to manufacture, making it a popular choice for MCPCBs.
The characteristics of aluminum core PCB are:
- Thermal conductivity- 5W/(mK) to 2.0W/(mK) (Watts per meter Kelvin)
- Peeling strength- >9lb/in
- Solder resistance- SF: 288℃, >180 sec.
- Breakdown voltage- >3000V
- Dielectric loss angle- 0.03
- Flammability- UL 94V-0
- Panel size- 18” x 24”
Copper Core PCBs: Copper, on the other hand, has excellent electrical conductivity, with a resistivity of approximately 1.7 x 10^-8 ohm-m at room temperature. This makes copper an ideal choice for power electronics and motor control applications, where high currents and low resistances are required. Copper also has good thermal conductivity, with a value of approximately 400 W/mK, which makes it suitable for applications that require both good electrical and thermal performance.
In addition to aluminum and copper, steel, stainless steel or nickel are also one of the materials used for metal core PCBs, but aluminum and copper become the first choice due to their special performance and cost performance.
Various base metals and their properties
Material | Thermal Conductivity (W/mK) | Electrical Conductivity (MS/m) | Density (g/cm3) | Cost ($) per kg |
Aluminum | 200 | 37 | 2.7 | 2.25 |
Copper | 400 | 100 | 8.96 | 9.35 |
Steel | 15 | 7 | 7.85 | 1.50 |
Nickel | 91 | 14.3 | 8.91 | 13.50 |
What is the Metal Core PCB Stack up?
The stack-up of a metal core PCB typically consists of three main layers:
- The metal core layer: This layer is typically made of aluminum or copper and acts as a heat sink, allowing heat to be efficiently dissipated away from the high-power components on the PCB.
- The dielectric layer: This layer is typically made of a thermally conductive material such as polyimide or epoxy resin, which helps to transfer heat from the high-power components to the metal core layer.
- The copper layer: This layer is typically a thin layer of copper foil that is laminated to the dielectric layer. It is used to create the circuitry and electrical connections on the PCB.
In addition to these three main layers, MCPCBs may also include additional layers such as solder mask, silkscreen, and surface finish layers. These additional layers help to protect and enhance the functionality of the PCB.
It consists of a single copper conductive layer on the top, a metal layer as a base plate and a thermal conductive dielectric working as the insulator.
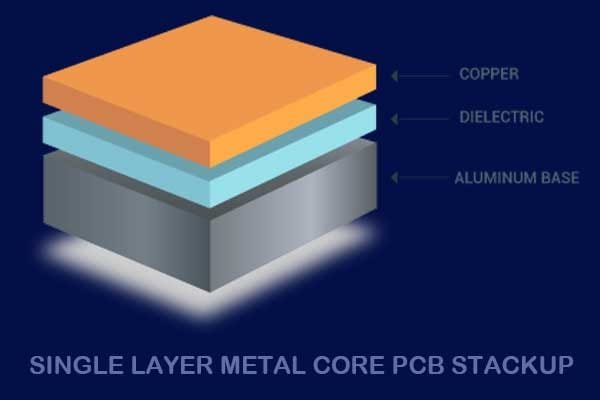
It has two copper layers and the metal core is between the copper layers. The copper layers are interconnected via Plated Through Holes (PTH).
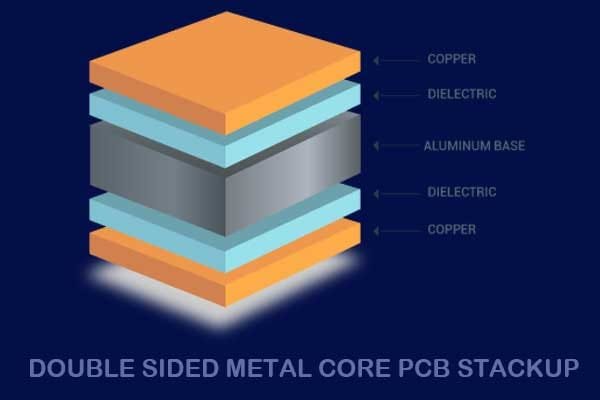
It has more than two conductive layers separated by thermal dielectric. The structure of the metal base is at the bottom. SMT components can only be placed on one side. THT components are not allowed, but it provides the possibility to make blind and buried vias.
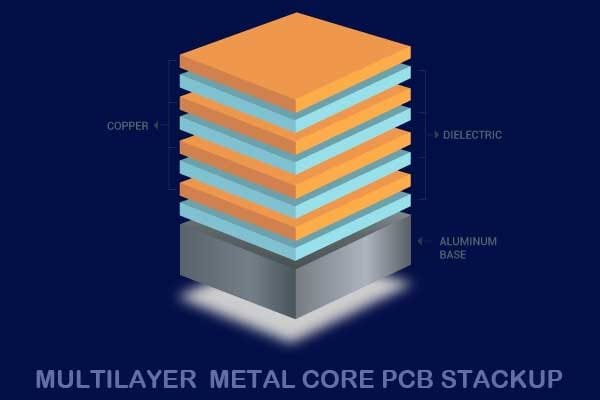
Metal Core PCB Manufacturer in China
We, at JHYPCB, are a reliable manufacturer of Metal Core PCBs catering to a wide range of industries. Our use of cutting-edge technology enables us to meet the custom requirements of our clients. With over four decades of experience in manufacturing state-of-the-art metal core printed circuit boards and a vast body of industry knowledge, we are the go-to PCB partner for our clients. Our team of PCB experts, equipped with industry best practices, provides great support in manufacturing custom metal printed circuit boards to exact requirements.
Our metal PCBs undergo stringent quality checks, ensuring that our clients receive products of the finest quality that comply with the highest industry standards. Our quick turnaround times give a boost to your go-to-market plan, offering you a competitive advantage. Additionally, our vast network of component suppliers enables us to offer cost-effective prices.
Whether you need Metal Core PCB prototypes or large production runs, you can count on our metal core circuit board services, without compromising on quality. We also provide turnkey Metal Core PCB manufacturing services, allowing you to focus on your core business while we take care of the entire end-to-end process.
Contact us with your bespoke requirements and allow us to offer you custom quotes.
Metal Core PCB Manufacturing Capabilities
Manufacturing Capability | Description |
Layer Count | Typically 1-8 layers |
Board Thickness | 0.4mm – 3.2mm |
Copper Thickness | 0.5oz – 10oz |
Minimum Trace/Spacing | 0.1mm |
Minimum Hole Size | 0.2mm |
Minimum Mechanical Drill Size | 0.3mm |
Surface Finish | HASL, ENIG, OSP, Immersion Tin/Silver/Gold, Hard Gold |
Solder Mask Color | Green, Blue, Black, White, Yellow, Red |
Silkscreen Color | White, Black, Yellow |
Material Options | Aluminum, Copper, Stainless Steel, Nickel |
Maximum Board Size | Up to 600mm x 1200mm |
Special Features | Blind/Buried Vias, Counter Sinks, Controlled Impedance, Edge Plating, Via Plugging |
FAQs
How To enhance the thermal management capabilities of MCPCBs?
To further enhance the thermal management capabilities of MCPCBs, additional techniques can be employed, such as thermal vias and thermal pads. Thermal vias are small holes drilled through the PCB that allow heat to be transferred to the metal core layer more efficiently. Thermal pads are areas on the PCB where the metal core layer is exposed, allowing heat to be dissipated directly to the heat sink.
Can metal core PCBs be customized?
Yes, metal core PCBs can be customized according to the specific needs of the application. Customization options include material selection, thickness, size, and shape.
How are metal core PCBs manufactured?
Metal core PCBs are manufactured using similar processes as traditional FR-4 PCBs, including etching, drilling, plating, and soldering. However, extra care must be taken in the design and manufacturing process to ensure proper heat dissipation and thermal management.
What are the design considerations for metal core PCBs?
Design considerations for metal core PCBs include thermal management, proper grounding, material selection, trace routing, and component placement.
How can I test the performance of a metal core PCB?
Performance testing of metal core PCBs can be done using thermal imaging, power cycling, and other tests to measure thermal conductivity, electrical performance, and reliability.
Where can I order metal core PCBs?
Metal core PCBs can be ordered from a variety of PCB manufacturers and suppliers. It's important to choose a reputable supplier with experience in manufacturing metal core PCBs and a good track record of quality and reliability. JHYPCB is a professional PCB manufacturer and supplier in China, offering high-quality metal core PCB prototyping to mass production; you can send the Gerber files to sales@pcbjhy.com for a quick and free quote.
What is Metal Core PCB Thickness?
The thickness of metal cores PCB substrate is typically 30 mil - 125 mil, but thicker and thinner are possible.
MCPCB copper foil thickness can be 1 - 10 oz.
What is MCPCB?
A metal core PCB, also known as a thermal PCB, is a printed circuit board that has a metal core layer instead of the traditional FR-4 (fiberglass) material. The metal core layer helps to dissipate heat more efficiently, making it suitable for high-power LED lighting, power electronics, and other applications that require effective heat dissipation.
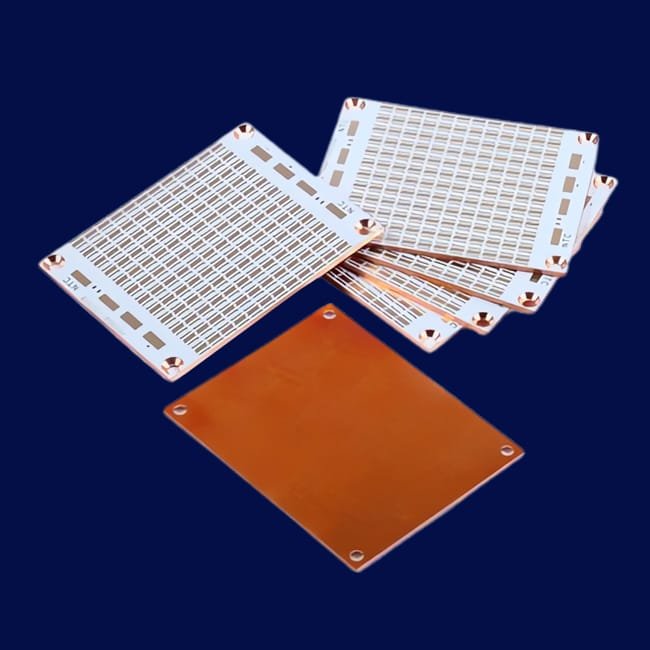