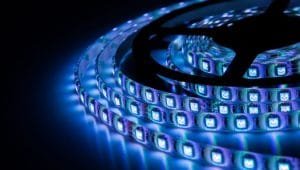
Flexible LED PCBs – Unlocking Design Freedom for Innovative LED Lighting
Flexible LED PCBs represent a game-changing innovation for LED lighting
The traditional rigid PCB cannot bend, and it will break if pressure is exerted. Thus, the product must be designed according to the PCB shape, and there should be a dedicated space for the PCB. Thus, there are many limitations in product manufacturing if a rigid PCB is selected.
Flexible PCBs have removed the constraints of product manufacturing that were due to the rigidity of the circuit. Now, electronic products can be more compact, reliable, and stylish in terms of design and shape. These are ideal for minimal and compact electronic items and have taken the PCB application to the next level.
In simple words, a PCB that can bend is called a Flexible PCB. There is no rocket science behind it; the only thing that matters is the core of the PCB. If the core is made from a flexible material, then the PCB will be able to bend without breaking.
For a Flex PCB, the core must be flexible, non-conducting, durable, and temperature resistant. These properties enable the PCB to offer optimal performance and last for a long time in different environmental conditions.
Figure 1: A Flexible Printed Circuit
Usually, flex PCBs are made of Polyimide; it is the most preferred material that can easily bend and withstand high temperatures. Another commonly used material is PET, which is a cost-effective option for normal environmental conditions.
Flexible PCBs can easily bend and be adjusted according to the shape of the product. They can bear pressure or strain more than a rigid PCB. Thus, they make the final product compact and minimalistic.
These PCBs can be used as an independent circuit having components and conducting lines. Plus, you can also use them as an interconnection between other rigid or different types of PCBs. These eliminate the need for unreliable wirings and sockets. With that being said, the overall circuit becomes more reliable and long-lasting
A flexible PCB can have multiple layers, but not as many as a rigid PCB. Irrespective of the number of layers, you will find four main components: The Core or Substrate, Conduction Layer, Protective Finish, and Adhesive Material.
The core or substrate is the base material, which is Polyimide or PET in the case of Flexible PCBs. It is the main layer because it holds everything on the PCB together.
The second most important layer of any PCB is the conducting circuit or layer. In most cases, it is made of copper and can conduct electricity.
The conducting layer on the PCB cannot be left exposed to react with the air. Instead, a surface finish is a must to protect the conducting layer and ensure optimal performance. There are different types of surface finishes available, such as HASL, ENIG, immersion silver, OSP, etc.
Last but not least is the adhesive. It is a must to join various parts and components together. It could be epoxy, acrylic, or any other similar material.
Figure 2: Structure of a Multi-layer Flexible Circuit
Flexible PCBs are quite common these days. You can find it in almost all electronic devices. If we consider the functionality of PCBs, then flexible PCBs will be the first choice of the designers. They would love to incorporate flex PCBs instead of traditional PCBs, but it will drastically increase the overall cost. Thus, rigid PCBs are used due to their low cost, and flexible PCBs are used with them to ensure flexibility, durability, reliability, and space-saving. In places where the preference is flexibility and compact design rather than cost, the best option would be Flexible PCBs.
Flexible PCBs are used in smartphones, smart wearables, automotive, aerospace, military equipment, medical devices, power electronics, and many other applications. It is used in almost all industries where the flow of electronics or electricity is required for the product.
Figure 3: Application of Flexible Circuit in Smart Wearables
JHYPCB is a leading manufacturer of high-quality Flexible PCBs, providing tailored solutions to meet the demands of various industries. With years of experience in the industry and state-of-the-art manufacturing facilities, we are capable of producing flexible circuits with exceptional performance, durability, and flexibility. Our engineering team is dedicated to delivering products that meet or exceed customer expectations, and we work closely with our clients to ensure their designs are optimized for cost, functionality, and reliability. Whether you need a small prototype or a large-scale production run, JHYPCB can provide you with a flexible circuit board that meets your exact specifications.
JHYPCB’s in-house prototyping services offer a comprehensive solution to bring your PCB designs to life. Our team of experts is equipped with the knowledge and tools to collaborate with our customers and act as an extension of their design team for new products. We work closely with our customers’ engineers to provide valuable insight and cost-effective design for manufacturability solutions. From PCB material selection to impedance modeling and manufacturing technology, we strive to ensure your product is launched on-time and within budget.
At JHYPCB, we understand the importance of prototyping and testing before committing to production volumes. Whether you need single-layer FR4 boards, rigid-flex multi-layered boards, or anything in between, our team can deliver a high-quality prototype PCB that you can modify and test as needed.
Discover the benefits and applications of rapid PCB prototyping by choosing JHYPCB as your trusted partner for all your PCB needs.
Learn More our Flexible PCB Prototype Service
JHYPCB is a leading provider of flexible PCB manufacturing services, offering a wide range of capabilities to meet the needs of various industries. Our advanced technology, quality materials, and expert technical support enable us to provide custom solutions for any application. Here are some of our key capabilities:
Capability | Details |
---|---|
Flexibility | Single-sided, double-sided, multi-layer, flex-rigid PCBs, and FPC With Coverlay or FPC With stiffener |
Surface Finishing | ENIG, HASL, OSP, immersion silver, immersion tin, etc. |
Material Options | PI, PET, PEN, FR-4, Polyimide (Kapton), Adhesiveless Copper Clad Base Material, High Performance Epoxy Laminate and Prepreg, and High-Performance Polyimide Laminate and Prepreg. |
Adhesive and Lamination | Acrylic, epoxy, thermally conductive, etc. |
Design and Prototyping | Stacking Consultation, prototyping, testing, and Material Consultation |
Quality Control | ISO 9001, IPC-A-600F, IPC-A-610E, and RoHS compliant |
Technical Support | Expert engineering support, design for manufacturability, and design for testability |
Production Capacity | Quick turnaround, on-time delivery, and scalable production volume |
Customer Service | Timely communication, comprehensive documentation, and collaborative partnerships |
At JHYPCB, we pride ourselves on providing high-quality flexible PCB manufacturing services to our customers. Whether you need a single prototype or a large-scale production run, we have the capabilities and expertise to meet your needs. Contact us today to learn more about our flexible PCB manufacturing capabilities and how we can help bring your projects to life.
A flexible circuit, also known as a flexible PCB or flex circuit, is a type of printed circuit board that can be bent or twisted without breaking.
Flexible PCBs offer a number of benefits over rigid PCBs, including the ability to conform to complex shapes and spaces, improved reliability and durability, reduced size and weight, and improved signal integrity.
Flexible PCBs are used in a wide range of applications, including consumer electronics, medical devices, aerospace and defense, automotive, and industrial control systems.
The materials used to make flexible PCBs include flexible copper clad laminate (polyimide, polyester, and other flexible substrates), flex PCB stiffener (FR4, PI, PET, Copper, Aluminum or Steel), FPC coverlay (Polyimide Film or Polyester Film), pressure-sensitive adhesive, and bonding sheet. Conductive materials such as copper is used to create the circuit traces. These materials provide mechanical flexibility, electrical conductivity, and insulation properties necessary for a reliable and durable flexible PCB.
When designing a flexible PCB, it is important to consider factors such as the bend radius, the number of layers required, the type of substrate and adhesive used, and the placement of components.
Flexible PCBs are typically manufactured using a combination of additive and subtractive processes, such as screen printing, etching, and laminating.
To get started with designing and manufacturing flexible PCBs, you will need to work with a PCB manufacturer that specializes in flexible circuitry, such as JHYPCB.
Flexible PCBs can be more expensive to manufacture than rigid PCBs, and they may be more difficult to repair or modify. They are also more susceptible to damage from sharp bends or creases.
If you have specific custom requirements for flexible PCB fabrication, you can receive a prompt quote by submitting your details. Simply reach out to us at sales@pcbjhy.com, and we would be delighted to hear from you and provide tailored solutions.
The thickness of a flex PCB can vary depending on the specific application and requirements. However, typical thicknesses for flexible PCBs range from 0.1mm (0.004 inches) to 0.3mm (0.012 inches).
The price of a Flex PCB varies based on a number of factors such as size, complexity, number of layers, materials used, quantity ordered, and manufacturing processes involved. The cost of a Flex PCB can range from a few dollars to hundreds of dollars per unit. It is recommended to request a quote from a PCB manufacturer to get an accurate price for a specific Flex PCB project. Additionally, prices can also vary depending on the region and the PCB manufacturer chosen.
There are several types of flexible PCBs, including:
Single-layer flex PCB: This type of flexible PCB has one conductive layer.
Double-layer flex PCB: This type of flexible PCB has two conductive layers, one on each side of the flexible substrate.
Multilayer flex PCB: This type of flexible PCB has more than two conductive layers.
Rigid-flex PCB: This type of flexible PCB combines flexible and rigid PCBs in a single board, allowing for complex and compact designs.
Sculptured flex PCB: This type of flexible PCB has a non-uniform cross-section, allowing for more flexibility and better bending performance.
Double-sided sculptured flex PCB: This type of flexible PCB has a non-uniform cross-section and two conductive layers.
Flex PCB and rigid PCB differ mainly in their physical structure and properties. Flex PCBs are flexible and can bend, twist, or fold, while rigid PCBs are inflexible and cannot bend or fold. Here are some of the key differences between the two types:
Construction: Flex PCBs are made of flexible copper clad laminate (FCCL) as the base material, and are often reinforced with a stiffener material for support. Rigid PCBs, on the other hand, are made of a rigid substrate, such as fiberglass or plastic, and do not require any additional support.
Size and Shape: Flex PCBs can be made in various sizes and shapes, and are ideal for use in products that require a high level of flexibility in their operations. Rigid PCBs, on the other hand, are typically used in products that require a stable and consistent electrical connection.
Applications: Flex PCBs are commonly used in applications where the PCB needs to conform to a certain shape or fit into a tight space. They are often used in wearable devices, medical equipment, automotive electronics, and aerospace applications. Rigid PCBs are used in applications where the PCB needs to be stable and secure, such as in servers, routers, and other computing equipment.
Manufacturing: The manufacturing process for flex PCBs is more complex and requires specialized equipment, while rigid PCBs are typically easier and less expensive to manufacture.
Overall, the choice between a flex PCB and rigid PCB depends on the specific application and requirements of the project.
The Single sided Flexible PCB manufacturing Process Steps including:
The manufacturing process of double-sided flex PCB typically includes:
Cutting → Drilling → Plated Through Holes (PTH) → Plating → Pre-treatment → Pasting Dry Film → Alignment → Exposure → Development → Graphic Plating → Stripping → Pretreatment → Pasting Dry Film → Alignment Exposure → Development → Etching → Stripping → Surface Treatment → Covering Film → Pressing → Curing → Immersion of Nickel Gold → Printing Characters → Shearing → Electrical Test → Laser Profile or Punching → Final Inspection → Packaging → Shipment. This is a complex and specialized process that requires careful attention to detail to ensure the final product meets the required specifications.
Flex circuits have several process characteristics, which include surface treatment, profile, and substrate copper thickness. Surface treatment is the process of preparing a surface to facilitate adhesion, solderability, and electrical conductivity. Flex circuits can be surface treated with immersion gold, OSP (Organic Solderability Preservatives), gold plating, HASL/LF (Hot Air Solder Leveling/Lead-Free).
Profile refers to the shape of the flex circuit. They can be manually shaped by skilled technicians, or they can be cut using CNC machines or laser cutting. CNC cutting is ideal for high-volume manufacturing, while laser cutting is more suitable for low to medium volume runs.
The substrate copper thickness of flex circuits is measured in ounces per square foot. It is an important consideration when selecting a flex circuit for a project. Typical substrate copper thickness options include 1/3 ounce, 1/2 ounce, 1 ounce, 2 ounces, and 4 ounces. Thicker copper allows for a higher current capacity, but it can also increase the overall weight and cost of the flexible circuit.
Flexible LED PCBs represent a game-changing innovation for LED lighting
Looking for a reliable and cost-effective solution for your flexible
Learn the contrasts of PET and PI for flexible PCBs.
The Flex PCB stiffener was developed to improve the rigidity
We will provide an overview of the manufacturing process, outlining
From single-sided to sculptured circuits, explore the various types of
The versatility of flex circuits lies in their ability to
Flex circuits, also known as flexible printed circuits or FPCs,
Fill out the form below, and we will get back to you within the next 24
hours to complete the order, and then you’re all set to get started!